Introduction: Repairing a Fiberglass Canoe
At the end of May last year I was online looking for jobs and wondering what I was going to do with my summer. Just before preparing to head to bed I decided to log into Facebook. Here in our little city we have a Buy and Sell Facebook page for folks in the area wishing to hawk their wares. While scrolling through the list of items for sale I came across a lady looking to sell an old, battered, blue canoe for $20.
It was dark when we arrived at her house and we were only able to locate the canoe on the property by the porch light from the front of the house. As we attempted to load the canoe onto the van it was difficult to see the true condition of the boat.
Step 1: Inspect the Craft for Damage
The next day a proper inspection proved that this $20 canoe was worth the money paid. Large cracks, holes, and a completely broken thwart and yoke were tokens of the work I had ahead of me.
This project felt very overwhelming at first. I wasn't familiar with fibreglass repairs or what I would need to accomplish such a heavy task. See a more detailed read of how I self taught myself here http://fivebravesouls.com/2015/09/29/rebirth-of-a...
Step 2: Make It Worse, Before It Can Get Better
After 3 hours of sanding I had gone through 3-1/3 sheets of sandpaper, and killed my orbital sander. The canoe was still very, very blue. A little discouraged I put a call out for a sander and in no time had a replacement loaner, THANK YOU! Long story short, I stopped counting sanding hours after 24, the canoe was significantly yellower, and the holes significantly bigger.
It's a good idea to remove any plates or hardware before you begin sanding. The ID plate was riveted on. The fastest way to remove these is to simply drill into the rivet centre. The trick here is to not use a drill bit much larger than the rivet centre itself. The goal isn't to drill a new hole, just separate the rivet from the canoe.
Good preparation is important. The yellow colour was the colour of the original gel coat, so with a complete restoration like this it is important to get right down to that original colour. Also, much of the research I did in this repair stated that it is best to get rid of as much of the damaged fibreglass as well. You don't want old problems to become big headaches down the road. I sanded with a small, orbital hand sander which I've been told is a bit of a "no-no" with large projects like this. This is possibly the reason for the wave in the hull that is quite noticeable (though other damage could have resulted in this as well). This can be avoided by using a longboard sander, much like what is used in automotive restoration. Supposedly these are easily found at any automotive store. I was told about this after I was pretty much done with sanding...so next time I'll look into this.
The gel coat on this boat was spider cracking all over the place as well. The advice I saw stated to sand those out the best you can. This was difficult and I was afraid of sanding more holes in the hull than I wanted to fix. The reason you want to get rid of these is so that they don't show up when you put on the fresh paint (which they do), but I was willing to let it go for the amount of sanding I had done already.
Step 3: Patchy Patchy
Before I got started on the more concerning holes in the hull and wanted to attempt repairing the thwart, yoke and deck. I went this route first so that I could make decisions about whether I needed to build or purchase a new thwart and yoke, as well as completely redesigning the deck.
Chunks of foam were missing from the thwart that made it difficult to connect, and then reinforce with fibreglass. I used a spray insulation foam, typically used to seal cracks around window and door framing, as a filler. I than wrapped the thwart with painters tape to maintain the shape and reduce the amount of foam I would need to shape afterwards. I used a strap wrapped around the hull to secure the thwart while the foam set, this strap remained in place until after fibreglass reinforcement was applied to the area.
The yoke was trickier to align properly to reinforce with fibreglass since it is hollow. Seeing as the foam spray worked with the thwart I decided to empty a can into the yoke (wrapped in painters tape) to force it to stay aligned properly. This worked well. Removing the foam afterwards however, was not an option.
The deck had been torn apart from the previous painter and had to be built up again. I did this by filling the gap with foam spray. Once it had dried I drilled out a new hole for the painter, and carved the edges closer to the original deck. A friend built me a model to create a fibreglass tube so that I could reinforce the deck. It kind of worked as I ended up with a fibreglass tube, but pulling it off the copper rod pulled the fibreglass inside out from how I had set it on the model. Perhaps if I had let it dry there it would have slid off easier. I wasn't certain I would have been able to remove it after it dried as it stuck to the copper quite well. Perhaps a smoother, or lubricated surface would not have had such issues, and offered different assurances.
Step 4: "There's a Hole in My Bucket..."
Once the canoe was completed sanded down, and the residue washed, dusted, wiped, dried off I moved the canoe indoors to avoid bugs and pollen get stuck to the sticky stuff. You also want to be sure your project won't be rained on or get too hot. A well ventilated area is also a must as resin has a hazardous odor.
It is important to have all the pieces you will be applying prepared before mixing the resin and hardener. Especially if you are working in warmer conditions. The resin can take anywhere from 8 minutes to 14 minutes to begin to set up and become unworkable.
Follow the directions for mixing the resin and hardener that appears on the container. It is slightly different for different products. I used a bristle brush to take the fibreglass resin up in just the tips of the brush. You apply the fibreglass resin by dabbing, not brushing, it onto the fibreglass cloth or material you are using (I used cloth). Brushing will cause the fibres to separate and you don't want that to happen.
Most of the fibreglass work on this canoe was applied to the outside. It doesn't really matter which side you're going to build up, but that first layer is important in supporting all the rest. You want to make sure that the first layer is at least 1"-2" wider than the hole being repaired. Obviously, we don't want the other material falling through the hole. I've seen some folks use painters tape, or packing tape to cover the hole on one side while filling in the fibreglass from the other. The premise is the same. You want to have a "net" to prevent the repair from going right through the hole.
I made a mistake and attempted to apply my fibreglass "net" while the canoe sat on the sawhorses with the hull facing the ceiling. I ended pushing it too far through the hole and when I went to sand between layers I created a hole in my "net". This occurred largely because I had not saturated my fibreglass before applying it and as I was attempting to do this while it was on the canoe I stretched out the fibreglass that straddled the hole, pushing it through.
You want build up the fibreglass patches by adding layers of fibreglass cloth that gradually get smaller and smaller in an attempt to create a level surface. Small holes of 1-2" may only require 5-7 layers, where larger holes can require twice that. You can apply multiple layers at a time. Sand once it is cured and reassess to see if you need to apply more layers in lower areas.
Step 5: Make It Perty
Gel coat is of course the best option for a finish. Gel coat is what is applied when the canoe is first moulded. Applying it after the fact as a repair is a more difficult and delicate process that requires expertise and a lot of elbow grease to prevent an "orange peel" effect. I didn't have the patience for that so opted for the Roll and Tip technique used with applying paint.
Marine enamel is the ideal choice. I had a difficult time tracking some down in the color I wanted. White, black and Red seem to be the more popular choices at almost $50/pint. Cloverdale paints however were my heroes and graciously made me a custom color to make my dreams come true. The issue I faced with wanting to paint it yellow was that they had to tint a transparent enamel which takes many more coats to cover. I managed to get 4 coats out of one pint on my 17' canoe. Maybe I could have squeezed another coat out if I had been more calculating about what I poured into my paint tray.
Roll and Tip technique is actually not as difficult as it sounds. You roll the paint on with a foam roller over small sections, then quickly and very lightly go over that area with a brush just using the tip so as to smooth out the bubbles left from the foam roller. There are some excellent youtube videos where you can watch a demonstration over and over...like I did. Remember to lightly sand between coats with 320 grit sandpaper.
I used the same method on the interior and gunwales, but I didn't feel the need to be as nearly as meticulous as I was on the hull.
Step 6: Finish Up With Some Bling
Once the paint has dried, it's time to put all the pieces together.
I riveted the ID plate back into place using pop rivets with some washers on the inside to prevent them pulling through the fibreglass. The Clipper stickers I was only able to purchase after showing the ID plate I had removed to a Clipper dealership. I then had to swear an oath that I wouldn't stick them on just any canoe. Finally, new painter rope in a bright blue for contrast.
Step 7: Put It in the Water
Finally, this boat was ready to hit the water.
The paint had only cured 48 hours before we slid it on the the van, and most of the paint scraped off of the gunwales. So I'll be redoing that. Still researching how to help prevent that from happening. Perhaps a longer cure time?
This boat has come a long way, but worth the effort. After the dust had settled, literally from all the sanding I did, this canoe cost me about $400. Not to bad for an old beat up Clipper.
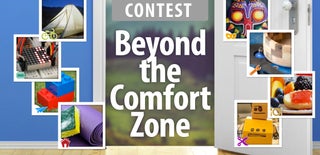
Second Prize in the
Beyond the Comfort Zone Contest
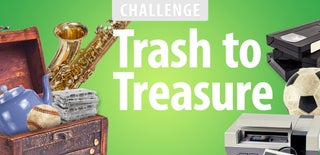
Runner Up in the
Trash to Treasure Challenge
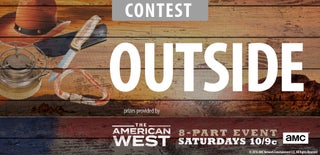
Participated in the
Outside Contest 2016