Introduction: Plaster Mixer - Made Easy, Easily Made
If you ever mix plaster in smallish batches, and you do it more than once or twice, then you need a mixer. Something to take the elbow greese out of it. Nothing fancy, nothing super long, and certainly not expensive.
In this Instructable we will build a small mixer just perfect for those small jobs. This is the mixer I used in my project titled Laying Your Own Eggs, so to speak.
In this Instructable we will build a small mixer just perfect for those small jobs. This is the mixer I used in my project titled Laying Your Own Eggs, so to speak.
Materials
- 3/8" threaded steel rod - 6 inches
- 1" x 4" x 1/8" flat aluminum
- Two (2) 3/8" nuts
Note: The metal needed can be acquired at most hardware stores and certainly any place that specializes in metal. You will likely have to buy at least three-feet of both rod and flat, however both are often reasonably priced and the unused lengths can be kept for future projects. I always keep stock threaded rod and 1" aluminum flat in my shop. Both very useful.
Tools
- Cut-off saw - or hacksaw
- Electric drill - handheld, drillpress, whatever
- 1/8" and 3/8" drillbit
- Metal centre punch - or a nail
- Hammer
- Metal file
- Vice
- Adjustable wrench
- Marker
- Compound square - ruler or tape measure are fine too
Safety
- Eye protection
Step 1: Making the Mixing Blade
First, let's get our aluminum flat measured for cutting and bending.
I am using a compound square here to give a clean square line. The reason I am marking so close to the end in the photo is that the end was rough and I wanted to clean it up.
The second photo shows all lines marked. The length between end cut lines is 4 inches. The diagonal bend lines are simply 45 degree angles from the cut line. Make your diagonals the same as shown in the photo to ensure proper mixing rotation in he finished tool. The squiggles on either end are simply the areas to be discarded after cutting.
Now would be a good time to measure the centre of your piece. I don't show it marked here because I forgot to do it until it came time for drilling.
In photo 3 you will see the flat setup in a mini cut-off saw. These saws create quick clean cuts in metal, but a hacksaw will work just fine. Use whatever you have handy.
In photo 4 I am using a small deburring tool to remove burrs left from cutting. Very handy tool when working with metal and should only cost a few dollars. Simply filing the ends works well too as shown in photo 5.
Your threaded rod can be cut at this stage also. Just measure 6 inches from the end and mark with a marker. Cut just as you did the aluminum flat, and clean the end with a file. That's it for the rod.
Now, let's move on to the next step.
I am using a compound square here to give a clean square line. The reason I am marking so close to the end in the photo is that the end was rough and I wanted to clean it up.
The second photo shows all lines marked. The length between end cut lines is 4 inches. The diagonal bend lines are simply 45 degree angles from the cut line. Make your diagonals the same as shown in the photo to ensure proper mixing rotation in he finished tool. The squiggles on either end are simply the areas to be discarded after cutting.
Now would be a good time to measure the centre of your piece. I don't show it marked here because I forgot to do it until it came time for drilling.
In photo 3 you will see the flat setup in a mini cut-off saw. These saws create quick clean cuts in metal, but a hacksaw will work just fine. Use whatever you have handy.
In photo 4 I am using a small deburring tool to remove burrs left from cutting. Very handy tool when working with metal and should only cost a few dollars. Simply filing the ends works well too as shown in photo 5.
Your threaded rod can be cut at this stage also. Just measure 6 inches from the end and mark with a marker. Cut just as you did the aluminum flat, and clean the end with a file. That's it for the rod.
Now, let's move on to the next step.
Step 2: Drilling and Bending
Next we drill the centre hole.
Take your centre punch and align to your mark. If you don't have a punch just use a large nail. Aluminum is soft enough to mark in this manner.
Now, clamp down the flat and chuck the 1/8" bit in your drill. Drill through to create your pilot hole.
Change to the 3/8" bit and drill through the pilot hole.
Ok, now let's make our bends. In photo 4 I have the flat secured in a small metal break, but a bench vise will work great too. With the piece securely in place bend to just slightly past 45 degrees. When you release pressure the angle will be 45 degrees. Do the same to the other side.
That is all. Next we assemble everything.
Take your centre punch and align to your mark. If you don't have a punch just use a large nail. Aluminum is soft enough to mark in this manner.
Now, clamp down the flat and chuck the 1/8" bit in your drill. Drill through to create your pilot hole.
Change to the 3/8" bit and drill through the pilot hole.
Ok, now let's make our bends. In photo 4 I have the flat secured in a small metal break, but a bench vise will work great too. With the piece securely in place bend to just slightly past 45 degrees. When you release pressure the angle will be 45 degrees. Do the same to the other side.
That is all. Next we assemble everything.
Step 3: Final Assembly
First take the rod and thread on one nut leaving enough exposed thread for the blade and the second nut.
If you have trouble threading the nut because of damaged threads, try using the other end of he rod. If that end is no better then just file the end some more.
Put the blade and second nut on. Make the second nut flush with the end and hand tighten the first nut down.
Place the second nut in the vice and tighten he first nut with a wrench.
We are all done.
To clean the tool after mixing plaster just let it dry and then lightly tap with a hammer, or against a hard surface. The dried plaster should just fall off.
If you have trouble threading the nut because of damaged threads, try using the other end of he rod. If that end is no better then just file the end some more.
Put the blade and second nut on. Make the second nut flush with the end and hand tighten the first nut down.
Place the second nut in the vice and tighten he first nut with a wrench.
We are all done.
To clean the tool after mixing plaster just let it dry and then lightly tap with a hammer, or against a hard surface. The dried plaster should just fall off.
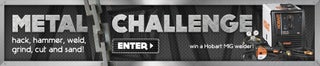
Participated in the
Metal Challenge