Introduction: PLA02 a Hybrid Rocket Engine.
!!-Disclaimer-!!
This project is dangerous and possibly illegal where you live. I do not take any accountability/responsibility for your actions. If however, you decide to continue anyway please join a rocketry club/group that knows and deals with hybrid engines.
Now with that out of the way we can begin.
What is a hybrid rocket engine and how can it be 3D printed?
A hybrid rocket engine is exactly what the name implies it is a hybrid between a solid fuel and a liquid or gaseous oxidizer. So how can you 3D print a rocket engine? Well being completely honest if you are not a millionaire or don't own an SLS or DMLS printer a traditional FDM printer won't be able to make a 100% 3D printed hybrid motor.
However, a few colleges and NASA have worked with 3D printed parts. In fact, the university of central Florida has done a test to confirm that ABS with some additives can outperform paraffin wax in motors, which is one of the best fuels for hybrid rocketry now. So with a little craftsmanship why not start my own mini R&D space program?
Step 1: Tools
Over the course of this project here are the tools/parts I used.
- Drill Press
- Drill
- Engine Rotary Bits
- 1/4 Drill Bit
- Bench Grinder
- Angle Grinder
- Scissors
- Pliers
- Welder
- Brillo Pad
- Oxy/Acetylene Torch
- 3D Printer
- Computer
Step 2: Testing
Initial testing
When I started this project I tried to make a simple hybrid rocket with a steel tube, rubber hosing, and an air compressor. When I began to light the rubber the flame was instantaneously snuffed out, after playing with it for a while I noticed the flame was not burning on the inner diameter of the tube. Most people think the air is only oxygen but its made up of 79.2% other elements/compounds. This means even though it is compressing the air I should only have about 20.8% O2 Just compressed. This would be like lighting a cigarette out the window on a highway.
After this little failure, I noticed I had some oxy/acetylene tanks sitting around. After connecting the nozzle into the steel tube instantly the flame ignited the rubber, causing a mini hybrid rocket engine to occur. Although this engine did not produce any noticeable thrust it was a milestone for my mini space program. From this point, I made a fully 3D printed engine to see if PLA could withstand the heat.(It did not duh.) It consisted of a 60mm grain which has a 28mm rod inside connected by 3 2x5 mm tabs on the inside. the injector was an inlet for a steel tube and a cone to direct the O2 into tubular grooves that line up with the grain. During printing of the grain the last roll of filament ran out, but the print was far enough along that it was ignitable and some spare PLA was found to make the igniter. With the igniter printing, I left to go get some more filament. When I returned the print was ready and begging to be ignited.
Step 3:
Step 4: Design
For the design of the new casing, I wanted to fit a 56.425x150.0mm fuel grain into the chamber. Leaving a few extra millimeters for the grain I made the casing 155mm long to account for the 16 gauge or 1.519mm thick steel bulkhead. The bulkhead has a 1/4" IM nut which is attached to the quick disconnect fitting and then attached to the oxygen tank via an aluminum shielded hose for extra safety. The nozzle will have 3 parts, a mounting bracket, a high temp gasket, and the nozzle. The nozzle assembly was made from sheets of 16 gauge galvanized steel. Sandwiched between the two steel nozzle parts is a Feltec High temp gasket to prevent leaks along the gaps of steel due to the warping from welding, and general hand machining. The gasket will also potentially hold in the possible 0.3 kilopascals(300 PSI) of pressure.
The fuel grain was a model of a solid tube, but using slic3r I print the grain at 25% infill and a honeycomb pattern.
Step 5: Construction
Parts I used:
- AP-15 Steel Fence Post
- 16 Gauge Steel Nail Guards
- Air Compressor
- Hose Quick Disconnect Fittings
- 8 1/4in Bolts
- FelTec High Temp Gasket
- PLA Filament
We started making the casing by cutting a 150mm long tube. After deburring the tube the first sheet of galvanized steel was used to make the bulkhead for injecting the O2. Using a hole saw a 56.425mm disk was cut and grinned down until it fits into the head of the casing. During the fitting process, a seem from the forming of the tube was discovered and a rotary bit was used to grind down the seem the bulkhead would set into the tube. However, when we inserted the fuel grain into the casing it was forced into the chamber with a mallet. Next, a male steel quick disconnect fitting was cut for the nut, then the nut was drilled out and welded to the casings bulkhead. At this point, the injector was finished. Then the galvanized tube was heat treated with my oxy/acetylene torch to make the removal of the galvanized coating easy. The casing was then spun to be cleaned with a brillo pad to make it aesthetically pleasing.
Step 6: Nozzle Fab/Desgin
Typical rockets have a De Laval Nozzle. This is a nozzle that incorporates a convergent cone and a cone following that is divergent. This is commonly called a CD or Convergent/Divergent nozzle design. When the engine shoots gases behind itself the gases are at a relatively low velocity, a CD nozzle speeds the gasses to sonic speeds when it travels through the convergent section. As the gases pass through a section called the throat of the nozzle the gases are accelerated to supersonic speeds by the divergent section of the nozzle.
A nozzle has a part called the throat, the throat is the smallest diameter section of the nozzle and the most important. When finding the nozzle throat diameter you need to characterize the propellant. This is attained by making a reusable casing for the engine. My design includes a mounting ring so that different size nozzles can be used on the same casing. By doing this its makes it easy to characterize the fuel. Allowing the fabrication of different nozzles and diameters within a certain size range. Then the collection of data on the casing with different size nozzle diameters during static tests allows you to find the proper diameter of the throat. The proper diameter is when the thrust is at its highest without over pressurizing the casing. Once characterization of the propellant is complete the fabrication of the entire nozzle and testing of it may begin.
The nozzle was constructed by printing 1:1 templates of the nozzles and marking where to cut on two 16 gauge galvanized steel sheets. The mounting disk is exactly 91.425mm on the outer diameter and 60.425mm inner diameter, and the nozzle is 91.425mm OD and a 25.4mm ID Throat.Then a hole saw drill was used to cut the inside diameter of both disks slightly smaller than the correct diameter. At this point, the FelTec High temp gasket was cut using scissors. An angle grinder was then used to make a rough cut of the outer diameter of the steel plates. Then using a hole punch the marks were made for the 1/4 in bolt holes, and then drilled out. After bolting all three disk together a bench grinder was used to trim and true all the disk by hand. After a rotary bit was placed on the drill press to cut the remaining burrs of steel this revealed two perfect diameter circles. The only thing left to do was weld the mounting disk to the casing. At this point, the rocket just needs a stand and the fuel grain inserted into the casing.
Step 7: Fuel in Propulsion
Almost everything in your life uses some sort of fuel to get it to you. So how do rockets use fuel today? Rockets use a few different types of fuel. First, the famous SRB or more commonly known as a Solid Rocket Booster/motor. An SRB uses a solid mixture of an oxidizer and fuel, they also use a binder which holds it together and acts as a fuel. When an SRB is made it is cast/molded into a grain. In rocketry, a grain is a shape a solid fuel is molded into. When this process occurs a single mistake in mixing or molding can cause the entire rocket to explode or have a damaging reduction in thrust, and did I mention you can not control it while it burns? A liquid rocket engine is a type of engine in which two liquids are burned in a combustion chamber. A liquid rocket design can easily become over complicated. To make the oxidizer and fuel into a liquid which allows for a larger density in the tanks you need to cryogenically cool hydrogen to -253C and oxygen to -183C thus adding to the complexity of the design. A liquid engine also has less thrust than an SRB but burns for a longer amount of time. Hybrid rocket engines take the design of both liquid and solid into consideration. A hybrid rocket engine uses a gaseous/liquid oxidizer and a solid fuel grain. This configuration has less complexity and has thrust and burn times in between an SRB and a liquid rocket engine. Hybrids can also be shut off reignited and throttled by controlling the amount of oxidizer flowing through the valve. Effectively hybrid rocket engines combine the best of both worlds. For my rocket engine, I will be using a 3D Printed Honeycomb tube made from PLA(Polylactic Acid) and an oxidizer of oxygen(O2) Hence the name The PLAO2 Hybrid Rocket Motor.
In this post I did skip the more exotic types of propulsion such as hypergolic, plasma, ion, etc. they all have their advantages and generally are too exotic/hard to make.
Step 8: Testing Requirements
"When one body exerts a force on a second body, the second body simultaneously exerts a force equal in magnitude and opposite in direction on the first body." ~Isaac Newton
When a rocket engine is ignited it produces a force called thrust. Thrust is the measure of force an object can act upon another. Thrust is usually said in newtons. One newton is the force required to move a kilogram at the speed of one meter per second, or about 2.236 MPH.
After viewing some videos and doing research it was determined that to define the performance of my rocket I need to calculate and measure the motors Total Impulse, Fuel Weight, and Specific Impulse. The term Total Impulse in rocket terms is It = F * dt or the sum of thrust multiplied by the increment of time used. The answer is then put into newton seconds. Specific Impulse is the efficiency of a rocket/plane engine the higher the Isp the more thrust a rocket engine can produce with the same amount of fuel. The equation for specific impulse is Isp = F/m*g0 Or ISP = Thrust / mass * Surface Gravity. After learning a bit from the formulas above it is clear some physical information is needed. Let's get the simple things out of the way first. g0(Surface Gravity) According to Nova Stanford the surface gravity of earth is 9.81 m/s^2. To find a mass of the fuel the easy way the weight of the fuel is needed, then apply it to the formula w/g = m or Weight / Surface Gravity = Mass. After weighing my fuel grain I calculated that 1.76N/9.81 = 0.179N. Now all that's needed is to fire the rocket engine and measure how much thrust the engine produces, and how long it burns.
To obtain the rest of the information a load cell is placed to measure the thrust. The information will complete the formulas, giving me an overall idea of the performance of the engine. Using the information I can design a future test engine to improve on the design. The only requirement for the stand that is found for the equations is Thrust and time. You can get better and more detailed results by involving more complex and accurate math which would need a pressure sensor, and sensors can easily cost over $100.
Step 9: Test Stand
With the requirements of:
- record thrust
- record time
- Mountable to a solid surface
A test stand was built with:
- 1" square steel tubing
- Chrome plated steel closet rod
- Drawer Roller
- Arduino Mega 2560
- HX711 Amplifier
- 40Kg load cell
For the stand, a load cell is required to measure the amount of thrust the engine is producing. This is completed by using a 40 Kg load cell in a Wheatstone bridge with an HX711 Amplifier which increases the voltage on the load cells output. The HX711 Is then connected to the Arduino Mega 2560. This is great the Arduino is getting readings, but they may be off by a little for the first test.
Pin Out
Load Cell [ Red -> E+ ] [ Black -> E- ][ White -> A+ ][ Green -> A- ]
HX711 [ GND -> GND ][ SCK/CLK -> Pin #52 ][ DT -> Digital / PWM 3 ][ VCC -> 3.3V ]
Arduino [USB -> USB-B]
The computer then has a windows only program called GoBetwino, which takes serial data and sends it to a file for reading/graphing.
If you have Linux then you can try a program called screen.
~Construction of stand~
The stand started by cutting two 70 cm square tubes, then mark 8 cm from the end of the tube on both sides of both legs. Next two more square tubes are cut to 15.875 cm, then placed on the leg line 8 cm from the edge front and back. Then for the cradle, two oval tubes are cut to 14 cm, then welded at a 70-degree angle. The cradle tubes are then placed 35 cm down the leg tubes. With everything set, it is spot welded into place to make sure it is properly set, once it's set properly the entire frame was welded completely. Finally, the drawer rollers are mounted to a particle board. With the top roller extended, a self-tapping screw is fastened to the roller and the steel frame.
The load cell was given a routed hole so it can be screwed into the particle board. The Arduino was then zip tied to the particle board just in case it needs to be removed quickly.
Step 10: 7... 6... 5... Ignition?
...nope
Step 11: Conclusion
Everything was planned up to this point. The motor, the stand, even the tubing to the O2 tank. But as the deadline closed for the metal contest, and the maker Olympics, things got a little rushed. The main plan was to test many nozzle diameters but the deadline is tonight at midnight. Currently, each grain takes 12 hours to print there is simply not enough time to show a successful ignition in this post. so let's review what happened.
- During the ignition, no pressure could build up due to the large nozzle throat.
This was planned. If the time was available I would have fabricated at least 10 grains and nozzles to test.
2.Towards the end of the uncut video, it was realized our O2 was running out.
We just need to buy a new tank.
3. The pressure sensor did not get a reading because the motor did not produce any thrust so no calculations could be made further.
Step 12: Credits
Made by: Zander Foster
Project name: PLAO2 Hybrid Rocket Engine
Instructable Start/Finish: 08/28/16 - 09/4/16
Sources:
- Wikipedia.org
- https://spaceflightsystems.grc.nasa.gov/education/...
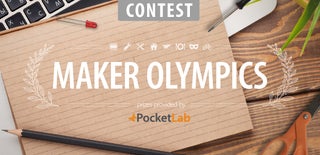
Participated in the
Maker Olympics Contest 2016
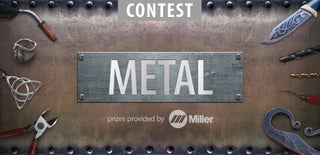
Participated in the
Metal Contest 2016
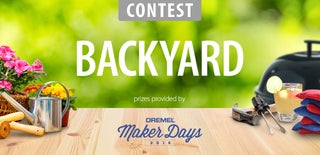
Participated in the
Backyard Contest 2016