Introduction: Modern Maple and Steel Coffee Table | How to Build
In this Instructable, I'll show you how to build this modern Maple and steel coffee table featuring a solid Maple top and welded steel base. This is a fairly in-depth build but the resulting piece is gorgeous!
Don't miss the build videos above for a LOT more details!
Step 1: Gather Tools and Materials
I'm going to split this build into two halves: the top and the base. Below are the materials and tools for both sections.
Materials Needed For Modern Maple and Steel Coffee Table Tops
- 65 board feet of Hard Maple, or 6 2x10x8' boards
- Biscuits : http://amzn.to/2oyPsw4
- Wood Glue : http://amzn.to/2nAFXbg
- General Finishes High Performance Water Based Polyurethane : http://amzn.to/2oVVbsi
- ¾" Threaded Rod, 4 x 29" lengths : http://amzn.to/2oyHUt7
- ¾" Hex Nut x 8 : http://amzn.to/2n7JYIJ
- ¾" Flat Washer x 8 : http://amzn.to/2nYRPHi
Tools Used For Modern Maple and Steel Coffee Table Tops
- Dewalt 20V Max Impact Driver : http://amzn.to/1QxJD7w
- SawStop PCS 1.75-HP Professional Cabinet Saw : http://amzn.to/2aqqRyn
- DEWALT FLEXVOLT 12" Compound Sliding Miter Saw : http://amzn.to/2ah20gS
- Supermax 19-38 Drum Sander : http://bit.ly/supermax1938
- DEWALT DW621 2-Horsepower Plunge Router : http://amzn.to/2niHu9f
- DEWALT DW682K 6.5 Amp Plate Joiner : http://amzn.to/2oyNPP4
- 8 Inch Jointer : http://amzn.to/2n7JK4z
- MIRKA DEROS Sander : http://amzn.to/2oz4QIN
- DEWALT TrackSaw : http://amzn.to/2nTMqzI
- Veritas Low Angle Jack Plane : http://bit.ly/lowanglejack
Tools Used On Modern Maple and Steel Coffee Table Bases:
- EVOSAW380 Steel Cutting Chop Saw : http://amzn.to/2omFaN7
- Pheer Grinders PH454 Belt Grinder : http://bit.ly/pheer
- Lincoln Electric POWER MIG 210 MP Welder : http://amzn.to/2ppBKIO
- DEWALT FLEXVOLT Grinder : http://amzn.to/2omETtH
- Drill Press : http://amzn.to/2ovtR7x
Materials Used On Modern Maple and Steel Coffee Table Bases:
- 1" Steel Square Tubing : http://amzn.to/2ovu8HB
- ⅛" Steel Flat Bar : http://amzn.to/2ovNoED
- 1" Square Tubing Plug Cap : http://amzn.to/2omHpzV
- Sculpt Nouveau Black Magic Metal Patina : http://bit.ly/sculptnouveau
Step 2: Break Down Pieces for Table Top Lamination
I used Hard Maple for this build and started with rough lumber. The tops have a final thickness of a little less than 4", so starting with boards at least 8" wide helps to reduce waste. If you wanted to keep the wood budget on this project down, you could use 2x10's from the home center and process them in the same way. 6 2x10x8s would give you enough wood for these tops.
I cut the boards down to rough length at the miter saw, about 30", then jointed one edge on the jointer, then ripped the boards in half on the table saw.
Step 3: Square Up Pieces for Table Top Lamination
With the pieces cut to rough size, I then squared up each piece using the jointer, planer, table saw, and miter saw. If you use 2x10s from the home center, you can probably get away with just skip planing the boards on the planer.
After getting everything squared up, I sorted the pieces so any imperfections were facing the bottom of the top and drew a large triangle on the top to keep the pieces in order.
Step 4: Drill Holes for Threaded Rod
One of the design elements on these tables is the nuts and washers that are embedded on each side of the tops. To accomplish this, I decided to go all out and use all-thread running all the way through the tops. I used ¾" all-thread, so I drilled 1" holes in each board. I used a stop block on my drill press to keep these holes lined up.
I also needed to drill a 2" hole into the outside boards to recess the washer and nut. I used a 2" Forstner bit for this.
Step 5: Glue Up the Table Top
Prior to the glue up, I cut slots using a biscuit jointer to help keep all of the boards aligned during the glue up. This is optional but highly encouraged.
I applied glue to each face, added biscuits, and got everything clamped up tight. This was a stressful glue up, but planning ahead really helped reduce the stress. I laid out all of my clamps ahead of time and made sure I had plenty of glue and biscuits at the ready.
Step 6: Flatten the Table Top
After the glue up, you will inevitably have some slipping so the top pieces won't line up perfectly. I flattened the bottom using a low angle jack plane and then flattened the top using my drum sander. If you don't have a drum sander, you could flatten the top with a hand plane, but I'm not quite that good at using a hand plane, yet.
Step 7: Square Up the Table Top
After flattening the table top, I squared up the two ends using a track saw. A circular saw and straight edge would work as well. Since the tops are so thick, I had to make a pass, flip the top, then make another pass to cut all the way through.
Step 8: Sand the Table Top and Round Over All Edges
Next came quite a bit of sanding. Consider there is so much surface area on these table tops, I had a ton of sanding ahead of me. I started with 80 grit and worked my way up to 180 grit. Before sanding with my final grit, I rounded over all of the edges using a ⅜" radius roundover bit on my router. This is a huge part of the look of these tables, plus it'll keep you from destroying your shins if you bump into the table.
Step 9: Apply Finish to the Table Tops
I used a water-based polyurethane for these tops, since they will see a decent amount of wear and tear with coffee cups, plates, etc. I sanded between coats and applied four coats in total.
Step 10: Cut Pieces to Length for Steel Table Base
The bases are made from 16 gauge 1" square steel tubing and ⅛" steel flat bar. The legs are 12" tall and the stretchers between the legs are 16" wide. I rough cut the pieces then taped them together and cut them to final length. This method, called "gang cutting", helps to ensure all of the pieces end up at the same length. I used a metal chop saw for cutting the steel, but an angle grinder or hacksaw would work as well.
Step 11: Bevel Edges for Welding
This is an important step that I used to skip. Beveling the edges that will be welded helps to provide more area for the weld to flow into, and this is especially important if you're going to grind the welds flush. I used my belt grinder, but an angle grinder would work as well.
Step 12: Weld the Legs to the Cross Stretchers
I used a Lincoln Electric Power MIG 210MP welder set up for solid core MIG welding. I first tacked the pieces in place then ran a full bead on each side of the joint. First, I attached the legs to one of the cross stretchers, creating a U-shaped section. I ground the welds flush after this step.
Step 13: Weld the Two Leg Sections Together
Next, I welded to two U-shaped sections together with the other two cross-stretchers in between. This structure forms the bottom of the base.
Step 14: Cut and Weld Frame Portion of the Table Base
I used the ⅛" flat bar to create a frame, which will attach to the top of the base and will provide a place for the base to attach to the table top. I cut the ends at a 45 degree angle, welded the pieces together, ground the welds flush, then drill holes for the mounting bolts to run through. The holes should be slightly oversized to allow for wood movement.
Step 15: Weld Frame to Base
With the frame and base assembled and the holes drilled, I welded the two sections together. Make sure to clamp these in place so they don't warp due to heat.
Step 16: Clean Surfaces and Apply Finish to Bases
I used a metal patina for my finish, so I had to remove all of the mill scale from my bases so that the patina could do it's work. I used a flap disc on the angle grinder followed by a random orbit sander for this.
The metal patina I used is called Black Magic, and is made by a company called Sculpt Nouveau. First, I needed to remove any oil and dirt from the steel, and I used a metal degreaser for this. Next, I applied the metal patina heavily and let it sit for about 5 minutes. I then rinsed it off using a hose and allowed the bases to dry.
Once the bases had dried, I sprayed a few coats of spray lacquer to seal the bases.
Step 17: Add Plastic Feet to Protect Flooring
Since the bottom of the legs are still open steel tubing, I needed to add something to protect the flooring beneath the tables. These plastic feet are just pressure fit and worked perfectly for this.
Step 18: Drill Holes for Bases to Attach to the Table Tops
I centered the base on the bottom of the table top, marked the hole placement, and drilled and tapped the holes. I tapped the holes in the wood using the Wood Whisperer Thread Taps, and I absolutely love this method for attaching table bases to table tops. It's simple, quick, and extremely strong.
Step 19: Cut All-Thread to Length & Attach to Top
The all-thread I used through the top only came in 36" lengths, and the table top ended up at 29" wide. I cut the rod to length with my metal cutting bandsaw, then ground a taper on the end using my belt grinder so that a nut would thread on easily. A hacksaw and file would be good substitutes if you don't have these tools.
To attach the all-thread, I ran it through and added a ¾" flat washer and ¾" nut on each end. I lightly snugged the rod up with a pair of wrenches, but this is just for show, so no need to really tighten them down.
Step 20: Attach Bases to Table Top
Using the tapped holes I drilled early, I attached the bases to the table top using 1 ½" long, ¼-20 bolts, lock washers, and flat washers. The holes in the base are slightly oversized to account for wood movement.
Step 21: Enjoy Your Finished Coffee Table!
As you can see, I built a pair of these coffee tables, as they're designed to work together but also be able to be used separately. I'm really happy with the way these turned out and they should last many, many years to come. If you enjoyed this project, subscribe to my YouTube channel and check out my website to keep up with my future builds. Thanks!
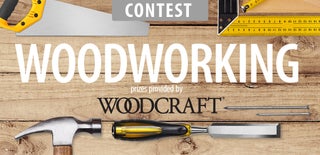
Participated in the
Woodworking Contest 2017