Introduction: Pinch Sticks
Are you square?
Not you personally, is your project square?
Is the corner 90°?
How important is this? That's questionable but different projects require different levels of accuracy. So we use a square or similar for most checks. But what if the item is bigger like a kitchen cupboard or a gate. 0.5mm out on your 200mm square can equate to 10mm at the other end of the work piece.
This is where pinch sticks (pinch rods, squaring sticks, story stick) come into play. This Instructable is about my alternative design on an age old concept.
Supplies
Aluminium square tube (25mm, 20 internal)
Aluminium rectangular tube (17.5 x 10)
ACM (Aluminium Composite Material) - 3mm
Acrylic (8mm)
Threaded wing-nut or a bolt or knob
In theory you can make and use any kinds of materials for this - steel, brass, plastic, wood, but aluminium is light and stiff.
I use what I have, in this case aluminium square tube from a skip, rectangular tube from a dismantled marquee, acrylic and ACM (aluminium composite material- thin aluminium sheet sandwiching plastic) from a skip. The bolts were just from my workshop supplies.
Step 1: Why?
Pinch sticks have been around for hundreds of years in all countries in one form or another. The use of them started to decline when more modern hand tools and measurement systems came about, but at one time every decent tool box contained one or more. There are a variety of modern ones on the market - some quire expensive, but once you understand why you're more likely to use them than not.
The basics are:
- 2 sticks - fixed together in some form when required, but can be lengthened or shortened as required.
- To allow measurement between 2 internal surfaces
- To allow measurement between 2 opposite corners to compare.
If two opposite sides are the same length then the measurement between diagonals will be the same. If the corner is off from 90deg then the measurements will change.
I had an issue where the side lengths were accurately cut the same, but I didn't pick up on the fact that the wood was slightly bowed. I was trying to use my square to set the pieces but couldn't understand why my diagonals were off. By using a ratchet strap I was able to correct the 'bulge' and continue. So potentially using a square and the pinch sticks will resolve most issues.Step 2: Design
The points I wished to cover:
- Use what materials I have
- Allow different length extensions
- Allow exchangeable ends
- Allow self support
So initially I needed pinch sticks to check the diagonals on the workbench I was building so I wanted them to reach around 1800mm. I also wanted to place them in situ and adjust without trying to hold them. Also due to an issue with bowed wood and straps across the work piece I could only sit the pinch sticks above, so the measuring points would need to extend below the sticks.
Also using aluminium tubing would create a very light and long tool and with the other non ferrous materials being used, equalled no rust!
Step 3: Aluminium Tubing
The square tube was cut to 60mm and filed smooth. A hole was marked, drilled and a thread cut to accept a wing bolt.
The rectangular tube - being scrap, was just cleaned up and the plastic inserts were removed from one end. I ended up with 3 pieces 850mm long.
Step 4: 'Pinch' Mechanism
The ACM -plastic sandwiched between aluminium - is light and strong, although you could use an alternative. This acts as a washer between the knob and the bars and tightening the knob applies pressure to stop the bars moving - 'pinching'.
This was cut easily with a hacksaw and file finished. It was done so it had projecting tabs to prevent it sliding out.
Step 5: Is It the End?
The 8mm acrylic was used for the end insert. This was already the correct width and I wanted a deeper profile to extend past the tube to cater for above surface measuring. This was cut and sanded into a 'V' (must be an angle less than 45°). I cut some ACM into a boomerang shape to create my 'self support' bracket. The design of this was so that the form allowed it to rest on the project but didn't obscure the insert point alignment. This was assembled along with the acrylic insert and drilled and threaded to allow a 4mm brass bolt.
Its tight enough to allow the bracket to rotate when not in use.
The acrylic insert could be cut in different shapes to deal with different scenarios. It could be a rectangular form with a nail inserted for instance to allow measurements into tight corners. For now I have stuck with this form but the design allows for other options.
Step 6: In Use...
So I now have:
2x tubes with end inserts and 'self-supports'
1x extension tube
2x pinch brackets
All assembled, equals a tool extension of 2.3m, so enough for my purposes.
As you can see in the photos the self support brackets work well and with the end profile extension allows it to reach the corner even with a ratchet strap clamp in place.
I also tested it as a 'story stick' or an internal measuring tool which worked fine, but I felt the design could be adapted further. Currently the tool does exactly what I want it to do, but I need to push it...
Step 7: Additional Design Element
So the current alloy tube length means I can't measure anything below apx.900mm. if I had more tube I'd cut shorter lengths to deal with this but I don't and I'm not going to cut what I have.
If I use the pinch brackets as they are I can create shorter wooden 'sticks', but I'll design this specifically for measurement transfer.
Two strips of wood 9.5x19.5 were cut, apx 400mm long.
One end was cut to allow the depth of the bracket on one piece. The other piece had an extension glued to one end. A 30° angled cut was done to each piece.
The idea of this is to have an extendable tool with each end flat against the surface so when you transfer the measurement it's more accurate.
Very simple to make, uses the existing bracket and I can create a few different lengths.
I now appreciate why a tool box would have once contained several length pinch sticks.
Step 8: Conclusion
The alloy tube works really well for long diagonals - its light and simple and the support 'boomerangs' work well with the extended end insert. The wooden stick version works well for measuring purposes as well. I need to look at ways of producing end inserts to be adaptive to both but for now it fulfils my design brief.
Thanks for reading
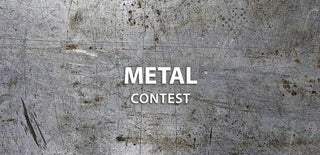
First Prize in the
Metal Contest