Introduction: Resistor Color Code Calculator With Arduino
HOW DOES IT WORKS?
There are 4 small stepper motors , 4 stepper motor drivers, 4 10K potentiometers and 2 Arduino UNO on a breadboard. As you turn the potentiometer, the motors rotate displaying a color and a value at the same time.
Step 1: Material List
ARDUINO UNO ON A BREADBOARD COMPONENTS LIST ( J )
At Mega 328p with arduino UNO boot loader
5v Voltage Regulator 7805-T
LED (2 red ) and (2 green)
resistor 1/4 w, 10k and 180 ohms
Radial Capacitor 10uf 50v
Ceramic Capacitor disc 22pf 50v
ceramic Capacitor disc 0.1uf 50v
Tantalum Capacitor 10uf 25v
16Mhz Crystal low-profile
Pushbutton switch, off/on
Stepper Motor with driver board (YD)
Blue LED light (YD)
Panel mount LED holder 5mm (YD)
DPDT On /OFF switch (YD)
10k small Potentiometer (YD)
10k Potentiometer chicken head Knob (SP)
9v Battery holder (Pack of two) (YD)
9v Battery (YD)
6v, AA Battery case (YD)
AA Battery (pack of 4) (YD)
40pin flat cable female ends (YD)
Breadboard jumper kit (YD)
Breadboard 16cm with power and Grd busses (YD)
Breadboard 8cm with power and Grd busses (YD)
Mini Digital Voltmeter 0-30v dc (red) (YD)
Hook-up wire, solid (black, Red & Green) (SP)
solder tube .031 Inch Dia. (SP)
Liquid Tape 4FL. OZ (HD)
Servo Mounts (SP)
Screw-Phillips head (1/2", 4-40, 10-pack) (SP)
Nut metal (4-40, 10-pack) (SP)
wood screws #6 x 3/4" pan head Phillips (HD)
11/32", 2' x 2' Plywood sheet (HD)
MINWAX wood finish stain (provincial 211) (HD)
Primer spray paint (HD)
Gold spray paint (HD)
1/8" Plexiglas 11" x 14" (HD)
Compressed wood (HD)
Narrow utility hinges 1" (HD)
1/2" x 2' PVC pipe (HD)
1/2" PVC 90* elbow (HD)
1/2" PVC coupling (HD)
2" PVC pipe Blocker (HD)
2" x 2' PVC pipe (HD)
3" PVC pipe Blocker (HD)
3" x 2' PVC pipe (HD)
Nailed metal bridging (HD)
4" (10cm) Cable Ties (HD)
Step 2: Building the Enclosure
Start by cutting the six pieces that make the enclosure, the first piece would be the base (bottom piece).
1) Grab the 11/32", 2' x 2' Plywood sheet and cut a 14" x 11" piece.
2) Cut the side pieces, (see 2nd picture) for measurements.
3) Cut a 13 1/8" x 2" piece, this is the back part of the enclosure. (See 4th picture)
4) Cut a 13 1/8 x 2 1/2 piece, and drill two 1" hole on each side. This is the top piece of the enclosure.
(see 5th picture) for measurements.
5) Put the enclosure together, use the #6 x 3/4" wood screws.
6) After the enclosure is been assembled, is time to sand and stain the enclosure. (pix 6)
Step 3: Front Panel
Cut a 14" x 2 1/2 " piece of the compressed wood, and drill 6 1/4" holes for the pots. You may have to check the drill bit size for the LED holder and switch. Depending of what LED holder and switch you get.
(see 2nd picture). Next paint the panel and let it dry before installing the pots, LED and switch.
(see 3rd picture) for measurements.
Next cut (16) 12" long of hook up wire, solder each wire to each potentiometer terminal, the LED and the switch. Make sure you use electrical liquid tape or shrinking tube to cover the splices. (see last pictures). Last screw the panel to the enclosure.
Step 4: Motors Support Bracket and Side Posts
Grab the nailed metal bridging bracket and put a line across on each end , right where the curved shape ends (see 1st picture). Measure 1/2" from the first line put a 2nd mark across, then make a 3rd line across 1/2". First bend the bracket 45* on the first line, then make a second 45* bend on the second line. Do it to both sides. (see picture 2,3,4,5).
Next cut the bracket in half, and place on piece on top of each other and tape them together, it should measure 9" from side to side (see picture 6,7,8,9). Last drill two holes on both ends of the bracket (see picture 10,11) and cut the rest of the end of the bracket at the 3rd line across it .
Now we are going to work on the side posts (PVC pipes)that hold the motors support bracket.
cut (2) 2 1/2" of 1/2" PVC pipe, and place the 1/2 " elbow on one side and the coupling on the other. (see picture 12,13,14) Once both pieces assembled is time to paint them. (I used automotive primer spray)
While the two posts are drying get the (2) 3" PVC pipe blocker and place them back to back together and drill a 7/8" hole in the center on both pieces at the same time, so you'll have the center holes of both blocker matching each other and will make the motor support bracket level without any more adjustments to make. Last test fit the posts make sure they fit on the enclosure and through the 3" PVC pipe blockers. Do not glue them together at this point. See pictures 15 - 22.
Step 5: Mounting and Making the Motors Base.
Now we're going to cut a 9 1/2" piece of Plexiglas this is the stepper motor base and drill (8) 3/16" holes (see picture 2,3,4) for measurements. Start by bolting the servo mounts from sparkfun to the stepper motors using the 1/2",4-40 bolts and nuts. Now place the motor on top of the Plexiglas aligning the rear motor mount with the holes previously drilled. Now mark the rest of the motor mount holes and drill them with a 3/16" bit (see picture 5,6,7,8). bolt them down and use 2 #6 flat washers on each hole of the motor mounts (see picture 9,10,11). Now place and center the Plexiglas piece on the motor bracket and drill (2) 3/16" holes through the Plexiglas onto the bracket, one on each side about 2" from each end (see picture 12,13,14,15)and bolt them together using 1/2",4-40 bolts and nuts. finally get the motor support bracket and bolt it to the 3" blocker with the 1/2", 4-40 bolts and nuts. 2 per side, as close as you can to the opening in the middle (see pictures 16,17). Now place the posts on the enclosure (see last pictures).
Step 6: Making and Mounting the Wheels (bands)
• 2" PVC Pipe
• 2" Knock out plug (4)
• 1/4" drill bit
• Label roll
• Color sharpies (black, brown, red, orange, yellow, green, blue, violet).
• A utility knife Glue stick.
Cut (4) 3/4" thick piece of 2" PVC Pipe (see picture 1,2,3). Next drill a 1/4" hole in the center of the knock out plugs. Place 2 knock out plugs together back to back and drill a 1/4" hole through both of the pieces. Make sure these holes a centered to the knock out plugs. Do the same for the other two plugs
(see picture 4,5,6). Get (4) binding post and cut 1/4" off the top (see picture 7,8), now place the knock out plug on the 2" , 3/4" thick PVC piece and the post through the knock out plug. do not glue jet, this is just to test to fit step (see picture 9,10).
Pull out 4 piece long , 8 1/2" off label roll, and draw a line across every 3/4" , you should end up with (11) 3/4" sections per piece (see picture 11,12,13). Now put a light coat of stick glue on each band ( I am going to refer to the 2", 3/4" thick PVC Pipe as bands from now on) and wrap the 8 1/4" label piece around each band, you end up over lapping the last section onto the first one see picture 14,15,16). Grab the utility knife and trim the label as close as you can to the band's outer edge (see picture 17,18).
Now time to color the bands, grab two bands, color and number them in this order:
• BLACK 0 (use a white or silver sharpie to number the black section)
• BROWN 1
• RED 2
• ORANGE 3
• YELLOW 4
• GREEN 5
• BLUE 6
• VIOLET 7
• GRAY 8
• WHITE 9
The Gray section was colored using a #2 pencil, go over the section with a very light pressure.
Color the 3rd band (The multiplier) and number them as follow:
• BLACK (Do not number this section)
• BROWN 0
• RED 00
• ORANGE 1K
• YELLOW 10K
• GREEN 100K
• BLUE 1M
• VIOLET 10M
• GOLD 0.1
• SILVER 0.01
The 4th band is the tolerance in percentage, color and number as follow:
• BROWN 1%
• RED 2%
• GREEN 0.5%
• BLUE 0.25%
• VIOLET 0.1%
• GRAY 0.05%
• GOLD 5%
• SILVER 10%
• last section do not color just write the word "plain" an number it 20% under the word plain.
See picture 19,20) and see last picture, is the chart with the color and values of each band, and I purposely taped off one section so it won't confuse you, you don't need that section. That section is for a 5-band resistor.
Step 7: Wiring the Small Stepper Motors
• BLUE (1st wire)
• PINK (2nd wire)
• YELLOW (3rd wire)
• ORANGE (4th wire)
• RED (5th wire)
now, cut off the connector of each motor at about 3 1/2" away from the connector. Take the one end of the labeled Cat5e and solder each wire to the wires on the motor to their corresponding color. Cover the splices with shrink tube or liquid electrical tape. Do the same to the rest of the stepper motors.
Once all the motor's wires had been soldered and covered, tape each motor wires together and label them motor 1, motor 2, motor 3 and motor 4. Run the other end of the wires down into the enclosure through the side post one by one. Make sure you label each bundle, 2 set of wires per side post. Now save the stepper motor connectors, you'll need them to plug them into the driver boars later. Once done with the wiring, install the band on each motor, just slide he the bands on the motor shaft.
See pictures for reference.
Step 8: Installing the Electronic Components
http://www.jameco.com/Jameco/Products/ProdDS/2151259.pdf
Remember you need to build 2 of these. Once your done, start by placing the stepper motor drivers on the top inside of the enclosure at about 2 1/4" center to center apart from each other). Screw the driver boards down one on each side opposite corners. (see picture 1,2,3) . Now place the bread board with the Arduinos on it on the lower left side of the enclosure, get the 2nd small bread and place it on the right side lower corner level with the first bread board. Peel off the backing paper exposing the adhesive on the back of the bread boards on place them down and put pressure on it for 2 minutes.
Next place the one 9v battery holder on the left side of the left bread board and place the other 9v battery holder in between both bread boards . Screw them down. And last screw down the AA battery pack on the upper right corner of the enclosure. see pictures for reference.
Step 9:
Attachments
Step 10: Arduino Sketch
#define STEPS 100
Stepper stepper1(STEPS, 9,11,10,12);
Stepper stepper2(STEPS,1,3,2,4);
int previous1 = 0;
int previous2 = 1;
void setup()
{ //How fast will we try to move the motor //If your motor stutters, its too fast so just lower the value
stepper1.setSpeed(150);
stepper2.setSpeed(150);
delay(500);
}
void loop()
{
int val1 = map(analogRead(0), 0, 1023,0,2046); //Move motor based off of last recorded position
int val2 = map(analogRead (1),0, 1023,0,2046);
stepper1.step(val1 - previous1); //Store current position
stepper2.step(val2 - previous2);
previous1 = val1;
previous2 = val2;
}
Step 11: Wiring
we are going to start by wiring the connectors back to the stepper motors . Starting from the 1st motor on the left, grab the end of the cat5e wires that we soldered to the motors in step 7, and solder them to the motor connectors with their corresponding color. At this point cut the wires short in length, just enough wire to reach the driver boards. Do the same for the rest of the motors.
Now we wire the (2) Arduino boards, start with the first stepper motor driver board on the left and connect a 4 conductor female connector and from there to the first Arduino's pin D1,D2,D3,D4 (see picture 1,2,3,4,5)
Here is the pin order: 1st Arduino Driver Board 1 2nd Arduino Driver Board 3
D4 IN1 D4 IN1
D3 IN2 D3 IN2
D2 IN3 D2 IN3
D1 IN4 D1 IN4
Driver Board 2 Driver Board 4
D9 IN1 D9 IN1
D10 IN2 D10 IN2
D11 IN3 D11 IN3
D12 IN4 D12 IN4
Now we need to power the stepper motor's driver boards. Connect a 2 conductor female connector extension wires to the board positive "+" and negative " - " terminals, then connect the other end to the small bread board's positive and negative bus bars. Positive to red bus bar and Negative to blue buss bar (see schematic and picture 6,7,8).
Next , take the 3 wires coming from the first pot on the left and connect one of the outside terminal wire to the positive bus bar (red) of the Arduino's bread board, and connect the other outside terminal wire to the negative bus bar (blue) of the bread board. Do the same for the other 3 potentiometers. Now take the middle wire of the first potentiometer on the left and connect it to the 1st Arduino pin A0. The middle wire of the 2nd potentiometer to 1st Arduino Pin A1. The 3rd Potentiometer middle wire to 2nd Arduino Pin A0 and the 4th potentiometer middle wire to the 2nd Arduino Pin A1 (see schematic and picture 9,10,11).
Now we are going to wire the SPST switch. Solder the 3 wire to each terminal of the switch. 3 of those wire are going to the power block of the bread boars, one for each Arduino and one for the motor's power supply. Now solder the other 3 wires to each battery positive wire. (see picture 12). Now the LED, solder one wire to the short leg of the LED and connect the other end to the small bread board Negative bus bar (blue). Now solder one wire to the long leg of the LED and connect the other end on the small bread board to a 220 Ohms resistor., and the other end of the resistor to the Positive bus bar (red)of the small bread board. At last upload the Arduino sketch on each Arduino and install the 9V batteries (one for each Arduino) and the 4 1.5V batteries for the stepper motors. Test you circuit make sure everything works and use tie wires to arrange wires nice and neat in the enclosure (see picture 13,14,15).
CONGRATULATIONS YOU ARE DONE , YOU ARE FINALLY DONE.
Step 12: Resistor Front Cover
Now cut a 3/4" x 3/4" opening on each location, I used a Dremel to cut the openings and then a file to make the openings smooth and square (see picture 14,1,16,17,18,19) . Next place a piece of tape on top and across each band and is ready to be painted. I used a glossy gold color. Once the paint is dried just peel the tape off (see last pictures 21,22). Now grab the Plexiglas and cut a 14" x 5 7/8 piece, install the hinges on the Plexiglas and then onto the enclosure. (see picture 23,24)
Step 13: Conclusion
Good Luck.
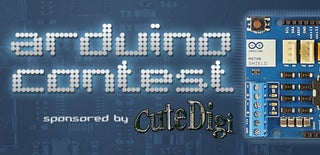
Participated in the
Arduino Contest
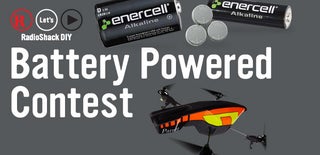
Participated in the
Battery Powered Contest
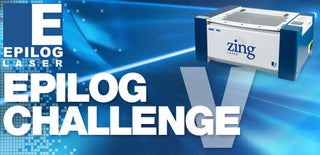
Participated in the
Epilog Challenge V