Introduction: Rotating 3D Model Capture Stand
Autodesk's app 123D Catch let's you upload a series of pictures of objects to create a 3D Model of the object from those pictures. If you read through, the suggestions are to take a series of pictures around the object from a few different heights making sure to encircle the entire object. I figured that an elaborate and unnecessary way to be anal retentive about getting the pictures from the same height all the way around was to create a rotating mount for the camera to get precisely aligned pictures.
I decided to do just that, and here are the steps I undertook to create such a monster.
Step 1: Tools and Materials
TOOLS
Drill
Saw (hand saw, circular saw, jigsaw, band saw)
Screwdriver/ (Drill)
Sander/ (Sandpaper)
Ruler/ Combination Square
Tape measure
Pencil
Hammer
Router with flush trim bit (or hand saw, jigsaw, etc)
MATERIALS
Plywood- about 3/4 of a 4'x8' sheet- if you use one thickness I recommend 3/4" (or glued up lumber)
Lazy Susan- size according to your project. I used a 6", but would recommend not being so cheap and using the 12" hardware instead (I'm not sure why Susan gets picked on- sorry, Susan. I know you might not be lazy- I know I am...)
Various Screws
Nail
Various allthread/ bolts/ wing nuts/ wing bolts (several build options)
Tee nuts
Dowel Pins (or nails, dowel, screws)
Please don't be intimidated by the above lists- again, you can make do with whatever you want to use. I ended up finding things in my garage for everything on this project- I did go to the store once, but it turned out to be unnecessary once I got home and realized I had the bit I needed already. That prompted one of a few impromptu side projects during the course of this, that one to organize my router bits.
The list of tools that I actually used was fairly extensive, but mostly because I have been fortunate to have acquired quite a few over the last 17 years. This project could certainly be done with far fewer tools rather easily (again, I am lazy and simply enjoy working with power tools), and some of the geometry could certainly be altered to make life simpler as well depending on what tools (and lumber) you have at your disposal.
Step 2: Determine the Size
I didn't make any official drawings with any dimensions throughout the course of this project, and this is the best it has turned out for not having planned more accurately. Initially I did a 3D model to get the workings right in my head and just to better visualize the final product.
My stationary platform for the objects is about 20" in diameter, the stationary bottom base is about 24" in diameter, the height between the two is determined by the thickness of your lazy susan hardware and the board you use to mount the camera arch onto. These platforms do not have to be round, so feel free to make them square for simplicity's sake.
What I discovered after the project was almost done was that using my real camera (and not my phone) will probably require a different rotating rig for anything bigger than the small hot glue gun in the main page photo, simply because the minimum focal length is then being taxed being so close to the lens. I could probably build one twice that size and that might be better- thankfully, one of the features I built in was to be able to disassemble the camera arch to make storing this beast easier, so I could easily adapt a new mount for the SLR and bolt it where the current arch bolts up.
Bottom line, the objects you want to scan and your camera's minimum focal length will pretty much determine how big your rig needs to be. Using the app straight from your smartphone will probably yield you the smallest setup since cell phone cameras tend to be rather wide-angled.
Step 3: Begin! Object Platform
Most of these parts don't need to be made in a specific order, so long as you know your sizes ahead of time, but I will take you through in the order I made mine (thankfully I didn't have any issues in that regard so this approach will work as it was originally done).
Cut your object platform- this will be the piece that your object to scan will sit on. I made mine about 20" and round out of 3/4" plywood. I laid out my circle by nailing a small finish nail into the center, using my combination square set about 10" and drew out a circle. Nothing fancy. I used a jigsaw to cut it out, and then sanded the edges a bit just to clean it up. Again, if you want to simplify things you can make this square so you can more easily make the cut with another saw. If you don't have plywood and want to glue up a wood blank to use that will work, too.
This is the part your future 3D model will be derived, so admire your progress and think of all the wonderful things that will one day sit upon this pedestal of yours.
Step 4: Object Platform Supports
The supporting stuff really does the hard work and usually gets little glory, but this is what comes next. Depending on just how big your lazy susan hardware is (I went relatively super cheap and did three times the work on these pieces because of it). I chose the 6" lazy susan, which didn't give me a huge opening in the center for my support pieces to connect through, so I made my support pieces T-shaped in order to be under more of the base. I could probably have gotten away without this, but I was feeling froggy.
These pieces need to fit inside the lazy susan hardware opening, and need to be tall enough to clear the lazy susan thickness + the thickness of the board you will be mounting the camera arch to. If you go with the 12" lazy susan you should be able to just use rectangles and be VERY safe in supporting your object platform.
I decided to get a tiny bit fancy and interlock the support pieces so that they would be a bit easier to make stay within the lazy susan during final assembly. You could probably do this differently to again simplify the tool requirements or to just make it simpler for the sake of being simpler. I chose the complicated route for fun. The pictures above show the geometry I used to: interlock the supports, fit within the smallish lazy susan and support the object platform more fully.
To do it over again, I'd probably keep the same geometry still, but with the 12" lazy susan. I may even go back and replace mine when I have nothing better to do and a few extra dollars to spend.
Step 5: Camera Arch Base
The next piece I made was the Camera Arch Base- this part needs to be wide enough to have a cutout for the supports in the center of it and still have enough strength to support the arch on one side. The other side probably needs to come out almost to the other side of the Object Platform to help counter balance the arch, and worst case maybe even put a support on to keep the arch steady. I haven't had to do that yet, but planned ahead because I can see it happening, especially with what happened to mine during fabrication :(
There are many designs possible for this piece- mine is pictured above. The only advantage to being cheap and having purchased the smaller lazy susan is that it means you can get away with a smaller piece for this than if you invest in a sizable 12" piece and have to have a 10" hole for the supports to pass through...
I cut mine out with a jigsaw. The center portion is cut it out with the jigsaw, too, after I drilled out a pilot hole for the blade. After some sanding to remove the rough parts this piece was ready to go.
The tapered shape on the one end actually became functional, and if you're going to follow this design, you will want to make sure and try to make those two edges parallel. In order to make my Arch removable, I decided to have the Arch come down over the Camera Arch Base in order to register it somewhat and add additional support. My intent is to even go back and add guide pins for additional support and less fumbling during the assembly of the Arch onto the Arch Base.
Step 6: The Golde...um, Camera Arch(es)
Brilliant! Now to the fun stuff. Here is the heart of the operation, aside from all the other useful parts : )
The Camera Arch is another one of those parts with a LOT of room for design changes based on tool limitations. You could make it out of flat stock nailed together with spacers to create the channel and just make the Camera Base swivel on it. If you have even fancier tools you could have it laser cut- it spans all options in between.
What I did:
I physically modeled the profile I wanted with a piece of doubled up tie wire (to help it keep its form better) with the lazy susan on my workbench, the Camera Arch Base sitting on the lazy susan and the Object Platform sitting on the supports (inside the lazy susan) so I could mock it up accurately. I bent the wire to the shape I wanted and then traced it onto plywood. I guesstimated the width I wanted it to be (keeping in mind a slot would be cut from the middle of it eventually) and offset the profile a few inches away. Because I wanted it to sit on the Camera Arch Base, I made sure and had material at the bottom of it to come down over the sides of the Camera Arch Base.
Once my profile was complete, I cut it out with a jigsaw and sanded the edges to smooth them out a bit. You can see that the shape isn't perfect, but it's perfectly functional. After sanding, I put the first profile on the plywood and traced the shape. I cut the piece for the second profile (just wide of the tracing) and then nailed the two pieces together, making sure I had an overhang all the way around on my second piece.
I used my router and a flush trim bit to cut the second profile to match the first (imperfections and all :).
Again I used my combination square and traced the profile shape along the center of the Arch, then offset it to each side by half of the width I planned to cut the slot. I had a piece of 5/16" allthread to make a bolt out of, so my next bigger router bit was a 1/2" (plenty of slack room there...).
I made a couple of shallow passes in the first profile piece (still with them nailed together) to cut the slot. When I had gotten deep enough, I did a plunge cut at one end all the way through both pieces. Then I flipped them over with the started slot facing my workbench and used my template bit again. This let me cut the rest of the slot through both pieces and not have to guide it by hand the whole slot- the flush trim bit followed the shallow path cut by the first couple of shallow passes.
Step 7: Spacers and Camera Arch Assembly
These spacers will be used for the Camera Arch- they need to be just a little wider than the narrow end of your Camera Arch Support where the Camera Arch will mount. I used a piece of plywood and a piece of a 2x4, with the plywood about 7" long to give it as much contact surface as I could.
I scribed a line on what would be the inside of each piece of my Camera Arch at 23/32" to line the bottom plywood up to. This lets the sides of the Camera Arch sit over the Camera Arch Mount (which is 3/4" thick) and have just a tiny bit of clearance without hanging below the mount. The top spacer isn't as crucial and should just be above the slot in the Camera Arch.
I glued, finish nailed and then screwed these together. You could get away with nailing, gluing and nailing or stapling or just screwing them- I just wanted super sturdy since my DSLR may be mounted on this and it's one of those items I can't afford to buy a second time!
Test fit the Camera Arch on the Arch Mount- I cut my spacers the same width as the Mount and then did a little sanding on my Arch Mount to make sure that the Camera Arch fit snugly but an extra 1/16" added to the spacer width wouldn't have hurt anything.
Once I was happy with how the Arch and Mount fit together, I clamped them together and drilled two holes through both pieces. To fasten them together I put a couple of Tee nuts in the Camera Arch Mount holes. I cut two too long bolts down and welded a wing nut on each piece to make a wing bolt (I didn't have any wing bolts- there's certainly no need to make them if you already have some). The allthread or bolts just need to be as long as the thickness of the two boards being sandwiched together plus a tiny bit to weld to if you're making your own. In my case it was 1-1/2" with the two pieces of 3/4" material.
You don't have to use wing bolts- you could certainly use hex heads or something else- but I wanted tool free assembly.
Step 8: Camera Mount
For the camera mount I held my camera in place and got a measurement of about how long the mount would need to be, going from a little bit forward of the tripod mount on the bottom of the camera (enough to help support the camera body but not interfere with the lens) and far enough back to almost come all the way back to the Camera Arch. The piece will need to be that length, and just shy of the width of your Camera Arch spacers since this piece will need to ride in between the uprights of the Camera Arch.
I had a piece of 5/16" allthread to use for my thru bolt to ride in the Camera Arch slot, so I marked where the slot would be on the mount and drilled a clearance hole through the Camera Mount. It had to be drilled from both sides because my bit wasn't long enough for one pass, so a drill press is very handy (but not absolutely necessary).
With that hole drilled, I held the mount in place, put the allthread through the mount and the slot and held up the camera on the mount to locate where to drill the tripod mount hole. I got my measurement and drilled a clearance hole for the 1/4-20 camera bolt. I had some 1/4-20 allthread and again welded a wing nut on to make a wing bolt. To measure the allthread i screwed it in to the camera body, put the body on the mount the best I could with the allthread in it, backed the allthread out about a 1/2 turn and measured to the bottom of the mount, marking it with tape to cut against. Backing off the 1/2 turn before you measure the length gives you clearance for the bolt to go into the camera and get a snug fit. Otherwise it may bottom out too soon and not tighten down. If you run in to that you can always grind down the end of the bolt.
To make life easier (and I haven't done it yet) it may very well be worth putting a 1/4-20 Tee nut in the camera mount so that the wing bolt acts like a captured screw and doesn't fall out every time you go to mount your camera. That'd be one less thing.
To see how I made the mount for a cell phone, you can see the companion Instructable here: Cell Phone Mount
Step 9: Camera Mount Guide
I added a block under the camera mount to add to the guidance of it as it moves in the slot made from a 2x4 and a couple of wooden dowel pins.
1. Cut a piece of wood the same length or slightly smaller than the width of your camera mount.
2. Drill a hole in each end sized for your dowel pin/ dowel/ etc for your guide
3. Attach the Camera Mount Guide to the Camera Mount, with the holes in the ends lined up with the hole for the thru bolt that rides in the Camera Arch slot.
4. With the Camera Mount attached to the slot, push in the guide pins. I adjusted the depth of my holes so that the pins would not stick out beyond the Arch.
Step 10: Now It's All About the Base
Finally! Time for the foundation of the whole ordeal. You can make your base round or square or hexagonal or whatever- it just has to be large enough to support your Object Platform and the whirling, twirling Camera Arch, so I recommend bigger than smaller. I made mine small-ish, with the knowledge that I may need to make removable outriggers in the future, but if not than I have spared a permanently huge footprint for this niche device.
I once again went with round (this being a rotationally themed item it seemed fitting) for my base. It is about 24" and my Object Platform is about 20"- seemed like a good starting point to me. Same layout procedure as the Object Platform- center nail, combination square and cut with a jigsaw, sand the edges. You know the drill by now.
Step 11: Lazy Susan Sandwich
The only sort of complicated thing about this is the lazy susan and the order of events required by it.
1. Lay out the location of the lazy susan hardware on the base (the center is probably a good idea).
Since I used a nail to mark out my circle, I used it as a reference to get the lazy susan in the middle. Draw perpendicular lines through the center point and then get the holes for the lazy susan that will be used to attach the base lined up on those lines. Trace them onto the base. Turn the top of the lazy susan (the ring not touching the base) so that the top ring's holes are in between the holes of the base. Mark the top ring holes on the base- these holes mark holes that will be drilled all the way through the base.
2. Drill thru holes
You need to drill holes big enough to let you put your drill/screwdriver tip through the base and drive the screws through the lazy susan into the Camera Arch Mount.
3. Attach lazy susan to Base
Put the lazy susan back on the Base and screw it onto the Base with it facing the same direction you had it when you laid it out on the perpendicular lines. Put the screws through the holes on the perpendicular lines. I highly recommend screws that are short enough to be fully threaded- if they are too long that's fine- you can grind the tips that poke through off (I had to grind mine).
4. Attach lazy susan to Camera Arch Mount
Put the Camera Arch Mount on your table/workbench. Put the Base on it, with the lazy susan in between them. You HAVE to center the hole in the Camera Arch Mount on the lazy susan at least enough to allow clearance for your Object Platform Supports!!! When you are sure you have that clearance, get the holes in the Base lined up with the holes in the lazy susan and screw the lazy susan to the Camera Arch Mount. The Camera Arch Mount should spin freely on the base
The hard part is done!!!
Step 12: Getting Closer!
Time to put on the Object Platform Supports and the Object Platform itself.
Apparently I got lost in the moment and either didn't transfer all my pictures or simply skipped them for this step, so I have some 3D representations of the step- it's an easy one (thankfully)!
1. Put the supports together upside down.
2. Flip the Base over on to the supports, putting the supports in the center hole of the lazy susan (and in the middle of the Camera Arch Mount).
3. Screw the supports to the Base. Be careful to line up the screws visually so they only go into the Object Platform Supports. The Camera Arch Mount should still spin freely once the supports have been attached. IF it doesn't, check your assembly.
4. Set your assembly so that the support top is facing up.
5. Center your Object Platform on the supports and attach it to the supports. Again, be careful to line up the screws visually so they only go into the Object Platform Supports.
Step 13: The Whole Point- Capture a Model
If you had removed your Camera Arch from the Camera Arch Mount, it is time to put it back on.
1. Mount your camera to the Camera Mount.
2. Put an object on the Object Platform
3. Take your pictures at one height, encircling the object, adjust the Camera Mount to different angles as necessary and repeat.
4. Upload your pictures and when your model is processed check it out!
Step 14: (Possible) Future Additions
There were a few things I thought of during the course of assembly that would make good improvements and add-ons but haven't done yet (some of which may have already been mentioned).
- add a 1/4-20 tee nut to the camera mount so that wing bolt doesn't fall out
- add a spacer between the Camera Arch Mount and the under side of the Object Platform to steady it more
- add an index pin to the Camera Arch Mount and index marks on the Object Platform to be able to repeat picture angles or get the pictures consistently spaced
- add lights to the Camera Arch- something with soft lighting to avoid harsh camera flash-like shadows
- decoupage or add newsprint to the Object Platform to have a permanent busy background (this helps the software register and align images to when it stitches them together)
- make another Camera Arch that sits further back from the Object Platform in order to be able to more fully utilize my DSLR and not be on the tipping point of its focal length
If you make this and incorporate any of these features or think of something different to put in yours, please post them!
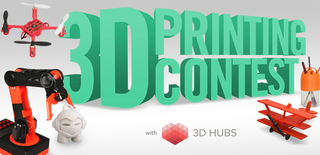
Participated in the
3D Printing Contest