Introduction: Scrap Steel to Orange Peeler.
It has been a long time since I visited instructables, between growing up, getting jobs and learning some of life's painful lessons I have finally found this site again.
I was actually looking for information on engraving stainless steel as I had a need for it and long story short, the google-prompted link was my own instructable I had created several years ago!
Well here I am again, this time, bringing you along with me, on a journey to make an orange peeler out of scrap steel.
Skip the story if you just want to get straight to creating!!
~~STORY~~
I collect steel scraps from projects and try to put them to use - a while ago, I started adding fresh oranges to my work lunch and I found it quite painful to carry a sharp knife in my insulated crib bag as none of my knives have proper pouches and I don't want them cutting up my bag.
I had bought a forge a fair while ago and thought it would be cool to try my hand at metalwork for a change and actually focus on one thing, but I wanted it to be different.
I have always wondered since I was a child, how hard is blacksmithing?
Obviously, unless you're a prodigy or have had access to extensive training and courses, it would be pretty difficult - google searches don't quite cover these types of questions fully so I thought I would try and find out myself.
I have already tried and failed at making a knife (simply because it was my very first thing I tried forging) and I wanted to make something practical that didn't need to be super straight and perfect.
I tried to think of all the things I could make that I would use and I remembered my older brother used to have an orange peeler many years ago when we used tot ravel but it got lost.
When I found instructables from my google search, I thought I would have a peek at the contests and if I could enter any, and that is how I came up with the idea to make another orange peeler from scrap.
(If everyone is interested, I might upload a photo of the original orange peeler I made)
Since I used my orange peeler everyday and and knowing I didn't need 2 peelers, I contacted a friend of mine and a good camping buddy and asked him if he would use an orange peeler and eat more oranges at work and he is super keen to try out the design!
In the end, we both now have orange peelers and I plan on revisiting this project when I learn how to properly work with metal, and who knows - I might even do something fancy next time!!
Step 1: MATERIALS I USED:
So, if you are going to try this yourself, I assume you already have a forge, know basic metal working and use safe practices.
This image is a representation of the finished peeler, I am not very good with a pencil and paper so I tried to design it on the computer... I'm not very good at that either lol...
Anyhow, the flat part is the handle, it also doubles as the peeler.
The long skinny piece is the cutter - I tried to recreate the blade with the curve in the image.
The rough size overall is 6" long, 3/4" wide and about .16" thick at the handle.
I am not responsible for any injuries or damage to person or property if you follow this guide.
- You will need a forge.
- Gloves
- Tongs
- Metal
- Files
- Time
- Sandpaper (or angle grinder)
- Hacksaw
- Dremel - I used the sanding attachment and also a diamond burr.
- Anvil (Or other solid, stable piece of steel)
- A pinch of common sense (more than I have...)
Step 2: Cut Your Metal to Size.
First thing I would suggest is to find a piece of metal which you are familiar with, this bar was much longer and I have been cutting it down project by project so I am confident working with it.
Ideally, your metal should be roughly the correct amount needed for this project - I used a small square piece of 1/4" flat bar - about 1.5" square.
Begin by either taking an angle grinder and cutting down your stock piece to an appropriate size and put it in the furnace until it is soft enough to work - in my furnace, the metal glows the same colour as the walls when I find it easiest to work but different metals have different working temperatures so be sure to check what yours is.
I used an axe to split off a piece of metal from the main stock while it was cherry red by pressing it through incrementally.
Step 3: Drawing Out the Main Shape.
Firstly, I apologize for the lack of progress photos in this step, I was working alone and it was difficult to get any photos.
You will need to draw out the initial shape from the piece of stock metal you choose.
Begin by beating out a long rounded (or square) section about 4.5" long, 1/4" wide on one end.
Leave the other end about 4 times the size of the shaft, we will flatten this in a while.
Use the square end as a sturdy place to grip your tongs onto for the moment and continue heating and beating your metal until the shape is similar to that shown in the photo.
We will be cutting this down to our finished size later so don't worry if you make either end too long.
Step 4: Flattening the Grip
When you have finished hammering the rounded end and drawing it out to about 4.5" long, you need to turn your piece around and start heating and beating out the handle part.
You will want to try and beat out the handle in a sideways manner, trying to not make the handle too long or thin, but rather just make it wider.
This step is difficult to get perfect so it is wisest to start with slightly more steel than you anticipate and cut the excess off later.
The ideal dimensions of the grip depends on the size of your hand, I made this one about 3/4" wide and about .16" thick.
I beat out my handle slightly longer than needed, I planned to cut it down shortly.
Step 5: Bending the Hook
Once you are happy with the size and shape of your handle, turn it around and place the rounded end back into the forge.
Grab yourself a pair of pliers you trust and prepare to bend the shaft back onto itself completely as shown in the photos.
This bend will provide a hook for the peeler.
The length of the part you bend depends on the size of your hand but for me, 3" works well.
You will need the metal to be red hot and you should be able to bend it with ease as it will be very soft.
Take care to ensure the steel is bent back onto itself straight and not askew.
Place back into the forge until the metal is back up to working temperature and then hammer down the end closing up the gap - as shown in the pictures.
It is up to you on which side you make this bend, I bent mine with the handle flat on the anvil so the peeler sits flat in the palm of your hand while peeling.
If you prefer to hold the peeler on edge while peeling, you can bend the hook to either edge.
This is all personal preference.
Step 6: Adjustments
Before you cool down your forge, you will want to make sure that your peeler is straight, flat and the surface of the handle does not have too many inclusions.
The rougher the peeler is in this stage, the more sanding you will need to do later if you want a mirror polished finish.
I like to keep some texture on the handle of the peeler, it gets slippery when the orange juice gets on it and trust me, once you find out how easy the oranges are to peel - you will probably want a second and possibly third :)
When you are happy with the final shape of your peeler, you can shut off your forge and cool down the peeler.
Because this is not a knife and it does not need to be extremely strong for any purpose other than breaking the skin of an orange, you can just dunk it in a bucket of water and swirl it around until it is completely cold.
If you have access to a quench tank and know how to properly quench steel, it is probably best to properly quench the peeler out of habit.
Step 7: Trim the Ends
Once the peeler has cooled down, you will need to trim off the excess steel from both ends.
The length of your peeler should be around 6" long on average - 3" for the neck/hook and 3" for the handle/peeler.
Take an angle grinder or hacksaw and proceed to trim the ends down like shown in the photos.
Feel free to refer to the diagrams in the beginning of this instructable if you are confused at all.
From here, we will make sure the peeler is roughly as shown in the diagrams and then move onto cutting the blade and tapering the handle.
It is ok not to follow the shape fully - it is a guide only.
Step 8: Shaping the Blade!
Cutting the shape of the blade is fairly easy, you can use a variety of tools, I used hand files and a Dremel.
I find it difficult how to explain in words how to cut the shape of the blade in, the pictures show the finished result and what tool got me to that step - I'll try and explain it but forgive me if it is confusing... lol...
The part you bent will be the blade, we will call it the head though, because the blade is only part of it.
Take the peeler and put the head in a vice or clamp of sorts, on an angle similar to that shown in the photo.
File (or grind) the tip of the head until it is flat like shown in the second photo.
Do the same on the other side so that looking at the head from top down, it looks like a diamond kite.
Refer to the photos as you work to make sure you are on the right track :)
Next, file or grind the handle so it is smoother and make sure you remove any flakes from forging otherwise rust will grow in those places quickly.
Take a wire brush or a sander of sorts and clean up the handle a bit once you removed some of the dents/hammer marks with the file/grinder.
When you file the handle, try and put an angle to one side of it - do not make it sharp, but make it a wedge shape so you can use it to remove the skin after it is cut.
I filed mine until I was happy with how smooth it was and then touched the rest of the peeler up with the sanding bit on the Dremel.
Step 9: Cutting the Blade.
Take either a very fine round file or a diamond Dremel bit and clamp the head of the peeler again in a vice.
Carefully make a rounded cut into the head and create a crescent shaped blade as shown in the photos - I apologize for the lack of action photos, they all turned out really blurry with the magnifying glass light I was using.
Cut both sides together, make a small cut on one side and then flip the peeler and cut the other side, this way you will be able to keep the blade straight and make sure your cuts are even and on the same angle.
When your blade is cut, you are basically finished!
Feel free to continue sanding, shaping, engraving, polishing or whatever you so choose after this step - I went over mine with a piece of sandpaper to give it a nicer look in the photos and because it was a gift for a friend - the one I use daily is the same color this one started out as...
Step 10: How to Actually Use the Peeler :)
If you made it this far and actually made yourself a peeler, good on you!!
If you are curious as to how this works, hopefully the photos will explain it.
- Take the peeler by the handle in one hand and an orange in the other.
- Insert the tip of the blade into the top of the orange and proceed to draw it along the length of the orange, cutting through the skin.
- Do this on 4 sides of the orange (you can do more than 4) to divide the skin into sections.
- Flip the peeler around and hold onto the neck and handle and insert the end of the handle under the top of one of the skin sections.
- Proceed to use your thumb and the handle to grip and pull off each section of the skin.
- Divide the orange if you so choose, by wedging the handle between segments and levering the orange apart.
- Enjoy your fresh orange!!!
- Clean your peeler after every use the same way you would clean utensils or cutlery.
Thankyou for checking this instructable out, I hope it inspires you to try it out!!!
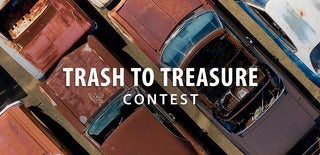
Participated in the
Trash to Treasure Contest