Introduction: Procrastination Station/ Hands Free Phone Bracket
I AM SICK AND TIRED OF DROPPING MY PHONE ON MY FACE!!!
If you're anything like me, you are a serial procrastinator. And so, after a long hard day you just can't wait to curl up in bed and watch some YouTube on your phone for hours on end. The only thing is that holding a phone in bed is one of the most frustrating things ever, especially if its connected to a charger. My arm cramps up and so I keep needing to change arms, and often I drop my phone on my face which isn't fun at all... in fact it hurts like hell.
I need something that will hold my phone which is fully maneuverable and which can lock into place wherever I need it. The phone needs to be able to swivel so that I can accommodate different positions in bed like lying on my side or sitting up or lying on my back. It also needs to be able to fold away for when I'm not using it. I would also like to incorporate a charger.
I'm on a student budget and only have limited tools so I'm definitely going for practicality over aesthetics.
This is what I came up with. I'm dubbing it the procrastination station or the YouTube watching station. I hope you enjoy :D
Step 1: Step 1: Materials and Tools
Materials:
As I said before, I'm on a student budget so I often just used whatever screws and hardware I could find in the garage but i'll try to make a cohesive list. I got all my lumber (pine) from the local hardware store.
Note: all measurements are in millimeters as that is the unit that lumber and tools comes in where I live.
- Four 22 x 22 x 1800 boards to make the beams and wall rail.
- One 12 x 94 x 1800 board to make the back of the wall rail which will be mounted to the wall
- One 22 x 44 x 1800 board to make the rail cap and the train
- One 22 x 94 x 250 board to make the swing mount.
- Various screws, use whatever works for you.
- M8 Lag bolt
- M8 T-Nut
- 2 small cabinet hinges.
- Two 6x60 nail in anchor (depends on your wall so use whatever suits your needs best).
Tools Used:
- Cordless drill/driver (used for drilling pilot holes and fastening screws)
- Anet A8 3D printer (this was used to make the phone mount swivel but one could also modify a shower head or just buy a mount pre-made if you do not have a 3D printer).
- Sandpaper
- Wood saw
- Pencil
- Tape measure
- Carpenters square (not essential but nice for laying out straight cuts)
- Hammer
- Countersink Bit
- Drill bits (3 mm, 8 mm, 10 mm)
- I don't have a vise so I often used a G-Clamp to stabilize my work.
- Miter box (if you aren't confident in your ability to make square cuts)
Please keep safety in mind. Only use tools which you are comfortable using.
Step 2: Step 2: Building the Rail
I need the adjustable arm to be able to move up and down. This is because I chose to go with a one arm system so in order to reach places close to the wall the shoulder of the arm needs to move up and in order to reach places further from the wall the shoulder needs to move down.
The rail acts like a t-slot with only one lip (see image)... so I guess it's an L rail.
Start by marking and cutting all your beams to length. I made the back plate 1300 mm and the rail sides and cap 1200 mm (see image). This gives me 50 mm of room on top and on the bottom where I can comfortably mount the rail to the wall.
Clamp the sides into place and pre-drill pilot holes from the back, be sure to do this or the wood will split. Use a counter sink bit so that the rail lines up smoothly with the wall. Then screw screw them in. I placed screws every 30 centimeters or so (like every 12 inches for you imperial folk ;)
Repeat this process for the rail cap. I managed to screw everything from the back so that none of the screws are visible. But if this does not bother you just screw from the front and it will save you a lot of hassle.
Step 3: Step 3: Building the Train
This is the connection between the rail and the bracket mechanism. It is what slides through the rail. I was initially going to make use a T-Slot style rail and train but the lumber dimensions didn't really line up so I decided to go with a L-Slot. The train is made using the 22 x 44 off-cuts of the rail cap.
Start by marking and cutting 2 pieces of length 250 mm. Sand down any blowout to make ends smooth.
Insert these two pieces into the rail as shown. Align them so that there is a little bit of play so that the train will slide easily on the rail but tight enough as to maintain rigidity (it should not be loose).
Then mark where the two pieces line up so that you know where to join them. Remove the 2 pieces from the rail and clamp them together along the line. Then, using a countersink drill bit, pre-drill the holes so that the wood doesn't split and so that the screws will sit flush and not cause the train to stick in the rail. Then screw the two pieces together.
Test the train to see that it slides easily but steadily in the rail. If there are any tight spits, just sand them down until everything slides smoothly.
Step 4: Step 4: Hinging the Swing Mount to the Train
The swing mount will allow the whole bracket mechanism to swing from side to side. It will allow me to fold the mechanism away against the wall when I am not using it, as per one of my requirements.
The mount is made from a piece of 22 x 94 mm board. Mark, cut and sand this board in the same way as shown previously to a length of 250 mm.
The mount is attached to the train by the 2 cabinet hinges. However these hinges are quite loose out of the box and swing freely. This is not good as it means that when I position the arm somewhere, it wont stay put. I therefore need to make the hinges tighter to increase the friction in the hinge. I did this by giving each hinge a few good whacks with a hammer. This upsets the concentricity of the hinge and makes the hinge tighter. After this the hinges moved tightly and steadily, just as intended. I quite enjoyed this McGuyver-esque solution as it goes rather well with the whole 'lazy life' theme.
Then lay out and mark where the hinges should be placed (see image). Leave a small gap so that nothing interferes with the motion. Then Screw the hinges down with the screws provided with the hinges. I did not pre-drill these as the screws were so small and unlikely to split the wood (they didn't...phew!).
Step 5: Step 5: Making a Torque Handle and Tightening System
The brackets that will hang over my bed will be able to pivot up and down from their shoulder at the swivel mount. But I need a way to lock them in place otherwise they will just fall on me once I have positioned them (which wouldn't be ideal). I decided to go with a tightening system which will use friction to lock the arms in place. Once I have positioned it, I will tighten joint with a torque handle.
Torque Handle:
The torque handle was made using a scrap piece of wood from the off-cuts of the previous steps. Drill a 10 mm hole in one end and hammer the M8 T-Nut into it. I then attempted to carve a handle with a kitchen knife (the only knife I could find at my parents house) and failed miserably. Please forgive my carving skills!
Tightening System:
On the Swing Mount, mark out where the 2 beams will pivot from. I made this 200 mm apart. This will be the base of the parallelogram arm system. One of the holes must be larger as it will accommodate the lag bolt which the torque handle will tighten against. I chose the bottom hole as it will be closer to the bed and easier to reach.
Drill an 8 mm hole at that point. Then place the M8 lag bolt through and hammer it into the wood. This will secure it in the wood and will prevent it from turning with the torque handle.
Drill a pilot hole into the top hole. This will be the pivot point of the top beam of the parallelogram arm system.
Step 6: Step 6: Making the Bracket Mechanism Part A
I have chosen to go with a parallelogram system for the bracket rather than just one beam. I chose this because in my mind it seems like it would be stronger and more stable. I also find it really cool the point where I will mount the phone will always stay level since the one side of the parallelogram will always stay parallel to the wall.
Cutting the Arms:
The 22 x 22 mm beams are used for the arms. First cut the arms to length. I used a length of 1000 mm but this will really depend on the type of bed you have. Unfortunately I accidentally split one of the beams rendering it unusable so I had to screw 2 pieces together to make one of the beams (see photos) since I didn't have enough wood to start over. It's ugly but it isn't a huge deal since I'm going for practicality over aesthetics... and I'm just too lazy to go to the store to buy another beam.
Drilling and Screwing
It is very important that the distances between the holes in both arms are the exact same length, otherwise the parallelogram won't work out and the bracket will either seize up or will not remain level, defeating the whole purpose of the system.
I therefore clamped the pieces of wood together and drilled the pilot holes at the same time. Be careful to drill straight and square. Since one of the holes (at the base of the bottom arm) needs to be large enough for the lag bolt to pass through, I enlarged this hole to 8 mm. The rest of the holes are then countersunk.
The top arm can now be screwed onto the Swing Mount using a screw which only has thread on the bottom half. This allows the arm to pivot around the smooth part but the screw to remain in the swing mount.
The bottom arm is free to pivot around the lag bolt between the Swing Mount and the Torque Handle.
Step 7: Step 7: Making the Bracket Mechanism Part B
The bracket mechanism is now complete on the wall side. On the other side, in order for the parallelogram mechanism to work, the arms need to be kept at the exact same distance on their other ends (200 mm) since that is the distance between their pivot holes as described in the previous step. This piece of wood will also be where the phone will be mounted.
I therefore cut a piece of 22 x 22 mm beam 300 mm long and marked positions 200 mm apart. I chose 300 mm because I want the point where i mount the phone to protrude slightly from the bracket mechanism. I then drilled pilot holes and countersunk them in the same manner as before.
Using the same screws as before with thread only on one half, I screwed the free ends of the arms to this beam.
The Bracket Mechanism is now complete! Now all that remains is the phone mounting mechanism and then we can put it all together and mount it above my bed!
Step 8: Step 8: Ball Joint Swivel Mechanism (3D Printing)
Now that the Bracket mechanism is complete, I needed a way to mount my phone onto the end. Since the bracket mechanism will always stay level, I need the mount to be able to swivel and tilt etc.
Swivel Mechanism:
I got the idea of using a ball joint. At first I thought of modifying an old shower head, which would work but would be time consuming and tedious and frankly I'm far to lazy to attempt that (but you can definitely do that if you dont have a 3D Printer!). I just built a 3D printer (Anet A8) so I decided to print one out of PLA plastic. I then went on Thingiverse.com and found a design which was perfect for my needs.
The "Universal ball joint set - D25mm ball" by kel can be found at: https://www.thingiverse.com/thing:1679540
I downloaded the STL file and sliced it in Cura (a free slicing software for 3D printing which can be found at: https://ultimaker.com/en/products/cura-software ).
I then printed the .gcode file on my 3D printer. I was quite pleased with the result. I just used the standard recommended settings on Cura with 20% infill and build plate adhesion. There was quite a lot of stringing on the print but this was easy to remove. After cleaning it up a bit with some files and clippers the ball joint worked perfectly.
Phone Mount:
I found an old phone holder which clips on to the air con vents in a car. I decided to use this to connect my phone to the Ball joint. I was initially going to try and break it apart to remove the vent clips and somehow glue it onto the ball joint, however I discovered that the vent clips can actually clip onto the ball joint very securely. In the spirit of 'laziness', I decided to go with it. It works great!
Step 9: Step 9: Attaching the Ball Joint to the Bracket.
I marked the 3 small holes of the ball joint onto the Bracket. This is a very small area of wood and is end-grain so it is very likely to split. So its very important to carefully drill pilot holes.
Then I carefully screwed the ball joint cup onto the bracket using the smallest screws I could find.
Step 10: Step 10: Finishing Touches + Mounting the Bracket to the Wall.
Drilling the Vertical Adjustment Holes.
Obviously I don't want this thing to fall on me when I'm in bed so I drilled some holes in the rail so that I can set the train at whatever height I want and it will stay there. I drilled 5 mm holes and countersunk them just to make it look nice. I used an old broken key as the stopper. I just sawed off the key part and made a pin.
I also drilled 2 holes at the top and bottom of the rail which will be used to mount it to the wall.
Mounting the Bracket to the wall
I first set the rail where I wanted it on the wall. Then I marked where the top hole needed to be drilled. I HATE DUST. So I took every precaution to prevent the brick dust from falling on my bed. Making a shroud from an old coffee cup and a lot of tape, and duct taping a dust pan to the wall worked relatively well. Remember to use hearing protection when drilling!
After drilling one hole and mounting one end to the wall using standard nail-in-anchors (6x60mm), I used a level to make sure the rail was plum and marked the second hole. Then I repeated the anti dust process, drilled the second hole and secured the other end of the rail to the wall.
I then slid the train onto the rail. GREAT SUCCESS!!! The bracket is now fully installed.
Attaching the Charger
I wrapped the charger around the arm. It is secure enough and it allows me to remove the charger if I need to. I also left slack in the extension cable so that when/if I lift the bracket, the charger doesn't pull out of its socket.
Step 11: FINISHED!!!
This project took me about a day and a half to build but I wasn't spending all of my time on it. You could definitely get it done in an afternoon, especially if you aren't documenting it.
The bracket works exactly as I was hoping. Its not the most beautiful of structures, and had I had more time and more money and more tools I could have made it look nicer (nicer wood, paint, better hardware etc). But ain't nobody got time for that! Anyways that was never my goal. I always favored practicality and cost effectiveness over aesthetics. It was really cheap to build. My only expense was the wood and the hinges. I had everything else (old screws etc).
And you really don't need any fancy tools to build this! The only specialty tool I used was a 3D printer to print the ball joint. But if you don't have one you can modify an old shower head or any other item you may have which uses a ball joint.
The bracket gives a wide range of movement. I can really position the phone wherever I want. It's also great that I can charge my phone at the same time.
Overall I'm super happy and would highly recommend this build to anyone who wants to NEVER DROP YOUR PHONE ON YOUR FACE AGAIN!!!
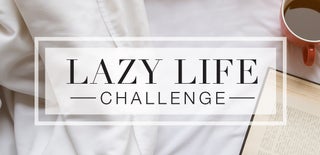
Runner Up in the
Lazy Life Challenge