Introduction: New Life for Used Orbital Sander
Just a short one today.
I've had a workshop up and running in some form or fashion for about 20 years now and let's just say I've been through my share of tools. Hammers break, squares bend and all sorts of blades get dull... that's to be expected. Beyond that, I've killed off a number of handheld sanders as they're always needed to hide my mistakes (RIP to the Craftsman, Dewalt, second Dewalt, another Dewalt and a case, plug and several pads on the Festool). Even with changing out the braking rings on the Dewalts, sooner or later they all give up.
Which brings us to the Festool ETS-150. Every Festool product is a serious investment and I've made sure to replace the various components on them as they've worn out. In particular, the foam pads that hold the hook & loop sandpaper in place that have a finite lifespan. The hooks start to degrade, the foam begins to warp and in the current case the plastic backing began to crack.
I've often thought that the used pads, which are too weak to take the energy from the motor could be handy in hand-sanding flat areas of my projects, especially the light work required between coats of finish. Since I had a few minutes to spare, I finally turned a matching knob from a bottle stopper blank.
Supplies
Random Orbit Sander
Lathe and 4-jaw chuck
Handheld drill
Bottle Stopper Blank
Friction polish or pen/small project finish
Step 1: Prep Work
The Festool ETS sanders use foam backing pads which can be quickly removed with a single bolt at the center which is for users to adapt the flexibility of the pad to the job at hand and also lends itself to attaching a hand hold. Most others use a ring of smaller screws so with some adjustment this could easily be adapted to any manufacturer; please let me know your results if you try it.
I decided on a simple round knob so I could let it slip and spin in use, but a rounded square or computer-mouse-like shape would probably work as well.
Use the included allen wrench to remove the bolt and pad from the sander, mark the center of your turning blank and round off the edges. I used a 1/4" bit to drill the pilot hole since I didn't have something on hand to match the standard M8 threads. From there, attach the bolt to the blank, either with a tap or brute force.
Step 2: Turning and Finishing
I used the detail jaws of my chuck to hold the end of the bolt and applied some pressure with the tailstock to hold the blank in place on my lathe. Granted, there are fancier ways to pull this off but I didn't have the whole weekend to adapt a jig to hold it.
Starting with a gouge to round the blank over, get the sides even and then move to round/flat scrapers to complete the profile. I got as close as I could to the tail stock and left the hole as-is so nothing got damaged.
Once the profile is acceptable, sand it to a level that you like; between the sharp tools and hard grain of the cocobolo blank, I started and ended with 600 grit and called it a day. There were no tool marks to be seen and even with no added finish it held a nice, warm shine.
To further protect the wood from damage in use and from hand oils, I added a few coats of friction pen polish (shellac/oil/wax mixture) and a top coat of Renaissance Wax. Once dry, remove from the lathe and extract the bolt. Reattach it to the sander and give it a try.
And that's about it. Get a more convenient way to finish-sand your projects, gain an excuse to warm up your lathe and save another accessory from the trash bin.
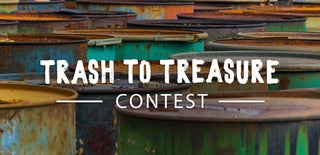
Participated in the
Trash to Treasure Contest