Introduction: Myford ML10 Lathe Headstock Pulley Lubrication for Backgears
The Myford ML10 (and some ML7s?) have an oil nipple on the alloy pulley fitted on the main spindle. This only needs lubrication when the backgears are in use (eg for threading). At last, I believe that I understand how it should be done properly and I now have an oiler which works well. This Instructable shows the process.
Page 6 of the "Myford ML10 notes on Installation Operation Maintenance" (document Nr. 743D) states:
Headstock pulley - Lubricate with oil gun every 4 hours when backgear is in use.
- The next step shows my way of doing this successfully.
- The following step gives details of how I modified a grease gun to make the task possible.
Perhaps it is worth pointing out that the oil nipple is an OIL nipple not a grease nipple, despite its superficial similarity to a grease nipple.
Step 1: Ensuring the Pulley Is Fully Oiled
- My method starts by pushing some folded kitchen roll paper underneath the left-hand end of the alloy pulley. This will show clearly when the oil injected into the nipple at the other end of the pulley, has reached this end. The drops will drip down onto the kitchen roll and be clearly visible. The clean kitchen roll is shown in the photo.
- Like most oil guns, my modified gun can let a few drops of oil escape from around the nipple. To catch these drops, some kitchen roll is pushed around the nipple.
- The oil gun is then engaged and pumped, while looking at the kitchen roll under the left-hand end of the alloy pulley. Eventually, oil will start dripping onto the kitchen roll, and lubrication can then stop. A torch illuminating the kitchen roll, helps to see this clearly.
Step 2: Modifying the Grease Gun.
My (ancient) grease gun, had a 'socket' screwed on to the working end. This socket is visible (detached) in the photos and is now redundant - being replaced by my longer extension. However, the whole spring-loaded plunger had far too large a diameter for it to properly engage with the oil nipple. It fouled on the gear wheel (bull wheel) and did not let the gun have a straight alignment with the nipple. Even if the 'socket' had been properly shaped to mate with the nipple, the misalignment would ensure that oil would squirt out everywhere and that no pressure would build up to push oil into the nipple.
The photos show the brass extension which I made. The rough dimensions are also shown. The main channel was drilled right through with a 1.5mm drill bit, which was just long enough to do the job from one end, without having to flip the workpiece around. The oil nipples seem to be 4.66mm in diameter and I hoped to make a slight taper on the working end of my extension (I'm unsure how to do this!). In reality, I used a standard 4.5mm drill bit mounted in the tailstock and drilled a 3mm deep recess. When I tested this (on the tailstock oil nipple), it worked pretty well, so I stopped!
I could not identify the required thread form (I would not have had a suitable die anyway). To form the small thread, I had to grind a tiny threading tool which I mounted in the tool post, then set up the change-wheels to form a 0.8mm pitch and then did the whole thread by 'hand' using my Spindle Handle (see another Instructable).
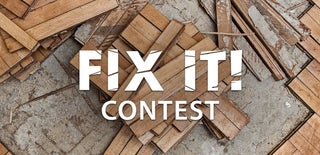
Participated in the
Fix It! Contest