Introduction: Portable Radiation Detector
This is a tutorial to design, construct, and test your own portable Silicon photo-diode Radiation Detector suitable for the 5keV-10MeV detection range to accurately quantify low energy gamma-rays coming from radioactive sources!
Pay attention if you don't want to become a radio-active zombie: it is not safe to be around sources of high-radiation, and this device should NOT be used as a reliable way of detecting potentially harmful radiation.
Let's start with a little background science on the detector before we go onto it's construction. Above is a wonderful video from Veritasium explaining what radiation is and where it comes from.
Step 1: First, Lots of Physics
(Figure legend: Ionizing radiation forms electron-hole pairs in the intrinsic region resulting in a charge pulse.)
Spark chambers, Geiger's, and Photo-multiplier tube detectors... all these types of detectors are either cumbersome, expensive or use high-voltages to operate. There are a few maker-friendly Geiger tube types, such as https://www.sparkfun.com/products/retired/11345 & https://www.adafruit.com/product /483. Other methods for detecting radiation are solid-state detectors (e.g Germanium detectors). However, these are expensive to produce and require specialized equipment (think liquid nitrogen cooling!). On the contrary, solid-state detectors are very cost effective. They are widely used and play an essential role in high-energy particle physics, medical physics, and astrophysics.
Here, we build a portable solid-state radiation detector capable of accurately quantifying and detecting low energy gamma-rays coming from radioactive sources. The device consists of an array of reverse biased large surface-area silicon PiN diodes, which output to a charge pre-amplifier, a differentiator amplifier, a discriminator, and a comparator. The output of all successive stages is converted to digital signals for analysis. We'll start by describing the principles of silicon particle detectors, PiN diodes, reverse biasing and other associated parameters. We'll then explain the different investigations that were conducted, and the choices made. In the end, we'll introduce the final prototype and the testing.
SolidState Detectors:
In many radiation detection applications, the use of a solid detection medium is of significant advantage (alternatively called semiconductor diode detectors or solid-state detectors). Silicon diodes are the detectors of choice for a large number of applications, especially when heavy charged particles are involved. If the measurement of energy is not required, the excellent timing characteristics of silicon diode detectors permit an accurate counting and tracking of charged particles.
For the measurement of high-energy electrons or gamma-rays, detector dimensions can be kept much smaller than alternatives. The use of semiconductor materials as radiation detectors also results in a larger number of carriers for a given incident radiation event, and therefore a lower statistical limit on energy resolution than is possible with other detector types. Consequently, the best energy resolution achievable today is realized through the use of such detectors.
The fundamental information carriers are electron-hole pairs created along the path taken by the charged particle through the detector (see figure above). By collecting these electron-hole pairs, measured as charges at the electrodes of the sensor, the detection signal is formed, and it proceeds to amplification and discrimination stages. Additional desirable features of solid-state detectors are a compact size, relatively fast timing characteristics, and an effective thickness (*). As with any detector, there are drawbacks, including the limitation to small sizes and relatively possibility of these devices to undergo performance degradation from radiation-induced damage.
(*: Thin sensors minimize multiple scatterings, whereas thicker sensors generate more charges when a particle traverses the substrate.)
P−i−N diodes:
Each type of radiation detector produces a characteristic output after interaction with radiation. Interactions of particles with matter are distinguished by three effects:
- the photo-electric effect
- Compton scattering
- Pair-production.
The basic principle of a planar silicon detector is the usage of a PN junction in which particles interact via these three phenomena. The simplest planar silicon sensor consists of a P doped substrate and an N-implant at one side. Electron-hole pairs are created along a particle trajectory. In the area of the PN junction, there is a region free of charge carriers, called the depletion zone. The electron-hole pairs created in this region are separated by a surrounding electrical field. Therefore, the charge carriers can be measured at either the N or P -side of the silicon material. By applying a reverse-bias voltage to the PN junction diode, the depleted zone grows and can cover the complete sensor substrate. You can read more about this here: Pin Junction Wikipedia Article .
A PiN diode has an intrinsic i region, between the P and N junctions, flooded with charge carriers from the P and N-regions. This wide intrinsic region also means the diode has a low capacitance when reverse biased. In a PiN diode, the depletion region exists almost completely within the intrinsic region. This depletion region is much larger than with a regular PN diode. This increases the volume where electron-hole pairs can be generated by an incident photon. If an electric field is applied to the semiconductor material, both the electrons and holes undergo a migration. The PiN diode is reverse biased so that the entire i-layer is depleted of free carriers. This reverse bias creates an electric field across the i-layer so that the electrons are swept to the P-layer and the holes, to the N-layer (*4).
The flow of carriers in response to a pulse of radiation constitutes the measured current pulse. To maximize this current, the i-region must be as large as possible. The properties of the junction are such that it conducts very little current when biased in the reverse direction. The P-side of the junction becomes negative with respect to the N-side, and the natural potential difference from one side of the junction to the other is enhanced. Under these circumstances, it is the minority carriers which are attracted across the junction and, because their concentration is relatively low, the reverse current across the diode is quite small. When a reverse bias is applied to the junction, virtually all the applied voltage appears across the depletion region, because its resistivity is much higher than that of the normal N or P-type material. Indeed, the reverse bias accentuates the potential difference across the junction. The thickness of the depletion region is also increased, extending the volume over which radiation-produced charge carriers are collected. Once the electric field is sufficiently high, the charge collection becomes complete, and the pulse height no longer changes with further increases in the detector bias voltage.
(*1: Electrons in the bound state of an atom are knocked out by photons when the energy of the incident particles is higher than the binding energy. ; *2: Interaction involving the scattering of a particle off a free or loosely bound electron, and the transfer of some of the energy to the electron. ; *3: Production of an elementary particle and its anti-particle. ; *4: Electrons are drawn in the opposite direction to the electric field vector, whereas holes move in the same direction as the electric field.)
Step 2: Exploration
This is the prototype version of the "detector" that we constructed, debugged and tested. It's a matrix consisting of multiple sensors to have a "CCD" style radiation sensor. As mentioned prior, all silicon semi-conductors are sensitive to radiation. Depending on how precise it is, and the sensors used one can also get a rough idea of the energy level of the particle that caused a hit.
We've used unshielded diodes already intended for sensing, which when reverse biased (and shielded it from visible light), can register hits from Beta and Gamma radiation by amplifying the tiny signals and reading the output data with a microcontroller. Alpha radiation, however, can rarely be detected because it cannot penetrate even thin fabric or polymer shielding. Attached is a wonderful video from Veritasium, which explains the different types of radiation (Alpha, Beta & Gamma).
The initial design iterations used a different sensor (a BPW-34 photodiode; a famous sensor if you google around). There are even a few related Instructables that use it for the very purpose of detecting radiation such as this excellent one: https://www.instructables.com/id/Pocket-Photodiode-Geiger-Counter/. However, because it had some bugs and was not functioning optimally, we decided to omit the details of this prototype from this Instructables to avoid Makers building a detector full of flaws. We did, however, attach the design files and schematic in case someone is interested.
Attachments
Step 3: The Design
(Image legends: (1) Block diagram of detector: from signal creation to data acquisition., (2) Specifications of the X100-7 photodiode: 100mm^2 active area, 0.9mm depleted zone, light blocking coating, low dark current... As shown in the absorption probability plot, PiN diodes readily absorb gamma-ray energy, (3) Application note of manufacturer which confirmed the design concept and helped to choose initial component values.
We settled for a larger area sensor, namely, the X100−7 from First Sensor. For testing purposes and modularity, we designed three different portions, stacked upon each other: Sensors and amplification (low noise charge amplifier + pulse shaping amplifier), Discriminators & comparator, DC/DC regulation, and the DAQ (Arduino for data acquisition). Each stage was assembled, validated, and tested separately as you will see in the next step.
A main advantage of semiconductor detectors is the small ionization energy (E), independent of both the energy and type of incident radiation. This simplification allows to account for a number of electron-hole pairs in terms of the incident radiation energy, provided the particle is fully stopped within the active volume of the detector. For silicon at 23C (*) we have E~3.6eV. Assuming that all energy is deposited and using the ionization energy we can calculate the number of electrons produced by a given source. For example, a 60keVgamma-ray from an Americium−241 source would result in a deposited charge of 0.045 fC/keV. As shown in the specifications of the diode specs, above a biasing voltage of approximately ~15V the depletion region can be approximated as constant. This sets the target range for our biasing voltage to 12−15V. (*: E increases with decreasing temperature.)
The functionality of the different modules of the detector, their constituents, and associated calculations. When evaluating the detector, the sensitivity (*1) was crucial. An extremely sensitive charge pre-amplifier is required because an incident gamma-ray may only generate a few thousand electrons in the semiconductor depletion region. Because we amplify a tiny current pulse, particular attention must be given to component selection, careful shielding and circuit board layout.
(*1: Minimum energy to be deposited in the detector to produce a distinct signal, and the signal-to-noise ratio.)
To properly chose component values, I first summarize the requirements, the desired specifications, and the constraints:
Sensors:
- Large possible detection range, 1keV-1MeV
- Low capacitance to minimize noise, 20pF-50pF
- Negligible leakage current under reverse bias.
Amplification and Discrimination:
- Charge sensitive pre-amplifiers
- Differentiator for pulse shaping
- Comparator for signal pulse when above the set threshold
- Comparator for noise output when within threshold interval
- Comparator for channel coincidences
- General threshold for event filtering.
Digital and micro-controller:
- Fast analog-to-digital converters
- Output data for processing and user interface.
Power and filtering:
- Voltage regulators for all stages
- High-Voltage supply to generate the bias power
- Proper filtering of all power distribution.
I chose the following components:
- DC Boost Converter: LM 2733
- Charge Amplifiers: AD743
- Other Op-Amps: LM393 & LM741
- DAQ/Readout: Arduino Nano.
Additional imposed specifications include:
- Operating rate: > 250 kHz (84 channels), 50 kHz (coincidence)
- Resolution: 10bit ADC
- Sample rate: 5kHz (8 channels)
- Voltages: 5V Arduino, 9V op-amps, ~12V Biasing.
The overall arrangement and order of the above components are represented in the block diagram figure. We made the calculations with component values used during the testing phase (see the third image). (*: Some component values are not the same as initially planned nor the same as those currently in place; nonetheless these calculations provide a guidance frame.)
Step 4: The Circuits
(Figure legends: (1) Overall schematic of stages 1-3 of a single channel, including diode basing and voltage dividers that provide references to each stage, Circuit sub-sections.)
Let's now explain the "flow" of the detection signal of one of the four channels from its creation to digital acquisition.
Stage 1
The only signal of interest originates from the photodiodes. These sensors are reverse biased. The biasing supply is a stable 12V which is run through a low pass filter to eliminate any unwanted noise larger than 1Hz. Upon ionization of the depletion region, a charge pulse is created at the pins of the diode. This signal is picked-up by our first amplification stage: the charge amplifier. A charge amplifier can be made with any operational amplifier, but low noise specification is very important.
Stage 2
The objective of this stage is to convert the charge pulse detected at the inverting input, into a DC voltage at the op-amp’s output. The non-inverting input is filtered and set to a voltage divider at a known and chosen level. This first stage is difficult to tune, but after numerous tests we settled for a feedback capacitor of 2[pF], and a feed- back resistor of 44[MOhm], resulting in a pulse of 2[pF] × 44[MOhm] = 88[μs]. An inverting active bandpass filter amplifier, which acts like a differentiator, follows the charge amplifier. This stage filters and converts the converts DC level, emanating from previous stage into a pulse with a gain of 100. The raw detector signal is probed at the output of this stage.
Stage 3
Next in line are the signal and noise channels. These two outputs go directly to the DAQ as well as to the second analog PCB. Both function as op-amps comparators. The only difference between the two is that the noise channel has a lower voltage at it’s non-inverting input than the signal channel, and the signal channel is also filtered to remove frequencies above the expected output pulse from the second amplifying stage. An LM741 op-amp acts as a comparator against a variable threshold to discriminate the signal channel, enabling the detector to only send select events to the ADC/MCU. A variable resistor on the non-inverting input sets the trigger level. In this stage (coincidence counter), signals from each channel are fed to an op-amp acting as a summing circuit. A fixed threshold is set coinciding with two active channels. The op-amp outputs high if two, or more, photodiodes register a hit simultaneously.
Note: We made a crucial mistake by putting the DC/DC step-up converter of the biasing power near the charge sensitive op-amps on the amplification PCB. Perhaps we'll fix this in a later version.
Attachments
Step 5: The Assembly
Soldering, lots of soldering... Because the sensor selected for the final detector only exists as an SMT footprint component we had to design PCBs (2 layers). Therefore, all associated circuitry was also migrated onto PCB boards rather than the breadboard. All analog components were placed on two separate PCBs, and the digital components on another to avoid noise interferences. These were the first PCBs we ever made so we had to get some help for the layout in Eagle. The most important PCB is that of the sensors and amplification. With an oscilloscope monitoring the outputs at test-points the detector can operate solely with this board (DAQ bypass). I found and fixed my errors; these included wrong component footprints, which resulted in our low noise op-amps to be wire-tapped, and end-of-life components that were swapped with alternatives. Additionally, two filters were added to the design to suppress ringing oscillations.
Step 6: The Enclosure
The goal of the 3D printed casing, the lead sheet and foam is for: mounting purposes, thermal isolation, providing a noise shield, and to block ambient light, and evidently to protect the electronics. 3D printing STL files are attached.
Step 7: Arduino Read-out
The read-out (ADC/DAQ) part of the detector consists of an Arduino Mini (code attached). This microcontroller monitors the outputs of the four detectors and the supply power to the later (track power quality), then outputs all the data on the serial output (USB) for further analysis or recording.
A Processing desktop application was developed (attached) to plot all incoming data.
Step 8: Testing
(Figure legends: (1) Resulting pulse of a 60Co source (t ~ 760ms) signal-to-noise ratio ~3:1., (2) Injection equivalent to the charge deposited by a source of energy ~2 MeV., (3) Injection equivalent to the charge deposited by a 60Co source (~ 1.2 MeV ) ).
Charge injection was done with a pulse generator coupled to a capacitor (1pF) at the sensor pad and terminated to ground via a 50Ohm resistor. These procedures enabled me to test my circuits, fine-tune the component values and simulate the responses of the photodiodes when exposed to an active source. We set both an Americium−241 (60 KeV) and an Iron−55 (5.9 KeV) source in front of the two active photo-diodes, and neither channels saw a distinctive signal. We verified via pulse injections, and concluded that the pulses from these sources were below the observable threshold due to noise levels. However, We were still able to see hits from a 60Co (1.33 MeV) source. The major limiting factor during the tests was the significant noise. There were many sources of noise and few explanations as to what was generating these. We found that one of the most significant and detrimental source was the presence of noise prior to the first amplification stage. Due to the huge gain this noise was amplified almost a hundred-fold! Maybe improper power filtering and Johnson noise re-injected into the feedback loops of the amplifier stages also contributed (this would explain the low signal to noise ratio). We didn't investigate the dependence of noise with biasing, but we might look into that further in the future.
Step 9: The Bigger Picture
Watch the video from Veritasium about the most radioactive places on earth!
If you made it this far and followed the steps, then congratulations! You've built an apparatus for real-world applications like the LHC! Perhaps you should consider a career change and go into the field of nuclear physics :) In more technical terms, you've built a solid-state radiation detector consisting of a matrix of photo-diodes and associated circuitry to localize and discriminate events. The detector consists of multiple amplification stages that convert small charge pulses into observable voltages then discriminate and compares them. A comparator, between channels, also provides information regarding the spatial distribution of detected events. You also incorporated the use of an Arduino micro-controller and essential software for data collection and analysis.
Step 10: References
In addition to the wonderful PDFs attached, here are some related informative resources:
- F. A. Smith, A Primer in Applied Radiation Physics, World Scientific, River Edge, NJ, 2000.
- First Sensor, First Sensor PIN PD Data Sheet Part Description X100-7 SMD, Web. mouser.com/catalog/specsheets/x100-7-smd-501401-prelim.pdf
- Horowitz, Paul and Hill, Winfield, The Art of Electronics. Cambridge University Press, 1989.
- C. Thiel, An Introduction to Semiconductor Radiation Detectors, Web. physics.montana.edu/students/thiel/docs/detector.pdf
- Lyndon Evans, The Large Hadron Collider: a Marvel of Technology, Ed. EPFL Press, 2009.
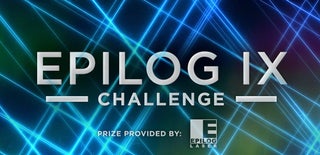
Participated in the
Epilog Challenge 9
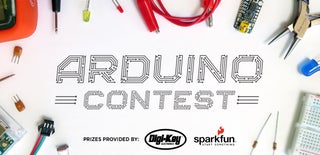
Participated in the
Arduino Contest 2017