Introduction: QR Code Logs
In my home town of Doylestown PA, we have a Native Plant Demonstration garden in one of our parks to show our residents what types of native plants they can plant in their own gardens. One of our members suggested that we place QR codes throughout the garden that visitors could scan with their phones to learn more about native plants and animals. I was looking into ways to do this with my 3D printer, but a block of plastic didn’t really feel in the spirit of the garden.
Flash forward to one of our work weekends. We removed a dead crab apple tree from the garden and cut into large logs to toss into the scrap pile. Felt like a waste to me to just toss perfectly good wood. Suddenly, a lightbulb went off in my head and I realized I could make this log into QR codes. What better way to add QR codes to the garden than with a log that was part of the garden?
Now I just had to figure out how to do it. After a couple failed ideas, here’s how I was able to “print” QR codes onto these logs and protect them from the weather.
Supplies
- Hand saw (or chainsaw)
- Paint brush
- Polycrylic
- Laser printer
- Masking tape
- Plastic card (like a gift card or similar)
- Epoxy resin
- Acetate sheets
- Toothbrush
- Heat gun (or hair dryer)
- Black marker
- Hobby knife
- Aluminum trays
- Painter's pyramids
- Plastic cup
- Popsicle sticks
- Car wax (rub on)
- Car wax with carnauba (spray on)
- Palm sander
- Sandpaper (120-3000 grit)
- Disposable gloves
Nice to Have (but not necessary)
- Bucket
- Sponge
- Sanding block
- Scrap metal
- Wood screws
* Links aren't necessarily what I used, but to give you an example of what I'm talking about if I'm not clear
Step 1: Cutting the Log
First step is pretty straightforward. I took the log I got from the garden and cut it into 10 slabs. I used a handsaw to do this part. If you have a powered option, like a chainsaw, I would recommend that instead. Unless you really want the arm workout.
Step 2: Wait
For a dead tree, the log still had a good deal of moisture in it. I waited a few months for the slabs to dry out.
As they dried, cracks formed in the wood. These will be addressed later with some epoxy resin.
Step 3: Sand the Slabs
Using a palm sander with 80 grit sandpaper, sand each of the slabs donate a smooth surface to work on. Since this isn’t going to be the final surface, it's not necessary to sand it further with finer grits.
Step 4: Creating the QR Code
I used the website https://www.qrcode-monkey.com to generate the actual QR codes. On this site, you can generate QR codes for various tasks. For this project, the goal was to link the user to a website where they could learn more about native plants, so I chose the “URL” option. I also added a custom logo to it, denoting the markers 1-9*. Finally, I went to “Customize Design” and choose some shapes that fit more with a garden theme.
I set the quality to the highest possible at 2000 x 2000 pixels and downloaded the generated code as a PNG.
To make the image transfer work, the QR code must be made into a mirror image first. Otherwise, the image will appear backwards on the wood.
Open the QR code image in an image editor and then flip it horizontal. I used Apple’s Preview. In Preview, go to the menu and select Tools -> Flip Horizontal. Scale the image to a size that fits your project dimensions.
* By the end of project, one of the logs met an unfortunate accident. So when you see only 8 logs at the end...now you know the horrible truth!
Step 5: Print the QR Code
Using a laser printer, print the reversed QR code. Only the type of ink used in a laser printer will work for the image transfer.
After printing, cut off the excess paper around code.
Step 6: Apply Polycryclic to Wood
Use your paintbrush to apply several layers of Polycrylic to the surface for the wood slab. I found that 3 coats worked the best for getting the image to transfer.
Step 7: Place the QR Code on the Wood
Take the print out and place it on top of the wood. Make sure you know where you want to place the QR code before putting it on the Polycryclic as it will be difficult to move after making contact.
Try to minimize how much the QR code is covering the cracks in the wood. A high resolution code will still read with some cracks in it, but there are limits.
Step 8: Smooth Out Air Bubbles
Take a plastic card, like a gift card and use it to smooth out the paper against the wood. Try to remove any air bubbles.
Probably best to avoid using a card you care about, like a credit card. You’ll likely get some Polycrylic on the card. You can just wipe it off, but why risk it with a credit card?
Step 9: Let It Dry
Let the paper and Polycrylic dry for at least an hour.
Step 10: Get It Wet
Now it’s time to remove the paper and leave the ink behind on the wood. To do this, get the paper nice and wet. It helps to have a sponge and a bucket of water. You could also do this over a sink if you don’t mind bits of paper in the sink.
Step 11: Rub Off the Paper
Using your fingers, rub the wet paper until it starts to roll up and peel off of the wood. Gently rub the paper until most of it has been removed. Take your time and don’t rub too hard or you may take some of the ink off of the wood.
Step 12: Remove the Remaining Paper
After removing most of the paper with your fingers, some paper will still be left behind. Take a toothbrush, dip it in water and use the the toothbrush to go over the QR code. Take gentle, circular motions to scrub off the remaining paper. Like with your fingers, don’t brush too hard to avoid taking off the ink. It will take a few passes to remove the remaining the paper.
Step 13: Dry and Repeat
After everything is nice and wet, it may look like all the paper has been removed. You can double check by drying the log and seeing what’s left behind. The log will eventually dry naturally, showing the left over paper. If you’re impatient like me, you can use a heat gun or hair dryer to speed things up.
If there is still paper remaining, use the brush again to keep removing it. This may take a couple times to get it down to an acceptable level. You don’t have to get 100% of the paper off, but sections that are still pretty white should be removed.
Step 14: Touch Up
Even if you were gentle as possible, some of the ink may have been removed accidentally. No worries. Get a black permanent marker (or the color you printed in) and touch up any gaps on the QR code.
Scan the code with your phone to make sure the code actually works!
Step 15: Coat With Polycrylic
Take your paint brush and Polycrylic and apply one more layer to the log to protect the ink on the wood. If there is still a little paper left, this should blend it in and it shouldn’t be noticeable.
Step 16: Prep for Resin Coating
Since the logs are going to be out in the elements, I wanted to give them some extra protection that would protect both the wood and the bark on the outside. I decided to coat them in epoxy resin to give them protection that would also fit into the nooks and crannies of the bark.
Since my logs had large open wedges in them, extra steps had to be taken to fill in the gaps. I took a piece of acetate sheet and cut out a piece that covers the bottom of the gap. I tried both square pieces and pieces cut to exactly the shape of the wedge. I found better success with the fitted pieces. Tape the acetate piece to the log to cover up the gap.
After the gap is covered, take strips of masking tape and cover the rest of that side of the log. Make sure the strips overlap to try and prevent resin from seeping in under the tape.
Flip the log over and use a hobby knife or razor to trim the excess tape to match the border of the log.
The resin will run across the top of the log, down the sides and onto the bottom. The goal is to get as much of that run off on the tape as possible to make it easy to remove and to not mess up the bottom of the log with stalactites of resin.
Step 17: Pour the Resin
Take an aluminum tray, like the ones used for cooking, and place some painter’s pyramids in it. Rest the log on top of the pyramids, masking taped side down, trying to make it as level as possible. Stack the pyramids if necessary to make a more level surface.
Wearing disposable gloves, mix up the two parts of resin in a plastic cup according to the instructions. Slowly pour the resin on top of the log. Coat the top and let it pour down the outside of the log. In my case, I also let it pour down in the wedge to coat the inside and rest on the acetate sheet.
Use a popsicle stick or similar tool to smooth out the top and push resin into the nooks of the bark on the outside. If you’re having trouble getting resin into certain cracks, pour the resin along the popsicle stick and guide it into the desired places.
Use a heat gun or hair dryer pointed at the resin to remove any bubbles.
Take a second aluminum tray and rest upside down on the other tray to keep dust and other debris from falling into the resin. Allow it to cure over night.
Step 18: Remove the Masking Tape
Flip the log over and remove the masking tape. Use a hobby knife to remove the difficult sections and the acetate strip.
Step 19: Repeat on the Other Side
Repeat steps 16 - 18 on the other side of the log. To keep water from seeping into the wood and damaging it, aim to encase the entire piece in resin.
Step 20: Fill in Gaps
Unseen holes or porous wood and soak up resin while it’s curing. It may be necessary to pour additional small amounts on those trouble areas.
For my logs, I decided to completely fill in the wedge gaps to make sure water couldn’t get in there and risk splitting the log from the inside.
Step 21: Sand Out Any Imperfections
Even with precautions above, resin can get into troublesome places. Bubbles may have appeared or resin got under the masking tape causing it to look rough instead of glass smooth.
Using sand paper and a sanding block, sand out any issues. Start at a low grit like 120 and work your way up to an ultra fine 3000 grit.
Step 22: Finishing Touches
Even after the ultra fine sand paper, there may still be scratches to work out. Take car wax and follow the instructions to rub it onto the resin. When dried, buff it out.
To take it a step further, use a car wax spray with carnauba. Follow the instructions and buff it out to finish.
Step 23: Installation
The original plan was to rest the logs on the ground throughout the garden. However, one of our volunteers had a metal shop and offered to put the logs on stands off the ground. He made a set of metal stands and screwed them onto the back of the logs.
Last step was to place them on the trails and spread the knowledge.
If you're ever in Doylestown, come check them out!
Step 24: Additional References
I learned the technique to transfer images to wood from this Instructable by Fix This Build That. If you would like to learn more about the Polycrylic technique, or other image transfer methods, check out their Instructable for more information.
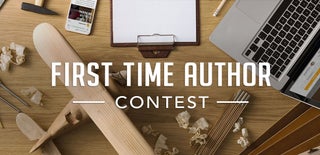
Participated in the
First Time Author Contest