Introduction: Quick Morse Code Practice Board
For a long time I have had interest in radio communications but never had the time to pursue it. With a bit of pushing from some friends at work and a little bit more free time that I have gained I decided to go for it. After a good deal of study I have recently passed my HAM radio exams and earned my Armature Extra license. A lot has changed from when I was studying on and off in the past like no longer having any requirements for Morse code.
Part of the intrigue for me of course was this romanticized interest in that form of communication. I decided I still wanted to press onward more and finally learn this as well. My wife knowing this figured she show me her support with a gift of a basic Morse key. It was meant more as a symbol and a gesture but I loved that she was thinking of me and I wasn't going to let it just sit on my desk. So I figured I should incorporate it into something to aid in my learning and build a self contained practice setup.
With this project you can make it as simple and quick as you like or go for more. It is all up to your goals, the parts/tools you may already have available, skills, and/or your patience. This doesn't have to be an art piece to be useful and educational. Take this tutorial as a general guide and make something that is yours however you can or like. Don't be afraid to step out of your comfort zone and push yourself as long as you are having fun and are being safe!
Supplies
Oscillator:
Options:
- Signal / function generator [Amazon]
- DIY signal generator project kit [Amazon]
- Premade code practice oscillator [DX Engineering]
- Scratch built oscillator from diagram (555 timer based or dual transistor)
- Multimeter / Ohm meter (with resistance testing sound mode)
- Piezoelectric speaker / buzzer
Since we do not want to be practicing live on the air this component is the most important. This is what is going to be driving the auditable part of this device that you will be hearing and it is producing what is called a sidetone. A sidetone is a sound just for the operator and is a feedback mechanism that helps indicate activity in the system.
The familiar tone of Morse code that most people know is anywhere between 600 hertz (Hz) and 800 Hz. That measurement of hertz describes the number of cycles a wave goes through in a second. The smoother this produced sound wave is the more pleasant to the ear it will be. To get the best tone we would want it to be as close to an ideal sine wave as possible.
There are adjustable generators available that will produce sine waves that work within the rages we need and are relatively affordable. You can use off-the-shelf units that are ready to go out of the box or you can spend the time and build a kit yourself. Besides sine waves these units usually are also able to generate triangle and square waves. For the quality of the sound being produced best is sine, then triangle, and last square.
If you are wanting something a little more special purpose you can find code practice oscillators that are made for only the task of producing a fixed frequency tone for Morse. These will usually have a single set frequency and might not be filtered to produce the kindest of sounds but get the job done. They are usually of the same kind of configuration as building one from scratch using the many available circuit diagrams out there.
Going even simpler you might already have a multimeter on hand that makes noise when testing for continuity checking resistance (ohms). This is a really quick way to making sound with little to no hassle and is mostly self contained without the need for much additional wiring. If you want to stick with the same level of simplicity you can use a piezoelectric speaker or a buzzer instead. All these need is voltage applied and nothing else to make a tone.
For my build I went with what I already had on hand and used a function generator. This allows me to get a very pleasing tone I like as well as tweak it to find my sweet spot to make it easier to stand for longer practice sessions.
Morse Key:
Options:
- Scientific / electronics project kit telegraph key [Amazon]
- Mini classical Morse code key [Amazon]
- Momentary switch / button
- Modified clothespin
No matter what you call it or what you are using we are just making a momentary connection and thus completing a circuit. The only real difference between your options is mostly about comfort and feel. Using something that is closer to a classical Morse key will in the end help you build an overall better technique. But since we might just be building this to learn the patterns and general timing we can start with just about anything.
Mounting Board:
Options:
- Scrap wood
- Edge routed board
- Craft board
- Wooden plaque [Amazon]
If you want to save time this is a piece to do it with. You can make this project as functional or as artistic as you want. If you just want mobility and keeping everything together just cut off a piece of random board and get to work. You might be a little more DIY as you can use a nicer piece of wood and edge route it yourself to make it pop. For me I wanted something a little bit more grab and go and went with a premade plaque board but could have just as easily went with any number of other craft boards.
Coating and Sealing:
- Paint or stain
- Polyurethane or wax
This is another part that you can save time or take as long as you want or need. Making your board presentable as you would like can take a lot of repetitive coating steps and most of it is waiting for those coats to dry. What you want to do or how you want it to look is totally up to you. Maybe you prefer a more classical look and will take the time to stain and wax your piece or feel the bare natural wood is more your style.
I chose I would use whatever I already had on hand and give it a uniform color and sealing. Every product is different in how long it takes to dry and the procedures for doing multiple passes. Make sure you follow the instructions for your specific product choices if you do decided to coat your board.
Wiring:
- Siliconized stranded wire
- Dual row strew terminal strip / block [Amazon]
- Forked wire connectors [Amazon]
Depending on what you have chosen for your oscillator / sound source you might not need any of this. I went the route I did so I could swap out parts for different configurations as I needed. If you are needing wire a good go-to for me has always been automotive wiring because I can run out and get it in a pinch. But for this project I just collected some wiring off an old computer power supply that has died.
Not all wire connectors will work will all sized wires and you will need to make sure you pay attention to the gauges. The connectors I used came with my terminal block and were just a bit loose but I stripped the wire a little longer then folded and twisted before I crimped.
I wanted a mix of showing and hidden wires in my setup and routed some of it under the board. You could also leave everything out on top and not need to manage them, drill any holes, or even put feet on the board. The style is all up to you and if you want to spend the extra time or not. You can always start with whatever is simplest for you and step your way up over time.
Audio Out:
Options:
- Electronics project speaker (stand alone / bare)
- Headphones wired directly (via cut off audio plug)
- Audio jack with wire terminal block (3.5mm female) [Amazon]
Again depending on what you are going to use for your oscillator / sound source you might not need any one of these. Only if what you are going to use doesn't already have something incorporated to make a tone audible will you need to figure how to get it outputting.
Tools:
- Pencil / pen
- Ruler
- Drill press / handheld drill
- Assorted drill bits
- Screw driver
- Terminal crimper / plyers
- Wire stripper
- Scissors
Hardware and Miscellaneous:
- Sandpaper
- Wood screws
- Zip ties
- Zip tie anchors
- Mounting Velcro
- Double stick tape / mounting tape
- Shims / popsicle sticks
- Rubber cutting board feet [Amazon]
Safety and Cleanup:
- Eye protection
- Disposable half mask or respirator
- Disposable gloves and/or solvent resistant gloves
- Ear protection for power tool use
- Paper towels
- Terry cloths or other clean rags
- Clean water
- Bucket for water and rags
- Trash bags
- Big box or enclosure to paint in
Step 1: General Idea
As previously discussed there are many ways to get sound out and wire it all up. Pictured above is a small sample of some of the ways to use these different configurations. My build uses a function generator and an audio jack so it corresponds to the first drawn diagram. Just keep in mind if using stereo headphones and want to hear your tone in both ears you will need to make sure your signal splits and goes to both left and right sides of your plug.
Step 2: Board Layout
Taking all your main components you will want to lay it all out and figure what looks and feels right to you. If you are going to do any routing of wires under the board you will need to mark where you will be drilling holes later. Since I was already going to be drilling holes I figured I would mount my audio jack with zip ties through some holes as well.
Step 3: Drilling Holes
Once you got you positions of your holes planned it will be time to drill them out. The size of your holes will mostly be determined by the sizes of your bundled wires and the connectors you might be fitting through them. I would suggest to drill a little bit bigger than you might think to allow for some wiggle room in maneuvering. For a little flare you might also want to consider using a counter sink bit to add some bevels to your holes after you drill them. Please remember to use appropriate eye and ear protection when using power tools.
Step 4: Sanding
After drilling your holes you might want to smooth out some of the sharp edges or possible splintering. If you are going to be coating your board you might want to sand everything to get the surface finish you will want. Even if you are not going to be painting or something you might want to still think about doing this since you might rest you hands on this.
Step 5: Painting and Sealing
Take your time and be patient when coating your board. Make sure you have good ventilation and a mask, something to spray over / into, and follow the suggested instructions of your products.
Step 6: Mounting Rubber Feet
If you are going to be adding feet to your board you will want to make sure to not put them right on the edge if you have some sort of decorative edges. You will want to measure this edge to make sure you set you feet back far enough not to have any screws poking out the top side. If you will not be routing your wiring under the board this step is totally optional.
Step 7: Audio Jack
If you go any of the generator routes that does not have a speaker built in you will need to add an audio jack (or wire you speaker or headphones directly). Since I will be using a pair of stereo headphones there is both a left and right terminal as well as a ground on my jack. You will need to strip your wires and screw them into the associated terminals. If your wires are loose like mine you might also want to add some zip ties to keep them all neat and together.
Step 8: Screw Terminals
Before moving on to any more wiring you will need to secure your screw terminal down now if you are going to be using one. Make sure to grab some wood screws that will match up to the same size holes as your terminal has for mounting.
Step 9: General Wiring
Even if you are using screw terminals you might not choose to use the connectors and use the stripped wires directly. If you do want to use the connectors be aware they are meant to be crimped to have a mechanical connection. Make sure even when you are crimping that the wire does not move around after you have made the connection. You can either use a specialty crimper or you can with some effort pinch them with a pair of plyers.
As for the actual organization and flow of the wiring will totally depend on prior choices you have made as well as the physical layout of your board. If you are going the same route as me refer to the general idea diagram from earlier and look over the pictures here. Note that with dual row terminals the one side is electrically connected to the other side within the terminal block itself. Where you see two wires coming off the same screw on one side it is splitting the signal in two from the other side.
Step 10: Shimming
If any of your parts are like mine and have hollows you will want to add shims to fill them out. Here I just cut and use popsicle sticks and double sided tape until I had it where I needed it.
Step 11: Mounting the Oscillator and Key
Since I wanted to be able to swap out parts, or use my function generator on something else, I chose to Velcro mount my pieces for easy removable or replacement. Do not try to stick the Velcro independently on the board and your parts and hope they line up. Combine the pair on your removeable parts and then place them together on the board. This will keep everything lined up.
Step 12: Wiring Up the Key
Wiring up your key should be rather straight forward. In most of your possible options you will be just connecting two posts to your screw terminals. If using a commercial Morse key you might find that it has an audio jack as well. You can wire another one and use a regular audio cable if you would like. You can also get an already made cable that has the plug on one end and connectors on the other or make one yourself.
Step 13: Wiring the Oscillator and Routing
Depending on your choices you might be stuck dealing with a decent length of device specific wiring. I didn't want to modify or make a custom one so I just routed it under the board. Here my function generator uses a BNC to alligator clip harness. I fished it under the board and used some sticky zip tie mounts to keep it in place. You could choose to just use some tape to hold it in place or some short screw to zip tie to. The alligator clips go to two wire connectors that I removed the covers from and crimped them without any wire.
Step 14: Practice and Enjoy!
Now it is time to stand back and admire your handy work! Feel free to experiment with different tone frequencies if you can as well as tweak everything over time. Remember practice makes perfect not only with your Morse code but your crafting as well! I hope you enjoyed this tutorial and look forward into possibly bumping into you on the radio some day.
THANKS!
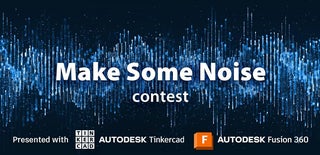
Participated in the
Make Some Noise Contest