Introduction: Oobleck Chladni Plate!?!?
What is a Chladni plate?
No, it is not some fancy serving platter that you get from your great aunt that you never put on your wedding registry.
No, it is not ... (alright lets get serious)
A Chladni plate seems simple at first glance it is just a thin plate with a low friction surface excited by oscillation but sometimes it is the simplest things that lay bare the most amazing phenomenon. This is a tool for visualizing and understanding the impact that resonance can have on the world. When you excite this simple metal plate to any number of resonant frequencies a few things will happen:
- You will wish that you had ear plugs because single tones produced by it are not very pleasant.
- You will wonder what is so special about this thing until you realize it is a tool to interact with other matter.
- Finally you put some powder or other small particles on the plate while it is a resonating
- Then just like every car seat or couch you have ever sat in the material mysteriously starts to collect in different places. The difference being that what you dropped in your car seat is gone forever while the sand on the Chladni plate is arranged into a beautiful resonant frequency mosaic.
Hopefully you are asking yourself a question along the lines of, "What is happening and why?" Just like my Rubens' Tube projects in the links below this is a manifestation of resonant standing waves but in this case we have moved from a one dimensional Rubens Tube into two dimensions with a Chladni Plate. I am also going to be looking at something I have no seen before and that is if we can generate a negative pattern on the Chladni plate using a non-Newtonian fluid like Oobleck!!!
https://www.instructables.com/id/Music-Controlled-...
https://www.instructables.com/id/Rubens-Tube-Flexi...
Lets look at what parts and tools we need and then in Step 1 I will go into greater detail about what is happening here.
FTC Disclaimer: I earn a percentage of the sales through the affiliate links provided through Amazon.
If you click on the link it helps fund future projects but bear in mind it might not be the best price for this materials.
Supplies
Materials
- Bluetooth or Wired Audio Amp
- Acoustic Exciter
- Plastic Tub (I used this to make clean up easier and to reuse the powder)
- 12" x 12" Metal Plate
- 1/4" x 2" Brass Drive Bolt
- 3x 1/4" Brass Nut
- 4x #6-32 1 1/2" Brass Machine Screw
- 4x #6-32 Brass Nut
- Sand Blasting Media
- Dry Lube
- 3D Printed elements (Connector between the Acoustic Exciter and the bolt)
- Sheet of Scrap wood ( I used some 1/4" plywood I had laying around)
- Glossy Black Spray Paint
- Electrical Tape
- Wire
- Frequency Generator App on your phone
- Super Glue
Tools
- Drill
- 3D Printer
- 5/32" Drill Bit
- 1/4" Drill Bit
- Ruler
- Marker
- Wire Cutter
Step 1: How a Chladni Plate Works?
There are so many demonstrations of Chladni plates on the internet, too many to list. Some are excited with a violin bow and others with speakers and still others with specially designed drivers. While you are likely able to find someone that explains it better me I am going to do my best to explain what is happening here.
Close your eyes and picture a a smooth pond surface. It is mirror-like. Now drop a small pebble into the water and watch the ripples in the water radiate away from the point of impact until they dissipate so they can no longer be seen. This is the start of what is happening with a speaker driven Chladni plate. The bolt in the center is like the pebble dropped into the water with waves radiating outer wards. However, unlike our example the waves do not have space to dissipate in the plate before they hit the edges and this is where things really get shaken up. At the edge some of the energy that is vibrating through the plate reflects backward towards the center of the plate where the vibration began like an echo in a canyon or like the rigid end cap in a Ruben's Tube.
We can try to understand this by going back to the placid pond in our minds and instead of dropping one pebble we drop two pebbles a small distance apart. Watching closely each pebble creates its own set of waves like our first test but as the wave patterns start to interact they create new peaks and valleys in the water through their constructive and destructive interactions. This same principle applies where the bolt in the center of the plate is one of the pebbles dropped into the water and then the surrounding edge is like a host of other pebbles reflecting waves back from the edge.
Most frequencies will just produce chaotic interaction with sand flying off of the Chladni Plate making all sorts of mess but just like what we saw in the different Ruben's Tube experiments there are certain frequencies that match the geometry perfectly to create consistent and beautiful interference patterns of both nodes and anti-nodes.
Nodes are where the plate seems to be sitting still like a valley of low energy. As a result the sand will collect in these places on the plate.
Anti-nodes are points on the plate where it is moving up and down wildly like a peak of high energy pushing and throwing the sand off of that point to try and find a less active spot to rest on the plate or off the plate.
However with Oobleck I am expecting what would be the opposite of this response. The nodes where the plate is calm is where I would expect the Oobleck to be liquid and flow easily. Now the anti-nodes will be moving violently which means that the Oonleck will act more like a solid building up from the surface. As the anti-node sections move I am thinking that they will collect the liquid Oobleck in the nodes and use that to build taller and taller.
The result when a resonant point is achieved is a stable pattern on the plate where the sand is pushed from the anti-nodes and settles in the nodes.
Ok, maybe enough explaining for now so lets get to making this things.
Both images in this step are sources from the Wave Interference article on Wikipedia where the creators are referenced.
Step 2: Build the Driver Mechanism Starter and Choose Your Own Adventure
Back in the day when you were reading the beginning of the instructable where I discuss the different methods you might have wondered how people have built or bought their drivers. Some people have taken old speakers and re-purposed them here on instructables by either attaching something to the cone or performing surgery to access the magnet and voice coil to be used for the driver or there are some that have purchased the premade solutions but these are so expensive like these two that I found below:
3B Scientific U56001 Vibration Generator
Eisco Labs Wave Vibration Generator
I wanted to explore a different approach that would not cost me less than $40 and would not involve trying to take a speaker apart. This design uses an acoustic exciter which is like taking the heart out of a speaker without having to go all Indiana Jones and The Temple of Doom on it. The important thing is making sure that you get an exciter of sufficient power to drive the plate. Since acoustic exciters are designed to be attached to large rigid objects that they effectively turn into the speaker cone an exciter seems like the most robust option and cost effective solution.
The driver mechanism will use a few different parts but the three primary parts are the following:
- Audio Amp
- Acoustic Exciter
- Mounting Hardware
- Base Mount
- Bolt Adapter
- Bolt Guide
The audio amp could be just about anything with the properly sized power output for the exciter. I am using the same Bluetooth/Wired Amp that have been for the last few projects because it has more than enough power with supposedly 50W per channel and is capable of using a Bluetooth or wired connection.
I have already discussed the acoustic exciter above and in my past projects if you want to check those out.
The third part is actually three parts. I am thinking that you figured that out from the list above.
- Acoustic exciter mount for attaching it to a base plate so the whole system is sturdy
- Drive bolt adapter that transfers the energy to plate from the exciter's voice coil.
- Bolt stabilizer/guide to go between the exciter and the plate. Without this guide it would be like trying to play a game of pool one handed holding only to the back of the cue.
I will be going through 2 different ways to make these parts one with a 3D printer and one without. If you want to go the 3D printing route the move onto the next step if you do not want to use a 3D printer then skip the next step to get to the non-3D printed solution.
Note: While I demonstrate how to make he non-3D printed solution I only tested the device using the 3D solution since it is much sturdier.
Step 3: 3D Printed Mounting Hardware
With the 3D printer you will simply need to take and review the attached gcode files. FYI I do not think that these files will fit any other exciter than the one that I am using. If you are using the same exciter go ahead and download and you should be ready to go. If you are not using the same exciter as I did the concepts of what they are are very simple and they were easy to make up in TinkerCAD.
You will see that I am using brass screws and and nuts throughout this portion of the project because steel and zinc screws are magnetic which creates problems with how compact this whole setup is with potentially distorting the speaker for the side mounting hardware but the major problem would be if the driver screw was magnetic it would severely reduce its movement because it is attracted to the driver magnet.
The acoustic exciter mount is very simple. The 3D printed element ensures a stable and level mounting surface that saves some mounting hardware. Looking at the exciter there are four mounting holes which are on a ~23mm radius from the center with 4mm mounting holes. I picked up four 1 1/2" long by #6 diameter brass machine screws with 4 nuts to securely attach the whole exciter apparatus to the base plate. Using the exciter mount for the hole pattern I marked and drilled the four mounting holes into the base plate. I then fed the machine screws up through the holes in the base plate so that the heads of the screws are on the bottom. I also decided to counter sink the screw heads to help the base plate sit flush on whatever surface I am working with.
The 3D printed exciter mount has the benefits of widening the base for support and ensuring that the exciter is mounted level which is a challenge with the non-3D printed approaches. I feed the exciter base mount over the screws so that it sits flush on the base plate.
After I had looked around at the hardware store and again at that mechanical drawing of the exciter I realized that the #6 machine screws would not fit in the mounting holes on the exciter. So I took a drill bit to the 4 mounting holes. This created some problems because there is a magnet at the heart of this exciter and the metal shavings are attracted to the magnet. This is why I covered over the opening to the inside of the voice coil to keep the shavings out and then when I finished I carefully cleaned up the resulting shavings from increasing the size of the mounting holes.
The next step is to put on the bolt adapter and ensure that everything is well lined up. I did this by first feeding the 1/4" x 2" brass machine screw I am using through the small bolt adapter puck and tightening a nut down onto it and adding some superglue to the nut to keep it from rattling off and to ensure that they stay connected. I then wrapped the brass machine screw in some electrical tape to mask the threading so that it would be rub against the bolt guide. I then used the bolt guide to help me properly position the bolt adapter onto the voice coil but first I had to do a little bit of trimming.
I made the bolt guide symmetric which means I did not take into account the cardboard plate that holds the leads for the exciter so my bolt guide unfortunately interferes with this piece. However it was a quick fix with a deft use of some wire cutters.
With the wire holder trimmed I position the bolt adapter onto the voice coil but I do not apply tape or glue yet. I then place the bolt guide lining it up with the 4 mounting screws and the driver bolt. Then using 4 lock nuts I tighten the bolt guide down to ensure that it is in its final place before I attached the bolt adapter to the voice coil.
The Bolt Adapter is a simple plug that attaches to the disk on the voice coil of the acoustic exciter. The shape of the disk is a ring with an inside diameter of ~21.8mm and an outside diameter of ~27.6mm. The benefit is that this solution will be lighter but more importantly the center where the drive bolt is set with the machine precision of the 3D printer and the file that I have made wraps around the voice coil disk to ensure that the bolt adapter itself is centered with 3D printer precision. The top of the bolt will need two more nuts to pinch the metal plate through a whole drilled through the center.
The guide for the bolt is very dependent on the length of the bolt that it being used. I went with a shorter 2" bolt for simplicity and stability while still giving enough clearance above the acoustic exciter.
With the bolt guide attached with the drive bolt passed through it all that is left is to attach the bolt adapter to the voice coil. I went with super glue to ensure a tight and sturdy fit that does not have the give of double-sided tape.
The final result is the 3D printed driver mechanism attached to the base plate. If you are just reading this step for fun but plan to make the non-3D printed version then go to the next step but it you went with the 3D printed solution then skip the next step and we can move on.
Step 4: Non-3D Printed Mounting Hardware
Maybe you are like me a few months ago and you are eyeing a 3D printer but you are saving up for it or maybe 3D printing is just not your thing and you like to push a different set of maker skills to the limit and adapt existing materials to your purposes. Whatever the reason it is fun to have you reading this step to make this system.
The acoustic exciter mount starts by looking at the exciter to see the four 4mm mounting holes which are out on a ~23mm radius from the center. I picked up four #6 1 1/2" brass machine screws with depending on which of the following methods you use 4 or 12 nuts to securely attach the exciter to the base plate.
Note: In the previous step I talk about how #6 machine screws are a little too large in diameter to fit into the mounting holes. Go back one step and read about how I carefully made these mounting holes bigger without getting metal shavings into the heart of the exciter.
Using the exciter for the hole pattern I marked and drilled the four mounting holes into the base plate and counter-sunk the heads into the bottom of the plate. I then fed the machine screws up through the holes in the base plate so that the heads of the screws are on the bottom. This is where the options branch.
- Clamp the exciter to the board using one nut on each screw to press the exciter into the base plate. (4 Nuts)
- Line the exciter up onto the 4 screws and allow it to slide all the way down to the base plate.
- Start threading the nuts onto the screws above the exciter ensuring that they are tightened evenly
- You are done and your exciter is attached to the base plate.
- Floating the Exciter on the bolts like standoffs (12 nuts)
- Run a nut down each of the machine screws to tightly attach each screw to the base plate.
- Run a second nut part of the way down each of the screws. This will be the nut that supports the exciter
- Line the exciter up onto the 4 screws and slide it down to the second nut.
- Double check to make sure that all 4 of the supporting nuts are level
- Place the third and final nut onto each of the screws and tighten it down.
The Bolt Adapter is a simple plug that attaches to the disk on the voice coil of the acoustic exciter. The shape of the disk is a ring with an inside diameter of ~21.8mm and an outside diameter of ~27.6mm. The non 3d printed solution uses a 1/4" long piece of 1" wooden dowel with a 1/4" hole drilled through the center all the way through the dowel for the bolt. Then one side is counter sunk with a 1/2" drill bit to set the head of the bolt inside the dowel. Tightening down on the bolt with a lock nut attaches it to the bolt adapter. Then using a steady hand it can be attached to the exciter using double sided tape. This will likely give satisfactory results but the closer to centered that you get the adapter the better for reducing off-axis movement of the drive bolt. The top of the bolt will need two more nuts to pinch the metal plate through a whole drilled through the center.
The guide for the bolt is very dependent on the length of the bolt that it being used. I went with a short bolt of 3" because it would be simpler and more stable but still give enough clearance above the acoustic exciter.
I started with a plastic bottle and cut the top off it so that I had the neck and the cap. This gives me a little bit more flexibility in case I make mistakes and to access the exciter because I can just unscrew the cap of the bottle to find its center and to have an opening for accessing the exciter.
However all of this written out this is not the path that I went with in the end since I do have the 3D printed parts which work much better. Let me know what sort of results you get through this method if you build it. I am thinking that they will be similar to the 3D printed solution if it is built with care.
Step 5: Preparing the Plate
The preparation of the plate is pretty straight forward. Using a framing square and a metal ruler I drew lines from each corner to the diagonal corner and where these lines intersected I knew I would find the exact middle of my square. With the center marked I used my metal punch to ensure that my drill bit would not walk away from the desired spot since I do not have a drill press. Using a 1/4" bit I made hole with a tight fit for the 1/4" bolt that I planned to use as the driving shaft.
With the center hole drilled I started to treat the plate with two coatings.
First, I chose to paint the surface black to improve the contrast with the white sand blasting beads I will be using. I picked up a glossy black paint to give me that contrast and an easy to clean off surface especially after I test the Oobleck.
Second, I applied a Dry Lubricant spray to the surface to reduce the surface friction on the particles to allow them to move freely. This will help lower the static and dynamic friction of the surface to allow the resonant shapes to be achieved at lower amplitudes.
With both the paint and the lubricant dry applied to the plate is ready to be attached to the driver mechanism using the two lock nuts.
Step 6: Preparing the Enclosure
The enclosure is simple. It is just a plastic tote that is larger than the base plate and the oscillating plate so that it does not interfere with the movement of the plate. I decided to mount my driver and the guide to a separate base plate so that I would not be ruining perfectly good tub/tote by drilling mounting holes into the bottom. You may have a different situation where you are totes flush with totes and have no issue drilling holes in the bottom. You have my blessing from the very bottom of my tub I mean heart.
It is helpful to have the tub be a little bit taller than your plate so that when the plate is excited the debris can still be caught in the tub as it bounces around which makes clean up so much easier.
Step 7: Putting It All Together
Now that all of the pieces are prepared we can finally put the system together to see how it fits. This step is rather simple since there are really only a handful of parts that need to be combined.
Wiring the Acoustic Exciter to the Amp board is simple as following colored wire conventions of red to red and black to black. The most important thing here is to have leads long enough so that the amp board does not need to sit in the tub with the Chladni Plate.
Adding the prepared plate to the driver screw is a little delicate to try and not touch the treated surface and to not torque the driver screw when I attach the lower lock nut beneath the plate and then sandwich the plate in place with the upper lock nut.
Now the whole apparatus should be built and all that is needed is to place it into the tube or tote that I am using and plug in the power for the amp board.
With this all done it is time to start testing!
Step 8: Testing and Experimenting
Learning from my fog tube and Ruben's tube experiments I started wearing ear muffs to protect my sanity.
With everything hooked up I first tested to make sure that without any sand that the system would hold up to the vibration otherwise it would be circling back to the drawing board. Thankfully the system did not shake apart which gave me the green light to try testing out the sand blasting sand to see where I could resonant frequencies.
I then add a thin layer of the the sand blasting beads to the plate and went in search of resonant frequencies. The pictures above are some of the cases where I found resonance!
The more complex the structure the higher the frequency. I found that only lightly dusting the surface produced very tight patterns that would be clearly seen. When I poured too much onto the plate the movement was dampened so that it was harder to achieve the resulting shapes.
As the frequencies got lower the shapes that resulted persisted for less time because the total mechanical travel of the plate is greater with each stroke at lower frequencies so it shook the sand off the plate quicker than what I observed at higher frequencies.
Now with some of the dry testing done it is time to see what Oobleck will do!!!
Step 9: Oobleck Chladni Plate!?
I was talking with my friend and he had this really interesting question about if there were more ways to use a Chladni plate and while I have few ideas that I will cover in another project the suggest that he made seemed brilliant!
What would happen if you put a non-Newtonian fluid like Oobleck onto a Chladni plate?
My Hypothesis was that in the places where the particles gathered in the previous step the Oobleck would stay relatively liquid but the empty spots would have firm piles of Oobleck that continue to grow from catching the liquid Oobleck near by. Effectively it would be a negative image of what we saw in the previous step.
All this depends on the plate and the driver being able to support the additional weight.
Here is what I found out...
There was a small amount of response in that when the oobleck was thin enough on the plate you could see mounds and valleys and they matched the expected hypothesis where the valleys lined up with the nodes while the mounds lined up with the anti-nodes which is the exact opposite of what we saw with the sand!
This is an exciting discovery even if the results of the testing look very nuanced. This is just more motivaiton to build a more powerful version with greater piston travel to support a heavier plate and more oobleck.
Let me know in the comments is this is something that you would be interested in seeing.
Step 10: Summary Thoughts
That was a fun and simple build. It create a very simple project that has impressive demonstration abilities. I will have to dig deeper into what it will take to make the Oobleck side of the demonstration more impressive but what was encouraging was that this setup proved the concept!
This was a fun build and the first project I got to explore using 3D printed parts and it certainly will not be the last. It really was a great feeling being able to design and print my own parts to make this project run that much smoother.
This was also a great project because through hearing from other people that are interested in the projects that I am doing a really great idea to test came from it which was testing with Oobleck!
There are so many questions about what could be done using vibration like this.
What about a pan that does not stick because of it is vibrating in such a way to continually move the objects being cooked ever so slightly?
This project has really lit a fire underneath me to see what other applications this project can have so stick around to see where this idea flares up next because I think it will be a real attention grabber.
Thanks for reading through my instructable and visiting my Youtube Channel RyanMake where I explore science and engineering ideas to see what sort of amazing potential is hidden just beneath the surface. If you would like to see more projects like this I would ask that you follow me here on instructables and like, comment, and subscribe to my youtube channel! Until next time happy making!!! RyanMake
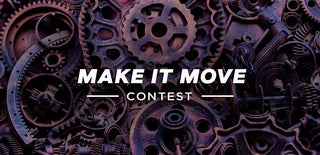
Runner Up in the
Make it Move Contest 2020