Introduction: Modified Horizontal Bandsaw for Vertical Usage
I recently purchased a WEN 3975 5" horizontal metal cutting bandsaw. This is basically a variable speed metal cutting bandsaw set up like a chop saw. The base and clamp are stationary and there's a lever that allows the head of the saw to rotate between 0-60 degrees. There are other very similar models with different brand names stamped on them that are all probably coming from the same factory. Eastwood and Klutch are two that look suspiciously similar to the WEN.
The problem with, or limitation, of these saws is that they do not work in the vertical position. Using a metal cutting bandsaw in the vertical position greatly increases the variety of work it can tackle. There are larger floor models that do work in both the horizontal and vertical position. There are also kits made to convert small portable bandsaws for vertical use. In both cases the user has to bolt on an additional fixture to the saw. I wanted the conversion to be quick and easy. I also didn't want to invest in another tool. So I set about converting the WEN 3975 bandsaw to work in the vertical position. Let's get started!
Step 1: Get Started Modifying!
*Safety first! Let me start by saying that modifying a power tool to be used in a manner in which it is technically not designed for comes with certain risks. Not only potentially injuring yourself, but also voiding the warranty on the tool. I don't want to get all lawyerly or mother hen on anyone here, but use some common sense when modifying power tools. The modification performed in the following Instructable needs to be rock solid and sturdy when complete. Anything less could cause serious injury, so please, take this warning to heart and don't build some shoddy version of what I'm about to show. Also, some photographs are taken with the cover off of the bandsaw. Never operate a bandsaw with the cover removed! People have been seriously injured by a broken bandsaw blade.
_____________________________________
Okay, warnings aside the first thing that needs to be done is to remove the pin that prevents the saw from going full vertical. And here's another warning... The saw is imbalanced. So when the pin is removed and the head tilts back, it can potentially tip far back enough to flip over. Keep this in mind, so work on a larger table, the floor, or have the base of the saw bolted down before removing the pin.
After I removed the pin I noticed the saw rotates further back then needed. I had to come up with a way to hold up the head vertically. At first I thought about stuffing a piece of wood or hockey puck under the bottom to keep it from tipping too far back. The problem is that I'd forget to do this at some point, or someone else in the shop would forget or not know, and soon enough the bandsaw would end up on the floor. Also a piece stuffed under the end wouldn't be secure enough when using the saw and pressing material through the blade. So I needed to hold up the head in such a way that was permanent and safe. I also wanted it to be adjustable.
This is when I took the plunge and drilled two holes 3" apart into the bandsaw frame. The casting is aluminum so it's very easy to drill. The black line in the photo is a reference for where the cover sits when installed. I used a 3/4" wide plate with some M6 bolts tack welded to install on the inside. The weird curve was ground to avoid the power cord that runs inside the case. The angle iron is 11.5" long with matching slotted holes drilled in for fine adjustment. Once installed, adjust the saw blade plumb and tighten down the M6 nuts.
Step 2: Building the Table
Once the head of the saw is sitting vertically I moved onto building a table. Unfortunately I didn't take too many pictures in this step though it's basic welding construction. This table is built using 1" square tubing. I had a piece of scrap plate that was the perfect size for this project. It measures 19-1/4 x 10-5/8, and is 3/16" plate. This is a slightly random size, but it works out very well. The 1" tube frame is 1/2" longer in both directions which allows the frame itself to be 1/4" wider/proud of the plate. This is because I wanted a perfectly square frame and I didn't want to spend time cutting and grinding the plate. The only modification to the plate I made was to cut a slit in it to accept the blade. Yes, the frame is cut underneath. I thought about having a bolt on plate to support the cut frame, but it was very rigid itself after being cut.
The trick to this table is the 1x3" piece of tubing that gets clamped in using the stock clamp that comes with the saw. In this case, the 1x3" tubing is 5-1/2" long. Add one inch for the tubing above and 3/16" for the plate. I also added an angle brace support coming up to meet the table.
I supported the opposite end of the table with some adjustable legs. The legs are made up of 1/2" threaded rod with a nut welded to the bottom. Then I welded in some couplers under the table in the corner to receive the threaded rods. The additional nut serves as a jam/locking nut once the leg is adjusted. The legs can be adjusted the length of the coupler.
Step 3: Building the Fence
Once the table was completed, I decided to build a fence for it so I could then rip pieces of steel or aluminum down to size like a mini table saw. The fence consists of three pieces of angle iron and is fully adjustable. The pieces of angle iron are secured using 1/2" bolts and nuts. The far side is a fixed hole. The other side has a slotted hole for the clamp. The T-handle is made up with some threaded rod welded to some round rod. This threads through a coupler and presses against the angle iron that rides in the slotted hole.
Why didn't I just weld the fixed side? Well, in my experience fences never stay true over time. In my opinion, it's easier to have it fully adjustable. The nut on the fixed end is very tight and it would take a lot for it to come loose. I also used the angle grinder to cut a line on the small piece of angle iron on the fixed side at 90*. So if the fixed side ever gets out of whack I'll be able to see that with the reference line. See the photographs for more detail.
Step 4: Enjoy the Saw in the Vertical Position!
Here are some more pictures after a quick bit of paint on all of the pieces. When not using the saw in the vertical position the saw can easily return to be used horizontally. Simply unclamp the leg and guide the table out through the slit for the blade and you're done. The piece of angle iron on the back stays with the head. The head being able to tilt full vertical also helps with loading material into the clamp when the saw is being used horizontally. When using the saw vertically the trigger handle switch needs to be held down for the saw to run. To do this I simply use a small quick clamp to squeeze the trigger switch.
The table works great! It's awesome for coping corners on angle iron. Ripping down plate is so simple now and the pieces come out super straight too. It was definitely worth the effort to make this modification.
That's it! I hope you've enjoyed this Instructable! Thanks for checking it out! Please vote for me in the metal contest! I'd love to have a new welder or brake (or any of the prizes!), but I desperately want a robot t-shirt! To vote for this Instructable, click on the little orange banner in the upper right hand corner. Thanks! :)
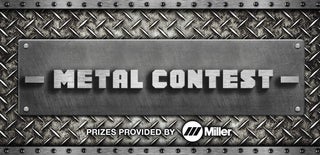
Participated in the
Metal Contest 2017