Introduction: Outdoor Kitchen - Casting Concrete Worktop With Curved Edges
I thought now was a good time to share my first Instructable on how to cast a concrete worktop for an outdoor kitchen, with almost perfect round-overs (if I do say so myself).
Back in early 2017 I had one of my silly ideas of creating an outdoor kitchen for my garden. I knew it potentially wasn't going to be easy or cheap and had to come up with a few creative solutions. And as it was for the outside I intended it to be a thick worktop. I knew if I cast it in a free standing form it would be impossible to lift. So I decided to cast it in place with a nice round-over to hind the ply base beneath. I was looking to achieve something close to a dark grey or black finish and I wanted to have a go at polishing.
My solution to getting nice curved round-overs without spending silly money on pre-made edging, was to make edging out of guttering.
Whist putting together this guide I found a number floors in the order I did my steps, so the guide has been revised accordingly.
Materials required: (quantities may vary depending on the overall size of the worktop you wish to create):
- 8x4ft Sheet(s) of Marine Ply 18mm
- 8x4ft Sheet of Ply 12mm
- Ballast
- Cement
- Concrete colouring
- Plasticiser
- Concrete sealant
- Concrete reinforcement mesh (In my case I used tent pegs and Chicken wire)
- Silicone (quick drying roofers silicone)
- PVC Guttering down-pipe or waste-pipe (Diameter, slightly larger than the thickness of the worktop you wish to make. I used 68mm guttering down-pipe)
- Screws 20-25mm
- Polystyrene
- PVC or duct tape
- Framing Screws 50-60mm
- Small piece of PVC conduit or dowel (broom handle worked for me) Length of timber 600-800mm (I used 50mm square)
- Stainless Steel Sink
- Stainless Steel Tap
- Mould release or furniture wax
Tools required:
- Mixing container (larger the better)
- Measuring container (the one from the kitchen will do fine)
- Shovel/Spade
- Orbital sander 60/80/120
- Aluminium Oxide sanding pads
- Hammer
- Polishing Grinder (240v or battery)
- Diamond sanding/polishing pads for grinder
- Diamond polishing sponge
- Drill
- Drill bits
- Spade wood bits
- Jigsaw
- Cement paddle (if you have one)
- Band saw
- Mitre/chop Saw
- Circular saw or Table Saw (if you have one)
- Sponge
- Silicone gun
- Clamps
- Bucket
- Spatula
- Paint Scraper
I had already built the base for the kitchen worktop at this point. I used standard construction blocks and a couple of concrete lintels to span the large openings at the front.
Step 1: Meassuring Up and Fixing the Ply Base
Measure up the size of your structure, add 50-80mm overhang to all of the sides. Then cut the marine ply to size for the base. Try to keep any joins to a minimum. However some joins are inevitable. Just ensure they are over the block work and supported or reinforced. Try to get as close a join as possible with the ply.
Due to only buying one sheet of marine ply and the shape of structure, there wasn't an entire piece I could use over what will become the pizza oven and log store area. I used what I had but unfortunately there was very awkward gap. This didn't matter to much as I would need to reinforce this joint anyway, as there is no support. I used a scarp of 12mm ply to cover the gap ensuring it was long enough so it would be secured into the block work and wide enough to ensure a good fixing. As the base is 18mm ply there wasn't to much concern that this wouldn't work.
Lay the ply out on the base structure, allowing for the 50-80mm overhang and begin securely fixing the ply to the block work with your preferred framing screws. Either by driving straight through the ply into the block work or by pre-drilling through the ply into the block work and driving in the fixing. You do not need many fixings just enough to keep the base flat and secured.
Step 2: Cutting the Guttering
To cut the guttering in half safely we need to setup a secondary fence on the band saw table.
Setup the band saw with the stock fence 34mm from the blade. Then secure a piece of 50mm timber as a secondary fence on the other side of the blade. Again 34mm from the blade. To ensure you have the correct support for the guttering this secondary fence needs to be around 600-800mm long. Clamp it flush with the backside of the saw's table. Turn on the saw. Hold the guttering up against the secondary fence and slowly push it through the saw. Be careful not to role the guttering.
If preferred the band saw's table could be extended to give even more support. To do this, fix the stock fence in place 34mm from the blade. Find a piece of ply or mdf board about 200mm wide and the same length as you secondary fence, ensuring one side is straight. Measure 68mm (in my case), in from the straight edge and fix the secondary fence in place. This is better done from the underside. Turn the band saw on and take the piece of board and run in through the saw up against your fence. Pushing it only as far as the back of the saw table. Turn off the saw, careful not to twist the board whilst you do this. Clamp the board to the saw table.
Cut the guttering into two pieces.
Step 3: Cutting Ply Strips
Rip 50-60mm strips from the 12mm ply sheet with the circular saw. Set the fence attachment for the circular saw at the desired width and run it the length of the board. You'll need as many as you have halves of guttering. Cut and addition 1 or 2 now as you will need them later.
On one face on the ply strip draw a line 20mm in from one edge (this will be the bottom of the edge form). Flip the piece over and on the other face draw a line 10mm in from the same side as before. If you are using bigger or smaller guttering then the 20mm line may differ. I'd suggest, offering the strip up to the guttering to find the best measurement. You need the ply to butt up against the curve of the guttering.
Step 4: Making the Edge Form Lengths
Fix the guttering to the underside of the ply strip. Using the 20mm line as your mark fix the guttering to the ply strip with 20mm screws, as shown in the picture (the screws are to big but this is easier than messing with smaller screws). Pre drill you holes in the gutting to prevent splitting the guttering. Be careful not to squeeze or distort the guttering whilst pre-drilling or fixing. Once this is complete run silicone down the edge of the ply where it meets the gutter to seal the ply and seal any gaps. This will help when removing the form later. I tried to do this once the edge form was attached, wasn't easy.
Step 5: Cutting Edge Forms and Fixing
Cut the edge forms to length. Pick a corner of your ply base to start from and set the mitre saw to the correct 45 degree angle. I started from the inside corner where the pizza oven area extends.
Place the edge form against the mitre saw's fence using the other straight edge of the ply strip. Slowly cut through the guttering and ply.
Place the 12mm ply strip under the ply base so the guttering curves towards the centre and align with the 10mm line you made earlier on the ply strip. Align the mitred end with the corner of the ply base. Fix from the underside with one screw through the 12mm ply into the 18mm ply base. Then mark the corner position of the next corner, unscrew and cut to length. Adjusting the mitre saw accordingly with the direction of the next corner.
Aligning with the 10mm line again and fix into place with screws down the length of the edging. Work your way around the ply base following the same method. As we're not going to form a round over on the back edge of the worktop, cut the two side pieces with straight ends and fix in line with the back of the base.
Step 6: Making the Back Edge
The form now needs a back edge piece. You'll need to cut some more 12mm ply strips first.
Measure the distance from the worktop base to the height of the guttering (n). Add 18mm for the thickness of the marine ply and another 10mm. {(n)+18+10 = x} Cut 1 or 2 strips at this width. Find the couple of extra 50mm wide strips you cut earlier (or cut some more). Fix the x wide piece to the 50mm strip with screws to make a right angle. Stagger the joints where you have to join pieces to get the right length for your form. Offer the edge right angle up to the back of the base and cut away the 50mm strip so the edge right angle sits neatly in place. Leaving the wide piece to overhang the guttering and creating a stop. Fix into place from the underside.
You may notice that in my picture (which was taken a few steps later) there are clamps... I didn't think this part through in the beginning and well, I'd built the structure to close to the fence and could not get down there with my drill! This was solved by using silicone to glue it into place and clamping it. Just meant waiting for the silicone to dry.
Step 7: Cutting Holes for Pipes and Fittings
Cut a hole in the ply base for the BBQ gas pipe and another for the tap using a spade cutting bit. Cut a length of PVC conduit or dowel to length (make sure its long enough to reach through the ply base and is longer than the thickness of the worktop. then feed it through the hole. If the hole is a little bigger than the pipe or dowel, simply wrap PVC tape around dowel or pipe to get the desired thickness. Fix into place with silicone or superglue.
Step 8: The Sink
Most sinks are designed so the outer lip sits on top of your work surface, this was not the look I wanted. And I could not attach the sick from the underside as I would see the ply base. My solution was to use the concrete to fix the sink into place.
Decide the location for the sink, flip the sink over and draw around the edge and remove sink. (You could be lucky with your purchase and get a template for the sink cut out, which will make this process a bit easier). The pencil line you have made is NOT a cut line. Measure the depth of the lip on the sink. Using this value measure in that amount from the pencil line you made around your sink and make a mark. Do a couple of marks and using a straight edge draw a line. Do this around all the sides. Then freehand a curve in the corners to replicate the sink outline. This is your cut line.
Drill a hole in all four corners near to your cut line, with a large enough drill bit and grab the jigsaw. Using the cut line cut out the hole for the sink. Drop the sink in to check the fit and make any fine adjustments. To keep the sink form moving about during any further steps, use a bit of silicone to hold it in place.
To stopping the sink from being filled with concrete Use some polystyrene. Cut and shape a piece to fit inside your sink. Depending on the desired thickness your worktop you may need to cut two pieces and stick them together. You do not need to be perfect with this just ensure its a good enough for a tight fit.
Wrap PVC tape around the edge of your insert. This will prevent the polystyrene ball effect on the edge of your concrete and hopefully make it a bit easier to get out. It may also be advisable at this time to drill a finger hole in the middle of your polystyrene insert. Trust me when I say this will help later. Then wedge it into your sink, ensuring it sticks up beyond the desired worktop thickness.
Step 9: Fill Gaps, Tape Joins to Seal the Form
Hopefully you have the form completed now with all the required holes cut and all the edging attached.
Start by filling the joins in the ply base with silicone and smooth off. Then run some silicone down the back edge to fill any gaps.
On the edge form, tape the mitre joint from the outside with PVC or duct tape. I found it easier to work with smaller piece of tape until I was happy the join was ok. Don't worry if there are gaps on the inside, just ensure the tops of the guttering line up and the line looks right. Then fill these gaps inside the guttering at the mitres with silicone and smooth.
Around the edge of the sink insert and the dowels use a bead of silicone, smooth and wipe away any excess. This is especially important around the sink. Remember you be able to see this part once completed.
Once the silicone in completely dry, wax the inside of the guttering, around the edge of the polystyrene insert and the dowels. This will aid in removal later on.
Step 10: Concrete Reinforcement
I was caught in to minds at this point as wasn't sure if it was required as the worktop will sit on the ply base. So I went with, my take on this with stuff I had on hand. Below I will detail the way I did it and a way it can be done better;
My way: I grabbed chicken wire and tent pegs. Take the role of chicken wire and cut a piece that measures the length of the worktop. Cut this piece in half so you have two piece the length of the worktop. Role the chicken wire tightly into a sausage shape. It would be advisable to wear good gloves when doing this.
Start in the left corner about 100-150mm away from the front and side edges. Fix a screw through the wire to hole/pin it in place. Then continue to run the wire parallel with the front edge of the worktop, fixing in place with screws every so often. Do the same along the back edge of the form about 150-200mm from the edge.
Take two tent pegs and hook them together. Using a lump hammer bend the end of the hooks over so they cannot come apart. Thread one end of the pegs into the chicken wire strips, then the other. Secure with a screw through the hook centre. Do this every 275-325mm down the form. To support further around the sink area I inserted pegs through the chicken wire and angled them into the voids. The idea here is for the chicken wire and pegs to be floating, not screwed down.
Alternative way: Cut some pieces of concrete reinforcement mesh to size to fill the form. Leaving around 50-100mm gap around the sides. Then put to one side for later.
Step 11: Mixing Concrete and Filling the Form
Use a concrete calculator to workout the amount of materials required based on the dimensions of your form. To keep it simple do not subtract the area for the sink, always better to have to much than not enough.
Mix the cement and ballast using the ratio of 4 or 5 Ballast to 1 of cement (4 or 5:1). Add the colour mix as recommended on the packet. I used a powered mix and mixed it into the cement and ballast. It is likely you will need to mix the concrete in batches, so if you are planning to add a colour ensure you measure all the components out accurately for each batch. Add water and plasticiser (as per the instructions) and mix together. It needs to be dry enough so it doesn't slop about, but wet enough to move around into the corners. The plasticiser will help to reduce the amount of water needed and help with workability.
Start filling the form with the concrete mix. Work the material into the curved edging, I found my hands worked best and keep filling. Use a block of wood to keep tapping along the underside and on the guttering as you fill to really get the mixture in there. Push and move the concrete mix around to fill in gaps and lower high spots. Using a straight edge skim the surface flat and trowel level. Once full and level use an orbital or vibrating electric sander to vibrate the form from the underside.
Run the sander along the form edges and try to get out as much of the air as possible. This process may take quite sometime if you want a really good finish. You may even need to fill or skim over areas after vibrating. Take the time to get the top surface flat and level with the trowel, with the least amount of bubbles. Go back to vibrating the edging until you have no more bubbles appearing. Any final bubbles on the surface should be popped with pin and allowed to settle.
Step 12: Floating the Surface
Wait for the concrete to partially dry. It's hard to know when to begin floating the surface, this is something that takes practice. This is what you need to look for. As the concrete sets, excess bleed water will rise to the surface. Wait until this water has evaporated and the wet shine of the concrete has started to disappear. If the concrete is still quite wet and forms ridges when you move the finishing trowel over it, you need to wait longer. However if the concrete becomes too hard and dry to finish properly (cracks may appear in the surface), throw additional water onto its surface.
Using a clean float or finishing trowel skim the surface in a curved motion with the trowel raised at an angle. You do not need to push hard on the trowel when doing this. You can create a very smooth finish by passing over the surface two or three times, waiting for the concrete to dry slightly between passes and raising the angle of the trowel a little more each time.
After a few hours cover the form with some tarp to keep in the moisture. If the mix dries out to quickly it will crack. Use the mist setting on the garden hose to add some moisture after 24hrs and over the following 3 or 4 days.
Step 13: Removing Form Edging
I waited about a week to remove the edging. Start by removing the tape from the corners. Then remove the screws from the underside of the edge forms. Remove the back side of the form, use a scraper tool to leaver the edging away.
Gently peal the guttering from the concrete, starting from one of the back corners. Rub off the silicone as you go. Breakout the polystyrene from the sink and again remove silicone from the gap. Cover with trap and wait 2-3 weeks for the concrete to dry.
Step 14: Slurry Coat(s)
I was a little disappointed by the number of voids I had in the edges, so decided to do a slurry coat.
With an orbital sander and 120 grit paper, prepare the surface and clean up the edges, removing any high points. Brush clean.
Mix cement and powder colouring to match your worktop. Mix water with the bonding agent as per the instructions. Then mix together into a paste must like soft peanut butter. Mix enough slurry to do coat the entire worktop. With a sponge and cold clean water wipe over the entire surface, wetting the concrete. This will make it easier to apply the slurry. It doesn't need to the be saturated. Because I had some large voids I took a bit of paste to one side and sprinkled over some sharp sand. Mixed it together and using this to pref ill the bigger holes. Pour some of the slurry on to the worktop and rub in, covering all the edges filling in the holes with your hands and/or plastic spatula. Allow to dry for about 24hrs before proceeding.
These articles and videos came in very useful:
Step 15: Sanding & Polishing
It's an art form in itself when it comes to sanding, grinding and polishing concrete. I tried a number of methods, but found the orbital sander to be the best starting point. Starting with 60 or 80 grit Aluminium Oxide sand paper. Sand the top flat and smooth, round over the edges and corners to preference. Using this higher grit paper can take more away than you planned to go gentle. Go over the worktop again and again down to 120 grit paper.
To get a more polished finish it needs to be ground with diamond sanding pads and water. These can be brought from the Internet as a pack, search for "Diamond Polishing Pads". The issue now is mixing water and an electric grinder, it would be advisable to higher a polishing grinder from a local supplier. These are designed specifically for this task and can be operated safely with water. Grind/polish the worktop surface starting with the 200 grit working through the various grits up to 3000. From my research I have two tips 1. Don't polish beyond 3000 grit as this is a waste of time. 2. Slow the speed of the polisher (if possible) as you go through the grits. Stop when you are happy with the finish.
Useful links:
Step 16: Sealing
Sealing the concrete surface is important to keep contaminates out of the concrete and prevent damage to the surface. And as this was an outdoor kitchen for the BBQ it would been to be sealed with a food safe product. This wasn't easy to find and I would suggest doing some research. Most food prep would be done inside or on chopping boards but I still need to ensure that is food fell onto the surface it would be an issue.
As per the instructions on the sealant apply coat(s) of concrete sealant and the job will be complete.
Step 17: Job Done
While this artical is about casting the concrete top, I wanted to show the complete artical. Well as complete as any project is.
I rendered the outside of the block work in a white rendered. This was my second attempt at renedering, my word it took ages!
The doors and the surround's are made from leftover scaffold boards, from my deck project. They'll grey nicely over the next 12 months or so and match just perfect. The hinges may look over the top but these door as quite heavy.
The tap has been fitted and is full operational, makes a nice touch when using the space.
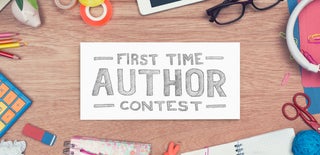
Participated in the
First Time Author Contest 2018