Introduction: DIY Car Crash Test to Show the Importance of Seat Belt & Air Bag
Hello everyone..
It’s been a while since I have published an article in instructables. Being a Mechanical engineering graduate I always watch car crash test videos by leading car manufactures where things are put to the limit and thus determining how much safe or how much catastrophic the damage is to the people inside. I always thought about creating a DIY test scenario similar to it but never took that serious and moved with other sort of projects. But a week back I though to make this idea practical and give it a try which finally turned into this project.
This project is a little effort from my side to spread an awareness for car safety. While thinking of car safety, seat belt is the main thing that I’m talking about. This project deals with mimicking different car crash test scenario. The first without seat belt & air bag the second one with seat belt and also including the added safety feature called the air bag. It would be better if you could watch the video first. the crash test can be seen towards the last 2 minutes of the video.
Step 1: Realizing the Reality
How often do you think of car safety??
So before we start I would like to begin with some simple questions to you all.
How often you think about wearing a seat belt when inside a car?? How often you make sure that your kids or your family always buckled up while inside a car?? Are you that person who ignores seat belt during a short drive??
Likewise there are tonnes of other related questions regarding this and it’s a truth that many of us would admit that we are not properly concerned about car safety.
Studies reveal that from 2011 to 2015, an estimated 343,000 children ages 8-14 were injured while traveling in passenger vehicles, and an additional 1,692 children were killed. A full 50% of those who died were unrestrained at the time of the crash. The numbers seems shocking right?? Then probably it would get worse if we include the death count from age 8 to 50. If putting a seat belt hardly takes around 10 seconds then why does these accidents happen so?? Can’t people even bare 10 seconds?? I believe that the simple answer is either ignorance or lack of knowledge from the side of people. So I think the solution for this could be creating an awareness and what I’m trying to do is just that. You could either continue reading or ignore this and it's totally up to you but one thing I could assure you is that if the kids and their parents find some time during weekends to try this project it will be a great experience and may even save their life one day in future . Being that said lets get into the project
Let’s get started......
Step 2: The Main Pressure Chamber
The pressure chamber is the most important thing in this project. It’s just like the fuel to run the project, as we all know when we mix vinegar with baking soda it causes a reaction, called neutralization which leads to the formation of CO2. This evolving CO2 under a closed vessel could build up pressure and can be used upon need.. Actually we are using two types of pressure chamber. First one is to force the car to hit on the crash block i.e the thing which moves the car. The second one, which is comparatively small, is used to inflate the air bag during crash. Let’s start with the bigger one. It consist of a 20 cm long 2 inch PVC pipe where one end is fitted with a 2inch ball valve whereas the other end is fitted with a 2 inch to 1 inch reducer. Then a 1 inch valve followed by 28 cm 1 inch PVC pipe. The length of the section are take according to my convenience and roughly calculated according to the final setup length and platform where all the fittings are done, which we’ll discuss in the later sections so there is no necessary to strictly follow the dimension. So in the end we will get a pressure chamber with valve at both end and a long barrel at the front just like a rocket launcher.This finishes the bigger pressure chamber.
The section between the two valves holds the mixture and gets pressurized where the 2 inch valve is used to fill the chamber whereas the 1 inch valve is used to release the pressurized mixture which pushes a specially made piston arrangement which we will discuss later. Thus it’s clear that the 2 inch valve side is the back side and the 1 inch valve followed by the 28cm long pipe connected to it forms the front side of the chamber. If looked closely it reveals that the mixture should be retained within the two valves and anything that overflow it is of no use. This is the main reason that we are using the 2 inch valve at the back since it is easy to look when the chamber is filled from back whereas in the front looking through the long 1 inch pipe to see the valve filled or not makes it way more difficult.
All the parts are well fitted and sealed with PVC solvent to create a strong permanent bond. Simply tight fitting the pipe won’t work for this project since it immediately burst open due to rapid pressure rise. Since we are dealing with this sort of pressure it is very important to use a thicker PVC pipe to be on the safe side. 3mm or 4mm thick at least.
Filling up the chamber
To fill the chamber first closed the front 1 inch valve. Open the back 2 inch valve and place it vertically such that the valve faces you. First fill it up with vinegar and then put the baking soda and quickly close the valve, give it a shake to mix properly. It only takes few second to get the chamber pressurized. One thing to be noted is that fill the chamber up to 3/4 of its capacity and leaves the remaining portion for the CO2 to get filled. So regarding the amount of vinegar and baking soda needed.. Since the concentration of vinegar and the quality of baking soda varies a lot from place to place it is difficult to specify the exact ratio so better to do some trial and error to get the best result. What I have followed is 1 teaspoon of baking soda for each 30 ml of vinegar. I think it’s a rich ratio and it’s essential to create this sort of pressure.
Step 3: The Air Bag Chamber Assembly
As discussed in the introduction I have also added the safety feature of air bags to the car which burst open during crash to safe the passengers. So it’s under stood that its not literally possible to open the valve at the same time of impact to mimic the effect of air bag. So in order to solve this I used a solenoid valve at one end of the chamber. This chamber is supposed to be kept outside the car (which is not the case in real life scenario) and we use flexible tubes to drive the pressure to the car air bags. This chamber is relatively small which consist of a 1 inch valve at the back followed by a 18cm 1 inch PVC pipe then a 1 inch PVC end cap. Before fixing the end cap some alteration should be made on it. Drill a hole on the end cap such that the solenoid valve inlet port fits tightly in place. Use plumber’s tape at the end of the inlet port of the solenoid valve to create a perfect seal. Please be careful not to confuse between the inlet and outlet port since some valves works properly only in one direction. In most of the cases It will be clearly inscribed on the valve itself. Now the 1 inch valve, pipe and the end cap fitted with the solenoid valve could be fitted permanently with PVC solvent. I also fixed the joints firmly to the end cap using hardening epoxy resin which would also helps further to make a perfect leak proof seal. Here at the back the 1 inch valve could be used to fill the mixture. While the solenoid valve could release the pressure upon giving a power supply. One thing to be noted is that before making the final air bag chamber I have tried it with a water purifier solenoid valve which works on 12v supply. But unfortunately it couldn’t handle the pressure and was not working properly so it left me with no choice that to use a much more pressure rated valve. This creates another problem that most of the higher rated valves are fed from AC mains supply. So I decided to trigger the valve with a signal 9v DC supply through a mechanical relay to the solenoid valve. to make its more safer to work with.
Filling up the chamber
Filling the air bag chamber is little bit different from filling the bigger chamber. A main disadvantage while using this technique to inflate the air bag is that the liquid mixture could enter the air bag and creates an undesirable effect during the inflation of air bag. So to drive only the CO2 only small quantity of vinegar is added in the chamber rather than filling it up. To be precise I only mixed around 25ml of vinegar with one teaspoon of baking soda. This could make a good pressure CO2 in the chamber which when opened by the solenoid valve leads to a sudden blow of CO2 and then totally stopped. No liquid was passed to the air bag and it was simply perfect.
Air bag construction,inflation & deflation
An air bag can’t be just an inflating balloon. Once it’s inflated and absorbed the impact from the passengers, it quickly deflates for the passengers to escape from vehicle easily. So it will be imperfect if I don’t add this facility to my project. On thinking about it for some time I found that the technique was within the part which I thought of using for this project. The flexible tube which I mentioned earlier, was supposed to carry this pressurized air to the air bag. This flexible tubing was actually used with water purifier. Since we can’t use a single closed pipe to run the full length due to the complexity in running the pipe inside the car I used joints in between. On a close examination of each joints I found that around its periphery it consist of a special locking mechanism for the tube. This mechanism provides a small clearance between the joint and the connected pipe which could depressurize the air bag before inflation. but lots of clearance could let the pressure escapes first through these clearances. So I sealed every clearence but left one intact, It is explained in detail in the air bag tubing section
Step 4: Air Bag & Tubing Arrangement
The tubes and fitting (joints) are actually used in water purifiers but it works fine in our arrangement. The tubes are around 2.5mm in diameter and could be bought from a nearby water purifier store. In order to achieve the correct shape to match with the profile of the car several pieces of pipe are heated and bended to achieve the required dimensions. While heating make sure that you insert an electrical wire which fits perfectly inside the tube before heating. This helps to maintain the internal dimensions unchanged while Appling stresses on the tube. Another thing to be noted is that I have mentioned about sealing the pipe joints perfectly but never explained how. Here it is I use this technique a lot in my experiments if air tight is a necessity. So first expose the place which is to be sealed. Since from the pack which I bought a small cap like structure was there and can be inserted in the joining section. This helps in holding the tubes firmly. I believe this is common for any water purifier tubing fittings. Ok back to sealing, after exposing the section put some talc powder on the seal and gently press it and compact it. After doing it apply some super glue on it and leave it for 5 minutes to perfectly harden. The result is a perfect seal without any leakage. The tube layout is as follows.
Let’s start explaining from the inside of the car. As you could see in the picture of the piping, a T joint is necessary to split the single pressure carrying tube to fed into the two air bag used in the 2 front seats. From the two split ends in the tube two smaller pipe arises which is hold in position with two L clamps which is bolted to the base of the car. At the end of the tube we will fix the air bag module. One thing to be noted is that while fixing this two segments make sure that it positioned in front of the passenger at a convenient clearance. The remaining last opening of the T joint is connected to a 90 degree bent downwards. A hole is provided at the base of the car to run this tube downwards. Which then is connected to a 90 degree bent (not heat bended, the factory made one) this 90 degree bent is very important for running the pipe line. It serves two main functions the upper portion of the bent which holds the downward heated bent acts like a pivot to the pipe. Since the car is moving forward and the pressure chamber for the car is stationary a resultant side force is acted on the car due to the strain in the pipe while the car is moving. Since the joint act like a pivot at the upper end it rotates and thus there is no side force acting. I’m struggling to explain the above mentioned idea in words I think you’ll get to know about while building if not do ask me in the comment section. OK the second main function of this joint is that it is the only place where we keep the clearance that we mentioned earlier. Note that only the upper portion of this joint is not sealed the bottom portion is sealed. From this joint a long tube can be connected directly to the air bag pressure chamber.
The air bags
The two air bags are made from the thumb finger section of a rubber gloves. Please make sure that you take a thin gloves for the purpose since we are supposed to be inflating it during impact and folding and tightly packing it during ideal time. As I mentioned earlier the air bag tubing and its connecting parts like 90 degree bent T section 90 degree joiners are all necessary for this project because we are not able to predict certain areas where which joints would come into play. After cutting the two thumbs from the gloves attach it on a head like structure. In my case it’s the joining head from another bent section. The advantage of using factory made joints is that we won’t be worrying about to fix the pipe to it. Since the head which is also a pipe obviously the pipe extending through the L clamp could inside it properly.
Step 5: Building the Test Car
The model of the car which I used is a scaled down version of BMW 328i. This is one of the area where more patience is needed to get the required result. However I was a bit fast since I tried to overdo some extra features on the car and really messed up the templates and was forced to redo the whole thing for 3 times and finally got it right on my fourth time. The car is constructed by printing out the layout in an inkjet printer and in a photo paper. The reason for inkjet rather than laser is that it is more preferable in colour contrast on photo paper in my opinion. The reason for photo paper is that it gives the necessary stiffness to the frame of the car. But the great disadvantage in using photo paper is that it is not that easy to fold along the correct marking provided in the layout also since its more thicker than the normal A4 paper the white edges are more visible and this adds up the task to colour the edges with permanent markers of suitable colour. Explaining on how to stick the templates would length up to pages so I’ll put a link to a video tutorial which I used to build it. It’s around an hour length and have every details on using the template.
Note: in the tutorial each templates is print in an A4 size paper. Printing each section fully in a fully paper would give a much larger version of the car which I believe spans a length of 38 cm. Which is too big for our project. So what I have done is I printed two pages per A4 size photo paper. By using the default printing option I.e. 2 pages per paper we could get the exactly scales for all the templates. So this template when folded and glued would give the exact half size of that seen in the tutorial.
The thing that are modified from the actual model of the car is the plywood base and the individual rolling tyres. First we start which the base. Since we are driving the car with external power pressure a strong but light weight material should be used. So the cheapest things to get are acrylic sheet and plywood. Thought the acrylic sheet is very light weight (I’m talking about 2mm sheet) it may crack while working on it and is a potential vulnerable material. So using plywood is better in my opinion but too think section could also damage while tightening the bolts at various positions. So I used a 6mm plywood sheet and to reduce the weight I reduced the width lesser than the width of the model car. In the templates the bottom section is available, what I have done is printed it on a normal A4 size paper and measured its length and then used a lesser convenient length for the plywood. While fixing the length make sure that the bottom plate extends to a length that it could support all the 4 wheels. My bottom plate was about 6.8cm width and 18cm length. Don’t take the lengths blindly use a length convenient to you.
Step 6: Car Templates
here are the templates which I have used. I thought it to add it in a separate title to reduce confusion with other pics.
Step 7: The Tyres
The tyres are the thing which put me to a stop while building. The reason for it was that maintaining proper circular symmetry and placing the Tyre shaft at the exact center of the Tyre and finally matching the diameter of my custom Tyre to that of the template was very difficult. Since we are building the model car with the templates matching the diameter to that of template is very important since it effect the aesthetic look of the car. So in order to tackle all these problems I found out a solution. The close thing which is exactly circular and has a perfect hole in the middle is nothing but a washer. The only problem is that is not thick to work as a Tyre. So fixing a bolt through the washer with a nut could give us a circle base to work on and a shaft at the perfect circle. So in order to achieve the thickness I inserted a washer into a bolt up to the head put two nut as spacers and tighten it against the washer then placed another washer through the bolt and secured that with another nut. The washer which I used has an approximate diameter of 2.8 cm bolt length is around 3.5cm and nut width is around 2mm. This made a sufficient space between the two washer which could match with the tyre thickness of the model car. The next thing to do is filling the space between the washer with a hardening epoxy resin. I used the brand called M seal to fill the space. After leaving it to cure for about 2 hours I then rolled 2 turns of rubber gasket over it. These gasket are actually used to seal room windows and doors and is very cheap and could get it online also. This finally matched the diameter of the tyre in the template. For the finishing touch I took the outer and inner rim of the tyre template and pasted it on the tyre with strong glue after gluing the disc brake template at the inside alingning the bolt head. Thus the bolt head is concealed. The alloys are also pasted on the inside rim. Follow these just as in the tutorial.
Here is the link https://www.youtube.com/watch?v=qI5WXuyWUeE
Step 8: The Piston, Rod and Attachment
We have discussed the generation of pressure inside the main pressure chamber which we could use to move the car against the crash wall. In order to achieve this the pressure should be transferred to a piston and then into the car. Also the mechanism to move the car should not be visible, so somehow the car should be moved from beneath the platform by providing slits in the platform and then attaching the driving system to the bottom plate of the car.
While thinking about something which I already have it brought my attention to my hole saw set. I found an appropriate one for my 1 inch pipe. Since the internal diameter varies according to the pipe the size of the hole saw should also be changed. The next thing that we want is the shaft which I brought from a local electric motor parts dealer shop. It should have a minimum length of the 1 inch pipe which we used at the front as the barrel.
Make sure that you buy a shaft with thread at both ends or at least at one end. This thread helps to fix the further attachment at the ends. One end of the shaft is fixed inside the shaft of the hole saw drill and tightened with an Allen key of appropriate size. The other end is attached to an L clamp with the help of nut and washers of appropriate size. In order for the car to be moving in perfectly straight line two nuts are used to secure the car from beneath. Two long nuts of approximately 8cm length are fist fixed at the bottom plate of the car and then can be attached to the L clamp.
Step 9: Building the Seat & Seat Belt
So in order for the proper test scenario we would also need two front seats for the crash test dummies. The front doors are removed or cut apart to accommodate the seat arrangement.and this also allows a much detail picture of whats happening inside during the impact which would not been possible if only the glass portion of the door is visible. The crash test dummies are my childhood GI joe toys which could easily mimic a crash test dummies however to accommodate the full toy I was forced to unscrew then leg part for easily accommodating the toy in the seat. The seat are made with very little effort. The backbone of the seat is a L clamp. This clamp is then coated with cloth adhesive and small piece of cloth according to the length of the toy was cut and pasted over the clamp. I said cloth right..?? actually is a black speaker math which I have a lot in my home so I moved on with using it. Also it provide a leathery touch to the seat and helps to create a more appealing look. For the seat belt, I cut out some thin strips of white cloth since the seat is black white would be better to get better visibility during the final test. This white strips of cloth is then glued in position at the back side of the seat itself using super glue. The seats are finally fixed at the base with some glue but its done just before the real crash test. The reason for this is that we would be frequently touching the inside of the car for lots of adjustments and the seat would make it really tough.
Step 10: The Relay and Trip Wire
The aim of using this arrangement of relay and trip wire is due to operate the air bag at the time of impact. One method is to use a proximity sensor at the front of the car so that when the wall comes closer it triggers the valve. But further thinking I thought why to make it simple since we would sure damage the sensor at each time of impact. So the better way is that to set a trip wire. And attaching the trip wire at the rear bottom portion of the car so that when the car moves forward It could engage the trip wire and fires the air bag. After drilling a hole at the required position at the rear of the car I inserted a bolt and fixed it with a nut this bolt is set in such a way that it protrudes towars the ground so that a fish hook wire could be attached at its back and used as a trip wire.
So we said about the relay.. right?? A 9v battery is connected to the coil of the relay, also a diode 1N4007 general purpose diode is soldered in reverse parallel configuration. If you are an electronic hobbyist your wont be having a doubt regarding the diode. For others, the diode is placed to avoid inductive sparking during the turn of of the coil. So its a good design practice to use the so called fly back diode. The trip switch is nothing but a cloth clip whose both eds are fixed with a metal strip in my case its a nickel ribbon but any conductor would do. A small piece of plastic sheet could easily block the current between these two conductor plates. This plastic sheet is then tied to a string in my case, its a fish hook wire. the other end of the fish hook wire is then attached to the back side of the car so that length of the wire is set in such a way that when the bonnet of the car hits the crash block the wire should be disconnected from the trip switch i.e. from the clip and thus connects the relay which in turn switches on the solenoid valve and inflates the air bag
The relay and 9V battery is hot glued on a small plywood piece, which could be later zip tagged to the final platform.
As I mentioned early I’m using a solenoidal valve that runs on 230v AC . So I could have directly used a clip to trigger directly the valve itself and why a relay.?? The reason is safety since for this experiment in which we are in close contact with liquid I mean vinegar any presence of it is dangerous and the relay prevents it to a great extent. Also first make sure that the relay is properly wired by using a 12v or 9v supply on both ends. Once it is perfectly fine we could proceed with the AC voltage.
I’m attaching a circuit diagram for the relay circuit in this discussion.
Step 11: The Test Platform
The test
platform is a plywood sheet of 6mm thick 50cm width & 120cm length. Using plywood below 6mm may deform from its straightness when we load all the components on it. Starting with the plywood the first thing to do cut the space for the two valves of the main chamber i.e. the 2 inch valve at the back and 1 inch valve at the front. When the final platform is completed all the components should go at the bottom of the platform and sufficient space is provided at the bottom by supporting the four sides of the platform with stacks of books. So the main pressure chamber is fixed at the bottom of the platform by using some PVC clamps. 2 clamps of 2 inch and another 2 of 1 inch. The clamps are very important for the test it’s actually this clamps which determines the path of the car. The clamps are fixed in such a way that once we have connected the car to the piston then the car should move in a straight path meaning that the main chamber should be straight aligned .Another thing to note is that though the tyres freely roll during the forward movement of the car it could also get stuck if the piston is not straight due to the development of a side force on the car thus creating greater friction to the tyres.
There is no need to fix the air bag chamber on to the board since its position is not important to the motion of the car. Since we attach a flexible pipe from the solenoid valve outlet to the air bag tubing inlet of the car the pipe could adjust according to the motion of the car. While fixing the main chamber. Since the PVC clamp does not complete fully around the pipe we can’t attach it directly on the platform so I used some plywood pieces on the sides of the PVC tube to create a raised support the PVC clam. The same thing is done with the 1 inch pipe section also.
After fixing the pipe section we could cut the slit at the after the 1 inch pipe. This slit enables us to connect the car base (plywood base as mentioned in previous section) to the L clamp at the end of the piston and thus we could transfer the force from the chamber to the piston and then into the car. After cutting the slit turn the platform to the other side. This side is the top side where the car crash test is conducted. After the slit the next thing to do is to attach the side panels. The side panels are just plywood section cut according to the test area. The test area is the region which includes the path of the car and the crash block i.e. the area where we focuses on our attention and video.
The facing side of the side panels are covered with white chart paper. This gives us a good colour contrast between the red car and the background. The platform in the test area is also covered with white chart paper and cut necessary cuts are provided at the slits on the platform.
Finally attach the relay trip wire to the platform either fixing with bolts or with a zip tag.
The final test platform also contain a crash block for which I simply covered a thick book and with a form sheet. using paper is more than enough but there should be some proper color contrast between the car, background and the test block. So use a different but suitable. Since the car is in red in color I used a white chart for a white background whereas the test block should stood a little apart from the background so used a form that is cream in color, which is light but different from white but less darker than red thus creating a color difference which gives the car more importance then the test block in white background while filming the crash test.
Step 12: The Final Test
So its time to do the awaited test after all these works. before the final testing make sure that all the components are working safely. The main pressure chamber, the air bag chamber and the relay & trip wire. One thing to note is that while dealing with these pressure always keep a limit to what you are doing. adding too much of vinegar and baking soda to create more pressure is unnecessary and dangerous. While I was doing some trials with the main pressure chamber the back 2 inch valve was experiencing some leaks because these valves are not meant to deal with this pressure and I also admit that the valves are not of superior standard and was suppose to meant only for water pipe line. The thing is that the valves don't burst out in this pressure but at the contact section of the valve and the pipe there will be a rubber type gasket and it is this gasket which creates the problem. later on I used some epoxy compound to fix this and the problem was solved but still its a potential weak point. On the other hand in the air bag chamber pressure should not be kept too high and thus helps to prevent unexpected leaks.
The final preparation is just like in the video shown. load the main pressure chamber with 3 cups of vinegar and 3 teaspoons of baking soda and quickly close the valve. then fix it in place with PVC clamps using bolts & nuts as mentioned previously. insert the piston in position, then fix turn on the battery of the relay but do not switch on the AC main supply. we'll do this at the last to be on safe side. Turn the platform upside down and fix the side walls in position with L clamps. fix the car to the piston beneath using bolts and nuts. Load the air bag chamber with 25ml vinegar and 1 teaspoon of baking soda and quickly close the valve. connect the tubing to the bottom air bag joint at the base of the car. Also connect the plastic sheet (which is attached to the car using trip wire) to the trip switch. Now turn on the AC main power. make sure you turn on the cam for recording. I used a cams to shoot this entire experiment out of which one is a 21 MP phone cam which is positioned at top of the crash block with an adjustable lazy phone stand and the final and the main cam is a DSLR positioned on the other side and recording at 50fps. to brief it shortly the higher the frames the more you can work on slow motion during editing. unfortunately the 50fps is a very low rate to produce a decent slow motion anyway but it was my only option. If you have the latest iPhone then I think it could record above 100fps and could give a much higher detail during slow motion editing.
Now the only thing to do is to open the 1 inch valve and the let the pressure take over the car. After each experiment with air bags make sure that the AC main supply is turned off even before you touch the platform because unexpected leaks may make the platform electrified and shock you. Repeat the experiment to get a satisfactory result. So that it guys thank you for being so patient to read up to this and I hope you like it. Also help me with your valuable suggestions and comments in the comment section below. Thank you...
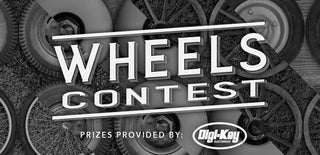
Participated in the
Wheels Contest 2017
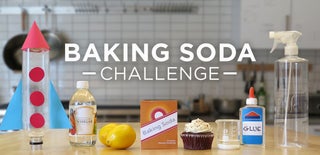
Participated in the
Baking Soda Challenge 2017