Introduction: NiChrome Hot Wire Cutter for Acrylic
Acrylic sheet is always a go-to for me when building something. It's relatively cheap, durable, and able to be used for a variety of applications. For the past few years, I've been using a Dremel rotary tool to cut the plexiglass, which gets messy, takes forever, and doesn't provide very clean edges. This project seeks to provide a better way of cutting parts out of plexiglass.
When I was an AiR at Instructables, I was spoiled with laser cutter. When I thought of how the laser is actually "cutting" the plastic, I realized that in reality, the laser is heating up and vaporizing the plastic, only a very small amount at a time. After doing some quick research, it became apparent that a nichrome wire could be made hot enough to vaporize the plastic, and was easily available in extremely thin diameters. I've deemed this project a "vocutter", or Vaporization On Contact, (VOC) Cutter because of this cutting method. I'm very happy with the results that this cutting method produces, and will be using it in the future unless if someway by the grace of God I get a laser cutter.
(What is this!? Instructables has a contest with a laser cutter as a prize!? Vote for me if you like this project. Thanks!)
Check out the next step to see what it looks like to cut things with a Vocutter, or head to step 3 to get started on the build!
-
UPDATE 5/7/14: I added a foot switch which greatly improves the cutting process! See step 6!
Step 1: Videos!
There are two videos here. The first one shows off different materials that can be cut with a nichrome Vocutter, and the second shows my first attempts at cutting designs out of plexilglass that I would have otherwise used a laser cutter for.
Step 2: Tools and Materials
A variety of tools and materials are needed to complete this project:
Tools:
- Drill
- Dremel Rotary Tool
- Tap set
- Car battery charger
- If you don't have one laying around, Harbor Freight is probably your best bet.
- Hot glue gun
Materials:
- 1/2" thick particle board
- 1/2" wide steel bar
- Nichrome wire
- Easily available online in every thickness. 30 Gauge worked best for me for this project.
Let's get started!
Step 3: Build: Frame
We need a sort of "C" shape to run the wire from one side to the other. The wire will get charged with electricity and become hot, and by moving our material through the wire inside the "C", we will be able to cut things.
My frame is cut from 1/2" thick particle board I had laying around. The gap between the two bars is roughly 5". This distance was determined by running tests with different power supplies beforehand. The depth of the C-frame is about 8 inches, to give some room to work the material. The thick part at the back is about 3" deep. I made it that depth so that if I want to add any improvements in the future, I'll have some room to mount components. Cutting was done by hand with an oscillating cutter.
I later cut a Back Plate roughly 5" wide out of the 1/2" thick particle board, and glued it to the C-frame. This allows the cutter to sit horizontally, and be clamped to a table either horizontally or vertically. A small piece of 1/4" thick plywood was cut to act as a Base Plate to help keep any materials level during cutting if necessary. See the images notes in the last picture.
Step 4: Build: Metal
Two 3" sections of 1/2" steel bar stock were cut using a Dremel Rotary tool.
1/4" holes were drilled and tapped (threaded) so that screws could be threaded into them, and a nut could be used to hold the wire in place.
Two 1/8" holes were drilled on each piece so that small screws could be used to attach each metal piece to the C-frame. Be careful to attach each metal piece so that they are parallel, and the wire will run as close to a 90-degree vertical as possible.
I think the pictures do a good job of showing what needs to be done in this step.
Step 5: Using the Vocutter and Conclusion
Cut and attach a piece of nichrome wire in between the two screws on either side of the C-frame. A car battery charger is plugged into the wall, and the positive and negative leads are attached to each piece of metal on the C-Frame. The wire then becomes hot, and the settings on the car battery charger can be adjusted to get the best results.
Cutting things like paper, foam, cardboard, etc., is as easy as gently guiding the material through the wire. There's virtually no resistance.
Cutting things like wood and plexiglass can be a little more difficult, and especially with thicker materials, dragging the material along the wire eases the process substantially, as the hottest part of the wire is able to contact the material. Dragging it along the wire and lose some of the accuracy in the cut, but as long as you're careful quality results can be had.
I've attached pictures of some of different materials after they've been cut. 1/16" Plexiglass, 3/32" Plexiglass, 1/8" foam rubber, and 1/4" birch plywood. There are also pictures of designs I made in Inkscape, as I would to be laser cut, but cut with this method instead by printing out, cutting, and taping them in place. The pictures show how close I was to the actual design, and all they need is some sanding to clean up.
-
Thank you for reading! If you have any questions or comments, please leave them in the comments! I enjoy reading them. I look forward to using this as a new tool to produce higher quality projects more quickly.
Step 6: Addition: Foot Switch
I added a foot switch so that the device could easily be turned on and off while cutting. This was done using a short section of 2x3", and some 1/4" plywood I had laying around. A simple pushbutton switch from Radioshack was found and wired up. The entire process only involved some drilling, cutting, and soldering. A drill, oscillating cutter, and soldering iron were used. Take a look at the pictures, and the video to see it in action.
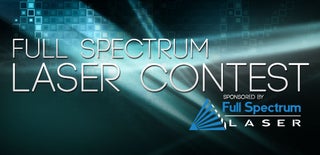
Participated in the
Full Spectrum Laser Contest