Introduction: Modeling Props for 3D Printing
This is going to be a brief overview of how I concept, design, and model semi functional props such as firearms. This Instructable will mainly focus on my Halo firearms but this method can be applied to nearly anything you wish to make! In this tutorial, we will follow the creation of my first major prop, the Halo 4 MA5D AR.
Disclaimer: I am the sole owner of the models shown in this tutorial. Models are not for sale, no exceptions. plastic casts made from the 3D prints can be purchased, however not all are available for sale. I do not, in any way own the rights to the Halo firearms above, nor do I intend to take credit for them. I only created the likeness from inspiration, and added my own moving aspects to the models. These are NOT game models taken from the game and edited. To avoid any legal implications all models are made from scratch with only reference images.
Step 1: Gather Materials
The ONLY things I use to model are:
-A creative brain
-Free time
-Autodesk AutoCAD Mechanical (For 2d conception)
-Autodesk Inventor Pro (For 3D modeling)
-Reference images (Easier if orthographic)
Additionally:
-Autodesk VRED Pro (For HD rendering)
These programs can be downloaded FREE from Autodesk Student for educational purposes, they are a GREAT learning tool. I am self taught with these programs and they link together great, making everything in this process much easier!
Step 2: Plan It Out
In this first step, you will want to plan out your end-game. Are you looking to make a fully functioning prop with lots of moving parts? A simple widget with one purpose? Or a prop with that mimics something in a game or movie?
All of these options require planning. Many images of what you are trying to create will be needed here, collect as many as you can! In my case, I went into AutoCAD and planned out what parts of the AR would be functioning, and what parts would be useful to move. While I do not have the original pictures, I did sketch out a rough AR on paper and planned for a few nights exactly how I wanted things to work out. This step may seem unnecessary, but it makes the modeling process a whole lot easier in the long run.
It may also be beneficial for you to collaborate with others. For the Halo 5 SMG, I chatted with people using reference images on what might each button on the SMG might do if it were real. After you are done planning, you are ready to begin.
Step 3: 2D Planning; Preparation for 3D
This is where we get started. This step should take you the longest. While I do not want this to become a full on "How to use AutoCAD & Inventor tutorial" I will give you the basics on how to plan out the model.
1. When you open AutoCAD, you should tab over to "Insert" and click "Attach". This will allow you to place and scale images within the document. Try to place one side view in the middle of the page, while the top/bottom/front/back go around each other. Scale every image to the same size and line up the images to make sure all parts of the prop/gun/etc line up in every view.
2. Start drawing! Overall this step will just have you playing connect the dots. Draw lines and curves and circles to show the outline of EVERYTHING on the prop. To connect lines, simple hover over an endpoint with the mouse until a green box appears, then click. This will ensure closed shapes for use in Inventor. While this program may seem WAY COMPLICATED at first, don't be afraid as its really easy. I recommend watching tutorials on YouTube or in other places. If there is a want I could make a video or two (post in the comments). However, there is only one way that you are going to learn how to use these programs: PLAY WITH THEM! Click things! Drag Things!!!. Find out what everything does! This way you wont have to memorize what the guy did in the tutorial and what not, you can just go! Anyway, once you get the hang of it trace the prop in AutoCAD. You will want to make sure every line you draw has a SOLID connection to the next line. Draw out anything that will help you in the modeling phase, you do not need to trace every view, just make sure that the side view you have it complete and that you have some idea of how large the other dimensions will have to be (Width etc)
3. Some tips. Design the prop in several parts if possible, the more the better. This will make the modeling easier and the print MUCH easier. Plus its fun to design pegs and joints and connecting "bits". Use different colors and create many layers in the layer tab to keep it slightly organized. (Mine become VERY messy anyway). Use the scale function and draw lines to measure how big you want the final product to be! This will help you model and will ease the process of scaling later (If you use Inventor you wont have to re-scale anything).If you need to, you can change the scale of the entire document by going to Layout>Page Setup>Modify>Plot scale. This scale will hold in the document, however if the sketches are moved into Inventor they will automatically be converted to 1:1 again. No worries!
4. The basics include an easy type in command system. When you first click to make a line for example, you can type in the specific dimension and hit tab for the angle of the line. Furthermore any command can be simply typed on the keyboard to your liking. Inventor uses the same "click to enter dimensions and angles system" but not the command system. Here are a few of the most common things I use to trace the images.
Line- Click for the first point, click again for the second. Simple as that
Circle- Click for center, second click for radius/diameter
Arc-Various points of the arc for clicking
Mirror- Select objects, select two points on the mirror line, enter "N" to keep the original object.
Overall, the program should guide you on what to enter next. Don't become overwhelmed with the massive amount of features in this program, you are only trying to trace an image.
Optional:
At this point, you could simply print your drawings to use as a template for foam or wood props. Check out my other tutorials on how to layer wood to create these props. When you print, the images you have been tracing will not print and only the lines and curves you made will print.
Step 4: Modeling
Here is the fun part. No in depth tutorial here folks, not gonna fly. Every part you make will be different, and all will have different methods for completion. As some general things in Inventor though:
1. When you open Inventor, hit new PART. This, well, will be a part of your final model. These parts can be placed in one big ASSEMBLY file later on. The parts in an assembly file can be jointed together to move it certain ways, etc. Play around with these with some simple geometric shapes to see how they react.
2. When you make your first part, hit new sketch and select a plane. Copy/ Past the 2d sketch you did in AutoCAD and hit save sketch. SAVE YOUR PART OFTEN! Here you will make your first extrusion to make a base to modify. The image above shows the extrude feature to make the main portion of the fore grip. Simply click on Extrude and then the outline of which part you would like to create. Do work in small parts! This is where the surrounding views in the 2D sketch come in handy, you now know what to enter as the width for this part. After a base extrusion is made, we then modify it to become the final part. The following is the list of modifications made on this base to create the final part.
-Modifiers:
Extrude- Moves the shape from a sketch either out or in, adding or removing to the base part.
Chamfer- Adds and angle for an edge
Filet- Adds a curve to an edge
Revolve- Revolves a single sketch shape around an axis
These are just a few things I use, what is really helpful is that Inventor has its own mini help system. When you hover over a button for long enough, an image and a brief explanation of what that does pops up. VERY HELPFUL.
Assemblies: When you have a bunch of saved parts, you can create a new Assembly file. From here you can "Place" all of your parts into one file and either arrange them by hand, or joint them together. Play around with the joints by selecting two faces that will interact with each other on parts.
Overall, I am not the best modeler in the world nor do I know everything about these programs. However I do know that the more you use them the better you will become and the more you will learn. Start playing around by creating new sketches on the base part, and modifying them etc. Split your screen in half with Inventor on one side and with your reference images on the other. Refer to the images and the 2D AutoCAD sketch you made the entire time.
Step 5: Optional: Rendering
Method 1: Inventor Render Studio
After the part is done, you can change the appearance of the entire part of certain faces (by selecting them individually) and changing the appearance in the dropdown menu at the very top of the program. There are MANY options but if you need to, you can edit and make your own materials by clicking on the color wheel next to it.
Within Autodesk Inventor, there is a great rendering program. Tab over to Environments>Inventor Studio. Click on render image to bring up some options on quality and lighting, this should be pretty self explanatory but..er...TRY THEM OUT!
Width & Height- Generally lock the aspect ratio at 640/480 and enter numbers from there. The highest width in Inventor Studio is 4K (4096 pixels wide)
Camera-This should stay the same (Unless you add a different camera to view from, generally the orginal camera works fine and you can move it around nicely)
Lighting Style- Various lighting colors and angles, they can be edited in the Lighting Styles tab under Scene
Scene Style- Various backgrounds/shadow types, also editable in the Scene section
Render Type-Shaded gives a realistic render, while illustration gives outlines of all edges (Really cool with a black background)
Output- Here you can make the render save automatically when completed, and adjust the anti-aliasing quality.
More options can be found in the "Scene" tab. Only render what your CPU can handle! All images above without the Halo 5 Label were done with this method.
Method 2: VRED HIGH END PC ONLY
If you are really into this, and have a CPU that can handle it jump into Autodesk's VRED. It works well with Inventors Assembly files and generally keeps the same materials. Play around with this too, i'm still learning it. All renders with the Halo 5 tag were done in VRED.
Import- You can directly import your Inventor files using the file>import command.
Materials- Much higher quality options than Inventor, editable as well. Select the parts from the left bar to change the material
Render- Here are a gazillion render options, from the amount of shadows to the number of light photons, have fun
WARNING: Only render what your PC can handle, laptops are generally not that great at high CPU for a very long time. Download a temperature manager and make sure it doeskin get too hot. My computer can get up to 100 C with no cooling, so be VERY careful. Grab a fan or three, you'll need them.
Step 6: Print & Finish
You are done! Unless you would like to model or edit more parts, in Inventor click File>Export>CAD Format. Use the drop-down menu to export the file as an .stl, and click options to bring the model to the highest resolution. After all that you will want all those details from your hard work! Send her out to get printed, or plop her into your own 3D printer's software and watch the fun!
That, ladies and gentlemen is about it! You have seen how I model, and you will most likely find your own route that works better for you. As I said before, the only way that you are going to learn how to do anything with these programs is to play around with them, so go to it! Post up some pictures in the comments and show off what you modeled! Let me know if you have any questions or things I should add to this (oh there will be, I've barely scratched the surface on this stuff).
Good Luck!
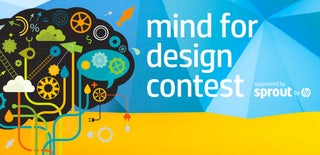
Participated in the
Mind for Design
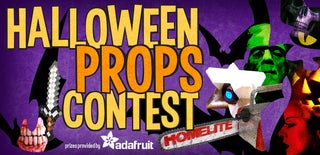
Participated in the
Halloween Props Contest 2015
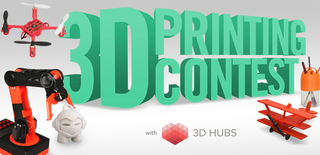
Participated in the
3D Printing Contest