Introduction: Pizza Oven Build
We decided to bring life to an under-utilised corner of our garden by constructing a brick and mortar pizza oven. This turned out to be great family activity and now that the oven is built, pizza-building is a regular family activity in our home.
Step 1: Preparing the Base
Clear an area for the base of about 1,5 x 1,5 m.
The foundation is a 100 mm thick concrete slab. The finished level of the slab should be about 50 mm above ground level so that ground water doesn’t run onto the slab, which will become the wood store. Level and compact the base area at a level of about 60 mm below natural ground level. Using shutter board or 114 x 38 pine sections, construct a box with inside dimensions of 1420 mm x 1370 mm (1420 mm is the width of the front end of the oven). Position the box on the levelled base area. We threw a 40 kg bag of river sand into the box and compacted it with a hand stamper to create a good base for the slab.
Step 2: Casting the Slab
Mix 2x 40kg bags of ready mix concrete in a wheel barrow or on a plastic ground sheet (mixing concrete by hand can be quite a workout for the unseasoned builder so try mixing one at a time!).
Cast the concrete directly onto the levelled surface inside the shutter box and level off with a plank. (Our oven happens to be over a manhole, which will still be accessible after the build; we boxed the manhole with polystyrene boards to allow a bit of movement around the manhole). Leave the concrete to cure for at least 24 hours before continuing with the build. The shuttering can be removed after 3 days.
Step 3: Building Up the Base Walls
Now you are ready to start building the base walls. We used a cheap face brick for the outer skin of the wall and a clay stock brick for the inner skin.
The base walls required 118 whole face bricks + 22 half face bricks; 90 whole clay stock bricks + 16 half bricks. We used about 6x 40 kg bags of ready builders mix (there was a lot of wastage due to lack of experience!).
Build up the two side walls 9 courses high on the inner skin and 10 courses high on the outer skin. Lay 13x 100 x 75 x 1200 mm precast concrete lintels across the inner skin on a mortar bed (you may need to trim the lintels to fit using an angle-grinder).
Step 4: Building Up Oven Walls and Floor
Now begin building up the outer skin of the oven side walls. Build up 3 courses using clay stock bricks for the outer skin (these will be plastered over at the end). Each course consists of four and a half bricks.
Before going further, screed over the lintels with a perlite mix (trade name PRATLIPERL http://www.pratleyminerals.com/construction-thermal-insulation). This is fairly dry mix that provides insulation and a smooth base for the oven floor.
The mixture seems crumbly and loose but when squeezed in your hand should form a compact lump that holds its form. Pat down the mixture with a float. Once the screed is laid and leveled, cover it with a plastic sheet and allow it to cure for at least 24 hours. If it dries out too quickly it will crumble. Not only is this perlite screed insulating but it also contains minimum cement and can handle the heat (cement will crack under the heat of the fire).
Step 5: Continuing the Oven Walls
Build the inner skin of the oven walls with face brick. A regular face brick is fired at about 1200°C and should easily withstand the heat of the oven - refractory bricks are not necessary. We used a soldier course which is equivalent to three stretcher courses. Make the joints between bricks as small as possible (about 5 mm) to minimise the amount of cement exposed to the direct heat and reduce the amount of cement in the mortar mixture by half (do this for all oven-facing brickwork).
Plot out the curve of the barrel vault on a piece of hardboard on the ground (or other horizontal surface if there are unwanted obstructions on the ground!). Lay out the bricks in a curve with the fire-facing edge of the bricks touching. Butt joints are used so that cement does not crumble in the heat of the fire and fall into the oven.
The height of the oven should not be more than about 500 mm at the apex of the arch. If the roof of the oven is too high, the oven will take too long to heat up and will lose heat too quickly.
Build the back wall of the oven, cutting bricks as necessary to suit the arch.
Note:
Since this particular oven was built against a double brick retaining wall, we only built a single skin on the back of the oven. For a free-standing oven, a double skin wall is necessary to ensure sufficient thermal mass to retain the heat of the oven.
Step 6: Building the Barrel Vault
Cut two matching pieces of hardboard to make the formwork for building the arches of the barrel.
Screw three or four pieces of equal length timber between the two pieces of hardboard to set them about 150 to 200 mm apart. At this point it would be a good idea to drill two finger holes in one of the boards to facilitate removal of the formwork.
Lay out the bricks for the first arch resting on top of the formwork before committing to mortar. Once you are satisfied that they fit, set them in place with mortar.
We used 40 kg bags of builders mix for the mortar but removed half the cement. The archway bricks with butt joints support themselves so the strength of the mortar is not too important.
Since the brickwork in the arch is self-supporting, the formwork should be able to be removed immediately.
Step 7: Completing the Vault
Shift the formwork along and build the next arch butting directly against the first.
Continue in this way until you have built 4 arches. Then begin to build the outer skin of the vault uisng clay stock bricks.
Step 8: Building the Doorway
Build the doorway walls using stretcher course or soldier course.
Plan the formwork for the arched doorway. The size of the door is important – it must be functionally big enough but not too big otherwise heat escapes. The width should be about 500 mm and the top of the arch about 270 mm. Construct formwork similar to that of the oven vault.
Step 9: Finishing the Oven Floor
It is important to do finish the oven floor before completing the chimney and doorway while it is still easy to reach into the oven.
Screed the doorway floor with screed or plaster mix of about 10 mm thick.
Lay dry plaster sand inside the oven; spread it around and smooth off to be level with the doorway screed.
Lay the oven floor tiles loose on top of the plaster sand bed. We could not find traditional terracotta tiles or refractory bricks so - as and temporary and experimental solution - we used contemporary un-glazed terracotta tiles (300 x 300 x 8 mm). These were cheap at R89/box of 10 and we easily trimmed them to fit using an angle grinder. The tiles in the doorway were installed using tile adhesive to secure the layout, while the tiles inside the oven are loose to accommodate thermal movement.
Step 10: Continuing With Doorway and Chimney
Build an arch over the doorway using half face bricks over the formwork.
Begin building up the chimney behind the arch. The actual cross sectional area of the chimney flue is only the size of one brick. It was a bit tricky as the first course of the chimney cantilevered off the doorway walls and required some temporary support.
The taller the chimney, the better the draw so build as high as you can reach or afford!
We completed the front wall of the barrel, cutting bricks as required to fit the arch. (We only built a single skin brick wall in the front and the heat is transferred through very quickly, so a double skin wall would be better.)
Step 11: Finishing Touches
The outside was plastered with perlite plaster (same as the oven floor screed) to insulate it. This required a bit of skill since the perlite mixture is very dry and tends to fall off if not applied correctly – we patted it on by hand. It is preferable to utilise the thermal mass of the bricks to radiate heat into the oven and insulate the outside to prevent the heat from escaping.
The perlite plaster was not very neat so we smoothed it over with regular plaster. We really liked the look of the oven before we plastered it, so we decided to apply brick tiles over the plaster as a finish with red mosaic tiles on the vertical sides. The pebbles on the front were 'something old' from the derelict water feature that used to be where the new oven now stands. You can decorate the outside in anyway that suits you.
We added wooden doors using old palettes hinged on a wooden frame for the fire wood store under the oven and added a wooden door for the oven. The oven door is loose and merely plugs into place in the brick doorway. We use the door when we are baking bread or roasting meat in the oven.
Step 12: Firing Up!
Before we finalised the decor, we built our first fire to check if the oven held. A few cracks appeared which we still haven't repaired but apart from small give-away streams of smoke, the oven works beautifully!
The biggest problem was the floor tiles, which cracked. We replaced the broken tiles with new ones which we trimmed smaller, thinking that the cracks were due to insufficient allowance for thermal expansion. However, after several trials we concluded that the thin tiles simply could not handle the heat.
After much searching, we found refractory tiles for a reasonable price (Southway Refractories www.southway.co.za). They were only slightly thicker than the original tiles and we could replace the inner oven tiles without needing to disturb the front door tiles, which remain secured in place.
Since the tiles in the oven were laid loose, it was relatively easy to replace them - except that this time the chimney and doorway was already built so access was a little tricky!!
Step 13: The Final Product
The next step is perfecting the pizza. We have learned that pizza is about bread, not toppings and that nothing beats a fresh fired focaccia with family and friends.
For more info on building ovens and making pizza www.fornobrava.com is a good resource. Also visit our website for other projects and paraphernalia https://www.thegoodhome.co.za/blog
Feel free to download plans,the Sketchup model and a bill of quantities here.
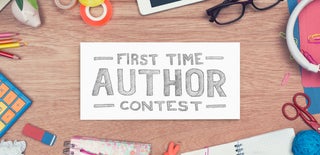
Runner Up in the
First Time Author Contest 2018