Introduction: O2 Splitter Valve
I was involved in making a very basic Oxygen Splitter. What a oxygen splitter does, it’s basically a manifold that supplies regulated oxygen to multiple patients that require oxygen, where each port the flow rate of oxygen is adjustable. This design would be for hospitals that do not have the infrastructure for supplies and resources for inventory. What was required, is a design of medical equipment that could be printed where the facility would only require a 3D printer, filaments, and a dependable power supply where they could print their required instruments.
This would keep inventory costs down, and create what is needed, when needed.
In development, I had done a very simple O2 splitter, during development, I came up with (2) different designs, one, a very simple design, which is what they required. And this design, which was more involved that had better control.
This O2 splitter would be used on (2) separate patients with only one regulated O2 supply with each patient having its own separate flow controls.
I had printed a model of the earlier proto-types, I had since revised and updated the files. As you will see the revisions numbers (R_) on the file.
Supplies
Resources and Materials used;
- AutoDesk Inventor (used to design the O2 Splitter)
- File (See File Picture in Step 1 - Assembly and Step 6 - Files)
- Simplify3D (used to program for printing)
- FlashForge Creator Pro (2 head printer)
- 1.75 Filaments (ABS) - Translucent Blue - Dark Green - Yellow - Red
- (2) Lower O-Rings -Teflon, virgin
- (2) Upper O-Rings - Teflon, virgin
Step 1: Assembly
Shown is the assembly unit as well as the files used.
Notes:
1.) Instead of using ABS, next time, I would chose a carbon fiber filled filament because the quality is a lot more sharpe, durable and more defined.
2.) On the settings on the printer, after the first layer is laid down, I’d lower the temperature on the printer platen, to reduce thermal distortion.
Step 2: Body Construction
After going through a number of iterations, (a few more is needed such as addition internal voids to eliminate print time and material, which I’ll get to later)
On SECTION A-A, you see the channel cut away view for the outlet. Along this view, you see the dimples, for the flow control dial lock. This is done for precision and repeatability. You can also see the groove to restrain the dial movement to insure a workable position.
As well as the having and upper and lower O-ring grooves for sealing and preventing O2 losses.
On SECTION B-B, you can see the flow channels as well as the voids, (to reduce print time and material usage).
The hex opening, that is shown, I have a standard FNPT hexagon plug that I insert. It has the thread geometry on it, and the hex I use in case I need to reference thread start. I do this to cut down design time.
I then print the assembly as one piece.
Step 3: Dial Assembly
From the drawing, you see that there are (2) colors, since the printer can print multi-colors, this works great for descriptive pieces.
- On the dial itself, it has the red swoosh, this will work in tandem with the cover viewing port for a visual on the air flow.
- Another point, is the pin to position and restrain the dial for flow control. And along with that, is the detent for positive lock on the flow dial For repeatability.
- If you look at the small penetrations, they are triangular, for printability, as the flow dial is moved to increase the flow, more openings are presented.
- And the center point of the dial, there is a detent, this serves a dual purpose
1.) to lock the cover in place and 2.) have the cover retain the dial in place - and finally, the dial has partial scallops for easier grip
Step 4: Cover Assembly
On the cover assembly, You’ll notice the arrow direction thickness gets larger towards the arrow head, this indicates, if you turn the dial in that direction, that will increase the flow rate.
Along with this, there is a small dimple in the middle, this will lock into the dial, keeping the dial in place as well as the cover locked.
The opening will display the flow going through this outlet port to the patient.
Tip: I didn’t do it to this printed model, with the material being ABS, what I would do to the next model, is to make a vapor chamber, with acetone in the basin and I would hang the translucent covers in the vapor chamber. What acetone does, the acetone vapors would wash and mend the outside layer, and when removed from the vapor chamber, it would be a clearer cover, as well as a stronger outer coating to fix and strengthen the stratifying layering effects from the printing process.
Step 5: Fully Assembled Oxygen Splitter
As shown, this is the fully assembled O2 Splitter.
The video shows the assembly from an earlier model. This video is only for demonstration, I didn't trim the flashing off FNPT. I would revise the material if I made one out of a different material.
Step 6: Files
Attached are the Inventor CAD files shown in Step 1, where it you can modify as needed.
Along with the CAD files I included *.stl print translation files unused in the programming Simplify3D software; O-Body-Threaded.stl, Dial Assem-R7.stl and Cover-Assem-R8.stl
Enjoy!... And feel free to comment.
Attachments
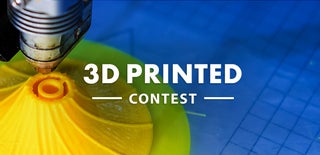
Participated in the
3D Printed Contest