Introduction: Country Garden Shed
Introduction
This is a document taken from concept to a finished project.
About 3 years ago, my significant other (Sheila), wanted a garden shed, to relieve space in our garage. We spent quite a bit of time looking at plastic, prefab construction kits, prebuilt from big box stores. The Garden sheds available either looked plain, cheap or just didn't fit our medley of garden themes.
Our garden, thou not large, it does have different themed areas that consist of Greek/Roman, Oriental and an English country side. This shed needed to compliment them all because it will be the center of it while at the same time not clashing with the different themes yet at the same time not over doing it with too much going on at once.
As the Garden Shed developed, it became somewhat, whimsical, yet subtle.
There were also some requirements that were put in place before hand,
One of which, it was to be as maintenance free as possible (No Painting)
Other requirements included;;
- Cement Floor
- Cement Curbing for wall sill plate
- Large enough door to get lawn mower in (push type approximatly 36" wide)
- Possible Expand door way to double door.
- All siding and trim was to be vinyl.
The construction of this project was made with one person, (myself) with the project difficulty on a scale of 1-5 would be a 4+.
Step 1: Tools
I was fortunate to have a rather complete arsenal of tools. The tools listed is what I used, of course one can improvise with what you have.
Step 2: Development the Basic Design and the Location for the Country Garden Shed
Sheila made a hand drawing of the outline of the shed as well as the color scheme of the shed of what she's looking for.
We then picked out a location that was basically between our Greek/Roman and Oriental themed areas that can still be seen by most of the rest of the back lawn/garden.
And then we marked it out with flour. After some slight placement changes we made a sketch of our property lines and the location of the Garden Shed, with some basic dimensions and went to our local Village government office to secure all the permits and to ensure we followed all the zoning requirements. (see links page, Village of Bellevue)
Your local community and government requirements will vary.
Step 3: Preliminary Development of Country Garden Shed (Cement Work)
Initially I had planned on a cement slab. (Alaskan Floating Slab to be more precise, see link on link file), with a cement curb for the walls to sit upon, but that changed soon after I started construction. When I started digging, there was a lot of clay in the soil. Clay, like sand is unstable and make for a poor substrate for foundations. It will not support the building and foundation and will basically move, sink and displace the soil around it with the weight of the building.
What I did was come up with a design that had pilings going down to a more stable substrate that will support the foundations. Rebar and mesh was used to reinforce the concrete.
For the cement work, there will be (3) pours; 1st the foundation and pilings. The 2nd pour will be the walls and the 3rd pour will be the floor.
We'll see how this works out.
Step 4: Preliminary Development of Whimsical Garden Shed (Shed)
I started to develop the shed itself, for a number of reasons,
- To get a basic design for the aesthetics aspect.
- And to get a Bill of Materials going.
The initial total budget for materials would start at $4,000.00-$4,200.00, but with the changes the final number was just over $4,700.00. That's a big change, but the change was purchasing items such as the Copula, as well as the keypad locks. Which these extra items, it did work out better. Also with those numbers, I did have extra material.
A complete Bill of Materials (BOM) is listed later on. And this would include links.
I began with the what I had, and when I completed the basic framing and laid out the OSB, it looked rather plain. So I extended the eaves to 12", it still did not incorporate or mesh well with all (3) theme criteria's.
- It had the scroll work under the gable ends that would work with the Greek and Roman theme.
- A 12 - 12 roof pitch would work with the English Countryside Theme without too much of a stretch.
- It was the incorporating Oriental theme that was the problem.
After looking at Oriental architecture, I thought about incorporating the Pagoda's roof line, so I did a little flair at the eaves, which seemed to compliment all the themes.
I then placed the Copula at the top, to get an idea of the scale of the Copula. Unknowing to me, Sheila already purchased a Copula.
Step 5: Layout and Preparation of Area
With the site already selected, I measured and outlined the building with flour.
After which I staked it out, and started digging using a transit to ensure I don't dig more out that I need to.
The Hole will be approx. 12-14" deep leaving plenty of room for the cement forms (About 18" larger than the footings.
The Building will be 8' x 10', Footing size, 8'-9" x 10'-9", over all hole size will be approximately 9'-6" x 11'6". I transit the site as I dug to ensure depth and grade is where its should be at.
After which, I auger out the holes for the pilings, The pilings will be close to the center of the wall.
I then laid the landscape fabric with landscape staple to hold it in place. I then cut an 'X' where the pilings forms would go. The piling forms are cut 6"-12" long depending on the grade for the drain tile. I then inserted the forms into the piling hole approximately 2-5" so that the top of the forms would be just under the foundations. I used the transit to ensure of the position. These forms will prevent the piling holes from filling up with gravel when added.
As the picture shows, we had a lot of rain after I started this phase. Due to the clay, it took over 1-1/2 Months for it to fully drain off or evaporate. Even when I pumped the water out, the clay soil had so much water saturation, as soon as I pumped it out, it started filling in again. Ignore the 6"x6" wire mesh in the middle, had no where else to put it and still be out of the way.
I then laid the 4" perforated cloth covered drain tile around the pilings, connecting them in the lower corner with a 'Tee'. From there I routed it to our underground rain reservoir where we use to water the garden during the dry spells.
After which, I used added 4" of 3/4" crushed stone for a substrate. (Approximately 1-1/2 yards). I then repeatedly packed it down with a 8" x 8" cast steel tamper. Using a transit and top dressing it where needed.
I then laid a vapor barrier throughout above the gravel. Cut openings where the vapor barrier passes over the piling holes. And ready for the footing forms.
Step 6: Footing/Foundation
With the substrate level, with string, I laid out the outer and inner footings form location. Using 2" x 4", the outside footing dimensions being 8'-9" x 10'-9". the inner footing dimensions being 6'-6" x 8'-6".
I then staked the forms on the outside of the outside forms and on the inside of the inside forms with screws, to insure they don't move or lift during the pour. The screws were only partially screwed in because I then took the transit to ensure the top of the forms were level. I'll fill it with cement to the top of the forms. And start off with everything level.I then back filled the forms (opposite side of the cement) with dirt or gravel to ensure the forms will not move.
And then I screwed 1" x 2" spanners to connect the outer form, with the inner form, to add ensureance that the forms will not move.
I again verified the top of the forms with a transit to ensure its level.
After which I then cut rebar approximately 42" in length for each piling, and then bend 3" on one end, this will go into the piling hole.
To bend this rebar, I used (2) 3/4" water pipe, approximately 3' long. I secured one pipe (in the pallet where the bagged cement is on) so that it would not move. I slipped 3" of the rebar in this pipe, I end slipped the second pipe of the exposed rebar until both pipe meet. I would used this as the leverage to bend the rebar.
I also used this technique when I laid the rebar in the footings and wall for the corners.
I then laid out (2) rows of rebar in the footings, spaced about 6" apart. Using small stones to keep the rebar suspended. I will also lift up the rebar as I'm pouring the cement, to ensure there are no air gaps under the rebar, or that the rebar didn't sag down to the substrate.
I then wire (I used 0.030" wire) the rebar in place as needed, by the joints where one rebar meet the next rebar, making sure there is at least 6" of overlap.
I'll be using a total of 2-1/2 yards of cement, in (3) different pours. Because of this, low volume, it was better to mix it, that get a ready mix.
I used a 3-1/2 Cubic foot cement mixer and used (1) bag of 80 lb bag of cement per batch.
And then used a 5 gallon bucket to transfer the cement from the mixer to where it's needed. I had more control this way.
As you get to the pilings, fill the pilling up to the top of the forms. and then insert the piling rebar made earlier making sure the bent part goes in first 'puddling' as you go along. Puddling is when you move it in, pull it out a little and stick it in farther and keep doing this until you're at the depth you require with 6"-8" of rebar exposed above the form. 'Puddling' helps eliminate air gaps in the cement.
As you're pouring, it's also a good idea to tap the forms with a hammer, this will also help eliminate air gaps in the cement.
When the cement is filled to the top of the form, Trowel off level, but not necessarily smooth. Having a somewhat of a rough surface will help mend the wall to the footing, but still smooth enough were the wall forms will contact the footings throughout on the second pour. I waited for the footings to firm up (week would be fine) before I started the walls.
Step 7: Setting and Pouring the Shed Walls
Using 2" x 12" as forms, I set the walls up. With the foundation level, it is just a matter of laying up the boards on top of the foundation. I started by laying down the outside form. Measuring diagonal corner to corner to ensure forms are laid square.
I still took a transit to ensure the top of the forms are level.
I used ThruLOK Bolts to hold the inner and outer forms together so they would not move and to ensure consistent wall thickness.
I block off for the door opening. This will later be filled in when the floor is poured.
I laid the rebar on top of the ThruLOK bolts and wire them to the ThruLOK bolts as well as the ends, making sure that the ends over lapped at least 6"
I then made a wood 1" x 2-1/2" wooden spanner to connect the inside form to the outside form, and drill a 9/16" hole to hole the anchor bolts in place. The spanners are place on top of the forms on the anchor locations
I then packed dirt and gravel on the outside of the outside form and inside of the inside forms. And run a transit one last time to ensure its level and measure corner to corner to ensure its square.
I begin mixing cement and pouring. Doing the 'puddling' and tapping the forms with a hammer. When the cement reaches to the top of the form, I troweled it smooth.
It was a week before I was able to work on it again, which I cut the ThruLOK bolts with a 4-1/2" grinder and removed the inside forms, Leaving and using the outside forms for the floor by the doorway.
Step 8: Pouring the Shed Floor
Before the pour, I top dressed the floor with 3/4" crushed gravel and packed it down repeatedly with a 8" x 8" cast steel Tamper to bring it to level. Strike it with a transit, and laid the 6" x 6" mesh throughout.
I then made a striker to spread the cement and a bull float to level it before troweling.
As I was making the pour, I would adjust the 6" x 6" wire mesh.
After it was floated, I laid a board across the walls to trowel.
Unfortunately, before I got done, the towns tornado sirens when off where a tornado was sighted less than 5 miles from us, so I left the cement mixer run and checked the weather. After 1/2 hour the sirens stopped, and I had to top dress the floor with an extra 1" to 1-1/2" cement to level the floor out. As you can see the Staging Picture, the sky was relatively clear with just clouds on the horizon.
After the floor set, I removed the outside wall forms.
Step 9: Framing the Wall.
For framing the wall, I constructed the (2) sides and the back wall leaving the front wall to be constructed in place. I did this to make up any dimensional discrepancies that may occur. There weren't any.
First picked out the 2"x4"'s and I cut to length the top and bottom plates and studs out for the wall. I marked the locations of the studs on the plates and laid everything out the them on a flat surface, (on our cemented driveway)
I set a stud and nailed it to the bottom plates started nailing the studs to the bottom plate.
I then position the top plate and nailed the outside studs to the plate.
I checked my measurement, and for square of the wall by measuring both corner to diagonal corner and opposite corner to diagonal corner made adjustment so both measurements are the same. I then nailed the remainder of the studs in the middle.
I again checked for square, made the adjustments until both diagonal corners matched in length and then I nailed a 1'x4" strip diagonally corner to corner to holding it square for me to move and place the wall keeping it square during construction.
I did the remaining side wall and back wall in the same manner. After which I moved the stud walls behind the house to the building site.
I use a chalk line to on the top of the cement wall for the position of the stud wall. and then set the stud wall line up to the chalk line and resting on top of the anchor bolts where I then hit it to mark the location for the holes on the bottom plate. I then used a 3/4" hole saw and drilled out where the anchor bolts mark the sill.
I did this for the remaining walls.
I then laid 5-1/2" x 3/16" Foam Sill Plate Gasket on top of the cement wall where the framing stud wall lower plate rests on.
Step 10: Erecting the Stud Walls
I first screwed in a (2) ground support 1"x4" boards and pounded stakes for these supports to fasten to.
After which I positioned the wall and fasten the ground support boards to the stakes. Then position the wall to the chalk line and snug the anchor bolts.
I check the wall for plumb with a level and made adjustments to the ground supports until the side wall was plumb.
I repeated this with the back wall, and then the remaining side wall. And then to make sure the walls are straight, level and square.
The front stud wall with door will be field constructed. Add another top plate and over lap with adjoining walls at the corners to tie in the walls.
Step 11: Rafter Base Plate/Gable Overhang
To get the overhang on the gable sides, I sandwiched a 3-1/2" x 1/2" plywood between (2) 2 x 4" and nailed together. Using 6" wood clamps to keep the 2x4's straight as I nailed together using 10 Penny x 2-7/8" smooth vinyl coated sinker nails.
I then centered and mounted on the side walls and toe nailed in the stud wall upper plate using 3-1/2" 16 Penny Bright Steel Smooth.
And also added cross bracing connecting the side walls
Step 12: Setting the End Rafters.
Before setting the end rafters I nailed the OSB to the side walls. I did this so I could remove the ground ties and use the scaffolding as well as the space for the rafter notches.
I then cut the remaining rafters (for a total of 16 Rafters) to size using a compound miter saw for the end angles and a sawsall to cut the notches out, I assembled the edit rafter assembly on a flat surface, using a 2x8 spacer for positioned the rafters, and a temporary gusset to hold in place for placement. I used drywall screws for fastening.
I then nailed a blocking cleat to the end of the rafter base plate (over hang) and positioned the end rafter in place.
I then screwed the temporary supports from the end rafter assembly to the rafter base plate. I Used a level to make sure the rafter is sitting straight and plumb, making an needed adjustments.
I toe nailed the rafter assembly to the rafter base plate and also screwed in added a Simpson Strong tie 3-1/4" gusset angle to the rafter and rafter base plate using 1-1/2" External Hex Flange Hex Head Construction screws.
Step 13: Setting the Remaining Rafters
After the end rafter assembly is in place, I then removed the temporary rafter spline spacer. and set in the rafter spline itself and first fastened using 3" construction screw and then nailed it using 3-1/2 16 penny common nail.
With the Spline in place, I placed and fastened the remaining rafters the same way. Starting on the outside wall each rafter is 24" on center. Toenailing the bottom of the rafter with the notch to the Wall Rafter Plate and using the Simpson Strong Ties 3-1/4" Gusset Angle using 1-1/2" External Hex Flange Hex Head Construction Screws.
Step 14: Making and Installing the Rafter Eave Flares
To make the rafter eave flare I had uses a combination miter saw to cut the angles and the band saw for the which I listed below.
I had first drew what looked good in the sketch and then dimensioned it out.in a sketch.
I nested it in a 2x8 Board to utilize the material and then cut out a paper pattern to cut one flare out of a the 2x8's to use as a template to cut out with the Meter Saw. There are (16) required, I made (2) extras for a total of (18).
When I cut these flares, I tried a number of ways, either way is fine. I attached a picture where I cut the long angle (sketch shows it was done with a table saw) with a skill saw and a jig.
I then use a string to align and fastened it to the rafter using #9 x 3 Star Flat Head Wood Deck Screws, I started to toe nailed it also, but changed to screw it in with the same type of screws.
.
Step 15: Sheeting the Roof and Flares.
I used 1"x4" boards for the flare and 4'x8'x7/16" OSB for the roofing. With the roof having a 12 - 12 pitch. I used roofing jacks to nail the OSM near the ridge
Since the 1"x4" boards dimensions are 3/4" x 3-1/2" there's a discrepancy of approximately 5/16" of an inch between the 1" x 4"'s and the OSB. To offset this, I used 8" Composite Shims on rafter to transition the OSB to the 1" x 4" and the OSB matched up to the boards perfectly..
Step 16: Framing the Gable End
Initially I was going to have the cupola as the top vent, so I framed the gable with a stud going down the middle. Later on, we decided to put in a vent on the back gable wall instead because the cupola was not really design as a vent., I didn't care to have a stud behind the vent, so I put in (2) 10" vents on the back gable wall.
I notched out the gable studs to fit the rafters and installed the studs.
Step 17: Hanging the Door
The door was picked up at a resale shop but I had to hang the door. I purchased the frame, but it was decide that there will be no tread plate.
- Installed the hinge to the door.
- I assembled the frame on a flat surface,
- That I laid the door in the frame and marked the hinge locations.
- I then took a 1" wood chisel and chiseled the recess for the hinge in the frame.
- I fitted the door, and then removed the door, and installed the door frame to the building.
- Using shims making sure the frame is square and true and installed in place
- I then installed the door to the door frame.
Now we wanted this door to open outwards, this would add floor space as opposed to have it open inward.
Since it was purchased at a resale store, to have it open outwards, the handle is on the left. It is odd, but its something we can live with.
Step 18: Gable and Eave Trim
Installing Gable and Eave trim.
Because of the eave flares, the Gable end trim had to custom made,
- I used 3/4" x 7-1/4" vinyl boards and temporarily installed them with (2) 2" finishing nails to set them in position and made the adjustments for final placement
- I then fitted the boards at the flare with 3/4" x 11-1/4" vinyl boards in and traced the flare to the roof line and cut them out with a band saw glued them I also cut a small triangle piece and glued that into place. .
- After everything was in place, I fasten them with 1-5/8" White All Purpose Screw.
- I then cut the stock off to the finish length with a skill saw.
Step 19: Installing the Back Wall Vents
- I first Measured out the placement of the vents using the vent backer as a template.
- Drill a 3/4" hole with a hole saw as a starter hole and used a hand jig saw to cut out the penetrations
- Installed the vent backer after tar paper was laid.
Attachments
Step 20: Installing the Gable and Eave Fascia and Soffits 'J' and 'F' for Soffits.
After I finished tarpapering the walls, I then snapped a chalk line for the placement of the soffit trim
Prior installing the soffit, I measured the eave length and cut the fascia from a 5-1/2" x 144" vinyl board.
I used a 'F' style trim against the wall as well at the eave. And Fastening the 'F' trim to each Rafter. After which I installed the fascia to the rafter.
Pretty much following the siding and trim requirements on that are attached. I installed the soffit and alternated between the solid soffit with the perforated one.
Attachments
Step 21: Shingling
After the gable and eave fascia installed, I can begin shingling.
I first laid down the tar paper, unfortunately, a wind came up and partially tore the tar paper off on the south side. I then tried out some synthetic roofing under underlayment with @12x1" Galvanized roofing nails with Plastic Caps. I used this synthetic roofing just due that it's advertised that it more slip resistance. It's not more slip resistance.
- I then installed 4-1/2" White Aluminum Drip edge
- Where I could then start laying the shingles by making a starting edge by cutting the shingles off for the first row.
- I then begin laying the shingles.
- About 1/3 way up, I installed the roofing jacks.
When I got to the ridge, I used the Hip and Ridge Shingles, and overlapped them, and on the last shingle, I used plenty of tar and then nailed the last ridge shingle in place, then tarred the exposed nail head.
Step 22: Rafter Cross Braces
Initially, I was going to add joists to the back 3'-4' of the shed for loft storage above the upper wall plate. This would also help tie the walls in. We ended up decided against that so I gusseted the rafters.
Step 23: Fitting and Installing the Cupola
The Cupola was purchased, unfortunately the cupola's base was for a 3-12 or 4-12 pitched roof, so I had o make the base. I sketched the base out, and fortunately, I had extra 1" x 12" (3/4" x 11-1/4") vinyl boards which will work great.
Even though the base would require a compound miter, this was relatively easy, I did sketch the base out using the existing dimensions as a reference and extrapolated to the larger base sketch.,
And for the cross-cut miter and table saw settings, I had written a spreadsheet program a while back to calculate the settings on your table saw and cross cut miter. Recently (this project submission), I re-written it to make it more user friendly for others to use and included it on this step.
Since it was a basically a square, I just needed to cut (4) identical pieces, with (2) of the pieces cut to match the 12-12 roof pitch.
I have a high precision cross cut miter that goes to the 0.1 Degrees, people may think that's extreme,... being a novice with compound miters,... it's great because with the table saw, you need to split the degrees, and one can run into trouble with stack errors for this joint.. As the picture shows...I set the miter to 6.3 degrees, and the table saw to 44.7 degrees (ish).
I then fitting the base up on the bench, and glued into place using the table vice and miter clamps. After which I fasten with staples.
I then used the instruction instructions for installing on the roof. As I did this, I also installed the Cupola's weather vane.
Pictures of the finish installed cupola and weather vane are shown in later pictures.
Step 24: Boxing in the Eave Corners
I took the measurements I had to work with from the building and basically made blocking for the eaves corners to support the vinyl boards and installed the boards using 2-1/4" White PVC Trim Screws.
Step 25: Installing the Soffits
Installing the soffits went quickly,... I tried different ways of cutting the soffits to size.
Heavy scissors, tin snips... I've found that a 4-1/2" cordless angle grinder with an abrasive disk worked great. I also used this for the 'Cabot Brown' siding. The horizontal siding (Sage) on the front gable the material was softer and I used the band saw.
About 2" from the outside of the rafter eave, I cut a 2" x 2" in toe nailed it between the rafters so I have a nailing section for the soffit.
I installed the solid and then perforated soffits every other one interval.
On the gable end I used a 'F' trim on the wall, and made a 2-1/2" by 3/4" along the gable to hold the soffit in place, and I nailed a 1"x4" with blocking inside the outside rafter to nail the soffit to.
When I installed the soffits on the gable end, I did a continuous installation going up. and when I reached the peak. I used a solid soffit, fitting it and marked where it reached the ridge, removed it, and bent it, and reinstalled it and continued the down side.
To fasten the soffit, I used (1) #11 x 1-1/2" Electro-Galvanized Steel Roofing nail on each soffit, securing it to the soffit 1bout 1" to 1-1/2" the outside part of the nailing slot of the soffit.
Step 26: Trim Around the Door
For the trim around the door, I basically cut it from the vinyl boards. I did put in drip backers that the siding 'J' trim will cover as well as over lapped the door frame. Using 2-1/2" White PVC Trim Screws.
After I installed it, Sheila wanted to have some type of crown molding on the header above the door. So I took a trim router and put in a 1/4" bead molding.
I included an example of the trim around the door trim upright profile
Step 27: Flashing
I installed flashing prior to the siding to protect the OSB, fastening it to the lower wall plate using #11 x 1-1/2" Electro-Galvanized Roofing nails
Step 28: Siding
- I first installed the outside corner trim. And then the 'J' channel trim.
- I measured the length can to size followed the installation guide. Using the 4-1/2" cordless grinder with an abrasive cutoff wheel.
When installing the siding... make sure that they are set before moving to the next panel. I had installed about 3-4 panels and one of the panels I didn't have it fully in the groove where it would be loose; I had to pull those panels to get back to it and set it. Then I took a 2x4 and set the panels to make sure it's engaged to the previous panel.
- To start out on a panel run, I would insert the panel into the receiver, whether its be a 'J' Trim or Corner Post.
- To install it, I would flex the panel and install it in the 'J' Trim, back it over the previous panel and then slide it to engage the previous panel and set it in the groove with a 2x4 and hammer.
- After it's set, the panel can move up and down where I would give it approximately 1/8" space on the top 'J' Channel and about 3/16" on the bottom 'J' channel. I would then nail it tight on the top, and then nail it down the length given it some room for thermal expansion.
- When I come to the end of the wall run to the corner post, depending on the geometry of the panel that fits in the corner post, to set the last panel, I would first nail the under sill trim into the corner post receiver, and then I would cut vertical the panel trim (Slotted nailing section off) to fit the under sill trim inserting a corner first and working it in.
- Then I would nail the last panel on the upper corner of the panel, This will be exposed, but you can paint the nail head.
On the back side with gable vents, I would basically work around it. The gable vents have a receiver for the siding.
This is basically how I would do the horizontal siding (sage color) on the front gable with the last triangle piece at the ridge side and nail it at the top corner, this nail head would also be exposed. The only difference I would cut it with a band saw, because the material is too soft for the 4-1/2" angle grinder.
Step 29: Installing the Scroll Work
I first fastened the center post of the scroll with 2-1/4" White PVC Trim Screws to the peak and made sure it was plumb.
I then tried different variations on the position of the scroll. Considering the scroll work was pretty big to the size of the shed, I did not want it hiding or taking away the contrast of the upper siding.
After deciding the position, I secured it with (2) 2-1/4" White PVC Trim Screws on each scroll.
Step 30: Installing the Door Handle and Keypad Lock
I pretty much followed the instructions on the package.
- To install the strike plate, I laid the strike plate backwards and closed to door.
- I then opened the door and traced the area with a pencil.
- Chiseled on the plate and the receding part to accommodate the bolt.
- Fitted and the installed the strike plate with the screws that came with it, and done. It took about 15 minutes.
I did the same with the Key Pad Entry bolt lock.
Step 31: Excel and Remaining PDF's Sheet That Contains the Bill of Materials, Tool and a Few Links.
This MS Excel file SHED BOM TOOLS contains the Bill of Material (BOM), Tools and a few links on the installation. Also on the BOM, there are links to each item. Where you can download any specifications or installation instructions.
The BOM (is in both in a PDF format and Excel spreadsheet format) is pretty complete with a picture of an excerpt of BOM.
One last tip...When you're buying your fasteners for this size of building, I would go with a 30 lb. box for the framing nails, this would be more than enough, but it is more cost effective than buying the 5 lb. box. Also for the roofing the 3/4" and 1-1/2" roofing nails for the roof and siding should be sufficient.
Step 32: And That Pretty Much Wraps It Up.
There may be some adjustment I'll do later on, such as possible boxing off between the rafters on the inside that goes out to the soffits, it all depends how much snow will blow in through the perforated soffits.
This project was somewhat challenging yet pretty enjoyable.
The costs may have been higher due to the aesthetics, but it was well worth it.
Lets take a final look around.
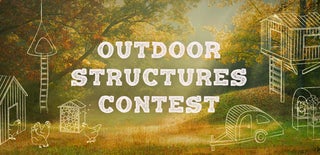
Second Prize in the
Outdoor Structures