Introduction: Newtons Cradle With Edge Lit Explanation
I've been wanting to build a Newtons Cradle for quite some time now, and with the Science Competition in mind I thought of building one, but I wanted to make it a bit different as there are quite a few DIY cradles on the Internet.
My plan is to not just to build the cradle, I wanted to build it with an Edge Lit sign in the base, the sign will give an explanation of Conservation of Momentum and Energy.
The Edge lit sign will sit centrally under the line of the chrome steel balls and should make for some interesting patterns of reflected light(In Theory).
We will be using Fusion360 for Designing/Sketching 3D printed components and Vetric Cut2D to create the slots in the base, the framework will be built using 8mm chrome round bar with 3D Printed Joints, Cast Acrylic will be used for the Edge lit Sign.
The Chrome bar is from an old 3D Printer strip down.
The LED set up is really simple and inexpensive, its a 50cm strip and it comes complete with battery pack and a remote, its easy enough to wire in a permanent 5v power supply if needed.
We are using a CNC machine for cutting the slots, the correct Personal Protective Equipment should be used with CNC Operations:
Eye protection:
Ear Protection:
Dust Mask rated for the work you are carrying out.
There is no design as such, its just an idea, lets see how far we get with it.
Supplies
Timber off cut 250mm x 90mm x 20mm(Any wood will be ok and size to suit your build).
6mm flat router bit
Carbide
Acrylic(Cast) 190mm x 40mm x 4mm
8mm Chrome round Bar( To suit)
6 x25mm Chrome Steel Balls
LED Strip with battery pack and remote
Sea Fishing Line to suspend the balls
Epoxy Glue
CA glue
3 x AA batteries
Step 1: Creating a Base for the Newtons Cradle.
The initial step is to create the base, the timber I used was just an off cut of cheap spruce 20.02mm thick, once cut down to size the piece was then secured on the CNC spoil board.
Vetric Cut2D was used to create the slots, input material dimensions and depth into the relevant boxes, and the start point will be the centre of the piece(Zero).
I created a rectangular slot 190mm x 4mm and used a 1mm bit for tighter corners, in the Toolpath section the depth of cut was set at 5mm this is enough to sink the acrylic into the base.
With that cut complete it was time to flip the base and create another slot, this slot is for the LED strip, bearing in mind our first slot was 5mm thick and the stock is 20mm thick, we make this slot 12mm wide 210mm in length and we need the slot to cut through the stock at one end for the LED strip cable.
In the Toolpath section we make the depth of cut 15mm this will cut all the way to our initial slot.
With both slots cut we can now make a piece of wood for the LED strip, cut a length of timber to populate the slot allowing for the led strip, doesn't matter if its a bit shallow or proud, its not seen, but flush If possible, this was a snug fit so no glue needed.
I routed the edges of the base then sanded, waxed and fitted 4no small suction pads, that's the base finished.
Step 2: Creating the Cradle Framework.
To create the cradle and for the main structure, I had some 8mm polished chrome bar from a 3D printer I'd stripped down some time ago, initially I thought a bit over the top but with 6 Chrome balls swinging about the frame needs to be sturdy.
I needed to create some 3 Way corner joints for the top angles of the frame, this was done in Fusion360.
Create a sketch, pick the top plane and create a horizontal centre rectangle 30mm long 15mm wide, create a 2 point rectangle vertically from the right hand corner of the first rectangle, same dimensions, then extrude this sketch to 15mm, finish sketch.
We now create a 2 point square from the corner 15mm x 15mm and extrude this 15mm.
Now we have the corner piece we need holes for the bar.
Create sketch and click on the first face to create the hole, it should snap to the centre if it doesn't, create a corner to corner cross, the circle will now snap to the centre, make the dimension of the circle 8.03mm for a snug fit with the bar, and extrude 28mm, same for the other 2 faces.
At this point I highlighted the the whole corner piece and fillet at 0.2mm just to round of the edges(Optional).
Step 3: Creating the Base Corner Angles.
These angles need to be quite sturdy as they hold the cradle framework in place, there is no room for flex on a Newton Cradle so rigidity is the key.
With that in mind I designed corner angles with a gusset.
Create a new component in Fusion and pick the top plane as our sketch surface.
I created an "L" shape right angle, thickness is 5mm for strength and extruded to 12mm then created a circle on the corner of the angle and offset it to 5mm then extruded the angle to 12mm and the extruded the circle another 12mm or so for rigidity.
Unfortunately I forgot to take screen shots of this process, but in the Cura screenshots you can see the Angles.
Step 4: Creating Ferrules for Suspending the Chrome Balls
Thinking cap was on again, the balls need to be in line and all at the same height, some way of adjustment was needed.
Not only did I want the balls in line and the same height but I also wanted to alter the distance between the balls to see what difference it made(From a scientific point of view) if any.
I came up with a 3D printed Ferrule with a 2mm hole leading to a 3mm hole going through the radius of the ferrule, the ferrule would need to have friction to stop horizontal movement and this ferrule would also be used for tension to align the chrome balls.
See the screen shots for the ferrule, had a couple of attempts initially which failed, its just extruded circles, extruded to 5mm then the holes created on the radius for the line to go through, and a 0.5mm fillet on the 2mm hole to stop the line from snagging.
The final ferrule design works well and ball alignment is made considerably easier, as the alignment is a crucial element.
Step 5: Making the Chrome Ball Line Attachment/connector
I needed some way of attaching the balls to the line and came up with a 3D printed component using the radius of the ball, then using epoxy to secure.
In Fusion360 Create component, then select the front plane to create our sketch, the steel balls are 25mm diameter so we need to create a sphere as our template.
Sketch a circle at 25mm diameter the sketch a line top to bottom within the circle and then trim one half of the circle, use revolve to make a sphere as our template, or you could just select sphere and make it 25mm
Create a sketch using the centre plane within the sphere, and from a front view, use the spline tool to follow the radius of the sphere, when you are happy with the the size of the radius line, off set it to 5mm or so and then connect the ends, select extrude and in the direction box select symmetyr, extrude to say 2mm overall this will be 4mm.
Create an off set plane and raise it 5mm above the extruded arc, create a sketch using this place and make a circle at 3mm, extrude it -6 and join to the existing extrusion, now create a sketch and using the top face of the newly extruded circle, create a 1.5mm circle and extrude straight through, and then flip, create another off set plane to create a 2.5mm circle and extrude to enlarge the existing hole, depth of 2mm or so, this will house the knot for the fishing line which will suspend the Chrome balls, this knot will be secured with a spot of CA Glue.
Step 6: Creating the Edge Lit Sign.
The design for the Edge lit display is created using Vetric Cut2D.
The slot size is 190mm Width x 40mm height x 4mm thickness and we are using cast Acrylic an off cut I already had.
In Cut2d input the dimensions etc and the starting point will be left bottom corner(Zero)
Create a rectangle 190mm x 40mm and radius the top corners @10mm using the Text function, the text can be written line by line and then spaced out to suit, leave a 5mm gap at the bottom of the acrylic, this is where it fits into the slot in the base.
The text needs to be flipped horizontally using the mirror function as we are engraving on the back of the acrylic leaving the face of the acrylic smooth.
For the engraving, I'm using a drag bit with a carbide tip, the engrave tab is used for this purpose, its pressure rather than depth for the cut, and this is set at 0.2 the drag bit is spring loaded so its really trial and error, bring the bit down to the acrylic, apply downward pressure, all its doing is scratching the surface of the Acrylic so the router isn't switched on in this operation.
Step 7: Finishing the Framework and Securing to the Base
I fitted the 4no corner pieces first, drilled then screwed, this gave me the length and width needed to cut the steel bar, top corner angles were fitted, and a height of the frame was best guessed, it turned out to be ok.
The ferrules for line adjustment were added 5 each side, nothing was glued in place at this point.
With reference to the chrome balls and the line connections, I used fishing line 15lb I think, created a loop and pushed this through the top of the connector, tied a double knot, pulled it really tight and sank it back into the hole, cut the loop of and used CA glue to secure in the hole.
Using 2 part 5 minute epoxy, the connectors were fastened to the balls and left to dry.
The final process is to fit the balls and align above the edge lit sign, the line was passed the ferrule and then a knot tied and sunk back in to hole using CA Glue, tension is by turning the ferrule on the bar.
Step 8: The Big Switch on and Summary
With everything in place and batteries fitted for the LEDS, and chrome balls aligned it was time to (A) see if the balls did what it says on the tin, they did, alignment is crucial, but once tweaked they clacked happily, I was happy with that part of the remit.
(B) Switching on the LED's and using the remote it did indeed light up the explanation, and on a glass coffee table it did indeed give reflections, it didn't reflect like a mirror ball and light up the whole room, but with the lights off in the room there was definitely light activity on the ceiling , I was happy with the overall outcome, its just a bit different from the norm.
To Summise:
I would like a better way of securing the line to the balls, the connectors are not symmetric.
I would make the frame higher,
A nice science project using Fusion360 and Vetric Cut2D Using 3D printed components and parts rescued from an old 3D printer and offcuts of wood and Acrylic.
I hope you enjoyed this Instructable and thanks for looking
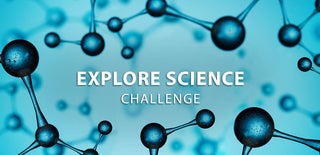
Runner Up in the
Explore Science Challenge