Introduction: Recycled Wooden & Metal Scrap Lamp
This lamp was born out of a few other projects.
You know how you end up with scrap material every time you finish something? I had left over veneer from a bent-plywood table, dark walnut from a wooden bench, and a lamp without a shade. After checking out the metal scraps from our community workshop space, I found two nearly identical metal pieces that had been abandoned long before (you can still see where someone else wrote 'film' on the inside of the metal in one of the process photos) and decided these would be the guiding structures of the lamp.
I really wanted to show off the veneer, both lit from the room and from behind.
I expect no two scrap lamps will look the same, which is part of the charm. For the land of Instructables, however, I'll walk through my process creating this lamp in case it sparks some new ideas for you.
Step 1: Find Your Limiting Component
These metal pieces were the last piece I found but their dimensions directed the rest of the lamp. I ended up not doing anything to alter these pieces, though you might find you want to adapt found objects or scraps as you create.
Step 2: Finishing the Exterior Frame
Here you see the front and back of the wooden end pieces.
For these pieces, I cut my scrap walnut to two identical rectangles and on the long edges, adjusted the table saw to cut at a slight angle.
Then, knowing I wanted the metal pieces to insert with a friction fit into the wood, I decided the best way to cut the notches was by using a table saw. Below are the main steps:
1) Measure the distance from the top and bottom of the piece to where you'd like the notch
2) Mark on the top side of the wood the outer edges where the notch should end
I adjusted the kerf of the table saw blade to match the thickness of the metal piece. The rounded edges of the metal piece lend themselves well to the rounded top of the table saw blade, so I used a different technique on the table saw. Carefully:
3) Place the table saw fence at the appropriate distance for the top and bottom notches
4) Turn on the saw with the blade below the table with the wooden piece held firmly against the table
5) Raise the blade to cut into the walnut, slowly, watching it break through the top of the wood until it reaches your pencil marks for the outer edges
6) Repeat this for the other wooden piece before adjusting the fence
7) Move the fence if the distance for the bottom is different than the top. In my case, the distance was the same so I just flipped the wooden pieces and repeated steps 3-6
At this point, I then cut the center slot for the wooden support (next step) using the table saw more traditionally, creating a channel that cut directly through the wood at roughly half the depth. I then glued a small strip of walnut to the angled edge. These small strips have grain perpendicular to that of the larger piece, but the angle also follows the slight angle of the metal piece, which will ultimately guide the veneer. These outer pieces will also cover the necessary table saw marks from the center cut.
The last step for the wooden pieces is cutting a thin channel on the sides. I did this by holding the pieces against a guard and pressing the pieces up against a band saw. Careful, of course, as you'll need to expose a large amount of saw blade to cut the entire length of this piece, but the cut is fairly shallow - it's just a guide groove for the veneer.
Step 3: Cutting the Wooden Support
This piece provides the shape for the gentle contour the veneer will follow and adds another point of stability along the walnut.
This was another piece of thin plywood left over from my table project. I traced the outline of the metal part onto the wood and cut it out with a bandsaw, then used a drill press to create an opening in the inside and a scroll saw to carve out the middle section. This part is not visible apart from the thin silhouette, so use your own judgement on how perfect this needs to be.
Step 4: Cut the Veneer
This part was an easy cut.
Mark out your dimensions with light pencil marks.
A cork-backed ruler and an Olfa knife will do the trick for the thickness of veneer in this project. Just remember to cut your piece long enough to fit into the slots of the walnut.
Step 5: Small Wooden Filler
This piece is necessary for connecting the metal part to the lamp.
Cut the filler piece to fit inside the metal. In the middle of this piece, drill a hole using a drill press to the minimum size that will fit over the top of the socket, preferably resting on the lip. Once you've finished, epoxy the wooden part onto the bottom metal part but not to the socket itself.
Step 6: Gather All Parts
Again, yours might be a different form, but if you're following along you should have:
- Two rectangles of veneer
- Two scrap pieces of metal
- Two wooden walnut end pieces
- One midpoint wooden support
- One small wooden filler
- One lamp, sans shade, with a lightbulb (low wattage, small bulb)
Step 7: Start Assembly!
Begin the assembly with the bottom metal part in place and add one of the walnut end pieces. It should be a comfortable friction fit and stay in on its own, unsupported, if it's cut correctly.
Step 8: Add the Wooden Support and Top Metal Piece
These parts should fit into the slots you've made for them and again, can lightly support themselves as long as you don't put pressure on them.
Step 9: Add the Second Walnut End Piece
Carefully fit in the three horizontal parts to the appropriate notches.
Step 10: Insert the Veneer
If you've made the slots correctly, the veneer should slide gently down the side channels.
Step 11: Slide in the Second Piece of Veneer
At this point, the lamp will be fairly rigid so you might have to wriggle the second piece of veneer into place.
You'll notice that there's a small crack in the veneer here. It's fine if that happens. They're not structural and the cracks will add character to the way the light shines through.
Step 12: Finished Lamp!
The lamp is a lovely piece and takes on very different characteristics in the daytime and when it's internally lit.
This whole project only took an evening to do, from scavenging and coming up with the concept all the way to switching on the bulb. Sometimes constraints really stump us and other times they guide the making process along like it's running on rails. Also, since this was made of scraps I already had everything on hand and couldn't over think my options - I've had more projects stall because of decision fatigue than anything, so this was a great exercise for me.
Thanks for taking the time to look at my recycled wooden and metal scrap lamp! Look around and see what parts you have from other projects and see if you have the makings of a new project already started.
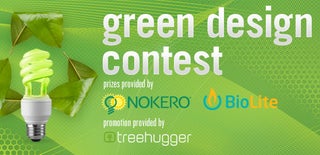
Participated in the
Green Design Contest
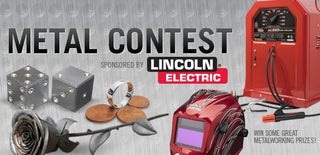
Participated in the
Metal Contest
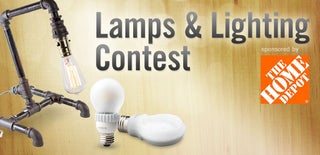
Participated in the
Lamps and Lighting