Introduction: Pencil Cup: First CNC Project
This project is something I put together to learn the Othermill, a small, precise CNC mill primarily meant to prototype printed circuit boards. It can work with a wide range of materials and is able to create more complicated components that would be handy for enclosures.
My goal was to design a cup, testing the basics of what a CNC mill can accomplish. The cup is a finger joint cut on 5mm thick material measuring 4" high by 2 1/2" wide. The bottom of the wall has a groove to fit the base.
( Yes, some parts are in millimeters and others are in inches. I started with one and then went to the other and was sort of stuck by the time I was done.)
You could probably knock this out with a router with a good jig. Yet I have neither of these and it looked like something relatively safe to learn about using a CNC mill. (Those are famous last words)
I have never used a CAD/CAM application nor a CNC mill prior to this project.
Step 1: Materials
- 1 or 2 Basswood 1/4"x4"x24" hobby boards. I used 2 but you can probably get away with just one.
- 1 or 2 Basswood 1/32"x4"x24 hobby boards.
- An Othermill or another CNC mill
- A 1/8" & 1/16" flat end mill
- A saw
- Double-sided permanent tape (I was surprised to find that you can get reusable double sided tap, but that won't work with this project) if you are using an Othermill.
- A hot glue gun if you are using an Othermill.
- A thin putty knife if you are using an Othermill
- Calipers
- 80 grit sand paper or sanding block, and more grits depending on how fine you want the finish to be.
- The attached igs file that you can hopefully import into whatever CAD application you are using and make the same model.
- Wood glue
- Vices
- A block plane if you want to make it look a little less machined.
- Paint or stain to finish the project.
- A shop vac when cutting.
- Ear protection
- Pencils
- Just under 1 hour to babysit the mill while it is cutting.
Notes:
I used Revell Basswood hobby boards because they are cut almost exactly to spec. You can use pretty much any hobby board, or any other wood for that matter. Basswood is a soft wood and lets the CNC fly through it. You will need to sand the pieces after cutting because of hanging fibers and the board is rough to begin with.
The 1/32" basswood is used as a sacrificial layer between the 1/4" stock and the mill bed. It is not necessary, but is handy if you have some variability in the thickness of the wood. It gives you a little (ok, very little) wiggle room to avoid cutting into your mill's bed.
The wood cost about $10 and everything else was stuff I already had and use for other projects.
Attachments
Step 2: Designing the Walls
I used the golden ratio to set the size of the wall, which is how it became 4" by 2.5" x.196".
The base groove is .196" x 0.09" x 2.207"
The tenons are .5" on one side. and .48" on the Y axis.
The mortises are .5" and .52". on the Y axis.
Why did I make them different sizes? First, I tried it where they were equal and that didn't go well. They were too tight and did not close completely. The tenons needed to be either smaller or the mortises wider to make then fit slightly better. Also, the interior corners are not a perfect 90 degrees. They are slightly rounded and this causes the pieces to stick out.
Using .02" or .5mm seemed like a good idea. Turns out that .01" may have been better, but I was running low on parts. The .02 creates just slightly too large a gap, but the pieces fit easily together. If you finish it with a stain then the wood will expand and the gaps will tighten shut.
The main lesson is that the modeling software assumes that things will fit perfectly. Yet real materials cut and behave differently. If you are planning on booking time with a CNC mill or getting one of your own, be prepared to spend much more time learning these odd little differences between the modeled and real world and compensating for them.
The mortises and tenons are .196" x .196" on the X and Z axises.
The project is modeled in Fusion 360 for both CAD and CAM. All dimensions were set using variables specified in the "Change parameters" dialog. Using variables makes it much easier to adjust the dimensions later. This feature is especially handy if you find out that your mill cannot perform some tool paths or you want to convert to feet instead of inches though that would make for a very large pencil cup.
I have shared the fusion link here if you'd like to give it a try.
Step 3: Prepare the Stock
Cut the 1/32" and 1/4" basswood into 4 1/2" blocks. The size of the block is excessive, but ensured that there was plenty of room for the piece.
Use calipers to measure both the 1/32" and 1/4" stock. Write down the dimensions on each piece of stock. I wrote it on the top of the 1/4" stock where the facing plan would cut it away. The dimensions are needed during the "Setting you tool paths" and "Milling" steps.
Step 4: Setting Your Tool Paths
I ran one facing operation with the 1/8 flat end mill with 60% stepover, which gave a better finish.
All other operations were done with the 1/16" flat mill.
Inexperience coupled with a lot of research got me to a spindle speed of 16,000 rpm (Othermill tops out at 16,500) and a feed rate of 710 mm/min (I found the basswood spec on the shapeoko wiki)
Othermill technical support helped out a lot too with general and then obnoxiously specific questions about the mill, tools and best practices. They were really amazing and I haven't encountered technical support like that before.
The CAM plan included the following:
Setup: stock was always measured with calipers for each piece on all planes. The sizes were synchronized between Fusion and Otherplan, which drives the Othermill. Note: multiple thickness checks were made and there were differences in the thickness from one measuring point to another on the same stock. X axis is the long side, Y axis is the short side. Z is well, Z :) Have fun adjusting the axises in Fusion. The X axis is the longer length on the Othermill.
Tool Paths:
- Facing, 1/8" mill.
- 2D Pocket for each finger joint and groove, 1/16" end mill.
- 2D Contour for finishing and smoothing passes on the joints and channels, 1/16" end mill.
- 2D Contour for the finishing cut and smoothing passes around the edges of the piece, 1/16" end mill.
Run the simulation and verify that you do not have any collisions or errors with your tools due to cut length. If so, change the design or the tool to accommodate your equipment.
Export two g-code files for the facing and all remaining operations.
Step 5: Cut
Import the three NC files into your CNC mill's management application, load the stock, tool and perform any necessary calibrations. Then settle in while it cuts the first piece.
The Othermill uses Otherplan. Follow these steps:
- Turn on your hot glue gun and the Othermill.
- Click on "Setup Materials" in the setup section.
- Set it to Birch Plywood, which is close enough to what we are using, and specify the X,Y and Z dimensions of your stock. Then click on Continue.
- A new dialog for setting the material origin will popup. I am using a sacrificial layer so here is where I specify any offsets. I only need to specify the Z value, which is approximately .04". Click on Done.
- Prepare the stock by putting double sided tape on the bottom of your stock and on the bottom of the sacrificial layer. Put the two pieces together. Do not prep more than one piece of stock at a time. You want the tape to adhere as best as possible, so minimize any unnecessary exposure to air, dust or any else that can affect it.
- Click on the "Loading" button. The bed will move forward and the head will move out of the way.
- Put the stock with the sacrificial layer onto the bed. Make sure it is well attached.
- Remove a side window, which is attached with some super strong magnets. Use the hot glue gun to lay a bead of glue along the Y axis of the stock.
- Add another bead of glue along the X axis.
- The glue needs a minute to dry. You can import the NC files while waiting.
- Load each file by clicking on the "Import files" button and either select or drag the NC files into the plans section.
- Set the tool for each plan.
- Click on the "Home" button.
Look carefully at the Side, Top and Isometric views and confirm that the tool paths look correct. If they are not correct then review the material setup to be sure you have the same values in your CAM processor as you do in Otherplan. They both need to have the same values or you will have a bad path. Cutting air, or the bed, is less fun than cutting the piece.
Click on "Start Cutting" for the face plan. It will prompt you to install the 1/8" flat end mill.
Go through the homing and tool positioning process.
Sit back and wait while it faces the stock.
- Repeat steps 15 through 17 for the next plan. You may want to use a shop vac and suck out the saw dust.
- Now that all the cutting is done, take the putty knife and carefully pry the cut stock off the bed. Be careful not to break the piece you just made.
- Remove any left over tape from the bed and piece. You may be able to reuse the sacrificial layer, but use new tape. Recycle the left over stock.
Note: You really should babysit the mill while it is cutting. The bit could break. The tool could bind up. The stock could tear off the bed and be spinning around with the bit. This does make it a little exciting. Hit the red emergency stop button if anything goes wrong and start from step 1.
Second note: Take a good look at the sacrificial layer. I was told that it was a good idea to use the extra layer till I really knew what I was doing. This is only 1/32" thick and cost about $1.99 for a 2' long sheet. That was money well spent because a mill bed and the end mills are much more expensive. See the picture above to see what would have happened if the sacrificial layer was not there.
Step 6: Inspect, Dry Fit and Cut Some More
You should have one of the four walls cut out. Take a look at it and make sure that everything looks the way you expected. You should only have tenons, mortises and grooves where you expected them to be.
The piece should be a little fuzzy around the edges. Carefully, take the 80 grit sandpaper and a file, and clear all that away. Avoid cleaning any edges as though you were finishing the piece. Just clear the fuzz away.
Use your shop vac and clean up the mill.
Cut the second piece and clean the fuzz off that one.
Take the two pieces and see how well they fit together. You may need to use a file to very carefully square the mortises and any internal angles that are too round to fit cleanly together. You should only have to drag the file once or twice at the most to square the corners. If they are off, they will only be off by about 1/2mm and over-sanding at this point will ruin the piece.
Recheck that the pieces fit snuggly together and are square. You may have to adjust either the design or perform further cleanup to get everything to fit well together. Then go back and cut the remaining walls and base and fit the whole thing together.
Step 7: Finish It!
Do a finishing pass of sanding on the exterior along the edges to get the finger joints flush. You may want to add a chamfer along the edges with a block plane. I like using hand tools to add a little human factor so that it doesn't look entirely machined.
Separate the dry-fit pieces. You may want to mark the bottoms of each piece so you can fit them back together exactly as you fitted them during the dry-fit phase.
Now do whatever finish you'd like, glue it together and use the vices to hold it in place while the glue sets. Then do a final pass on your finish.
My cover photo shows my finished cup. I used a really dark stain for all the pieces and let them dry. Then I glued everything together. After that was done, I sanded with 80, 120 and 180 grit paper the exterior walls. Cleaned off the saw dust and used a moist paper towel on the wood to open its pours. Finally, I gave it two coats of a light stain.
The dark edges are what showed from around the finger joints. If the wood contracts or expands then it will still have the same look and finish. I prefer to fully stain all the joints and edges to ensure that there is some kind of intentional look to the work even when it is affected by humidity and temperature.
Thanks!!
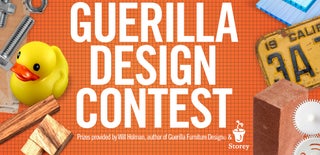
Participated in the
Guerilla Design Contest
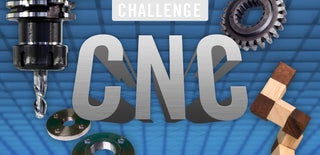
Participated in the
CNC Challenge