Introduction: Quilted Aluminum Backsplash
So I bought a ‘82 Winnebago. It came with this ugly wallpaper and wood paneling. I’m going to attempt to live in this beast full time starting January 2018. Here’s one project of which I am most proud.
After doing some research for lightweight backsplash ideas I came across quilted stainless steel and I thought it looked retro yet modern. Then I discovered it would cost me $120 to do the tiny RV kitchen.
Here’s how I get the same effect from aluminum flashing.
After doing some research for lightweight backsplash ideas I came across quilted stainless steel and I thought it looked retro yet modern. Then I discovered it would cost me $120 to do the tiny RV kitchen.
Here’s how I get the same effect from aluminum flashing.
Step 1: Tools & Materials
Here’s a list of the things you’ll need:
Carpenter Square
Tape measure
Tin Snips
A LARGE and long level (being used as a stencil not to level)
Screen Repair Tool (MUST be metal)
Hacksaw if you decide to use J threshold trim for a finished edge. Optional.
Materials:
Aluminum Flashing (not galvanized) - it comes in a 20” x 10’ roll on amazon for cheapest price.
Contact Cement (and brush or roller to apply it)
Aluminum J threshold (comes in 10ft at major hardware stores in the flooring department) - this is for a finished-edge look for the pieces not going behind other trim work. Optional.
Carpenter Square
Tape measure
Tin Snips
A LARGE and long level (being used as a stencil not to level)
Screen Repair Tool (MUST be metal)
Hacksaw if you decide to use J threshold trim for a finished edge. Optional.
Materials:
Aluminum Flashing (not galvanized) - it comes in a 20” x 10’ roll on amazon for cheapest price.
Contact Cement (and brush or roller to apply it)
Aluminum J threshold (comes in 10ft at major hardware stores in the flooring department) - this is for a finished-edge look for the pieces not going behind other trim work. Optional.
Step 2: Cut to Fit
Unroll the flashing and cut the pieces to size. Be sure to notch out for windows and outlets as necessary. I decided to do each wall as a separate piece after handling the material; it’s flimsy.
Next: Dry fit each piece. The next step is tedious so you best not waste time on a piece that’s not going to fit.
Optional Trim: While I was dry fitting each piece, I cut and glued the J trim in place using the contact cement ( followed directions). The screws were there only to hold the trim in place as the glue dried.
Next: Dry fit each piece. The next step is tedious so you best not waste time on a piece that’s not going to fit.
Optional Trim: While I was dry fitting each piece, I cut and glued the J trim in place using the contact cement ( followed directions). The screws were there only to hold the trim in place as the glue dried.
Step 3: One Direction (Not a Fan)
So to get the etched lines perfectly square and also rotated use a carpenter square on the bottom edge of the aluminum. The hypotenuse of the tool is at 45 degrees. Lay your long level on that edge and try to line up the top the level to one of the corners of the aluminum.
Once the level is in place put pressure on it to keep it still as you roll the screen repair tool down one side. Put a moderate amount of pressure, but don’t make it a workout. You will notice two sides of the screen roller. I used the double edge (or concave) roller. I feel it gave me more control on the runs.
Once you rolled your first line, move the level over and use the first line as a guide for the second and roll your next line. DO NOT slide the level across the face of the sheet. You will scratch the surface and not be happy. Lift up the level and replace it in the next position.
Continue these steps until you have the entire sheet lined out in the same direction.
Once the level is in place put pressure on it to keep it still as you roll the screen repair tool down one side. Put a moderate amount of pressure, but don’t make it a workout. You will notice two sides of the screen roller. I used the double edge (or concave) roller. I feel it gave me more control on the runs.
Once you rolled your first line, move the level over and use the first line as a guide for the second and roll your next line. DO NOT slide the level across the face of the sheet. You will scratch the surface and not be happy. Lift up the level and replace it in the next position.
Continue these steps until you have the entire sheet lined out in the same direction.
Step 4: Opposing Direction
Now it’s time to make squares. Flip your carpenter square over and line up your level in the opposite direction of the lines you previously rolled. Try to position the level so that your next lines make a complete square at the top or bottom of each piece, whichever you prefer. I chose the bottom because I’m 6’8” and I can’t see the top edge under the cabinets. This will make a more professionally finished look.
Keep it rolling just like you did in the previous step.
Keep it rolling just like you did in the previous step.
Step 5: Stick It!
You’re ready to install.
I followed the directions on the can of contact cement and painted both the wall and the backside of the flashing. Waited 5 minutes for both to get tacky and pressed it on. Use a towel instead of your fingers when pressing on the aluminum. The fingerprints are everywhere.
I followed the directions on the can of contact cement and painted both the wall and the backside of the flashing. Waited 5 minutes for both to get tacky and pressed it on. Use a towel instead of your fingers when pressing on the aluminum. The fingerprints are everywhere.
Step 6: Competed Look and Optional Trim
I’m very happy with the results. I spent $32.76 (I already had the contact cement).
Take a look at the J trim. The metal would have just ended at the end of the counter. The J trim slides right over the edge of the flashing hiding the ugly cut I made. It was super easy and took no time at all.
Take a look at the J trim. The metal would have just ended at the end of the counter. The J trim slides right over the edge of the flashing hiding the ugly cut I made. It was super easy and took no time at all.
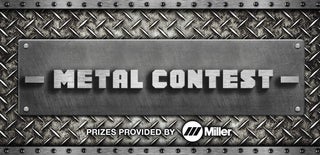
Runner Up in the
Metal Contest 2017
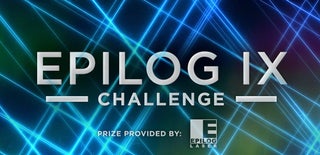
Participated in the
Epilog Challenge 9