Introduction: Recycled Kiridashi
From scraps left-over in shop class, to a classy little tool that originated in Japan.
Please wear eye protection when working with metal or high-speed tools.
Metal shaving can be very small, but they can do a lot of damage if they get in your eye or lungs.
Although power tools (band-saw, angle grinder, disc sander, and rotary tool) were used, they are by no means required to do what I do. They simply speed up the process. A hacksaw, coping saw, and files are all you really need, if you are on a budget. I suggest trying out different tools and designs, to feel what you like and dislike.
Step 1: Supply and Design
After cleaning up in shop class, I happened upon a small bar of low-carbon steel and a scrap of ripped board. I advocate recycling, so this was a perfect chance to follow-through. Since the metal was very small and low-carbon (1020), a kiridashi was perfect. Above is preliminary design and rough cuts with scroll saw and angle grinder.
If you are wondering what a kiridashi is, or what it's used for, look no further.
"Art is not about making the same thing over and over, but making what you feel over and over."
Step 2: Parts, Assemble!
The stock piece (metal) was almost as thick as the wood, so I taped the area and traced out my design beforehand so I wouldn't stray when using tools. I used an angle grinder and bench vise to cut and roughly shape the metal. You can use a wheel grinder to "fine-tune" the metal like I did.
Since it's a pretty small friction folder, I didn't pin it, I just glued and clamped it together. A small bar was used to align everything together, so it would rotate freely. remember to sand the parts you want to glue, so that it has good hold.
Step 3: Small Steps
This type of inlay was simply 'wood on wood'. It's perfect for beginners, since you just glue in the wood, and sand off where the edges don't meet. That being said, It's also of the most difficult types to master. However, if you have access to a CNC router, you can make splendid designs all in CAD.
Step 4: Designing and Refining the Prototype
A disc sander was used to roughly sand down sand down the wood and shape it. The final shaping was done with a fine grit sandpaper sheet and some metal files. (I really do not care to use rasps, most of the work I do is entirely delicate)
Please take a moment to compare the original design vs the almost finished product. They are similar and different in varying ways.
You'll find out that what you plan is not always what feels right when you are making it.
Step 5: A Little Something Extra
No project would be complete without adding a little aesthetic!
A rock and gem shop near my town landed me a slab of impure turquoise for a buck! I used a rotary tool with a disc bit to cut out a parallelogram-shaped piece. Next, again using the rotary tool, but with a cutting bit, to bore out a hole for my gem. My hands were in no way steady at all, but that's not an issue.
I mixed 5 minute epoxy and wood shavings (dust, really) and scraped that into the hole. Next, the gem was pushed in left to set for 4 hours (I know, I know, 5 min epoxy set in 4 hours!?! I wanted it to be like rock before I began sanding). A sanding barrel bit for the rotary tool wore down the glue and gem flush with the wood. The gem was then buffed and polished with the rotary tool.
I'm a huge fan of pyrography, even if I don't do it much. The simple leaf design was done with a $15 soldering iron in about a minute. Sure, you can buy an expensive kit with all kinds of tips, but a simple pointed soldering tip can yield you all kinds of designs.
Thank you so much for reading this through! If you liked it, or you know someone who might like it, please favorite and share!
I stumble through life by trial and error, for it has never lead me astray.
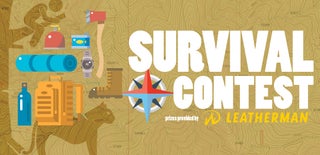
Participated in the
Survival Contest
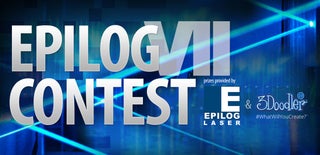
Participated in the
Epilog Contest VII