Introduction: Darrieus Wind Turbine From Pencils and 3d Printed Parts
Wind Turbines can be divided into two main groups according to the orientation of their rotor shaft: Horizontal Axis Wind Turbines (HAWT) and Vertical Axis Wind Turbines (VAWT). Wind Turbines can also be classified with respect to the principle of operation: Lift-Driven and Drag-Driven technologies. Although, HAWT are now widely spread around the world because of his greater efficiency and characteristics, VAWT are designed and constructed as commercial or DIY solutions in many countries. The Aerodynamic Efficiency (Power Coefficient) of Drag-Driven Wind Turbines as VAWT (Savonius) is low, with values between (10-15%) compared to the typical values of the Drift-Driven machines (30-50%).
In 1931, Georges J.M. Darrieus, a French aeronautical engineer, patented a new type of Windmill designed for power generation. The Darrieus Wind Turbine is a VAWT and Lift-Driven, having two or more airfoil blades. The rotor of the Darrieus Wind Turbine can achieve relatively high Aerodynamic Efficiency, around 40%. The original Darrieus Wind Turbine had curved blades with a symmetrical airfoil in their cross sections, similar to an Eggbeater.
The main characteristics of the Darrieus-type Wind Turbines are: relatively simple devices, just a slightly lower power coefficient than Lift-Driven HAWT, the electric generator and gearbox can be installed at the ground level; the yaw system is not needed because the rotor operates regardless of the wind direction. Shortcomings of these wind turbines are: low starting torque and vibrations of the structure during rotor operation.
The growing demand for decentralized electricity generation in rural and urban areas are motivating the study of this type of wind turbines in a small scale.
In this Instructable I am presenting the steps for the construction of a small VAWT (Darrieus), a type H with three Airfoil blades, which I plan to use with my students. I also propose a series of measurements and experiments. Comparisons are made between this type of VAWT (Darrieus) and a Drag-Driven Wind Turbine.
INITIAL CONSIDERATIONS
For the design of this small Wind Turbine, the use of 3D printed parts, assembled together using pencils, was considered. Surely you are wondering: why I chose pencils? One of the reasons was that they are very accessible around the world, specially in schools. Another reason I thought about using pencils was due to their properties of relative low mass and good strength as they are straight and show a low deformation while facing the forces on the proposed generator. Using pencils to interconnect also saves a lot of 3D printing time which for these types of assemblies is usually a bit time consuming. As pencils have a standardized size will fit into the parts that were designed, after downloading the STL files and printing them. Lastly, they come in small scale making them simple to manipulate allowing the students to use their creativity in class or home.
The advantages of using a 3D printer can be obvious. Almost identical replicas of all the designed parts, possibility of using various types of thermoplastic filaments available on the market and giving it a peculiar appearance and properties are some of them. Excellent opportunity to interact with these types of technologies and understand their advantages and disadvantages are also opportunities you can exploit in your classroom with your students in order to expand their knowledge.
After having analyzed the possible variants of Darrieus generators, I decided to design one that had 3 airfoil blades of the NACA 0018 type. You can find technical information on the Airfoil NACA 0018 and others in the following links:
https://www.pdas.com/refs/tm4741.pdf
https://lin-web.clarkson.edu/~pmarzocc/AE429/The%20NACA%20airfoil%20series.pdf
I consider that the analysis of these NACA profiles, from the mathematical point of view, offers an excellent opportunity for the treatment of equations of several variables, as well as the geometric construction of these profiles. The historical importance derived from the application of this knowledge in Science and Industry is something very interesting as well.
The fixation of the airfoils on this design is from their center of mass, where a protrusion was placed for the fixation with pencils. To promote stability to the system, each Airfoil would be 120 degrees apart from each other.
A small DC motor was used as a generator. These motors work at relatively high RPM and if they are used as generators they will have to rotate fast if you expect a useful voltage is to be obtained from them. To promote this, two gears with a multiplication ratio of 1: 4.5 were calculated.
One of the distinguishing characteristics of Darrieus three- airfoil blade generators is that they generally operate at high RPM, even with tangential speeds on the order of 2-5 times higher than the wind speed that enables their rotation, thereby improving the system efficiency. Precisely one of the proposed experiments involves comparing the tangential speed of this Darrieus generator (Lift-Driven) with one of the Drag-Driven type.
Since the main objective of this Darrieus Generator is to provide a teaching-learning environment with which to experiment, it was considered to use a typical home fan due to its availability and low weight. Its function is to provide the necessary wind for this project to work. The wind generated by this type of fans is rather turbulent. The blade guards were removed during the experiments to improve turbulence indices. Care must be taken with these blades in motion so that they do not cause damage to people or the environment. Ideally, there should be no objects in the vicinity of the proposed generator also to avoid turbulence.
I consider it very timely to address this topic in class and it constitutes an excellent opportunity to discuss topics related to STEM subjects.
note: According to my humble opinion and during my research on this topic I was unable to find an easy to replicate, 3D printable modular Darrieus generator to fit into school projects and to experiment at home. That is why I am suggesting this project so others can benefit from these ideas.
Supplies
- 3D printer
- Printer filaments: PLA, PETG, ABS or similar
- Ballbearings
- Seven Pencils, preferably hexagonal
- Silicone-hot glue gun
- Small DC motor with brushes and permanent magnets (approx. 35mm diameter)
- Electric cables
- Electric soldering iron and solder
- An M4 screw with its corresponding nut (approximately 15mm in length)
- Two appropriate screws for fixing the DC motor to its support (depends on the type chosen)
- Instant glue
- Oscilloscope and Photoelectric Sensor or Digital Tachometer
- Ruler
- Double contact tape
Step 1: Print the Designed Parts on a 3D Printer
To print the pieces, a FDM (Fused Deposition Modeling) printer was used, specifically a Longer Lk5 Pro. Any other printer could work perfectly since they are not complex pieces to print. The use of an SLA printer (StereoLithography Apparatus) is also not ruled out.
CURA 4.10.0 was used as Slicer software. The parameters with which the pieces were printed in my case were: low quality profile with layer height of 0.28mm, 10% cubic infill and support for the pieces and adhesion Raft was used (see picture above for more details).
The material used for printing was (PLA) in Gray color. The pieces were printed in several sessions during the nights. The pieces that took the longest were the NACA 0018 airfoil blades which took about 8 hours each. The other pieces took much less time.
Attachments
Step 2: Glue the Leg Endings to the Pencils
This step is very simple, you just have to place a little hot silicone glue inside the holes and insert the pencils. Make sure the glue is hot enough so that there is a correct bond among the parts.
Step 3: Insert the Bearings Into Their Cavities and Glue the Legs to the Bearings Support
To insert the bearings in their cavities, just press them with your hand, if necessary, gently tap them with a plastic hammer until it has been inserted correctly. They should be tight, however if you consider that you should use some instant glue that fixes them to their cavities you can use it. Be very careful not to get glue inside and block them.
When you have done this, glue the legs with hot silicone making sure they rest correctly on a flat surface.
Step 4: Fix the Small DC Motor to Its Bracket
Insert a 15mm length M4 screw and corresponding square nut into position on the DC motor bracket and do not over-tighten them. Attach the two sliding washers to the DC motor with their corresponding screws and do not over-tighten them either. The washers should line up as shown in the picture. Put the motor in position and turn each washer 90 degrees. The motor should run in the groove, but it should not come loose. If your motor does not have cables soldered in its terminals you can do it now. These cables are the ones that you will use later for measurements and experiments. At the end, insert the whole assembly in its position on the Central Support.
Step 5: Glue the Pencils to the Upper Holder and Fix the Airfoil Blades NACA 0018
The upper support has 4 cavities where 4 pencils should be stuck. To do this, you must place hot silicone glue inside the holes and insert the pencils. The center pencil must be of the hexagonal type! Also glue the airfoil blades to the end of the horizontal pencils. Make sure the upper and lower planes of the Airfoils are contained in the same plane respectively. Make sure the glue is hot enough so that there is a correct bond.
Step 6: Insert the 45 -tooth Spur Gear and Its Spacer
Insert the gear first and then the spacer. They were designed to fit right through the hexagonal body of the pencil. Don't glue them yet! It is advisable to apply some lubricant for plastics between the gears.
Step 7: Attach the Top Support to the Central Support Plus Final Details.
To do this insert the center pencil through both bearings. Then, insert the bottom spacer and glue it flush with the end of the pencil. Adjust the top spacer and top gear so that there is no excessive vertical play. Insert the 10 tooth gear into the DC motor shaft, I recommend using a very small amount of instant glue to stick it on. Adjust the two gears so that they can rotate freely by moving the DC motor assembly forward or backward. When you have found the correct position, tighten the screws on the slide washers to secure them in position. It is very convenient to use some kind of plastic lubricant between the two gears.
In this step you have already completed the construction of your Darrieus Wind Turbine. It is convenient to fix the legs with double contact tape to a base as shown in the photo.
Here are some suggested experiments.
Step 8: Determination of the Tangential Rotation Speed of the Airfoil Blades and Comparisons With a Drag-Driven Rotor
An important aspect in the design of Wind Turbines is the calculation of the tangential speed of the Airfoil Blades in relation to the speed of the incident wind. This is known as the Tip to Speed Ratio (TSR) and it is a determining value in the efficiency of the Wind Generators. For example, it has been shown that a TSR of around 4-5 ( no dimensions) is very appropriate for the efficiency of the generator that we have proposed here.
Regardless of knowing the speed at which the wind is blowing, which is determined by an instrument called Anemometer, knowing the tangential speed of the tip of the Airfoil is a requirement to calculate the TSR. Next we will explain how to calculate the tangential speed of our design when the wind from a house fan hits it.
The tangential speed (v) is determined by the following equation:
v = ω * r and is expressed in (m / s)
ω is the angular speed expressed in (rad / s) and equal to ω = 2π * f, where (f) is the rotation frequency expressed in (Hz)
r is the radius of rotation
Therefore, the tangential speed would be:
v = 2π * f * r
First, we need to know what is the radius (r) of rotation in our Wind Turbine. It would be the distance from the center of the axis of rotation and the center of our airfoil blades. With the help of a ruler we can determine it as seen in the photo.
To determine the rotation frequency there can be several methods. A digital tachometer could be used and the RPM converted to Hz, or as in our case a photoelectric sensor and an oscilloscope were used.
The photoelectric sensor was powered by a 14V DC voltage source and its detection output to the oscilloscope probe. The oscilloscope was set to 100ms horizontal division and 500mV vertical division.
When the maximum revolutions were reached, a capture was made on the oscilloscope screen. By measuring the time elapsed between the first and a fourth pulse corresponding to a complete turn of one of the Airfoils and using the Cursor mode, the period of time elapsed was determined, the inverse of the period is the frequency.
Substituting the values in the equation we obtain the following results:
v = 2 * 3.14 * 5.32Hz * 0.195m
v = 6.52m / s
Converting that value would be 23.47 km / h or 14.58 mph
Similarly, measurements were carried out on another type of rotor, in this case one of the Drag-Driven type. The results were the following:
v = 2 * 3.14 * 2.63Hz * 0.185m
v = 3.05m / s
It is clearly remarkable that the tangential speed in the Darrieus generator is twice than of the other generator.
Step 9: Bonus Tip!
As stated in the introduction, one of the drawbacks of this type of generator is that they have very low torque during start-up, an aspect that in many cases prevents it from being able to start up by itself with relatively low wind speeds. For this, in this project a small electric motor was chosen as a generator, which offered very little resistance in the initial moments of starting up. Once this generator reaches its operating speed, the power that can be extracted from it is much higher. Did you know that you can create a hybrid generator (Darrieus-Savonius) and give it more torque during startup? If you insert the Savonius profiles between the Top Support and the airfoil blades you will achieve this, as you can see in the above assembly.
If you want to improve or modify something of the 3D model created, then I attach a file of the STEP type.
There is another method to quickly reach the required operating rpm in this wind turbine. Do you know which? Let me know in the comments.
I hope it has been interesting and useful for you, see you in a next Project!
Upgrade!!!
I suggest you using the 608-ZZ bearing instead of the 608-2RS, plus important aspects suggested by JayH25 (updated in bill of materials)
I have included a drive-belt system for this wind turbine to compare between different transmission systems. Suggested by xxWJKxx.
I suggest you read all the comments session where you could extract improvements for this system!
Good Luck!
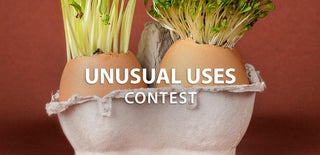
First Prize in the
Unusual Uses Contest