Introduction: Plexiglass Space Pistol
This plexiglass space pistol was built with the minimum of tools so that almost anyone could make their own. Can this space pistol be built with only a hand drill, hacksaw, a few files and sandpaper? Absolutely!
Oh, and no gluing required!
I had some leftover florescent orange 3/16 inch and 1/8 inch thick plexiglass that will be used. By using transparent plexiglass, you can have internal components seen from the outside. Use opaque plexiglass if you want a solid color. Using solid colors makes this project easier but transparent colors will show a much more detailed space pistol. This is a somewhat advanced project but worth the effort.
Oh, and no gluing required!
I had some leftover florescent orange 3/16 inch and 1/8 inch thick plexiglass that will be used. By using transparent plexiglass, you can have internal components seen from the outside. Use opaque plexiglass if you want a solid color. Using solid colors makes this project easier but transparent colors will show a much more detailed space pistol. This is a somewhat advanced project but worth the effort.
Supplies
Plexiglass
Scrape wood
Hand drill
Hacksaw with fine blade
Assorted drill bits
Assorted files
Sandpaper of various grits
Assorted fasteners
Heavy Wall Brass tubing
Optional
Power tools, scroll saw, sanders and anything that will help you build this easier. The goal though is to build this with the minimum of tools.
Scrape wood
Hand drill
Hacksaw with fine blade
Assorted drill bits
Assorted files
Sandpaper of various grits
Assorted fasteners
Heavy Wall Brass tubing
Optional
Power tools, scroll saw, sanders and anything that will help you build this easier. The goal though is to build this with the minimum of tools.
Step 1: Design Layout
After you have your design, cut out each shape carefully and tape down on one piece of plexiglass. This was designed on Coreldraw but your favorite program will do just fine. No design program? No problem. Any hand drawn space age looking design will work just fine.
Step 2: Stack and Drill
Stack all the pieces with the taped down design on top and temporarily clamp them together. Drill 3/16 inch holes, where indicated, completely through the stack. These holes will accept the brass tubing used for fastening the layers together. Try to drill the holes as straight as possible.
Step 3: Insert Brass Tubing
Heavy wall 1/4 inch brass tubing should be used. This will allow for tapping threads. Depending on how many layers you use, cut the brass tubing slightly shorter than the total thickness. In this design the total thickness is a little over 7/8 inch so the brass tubing is cut to 13/16 inch. This will allow the layers to be tightened down snugly. Tighten each piece of tubing into the drill chuck and hand cut 8-32 threads about a 1/4 inch deep on each end. Do NOT operate the drill while tapping. The drill chuck is used as a clamping vise "only" while tapping. These brass tubes will be used for alignment throughout the project and for final assembly.
Step 4: Cutting Out the Main Body
After you drill all appropriate 1/4 holes, these will help to keep all the pieces accurately layered while cutting out. Always use wood while clamping to avoid damage to the plexiglass.
Step 5: Stacking and Cutting
Use the brass rod sections to tighten down the layers while cutting. Cut as close and straight to the layout lines to help minimize filing and sanding.
Step 6: Cutting Out the Pistol Grips
Since my leftover plexiglass wasn't large enough, the pistol grips have to be fitted separately to the main body. This goal of this project is to use the minimum of hand tools only. If you have access to a scroll saw or band saw please feel free to use them. This project demonstrates how the lowly hacksaw can be used for more sophisticated work.
Step 7: Fitting the Pistol Grips
It is very important to fit the grips as precisely as possible. After the fit is good, drill through the 2 existing holes into the grips. They are now securely attached. If you have large enough plexiglass, you could eliminate this step since the main body would include the grips. I always say, "use what you've got ".
Step 8: Drilling the Finger Hole
Use the largest drill bit you have or a forstner bit preferably. I drilled a 7/8 inch hole which left enough plexiglass for filing. Use a round file and enlarge the trigger hole until it matches the design. This can take some time so be patient.
Step 9: Adding Wooden Grips
There are many choices when it's time to finish the grips. You could build up several more layers of a different colored plexiglass for a nice contrast. I decided to use what I had laying around. In this case I had some leftover oak flooring. Clamp the wood in your vise and cut out as close to the layout lines as possible to avoid extra filing and sanding.
Step 10: Sanding the Grips
Use the existing holes in the plexiglass and drill through into each half of the grips. Use the same 1/4 inch brass tubing process and screw down the grips securely. Now you can start filing and sanding till each side feels comfortable to your hand. This will take some time. Be patient and sand, sand and sand some more.
Step 11: Finishing the Grips
After sanding to your liking, drill one more hole at the bottom of the grips. You could use the same 1/4 inch brass tubing but I used a heavy walled 1/2 inch brass tube for a more proportional look. I tapped threads for 3/8-16 button caps.
Step 12: Fitting the Trigger
This step was saved for last because this section is the most fragile and needs to be very accurate. Only the inner 2 layers need to be cut out to accept the trigger and spring. You can make the trigger from plexiglass, wood, metal or whatever you have available. I chose brass for a more classic look. The trigger is made with the same basic tools. Drill a pivot hole and file then sand till smooth. Check for fit and adjust as needed. Once the trigger operates smoothly, insert a small 3/4 inch long spring into the slot. The trigger is finished!
Step 13: Drilling Top Vent Holes
Tape down the pattern with the vent holes and drill out with a 1/4 inch drill bit. Always use several of the brass tubing pieces to keep the sections lined up.
Step 14: Internal Design Patterns
Because this project uses transparent plexiglass, it allows for an internal design to simulate the workings of a laser pistol. Cover the inside pieces with masking tape and carefully cut out your design with a razor or xacto knife. After cutting and peeling off the waste tape, make sure the remaining tape is flat and secure. Now spray paint the entire piece and let dry. After drying, peel off the remaining tape and now you have the simulated internal workings of a laser pistol. Repeat the process for the other sections with different designs and paint color for a great 3-D look.
Tip - always paint on the inside of the pieces and never on top. When you're finished, the paint is protected forever.
Tip - always paint on the inside of the pieces and never on top. When you're finished, the paint is protected forever.
Step 15: Final Sanding and Polishing
All leading edges should be rounded over and sanded smooth. Start with a small flat file and work until all edges have a pleasing look. Use a half round file for all inside curves. Now sand all edges until they feel buttery smooth. Ideally you should start with 120 grit sandpaper and work up through 400 or so. Partial disassembly is required to sand all parts.
After final sanding, use a plastic polishing compound and buff the entire pistol.
After final sanding, use a plastic polishing compound and buff the entire pistol.
Step 16: Adding Embellishments
This space pistol is basically finished but adding small embellishments creates extra detail. Cut 7 small lengths of the 1/4 inch tubing and insert into the top vent holes. If you want to add a front emitter (recommended), find something that looks interesting and attach by drilling into the front end and tapping the appropriate threads. Keep it simple and don't add too much.
Step 17: A Finished FLORESCENT Laser Pistol
This is not an easy project but the end result is something you can enjoy for many years. Since the plexiglass is florescent, it has a fantastic glow when lit. You could install a small battery and led or build a 120 volt base that it sits on and then you have a futuristic table lamp with a detachable space pistol! I intend to build a lamp base in the near future.
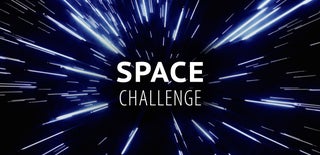
Participated in the
Space Challenge