Introduction: Pallet Wood Parquetry Circle Table
This is my step by step guide to making a small circle table with a parquetry top, made entirely of pallet wood.
Tools Required
Table Saw
Jig Saw
Planer (You really really need one of these for this)
Miter Saw
Various Sanders
Clamps... lots of clamps
Drill
Screw Gun
Glue
Pry Bar
Lots of table space
This is a rather involved project, it took me about a week to finish it, and seriously the hardest part of it was breaking down the pallets, so with that.. onto step one.
Step 1: Breaking Down Your Pallets.....stupid Stupid Pallets.
So what I did, and some how lost the photos of, was take my jig saw and run it down the top boards separating the outside runners from the tops and bottoms, then sawing off the thin boards connected to the middle runner.
For what we're doing we dont really need long lengths of the top boards (the stuff whatevers on the pallet sits on) and we dont want nail holes so we can just hack them apart and cherry pick out the good pieces.
Then I took my hammer and beat the crap out of the little pieces of wood stuck to the nails and the runners till they broke apart leaving just the nails stuck into the runners.
Now this is the first time I've ever tried to break down a pallet, so there was some trial and error and youtube videos involved.
What worked best for me, and is pictured, was to take a pry bar and sandwich it between two scrap 2x4's screwed down to my heavy work table. Then insert the nail head into the pry bar and use the entire length of the runner as a lever to pull the nail from the board. A hammer or just a pry bar alone will take forever, after my 3rd one of these I had it down pretty solid and was able to rip those things out.
Note: sometimes depending on the amount of weather that your pallet has seen, some of the nails can be rusty and the heads will break off, this happened to me in a few places, and the only thing I could do was suck it up take a hack saw and cut the nails flush. oh ya... you might need a hack saw too.
We're going to be running these boards through the table saw, so you really want to get all the nails out, otherwise sparks are going to start flying.
Step 2: Cutting the Runners to Length for Use As the Legs
Not Pictured: Run your freshly de-nailed runners through the table saw lengthwise removing the nobby ends so you're left with one solid piece of wood roughly 2"x2"(ish). This may seem counter productive consider we're going to glue on some blocks to either end of the board soon, but you'll see why here in a second.
Measure out 30 inches along your 2"x2" runner boards and chop them to length, stack all three together and feel the ends to make sure they're flush. Keeping everything the same size now will pay off later.
After you have your 3 runners cut down to 30", set your table saw to 60 degrees. Pick a random amount of length to use as a guide for your saw fence. I picked a half an inch.
Begin one of many 60 degree cuts you will make during this process, flip the piece over and cut the other side, till you're left with a piece of wood with 2 60 degree angles on one side (see photo).
It doesnt really matter how far into the wood you cut the angles, as long as you keep the guide fence of your table saw in the same place, once you cut both angles the peak of the angles will be directly in the middle of the board.
Once you've done all 3, dry fit them together, rejoice at your handiwork and curse your high school geometry teacher, because damn it... you did need to know this stuff outside of high school. (60 x 6 = 360)
Step 3: Plane Your Legs Down and Glue Up the Top and Bottom Pieces
Out of the scrap left over pieces from your leg runners, hack up a couple blocks around 3" long to use as the table feet and as the supports to for the table top itself to sit on.
Plane these down to 1 1/4"
Remember on the legs with the 60 degree angles in them, everytime you plane one side reduce your planer by the same amount and plane the other side, to keep the peak in the center of your legs.
Once you have everything to the right thickness, slap some glue on either end and clamp them up.
Drink a pot of coffee, and post to facebook "Watching glue dry, exciting stuff"
Step 4: Adding Feet to Your Legs
From another full length pallet runner, hack off a nice sized thick hunk to use as your tables legs, square off the edges to make sure you have good wood and a flat gluing surface and attach it to one side of your table legs.
Make sure you're consistent with your choice as to which side you stick your feet on otherwise things are going to get messy when you go to cut out your leg profile.
Note: I just used glue, but if you wanted you could drill a couple holes in the end of the pieces insert some dowel rods to give it some extra support for the glue up.
Drink another pot of coffee, and clear out your spam folder and your inbox that things getting pretty full of useless emails that you forgot to delete from your phone. Wait for the glue to dry, you're going to be cutting the profile for your legs next so you want to make sure the glue is good and dry so give it a couple hours before popping the clamps and drawing your profile out.
Step 5: Drawing Your Profile, Cutting and Shaping Your Legs.
Get creative, draw out what you think a table leg should look like, just free hand it, dont worry about making templates or anything crazy like that. Just draw what you like, or heck just leave it all chunky and palletey. I went for a more traditional table leg.
After you draw out your leg and are happy with it on one of your leg pieces. Take it to the bandsaw or use a jig saw and cut out the profile. Take your cutout leg and trace the profile onto the other 2 leg pieces and cut those out.
Then stack them all together and trace out the imperfections onto the other pieces and cut and shape those with the jig/band saw and sander/rasp.
When you're done you should of 3 legs that are very if not exactly the same. At least they'll be close enough so at a glance no one will be able to tell the difference.
I dont have a spindle sander, which would of worked great for the tight corners, but a portable belt sander clamped to my work bench and a clamp on the trigger makes a good rigged up sander.
Step 6: Dry Fit and Router Your Edges
Now that you have all your pieces the rough shape you want, dry fit them together just to make sure everything is lining up how you like it. Also this will give you a overall sense of how the base will look and any changes you want to make to the profile of your legs you can do now. (I changed how mine looked)
Once you're happy with how they look, take them over to your router table, or if you dont have a router table you can use a hand held router, just make sure to camp your piece down to the work bench so it doesnt go flying off.
Afterwards stack all your pieces together and check once again to make sure they're all at least really close to the same look, make any adjustments you need to and get ready to glue stuff together... get your clamps its gonna get complicated.
Step 7: Gluing Your Legs Together and Checking for Level.
Apply A LOT of glue to the angled faces of your legs, make sure to get even coverage all around.
I used a band clamp in the center to sort of hold everything together at the start, then slowly started adding gripper clamps, apply one just lightly, then another, and tighten each down a little bit at a time. That way you get even pressure all around and pieces dont shift out of alignment.
Through this clamping process, keep checking the top to make sure everything is in level still, and adjust your clamps as necessary to make sure you have good tight clamping pressure around the top and the bottom, after you're done tighten down the band clamp in the center again in case it needs it.
Step 8: Laying Out and Glueing Up Your Table Top
I had a scrap piece of 3/4th ply wood laying around, and I know what you're thinking. "But that's not a pallet!" but wait.. i had a shipment of door casing delivered, and thats what it was shipped on.. so technically its a pallet.
Moving on, measure from the edge of your tables foot to the center. Mine showed up right around 16", So I decided to make my table top 32" in diameter. The scrap piece of ply i had wasnt big enough to make the full 32" circle on. So I cut one piece at 16"x32" and another at 16.5"x32"
The reason for making one of the pieces longer then the other, is once you find the center point of the two boards, by drawing diagonal lines connecting the corners. this will offset your center point so its not right on a glue joint, it'll be just off to the left or the right depending on which side of the board you're standing on. Once you've found your center point, take a small 3/8ths drill bit and drill all the way through the center. Also on your legs drill a corresponding hole at the center point of all 3 angles.
This will be your marking gauge so that once the table top is completed you'll be able to mount it directly on the center of your legs.
I chopped off some of the excess with my sliding miter saw, or you can hack it apart with a circular or jig, jut to cut down on some of the bulk. apply a crap all of glue and clamp it up. I also clamped on some scrap pieces as culls, to keep the board from folding in on itself while under pressure. Its a good idea to take some packing tape and line the scrap boards with it, that way any squeeze out from the glue joint wont glue your scrap pieces to your table top.
Drink another pot of coffee. its gonna be a couple hours before you do anything else with this piece.
Step 9: Cutting Out the Table Top and Reinforcing It.
Once your glue has set, you can either cut out your table top on the band saw, jig saw, or you if you have a long cutting bit for your router you can make a quick circle jig for it and use that.
I did all 3, im terrible with the band saw, pretty awful at following the lines with the jig saw, and ended up piecing together a quick and dirty circle jig for my router.
There's plenty of youtube videos on how to make a circle jig for your router. but mine was just a piece of scrap long enough to make the radius and thick enough to support my router. I marked the center of my scrap piece, drilled a 38ths hole in one end, and then a 3/4th hole in the other at the end of my radius from the 3/8ths hole i drilled.
I set my router up with a collar guide that fit nicely inside that 3/4ths hole and lowered the bit until it was halfway through the ply wood, inserted a nail into the center point of the jig and the center of my circle and went to routin town! Flipped the piece over and routed the other side, and poof, perfect circle.
I also, to add strength to the piece, routed 3 3/4th inch datos into the underside of the table top and ripped some scrap maple i had laying around down to half an inch, glued and nailed them in, then took a belt sander and sanded them flush.
Just gives it a little extra strength.
Step 10: Getting Ready to Parquetry
Once everything's cut out and dry and out of the clamps, take a moment and stick a nail in the center point of your table top, and then insert that nail into the hole you drilled in your legs, stand back and admire your half completed work.
After you're done patting yourself on the back, (no really you should, you're not building a bed frame or a outdoor couch out of just stacking a bunch of pallets on top of each other, you dont play with blocks! you're a (wo)man! embrace your awesomeness) take some of the top pieces from earlier and lay them out across the top of your table until its covered in raw weathered pallets then throw a couple more on for good measure, you're going to have a lot of waste, so its better to make more then what you need then get into like step 13 and realize you need to come back here to make more stuff. So more is better.
If your top planks are whole then just hack the nail parts off on the miter saw, we dont want nail holes in these pieces anyways, also do a rough sort of your wood here too. What you're looking for is pieces that are solid, without any huge knots in them, or cracks, and you want a semi-straight side. So after you've taken stock of your pieces and cut all the nail holes out, double check and make sure you still have plenty of wood to cover the table top. Remember more is better you can always throw this junk away that you dont use, or use it for drink coasters or whatever your hippy heart desires.
Next separate you wood into piles of thickness, no need to get out the tape measure and be exact here, just throw it into piles so you know the rough thickness you need to start at when planing them.
Get ready to make a mess
Fire up that planer and start making ugly weathered wood pretty again, start with your thickest pieces and work your way down till you're planing your entire pile. on the first couple of passes, you want to plane both sides, just to get any warped or curved pieces flat. But then just concentrate on one side, that way you'll have a "rough" side and a "cleaner" side, to use for your parquetry. Get all of your stock planed down to 3/4ths of an inch.
Now that you can actually see what kind of wood you have, separate it into piles of types. I had 3, red oak, pine and i think poplar. Take it over to the table saw, set your fence to just rip one side barely, just to clean it up and make it a smooth edge. You'll need to reset your fence for your different boards, unless for some strange reason yours were all of a uniform thickness, mine not so much, they were all over the place. Once you've cleaned up the edges, set your fence to 1 3/4" and start ripping slats.
You'll end up with a nice pile of even thickness boards, arranged by wood type.
Step 11: Making a Jig
Now this is where it gets tricky
What you need to do is make a jig that can consistently cut a 60 degree angle in all your pieces, safely is the key here. I had an old cross cut sled that i had retired that i repurposed into a jig for this, but you can make one for specifically for your table or jig saw, for me it was just easier to use what i had laying around.
If you've never made a cross cut sled, i suggest stopping here, and making a cross cut sled, its a good skill building project and it really adds a lot of versatility to your table saw.
Quick run down of what I did for my jig. I set my miter saw to 30 degrees, and cut up a piece of scrap.
"whoa whoa whoa 30?! you said 60.... is this a high school math thing again?"
Yep, for one no miter saw is going to have a 60 degree setting on it, cause they only go to 45. So if you cut a straight piece to 30 and flip it over, you have a 60. Trust me it works.
Then i cut my scrap piece in half, put a piece on either side of my saw cut in my gig, measured 1 3/4ths from the edge of the blade and drew a line, i cut another piece of scrap to 30 (60) flipped it and nail gunned it down. This will give me a repeatable stopping point for my wood to sit against.
Then i started cutting, your first cut is free from the stop block and just resting against the 60. Cut the piece so that there's a continuous angle through the entire piece. Then slide the piece into the stop block and make another cut, you've now made your first of many... oh oh so many pieces.
Continue cutting up pieces in this method until you've exhausted your supply of boards.
Step 12: The Wrath of Parquetry
Now that you have a billion little pieces of wood, do a dry fitting, so you can get the idea of how they go together and you can get a rough estimate if you have enough pieces to complete the entire table top. Start at your center point, and work your way out. I found it easiest to make the little 3 pieces and then build off that.
To get a good 3D effect you want to be consistent with the colors of your pieces and where you put them. If so inclined you could stain the pieces 3 different colors, a dark/medium/natural and that would also give the same result. I wanted to keep this as natural as possible to show off that its all just pallet wood, nothing else. so i kept things simple and put my darker pieces on the "bottom" and alternated my lighter pieces.
You'll want a piece of sand paper to clean up any rough edges on your blocks, pour some glue into a little container and get a brush to apply the glue. This is a lot like tiling, its better to glue each tile, then try to pour a lot of glue down at once and work quickly before it sets up. You want to make sure you have a good amount on the bottoms and on the sides. Continue process until entire board is covered.
wait... wait awhile, do some laundry, get lunch, take a nap. you want to make sure everything is dry and secure before going further.
Sand...sand...sand..sand and more sanding. I started at 80 and went up to 220. Then I put some scrap wood under neath the table top to raise it off my work surface, attached a flush trim bit to my router, set the depth and buzzed that bad boy around the edge.
There was chip out.
Mostly on my red oak pieces which didnt surprise me in the least, i tried to find the pieces that went flying, and on the ones i couldnt, I just took a chisel and cleaned up the spot and from my left overs matched a new piece in, cut it out on the band saw and glued it home.
another quick sanding to clean up any rough spots, then take a measurement of the total thickness of your piece, and get ready to make a mess.
Step 13: Planer the Next Generation.
Now with your measurement of the total thickness of your piece, grab some more top planks if you have any left over, or break down some more pallets and start ripping them down, but rip them 2/8th larger then the total thickness. Then once those are done and to size, go back to your planer, you want to get them to anything below 3/8ths 1/8th would be great, but lets not kid ourselves this is pallet wood. So get it down a "bendable" thickness.
Then you're going to want to put a 45 on the edge of each piece (see photo) this way you can over lap your edge banding, one to hold it in place easier and two, it'll look nicer.
I was in a time crunch to do this, so I did all the edge pieces at once, I do not suggest doing this, take your time, do 2 at once. Glue the crap out of them, stagger your 45's and tighter your band clamp around the piece, any parts that are sticking out, stick a big heavy duty clamp on them to hold them in place. wait an hour or so and repeat the process all the way around.
Congrats you've just done parquetry and bent wood lamination in one project (first for me too).
The end is in sight, just a couple more steps.
Step 14: Prepping to Finish Your Piece
Now stick a nail back in the center hole of your table top from underneath, and line it up with the center hole in your table legs. Flip your table over, drill a 3/8ths hole in each part of your leg that connects to the table bottom. counter sink, and use a screw long enough to secure into the table top but not poke through into the parquetry.
You can get some plugs to fill the screw holes, glue them in wait for them to dry and use a little pull saw to cut them flush, sand and get ready for finishing.
I used a water based spar urethane on the legs, spray, wait 30 minutes sand, spray, wait sand spray wait.. you get the drift.
Now on the top I used an acrylic two part epoxy, like would be on a bar top. I think the cost was around 16 bucks, and 4 for a clean bucket. you want a clean bucket to mix this stuff in.
So for this part you need a clean bucket your epoxy a stir stick and a blow torch/heatgun, and a disposable brush foam is best.
First prep your surface, more importantly under your surface, anywhere there's a gap this stuff will find a way to drip out of it. So if you have any holes in your edge banding, tape those up. Or what you can do is get some clear silicone and run a bead of that around the base between the table top and the edge banding, wait for that to dry, and then move onto the epoxy stage.
Follow the instructions on your epoxy kit for mixing and what not, and pour it on. then use the brush to move it around. You dont have to get too crazy this stuff is self leveling so its going to go where it needs to go, but sometimes it just needs a little help getting there. Also this stuff is the reason we made the edge banding a little higher then the actual depth of the table top. so it just doesnt run over the sides, and it will give it some visual thickness and depth.
wait 15 minutes, bubbles will start to appear use the blow torch/heat gun in quick movements over the bubbles stay at least 6 inches away from the surface, and poof.. bubbles be gone.
Oh by the way you're basically married to this piece of epoxy for the next hour. Every 15 minutes use the torch to get rid of the bubbles. depending on the temperature where you do this, it can take anywhere from 3 hours to 6 to set up, and 24-72 hours to fully cure.
For mine i went a little too thick with my edge banding, and had a few too many gaps between some of my tiles, so in 3 days im going to apply a second coat of epoxy, its just one of those things you have to play by ear, every table and wood is going to take this stuff differently.
Enjoy your time with your table, and using a torch on it.
Step 15: And Then?
Hey you're done.. sorta you've got up to 3 days before you can do anything with your table. But for now you can sit and look at it and say hey I made that and its awesome.
I hope you enjoyed my walk through on how to build one of these. This was my first pallet wood project and my first Instructable.
oh ya one more step.
Step 16: No and Then.
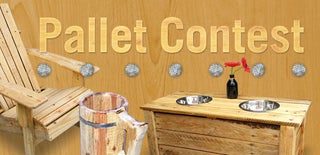
Second Prize in the
Pallet Contest