Introduction: Rubens Tube: Flexible & Variable Length!
You may have had your eyes light up upon seeing this fun demonstration of acoustic physics somewhere on the internet or maybe even in person! However every Rubens Tube that I have seen has been a simple boring pipe because all it is is a rigid, straight pipe with holes bored into it that would take a lot of space to store when not in use and has limited applications outside of demonstration because the configuration is fixed. What if we could make a Rubens Tube that could have a variable length and the potential to explore if a curve path has any effect on a standing sound wave! Before we make this variable length, flexible Rubens Tube we first need to understand what Rubens Tubes have been and how they have worked for over a century.
The Rubens Tube was invented as an acoustics demonstration by a man named Heinrich Rubens in the early 1900's. Mechanically it is a tube capped at both ends with a series of holes set in a line, but the two end caps have different purposes. There is a flexible membrane at one end to allow for acoustic energy to be coupled into the enclosure while the other end of the tube is rigid and has the job of reflecting the acoustic wave back into the tube.
Now for most frequencies very little that happens with this configuration. However depending on the gaseous contents of the tube and its length there are a collection of frequencies that will match the geometry perfectly to create a phenomenon known as a standing wave. This happens when the length of the tube matches some multiple of the wavelength of the acoustic pressure wave that is passing through it. The result is a series of nodes and anti-nodes along the length of the tube.
What is exciting is that we can calculate what the standing wave frequencies might be through understanding the relationship that exists between frequency, wavelength, and speed of the wave in the medium which is modeled most generally by this simple equation:
frequency = speed / wavelength
The first interesting thing that we encounter is that sound moves at different speeds through different mediums. When sound moves through air it typically goes 340 meters/second but when sound moves through something like propane which we will be using for this experiment it moves much slower at 257 meters/second.
How then do we use this information to predict what our resonant frequencies will be? Well first i want to note that these will be approximations since the gas inside the tube will not be 100% propane so the speed of sound will be somewhere between 340 meter/second and 257 meter/second but closer to 257m/s. However even though we will not be able to predict it perfectly this process will help us narrow down where to look for these resonant frequencies. One help feature of resonance is that we only need to solve this equation once since resonance follows harmonics which are multiples of the lowest full wavelength frequency which we are setting to the length of the tube to solve for the frequency in the equation above.
Even though the tube says it can be 8' long I did not trust myself to not tear through the side so I decided to go with a set up that is only 5' 10" long otherwise known as 1.78 meters long so that we could theoretically get simple whole hertz standing wavelengths instead of decimal values and so that one of the harmonics would land of 432Hz if the tube was filled with pure propane. The rationale behind this decision is that it makes the math easy for this portion of the instructable until I decide to start adjusting the dimensions! Now we put our numbers into the equation replacing the wavelength with the length of our tube and the speed with both the speed of sound in air or the speed of sound in propane:
Frequency(Air) = (340 m/s) / (1.78 m)
Frequency (Air) = 191 Hz (Note: Hertz (Hz) is the unit for 1/s)
Frequency (Propane) = (257 m/s) / (1.78 m)
Frequency (Propane) = 144 Hz (Note:Hertz (Hz) is the unit for 1/s)
One of the easiest ways to visualize this before we build the Rubens Tube is to tie a piece of rope to a fixed point and then start swinging your arm up and down. If you find the right swinging frequency you can achieve a first harmonic standing wave in the rope where there is a section of rope halfway between you and the fixed point that looks like it does not move while the other sections of the rope swing wildly. The still section is a point called the node and the sections that move the most are called the anti-nodes. We will talk about these more later when we get to how they affect the Rubens tube.
So if the Rubens tube was just a tube with end caps it would not be that interesting or impressive. While you would be able to hear the resonant frequencies by the fact that they would be louder than the other frequencies there would be no other affect to observe. This where a small set of changes can be made to this tube to create an impressive demonstration that if you are not careful it could burn your brows off.
What I have described so far is at best auditory but potential boring and purely intellectual because how are we supposed to visualize this concept like we did with the rope to understand phenomenon that is generated solely by the use of sound which is a term called cymatics? This is where the most fun part of the Ruben's Tube comes into play and why I reference the idea of using propane as the gas in our tube. When a standing wave is achieve there are zones within the tube of compression and rarefaction. These zones find brilliant expression through the series of spaced holes on the top of our tube where the zones of compression release more propane making the flame above those zones larger and the zones of rarefaction release less propane making these flames smaller. This lets us see a unique sinusoidal waveform of rolling hills in the flames that come from the tube.
This remains true as long as your tube is properly sealed which took me many iterations and interestingly enough using Duct Tape for its intended purpose of actually taping a duct!
With our understanding of Rubens tubes primed a little bit lets get into the materials and tools that you need to make a flexible Rubens tube!
FTC Disclaimer: I earn a percentage of the sales through the affiliate links provided through Amazon.
Supplies
Materials
- Duct Tape!!! (Lots of Duct Tape to keep all of the leaks out!)
- 4" x 8' Semi-Rigid Aluminum Duct (Main body. Caution: It is super fragile and easily accepts unwanted holes)
- Two 4" Round Duct Cap (Hard cap to reflect the sound and mount the fuel inlet and rigid cavity for speaker)
- 4" Aluminum Duct Connector (Used to connect the flexible duct to the end cap)
- 3" x 4" PVC DWV to Sewer and Drain Adapter (Used to connect the 3" Flexible cap to the tube)
- Caulking (Sealing the cap connections)
- 1/4" x 1/4" NPT Male Industrial Brass Plug (Input port for the fuel)
- 1/4" NPT Female Brass Bushing (Only way I could find to secure the Brass Plug with the same threading)
- Two 1/2" O-Rings (Used to seal the connect of the Industrial Brass Plug to the 4" Duct Cap)
- Bluetooth Enable Audio Amp(Used to control the Acoustic Exciter from a cellphone)
- Or there is the gutted Bluetooth Speaker that I started with that is here!
- Acoustic Exciter (Used to drive the 4" Flexible membrane in the end cap)
- Or there is the smaller exciter that I started with that is here!
- 4" of red and black wire (Connecting the Bluetooth Speaker to the Acoustic Exciter)
- Party Balloon (Speaker Diaphragm)
Tools
Step 1: Preparing Your Rigid End Cap and Propane Input
Starting with one of the 4" round Duct Caps find the center of the round face and mark it. While there are ways to do this that are very accurate we are only needing to be approximately centered so I just eyeballed it.
Then using a Step Drill bit place the cap onto your work surface and drill a hole to 1/2". You might be thinking like I was while planning this project that the dimensions of the brass plug say 1/4" but just like how the 1/2" copper pipe in the sugar snake instructable was nowhere near 1/2" or boards are not that close to their nominal dimensions of 2"x4" this seems to be another place where measurements are only useful when they are used within the same space but if you are trying to use other materials they just will not work. This played out also when I purchases a 1/2" 13TPS nut for attach the male connector to find that the size and threading are completely different and I ended up going with 1/4" NPT female brass bushing from the air tools section to ensure that the threading would fit well.
Once you have the 1/2" drilled use a small needle file to carefully smooth and deburr the hole. Now using the two 1/2" O-Rings place one all of the way onto the threaded end of the air connection and push this threaded end through the hole we just made in the duct end cap so that the threads go into the cap. With the connector in place slide another O-Ring onto the threaded end so that the metal cap is like the patty in the middle of a doughnut bun sandwich. The goal behind using these O-Rings is to seal the hole around the port from leaking propane from this connection point by pressing the end cap between the two O-Rings
With both O-Rings in place grab the brass bushing and start to thread it onto the connector by hand and once you hit the limit of what you can do grab your pliers/wrenches, and socket set to tighten the setup down to ensure a good seal on your O-Rings.
Step 2: Finishing and Installing the Rigid End Cap / Propane Inlet
We have made a good effort to make this connection leak proof but if you are looking at the rest of this cap you might have been wondering what was the point of the O-Rings when the seams on the cap itself and where this cap will connect with the ducting look gas would go right through them. This is where the caulking and the duct tape come into play. I decided to caulk the inside of the seam for both aesthetic reasons and because a higher pressure will exist in the tube during operation and by having the sealant on the inside this pressure will work to my advantage ensuring a better seal. I then applied duct tape around the outside of the cap to seal the other side of the seam that I just sealed with the caulk.
Next I laid a bead of caulk along the inside lip of the end cap and inserted one end of the 4" duct coupler that would be used to connect the end cap to the flexible ducting. I learned after testing the full set up and having this seam catch on fire that I needed to add a layer of duct tape to the seam between the duct cap and the duct coupler. The rigid end cap that also doubles as the input for the propane is now ready to inserted into the flexible ducting. Once this is fully pressed in which might take a little bit of convincing it should set well. Originally I planed on only using duct clamps to seal this seam but that again provided to be a bad idea in that they do not make an air tight seal. It was at this point after this seam also caught fire during testing that I pulled out the duct tape again to ensure that I had a firm seal on all of the coupling points at this end of the Rubens Tube.
Step 3: Building the Acoustic Exciter Cap
Most of the Rubens Tubes I have seen utilize a two part system of flexible membrane air gaped to an independent audio driver or speaker but I wondered if I could cut out the air gap middle man improving the acoustic transfer of power. There are these interesting parts called acoustic exciters which are effectively a speaker without the cone so you are only getting the driving coil and magnet. The way that they work is that you can attach this driving coil to a surface with the provided adhesive and it couples the acoustic vibrations to that surface effectively turning it into a speaker.
I had started this project using a smaller 19mm acoustic exciter I had laying around from a different project and a small bluetooth speaker as the driver hoping that it would give me enough acoustic energy to generate the standing wave I was after and to survive having the tube bent or manipulated. While it did start to achieve the characteristic Rubens Tube display it was clear that it was under powered so I moved up for the 4W exciter and probably 3W bluetooth speaker. Not wanting to delay this project any further I decided that I was going to turn the old adage on its head by going Big because I am stuck at home. This meant that I purchased a 24W exciter and a 50W amp to drive it with. Needless to say I am determined that this project will not fizzle out of again if it is going to fail it is going to go up in flames.
Starting with the other 4" duct coupler and a party balloon I went to work. First I trimmed the party balloon with a scissors to get rid of the inlet lip and the narrow neck of the balloon to make it easier to put on. However it is important to not trim back too much otherwise the balloon has an increased chance of walking off the end of the coupler due to its own tension.
Now that I had the balloon on the duct coupler it was time to build out the acoustic exciter circuit.
Like I had said above I originally had gutted a small bluetooth speaker but that turned out to be under powered therefore really did not light my fire. I shifted gears to use a compact but powerful audio amp board that contains the audio amp and Bluetooth chip for the speaker. Since there was such a wide selection on the internet it was a little bit of a challenge narrowing it down, but after sounding out my options I picked one that I thinks resonates with me. I then soldered some wires to my acoustic exciter so that it would be easy to attach to the terminals of the audio amp board. The exciter then has a small adhesive disc that I used to attach the exciter to the balloon that I have attached to the end cap. Testing the driver resulted in a fun small speaker which means that this has a great chance of working without needing to find a larger driver.
One of the reasons that I think we can use an acoustic exciter instead of the the speakers I have typically seen for this project is because the acoustic energy is directly coupled to the rubber end cap instead of having a speaker conduct sound through the air before the air has to act on the rubber membrane which introduces all sorts of loses and potentially confounding factors. This also creates the potential of having the demonstration of standing waves to be much quieter since the sound energy is more effectively directed into the tube and less prone to stray radiation.
Taking the completed acoustic exciter and BT driver board I applied it to the balloon membrane and took it for a test drive. It sounded like the literal tin can that it was since it is made from sheet metal tube. One thing that I noticed was that a reasonable amount of acoustic energy was coming off of the back end of the speaker so I decided to enclose the duct coupler speaker with the other duct end cap. The result was a sealed speaker that had a slightly improved acoustic response.
I learned that it my initial testing that the seam between the coupler and the end cap was prone to leaking propane so I grabbed my duct tape and caulking once again to seal the seam at the end of the cap and where the coupler and the end cap met which is also where the wires came out for the speaker amplifier which turned out to be a difficult path to seal up.
Step 4: Attach the Acoustic Exciter Cap to the Tube and Trying to Not Start a Battery Fire.
This should have been straight forward. The acoustic exciter cap was finished and the remaining open end of the flexible ducting was just waiting to have a cap put on it. Initially like I had said with the rigid end cap I only used a duct clamp which seemed like it would work fine but after my first test this end of the set up caught fire in spectacular fashion you can see it happen in the YouTube video I have for this project.
I then went through multiple iterations adding more and more duct tape to ensure that the end of the tube would be sealed tight and not let any more propane out. During this process the plastic casing around the the battery on the speaker actually started to melt and the pouch cell has puffed up a little bit meaning to me that I will need to change this out for future demonstrations but that it will hopefully in the wise words of Gimli at Helms Deep, "Lets hope they last the night".
Once I had enough duct tape to hold a boat together applied I was confident that I had a stable seal and that I was ready to go as long as the speaker driver did not fail.
Step 5: Preparing and Drilling Holes in the Main Tube
Starting with the semi-rigid ducting still compressed I took a few moments to inspect the material. Looking at how this material is designed to expand and flex it looks like it should be perfect for this project. There are fixed rings in between smaller accordion sections where the stretching and bending happens. The fix sections are evenly spaced and will not be obstructed when the pipe is manipulated evidenced by the fact that when the pipe is fully compressed they are still visible. This simplified the project in this step by not needing to measure the distance between the hole sites. However in extending the tubing I noticed that the accordion sections actually are spiral in nature so that they cause the tubing to twist as it is extended. I measured out the length of tubing I wanted and marked the line that I wanted to drill with some painters tape so that it would be easily removed.
Note: One extra benefit of the semi-rigid ducting is that it is made of aluminum and not galvanized steel. I talk about the dangerous potential of Zinc Oxide fumes in my Sugar Snake instructable at the link here where I decided to use an enameled pan instead of galvanized tub:
FIRE SNAKE!!!The particular section of interest about avoiding metal fume fever by avoiding galvanize materials is found in Step 1.
With the tubing extended to the desired length I measured in a length of ~5" from each end after factoring in the end caps which are ~2" tall so that I would have some spacing between the end of the tube and the first hole to try and keep the ends of my tube from igniting. Once I had that marked off I start using the the same 3/64" bit I used in the fire snake project to create holes that are 1.2mm in diameter in each of the fixed sections of the duct.
Step 6: Testing the Rubens Tube and Let the Experiments Begin!
If you have survived to this step then you should have a completed adjustable and flexible Rubens tube with both ends capped off and access points for the propane and for the acoustic energy.
NOTE: Before you fill the tube with propane it is very important to have protective equipment. Steve Mould on youtube discusses a very important safety factor in his video about resonance where he uses a Rubens Tube and that there is a stoichiometric mixture of propane and air that is explosive and it is important to get the mixture inside your tube above that percentage before you attempt to light your tube. Check his video out! I can not "smell percentages" like him so I am just stuck being careful.
OK we are ready to start out own experimentation.
NOTE: Burning propane produces large quantities of carbon monoxide so if you are replicating this experiment I would implore you to do it in a very well ventilated area because carbon monoxide poisoning is no joke.
First we attach our propane or gas source to the connector on the end of the tube and using your regulator begin feeding in the gas. Once there is a noticeable odor of propane coming from the tube start by lighting your tube at the end where the gas is sourced from since this end will be the first to have a sufficient concentration of propane. After you have the first few ports lit it should be easy to move you lighter along the whole tube or even using your hand to fan the flame to the other ports.
When you have all of you ports lit you might need to tune your flame height by adjusting the flow from the propane regulator. The target should be to have flames at least 1" tall. Once you have the desired steady state effect in your tube now is the time to crank it to 11 by turning on the Bluetooth speaker and start playing your favorite songs to see how the tube responds or finding resonant notes to see how the flames respond! I took my time to get an intuitive sense for how the tube operated in a straight configuration before I started to test adding a curve to the tube but once I added the curve it was awesome!
Using the calculation of of the resonant wavelengths from the first step based on a tube length or 1.78 meters and the speed of sound in propane being 257 meters per second we could expect the resonant or standing wave frequencies of this Rubens Tube to be multiples of the first harmonic which is 144Hz. Now as I was working with this something dawned on me and that is that the length of the Rubens Tube will never be a full wavelength. The reason being is that the reflecting end cap will always be a node and the audio driver will always be an anti-node which means that the progression would look like the following frequency multiples of the first harmonic to create a standing wave:
1/4, 3/4, 1 1/4, 1 3/4, 2 1/4 ...
The progression is because nodes and anti-nodes are a quarter of a wavelength apart while a nodes and also anti-nodes are half of a wavelength away from each other hence the initial 1/4 wavelength and then the progression in 1/2 wavelength jumps.
It was a blast to see how well the tube worked and that bending the tube in a sharp U-shape or even into an S-shape did not negatively impact the tubes ability to generate and sustain a standing wave.
Step 7: Summary Thoughts
One of the things that I noticed with this set up was that one of the resonant frequencies was closer to 320Hz. How can we use this information of frequency and the speed of sound in air and propane to estimate the percentage mixture of propane to air in the tube? We know the length of the tube at ~1.8m and we know where the resonant multiples will be: 1/4, 3/4, 1 1/4, 1 3/4, 2 1/4 ...
So using a simple spreadsheet and a little bit of math we can make a guess at what the composition might be.
Since we know the length of the tube and that the mixture inside of the tube consists of air and propane we have the potential to make an estimate of the stoichiometric composition of the gases in the tube by looking at the speed of sound in the tube by solving the following equation in reverse for one of the cymatic frequencies knowing that the answer is somewhere between what we would calculate of air and propane.
frequency = speed / wavelength
Frequency(Air) = (340 m/s) / (1.78 m)
Frequency (Air) = 191 Hz (Note: Hertz (Hz) is the unit for 1/s)
Frequency (Propane) = (257 m/s) / (1.78 m)
Frequency (Propane) = 144 Hz (Note:Hertz (Hz) is the unit for 1/s)
The result that I came up with might feel like a little bit of a wet blanket in that I think that the composition is in the higher 90% but there are considerable margins for error in the length of the tube and the accuracy of the frequency that is being coupled into our Rubens Tube. This high concentration is likely due to a multitude of factors.
- The only gas that is entering the tube at any pressure is propane through our inlet and the rest of the tube is either spouting fire or sealed up as tightly as we can make it
- Propane is a heavier than air gas which means that over time it will eventually fully replace the air the tube just like when you fill a fish tank with water the air is displaced by the denser substance.
One of the many takeaways for this project is to prototype the idea of a curve Rubens Tube to see it it would be worth it to make a more robust curved setup by actually bending a rigid pipe. This was another major insight that was gained through testing. The way that the flexible tube is constructed and its lightweight nature made it susceptible to vibration which undermined the results of the demonstration. This was clearly seen at higher volumes and when the tube was in bent configurations. It would be really fun to make a system that could wrap in front of drum set driven by the fundamentals of the different elements of the drum. Leave me a comment on the YouTube video or the instructable if you would like to see something like this idea in a future project!
Thanks for reading through my instructable and visiting my Youtube Channel RyanMake where I explore science and engineering ideas to see what sort of amazing potential is hidden just beneath the surface. If you would like to see more projects like this I would ask that you follow me here on instructables and like, comment, and subscribe to my youtube channel! Until next time happy making!!! RyanMake
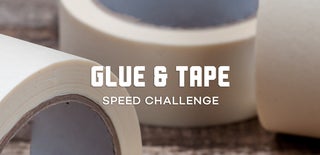
Grand Prize in the
Glue & Tape Speed Challenge