Introduction: Restoring Rusty Japanese Kitchen Knife and Making Secret Wood Handle
I bought this rusty chipped Japanese kitchen knife for few bucks to restore it. I was thinking what sort of handle I would like to do and I came up with an idea to change the traditional band around the neck of the knife into a secret wood type clear resin casting. I love winter and snow, and there currently a lot of snow where I live so I thought I'd like to have slightly blue ice looking resin on the handle. This was my first try at casting resins and it turned out quite well (on my second try).
Step 1: Restoring the Blade
i started by removing the handle with chisel and cutting the black plastic band off with a dremel. Underneath I found badly rusted tang. I decided to dump the blade in vinegar overnight so the rust comes off easily. I am going to sand the knife anyways but I thing it's often best to remove rust first so I know I'm not sanding off any stamps an If I have extremely bad pitting which requires me to start with very rough sand paper. After vinegar I used a wire brush to cleaned the blade. I also noticed the very edge of the blade was dark after vinegar which means the blade probably has very hard steel inside maybe a stainless steel jacket.
I decided to also use a belt sander to remove rust from the tang as it was badly rusted. After this I took out most of the pitting from the blade with the belt sander. this was followed with sanding down the chipped parts of the edge on the disk sander. Because I sanded the edge down I now had to regrind the bevels so I moved back to the belt sander to do most of the work. I finished the edged by filing as I personally find that more accurate way to do it.
After the blade was already usable but not very sharp or shiny I moved to polishing as polishing is also usually a good way to get extremely sharp knife. I started by sanding the sides of the blade with 120 and 240 grit papers on a block to keep the sides as flat as possible. I did some hand sanding around the makers mark to keep it intact. Then hand sanded the whole blade with grits 400, 800, 1200 and 2000. When sanding, every time you move to finer grit you might want to change the direction you sand slightly so you can see when you have removed all the scratches from the previous grits.
After getting the blade to 2000 grits it was already quite shiny but using metal polish compound on wool buffing wheel takes it to next level. I have found that during winter when I use these wax based compounds I need a little higher RPM to get a good polish than I need during summer. I think it helps the wax to melt the wax giving better polish.
Step 2: Making the Handle
For the handle I cut a piece of ash with some nice splits to fill with resin but my fist try failed because I used wrong type of resin. You can see that on the video. I bought clear casting resin for my second try. I put the piece of wood in a vise and hammered on it until it broke in two parts. This gave me cool broken wood texture which would be visible inside the resin on the handle. the I used a dremel to flatten an area in the middle of the black to make drilling easier. The I drilled a hole for the tang of my knife. I made two holes next to each others to make the hole wide enough for the tang. Then I used epoxy glue to attach the tang to the wood. The resin will later lock the blade in the handle so that it wont come off.
I had made a mold in which I would pour the resin. My mold had 3 layers and worked fine as I was going to sand the handle to final shape anyways. I made a box from cardboard which barely fitted around my wooden handle blank. Cardboard was used to give rigidness for my mold as the 2 outer parts of the mold were not as sturdy. The cardboard was tall enough to fit all the resin in. I covered the carboard firs tightly with aluminum foil and then with tape to prevent any leakages.
I used a bit of food coloring to make it slightly blue to imitate ice better (although ice actually is colorless but we think it's bluish so that makes better fake ice). Depending on the resin you use you might need different type of approach. I mixed the color before adding hardener to give me more time before the resin starts to gel down. Then I slowly poured the resin in the mold trying to avoid bubbles. I tapped the mold lightly to the side to get most of the formed bubbles out. The I just left the resin to dry.
After the resin was dried I sanded the handle to my wanted oval shape. At this point the surface was of course very rough and the resin was not transparent. Also a couple bubbles that were still left to the resin had surfaced. I filled the bubbles with resin and coated the whole handle with a layer of the resin to make it nice and shiny. This also causes the sanded resin to become transparent again. Before doing this you want to wipe down all the dust you might have on the surface from sanding the handle. the I just waited for the resin to dry again.
Step 3: Finished Product
After the resin was dried there was nothing more to do. I tested and the blade was razor sharp from the polishing. I don't think I've seen so sharp knife before. The steel seems to be very high quality. Overall I'm extremely happy how it turned out. The resin ended up looking very much like ice, as I had intended. The blue tint can best be seen on the pic with white background.
Thanks for checking out my instructable. Please also check out my project video and my other projects on my youtube channel. I post all of my work there. If you like my work leave a like and a comment as that helps me to keep making weekly projects.
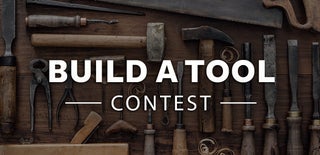
Participated in the
Build a Tool Contest