Introduction: Seafoam Kayak, the Unsinkable Foam Kayak Anyone Can Build, 16 Pounds and Eight Feet of Fun
can you cut a crusty bagel with a knife, stick a sandwich together with mayo, grate cheese, cut thin fabric with scissors, stretch wrinkles out of bed sheets, and roll paint onto a wall? Then you can build this boat!
I've built seven small kayaks over the years, all have been from the design type called a mouseboat. The mouseboat is a free plan offered by Gavin Atkin, variations on the design have been drawn by others, and are also offered on the Mouseboats yahoo group page.
my first seven mice were built of plywood and glue, either polyurethane construction adhesive, or marine epoxy and fiberglass tape. The mouse is a great little boat for a beginer, your whole investment in the project comes out to roughly $100 US to have a finished boat that will be the envy of those on the shore. Just about every time I go out in them, at least one person wants to know where to get one.
for more information on the mouseboat check out the Mouseboats facebook page.
I've built a couple teardrop trailers, the first was built of plywood and used the same process I knew to use from my first couple mouseboats. The second is built of XPS foam. I wanted to learn how to build with foam on a much smaller, simpler project than a full size camper. Since a mouseboat costs roughly a hundred dollars, and a teardrop costs a few thousand, another mouseboat was the best answer to learning without wasting a ton of money.
The winter after I built Seafoam, I decided to make a bigger, more capable kayak out of foam also. The result of that experiment was Sawfish my 12 foot 23 pound kayak, a much more capable boat. I've taken it out on the North Atlantic Ocean, on the coast of Maine, and ridden in some rather rough surf with no issues.
As soon as I finished with Sawfish, I jumped right into the foam teardrop, with the experience I gained from the foam boats, I was able to finish enough of Mercury for a great camping trip in the Adirondack mountains. This spring I plan on constructing the removable second story, and finishing a bunch of details on the doors and windows.
Step 1: Collecting
I got the plan for the mouseboat from the yahoo group "mouseboats". Some people have a problem getting the files there though as they come as a zip file and must be opened once downloaded. To make it easier, I converted the best mouse designs, IMO, to JPG files in an album on my facebook page here mouseboat plans if they are not clear enough ask me, I might be able to clarify details for you. There are a few different plans, the best and fastest boat will be the original mouse.
I added the original mouseboat plan to the photo gallery at the top, and another called the fisherman's mouseboat, as it is wider for more stability. the designer figured it was wide enough to stand an cast from. for those who weigh over 200 lbs, the fishing mouseboat will handle the weight better. It takes two 4x8 sheets of foam instead of one and a half like the original mouseboat.
to build one boat you will need:
- three sheets of 2'x8' 1" XPS foam, I prefer the Owens Corning pink foam from Home Depot as it is softer and easier to shape. The green foam at Lowe's is very tough, The blue seems as soft as the pink.
-two cans of Great Stuff (GS) expanding crack sealer, (the basic stuff is fine)
-old bed sheets, the thicker they are, the stronger and more resistant to punctures (the more synthetic in the fabric the harder to get glue to bond to it, and the harder to get paint into the fibers) asking around at hospitals, nursing homes, or hotel laundries may get you some free, torn or stained sheets. thrift stores should have plenty, stretchy fabric will be harder to keep wrinkles out.
-coarse thread drywall screws 2" long or more (I can't imagine needing more than 20 of them) some people use bamboo skewers instead
-a gallon jug of titebond II (TBII)
-1 gallon exterior house paint, check the oops paint rack in the paint department every time you visit, they might have the color you want for a much cheaper price.
-two gama seal bucket lids (the paint department of Home depot stocks them in black around here. I found them in white at a lowe's for a little over $7. in six colors on Amazon
- 2" or wider. duct tape, masking tape etc.
-a tube or two of PLpremium construction adhesive, (PLp) the 3x is best and cheaper. you can just buy gorilla glue instead
- gorilla glue (GG) get the 8 oz bottle minimum
-1" strips of 1/4" plywood, cheap wooden yard sticks, etc. you need a bit over eight feet of them though. (every time you visit the paint department ask for a 5 gallon paint bucket stirring stick or two, in a few visits you will have enough to make these anti-dent rails)
-a few feet of nylon webbing 3/4" to 1" wide, for making handles (I use the ends of shortened nylon tie down straps, cut them by melting with a heated knife to stop fraying) nylon straps
-about a foot of PEX plastic plumbing, or PVC tubing, for making the handles much more comfortable
tools:
-gloves! I find disposable vinyl gloves work best for this project as they will not stick your fingers together with titebond II, instead the glue will just peel off unlike latex or nitrile.
-safety glasses
-dust mask
-werner 250 wallpaper perforation tool
-hand drywall saw http://www.harborfreight.com/6-inch-double-edged-...
-sureform the harbor freight model works best for this, and is easier to hold
-flush cut pliers if you use the bamboo skewers
-screwdriver if you use drywall screws
-paint roller handle, tray and rollers I prefer a three or four inch roller, I buy the full length rollers and cut them to fit the shorter roller handle.
-a small paint brush
-tape measure, yard stick, etc.
-10 foot long 3/4" pvc pipe
-carpenters pencil, sharpie marker, ink pen
-chalk line for easy straight lines
-mixing board for folding great stuff, this one is the best as you can bend it to remove cured glue
-caulking gun for the PLpremium
-scissors
-bricks, paint cans, stacks of books etc. something heavy enough to hold the PVC pipe bend in place
Step 2: A Pile of Parts
start by copying the lines on the paper plan onto the foam, this step is important, a wrong line here could cause a lopsided boat later on, this is where you really must "measure twice, cut once".
I use a 10 foot length of 3/4" PVC pipe to mark my curved lines. I use bricks to hold the pipe in place then trace the shape.
Once the panels have been marked out, only cut out the side panels (you did label them as you drew them, right?) you will notice the instructions say to only cut out one side panel, take this panel, flip it over to the other side and trace it on the other sheet of foam to get the second side. make sure you put the marked up side against the marked up side for all sanding and tracing operations.
clamp the side panels together, I used drywall screws, then use the sureform to even out the lumps and bumps until both panel edges are even.
measure out and trace the bulkheads (make sure you clearly mark the center line of each bulkhead from top to bottom) so that you have all four as shown in the plans. since the mouse plan is drawn for a sheet of 1/4" plywood and we are working with 1" foam, you will need to cut an inch off each end of the bulkheads, bow, and stern. Otherwise your bottom panels won't be wide enough.
If you do goof and make a panel the wrong shape, the easy fix is to glue the cut back together with GG, then cut to the correct shape. Always save your waste sections until the hull is 3D. Once the boat is coated, sheathed and painted no one should be able to see the goofed section.
Draw the two bulkheads and cut them as shown in the drawing in the gallery. save the rest of the sheet for decks.
Step 3: Going 3D
this is the exciting step, in a very short time the boat takes its shape.
take your two side panels, unclamp them, put them on the ground or sawhorses if you don't want sore knees. Make sure the bow end of each is facing the same direction, and the marked up sides face in toward each other.
take your bulkheads and line them up with the bulkhead station lines you made on the sidewalls, align the top edges so they are all even (they will line up on the bottom as you are building upside down) use two long drywall screws to anchor each bulkhead. Once again you are dealing with 1" foam so put your bulkheads forward of the mark at the forward bulkhead, and aft of the mark at the aft bulkhead.
Now draw the ends in and screw them into the bow and stern bulkheads, you will find this easier to do if you profile the ends of the bulkheads to match the curve of the sidewalls. I used duct tape to hold every thing together at the corners.
Once again the 1" foam causes another problem, when we shortened the bulkheads we didn't recut them to the new end dimensions (notice the gap under the sureform), it will help if you mark where the two panels meet at the bottom edge, then draw a new line from there to the point of the V on the center line, then cut the bulkhead to the new dimension.
I used the sureform to taper the bottom edge of the foam sidewalls to match the angle the bottom will meet them, you can wait to do this until you have the bottom ready to go on.
Step 4: Now It All Gets Messy
(wear clothes you don't care about ruining for this step, and wear gloves, I'm a mechanic for a living, so if I walk around with black patches on my hands nobody is surprised, other lines of work this could be a problem, once the glue cures onto your skin, it won't come off easily)
Great Stuff (GS) is an expanding foam sealer sold at home centers as a quick and easy way to stop air leaks into your home. It is not water proof, it will soak up tons of water and hold it, but since I'm not using it to fill a void it will work for what I want, filling gaps up to one inch (advertised on the can) and gluing the foam panels together. We don't want the expanding properties though, so we need to knock the foam down.
Start by spraying the foam onto the metal mixing board, take a plastic bondo spreader and "fold" the foam back on itself. Each time you fold it, some of the air will come out, the foam will change from fluffy, to marshmallow fluff, to mayonase like, and even mustard. the last two stages are the ones to work with, depending on how large of a gap you need to fill.
you can clean the metal board with kerosene, or other solvents, or once cured, flex the board and chip the glue off.
On the one inch foam edge, a 1/2 inch bead of mustard like GS was more than enough to fill the gap and ooze out. Once the joint is in place I used coarse thread drywall screws to pin everything together, on joints seeing tension on the screw, I used duct tape to make sure the screws didn't pull out.
Once all the joints were together I went back and scraped out any oozed out glue with the bondo spreader, this saves sanding later.
Step 5: No Glass Bottomed Boat
as you can see from the first picture in this step, once the GS was cured, the screws and tape were removed, and I could balance the frame of the boat on one pinky.
Of all the mice I've built, the restl have had a flat bottom, If you end up building one, don't make a flat bottomed mouse! they are slow.
This was my first V bottomed mouse, and I wanted as tight of a seam for the center of the V as possible. This took a bunch of shaping with the sureform, but I ended up with a seam that was tight. Make sure the frame of the boat is straight, I marked the centerline of each frame before cutting them out. With the boat hull assembled and lying upside down it was easy to see if the centerlines all lined up. Making the bottom panels line up with these center lines helped with making the center seam straight.
shape the bulkheads, bow, stern, and sides to meet the bottom panel now.
I used the duct tape to hold the panels tight together, then used screws to hold the edges of the bottom tight against the frame.
I then used a drywall saw to trim the edges of the bottom panels that were left uncut when I cut out the side panels. leaving a small ledge of extra foam for final trimming. This is the time to check the shape of the bevel where the sides and bottom meet..
Once I was happy with the bevels and the overall fit of the bottom I removed one half of the bottom and glued it on with more GS, using tape and screws to hold it all in place. Then I removed the other half and glued it on. duct tape along the V seam would have keep the GS from foaming so badly on the inside, on the outside extra foaming is fine as it can all be sanded off easily.
Step 6: Taking Off the Rough Edges
After the GS cured, I removed the drywall screws, and used the sureform to remove all the extra foam GS that oozed out of the joints. (I call it the beard)
As an experiment I used gorilla glue (GG) to fill the holes left behind by the screws. this caused problems, GG cures to a tougher consistancy than GS, when I was removing the excess, it tended to come out in one chunk, taking some foam with it. Folded GS cures to a easier to work consistancy. Both glues expand as they cure, keep any joints clamped, weighted, taped, and pinned to keep them from pushing things apart.
Step 7: Rebar
I like to think of this as the rebar stage. If you watch concrete structures being poured, you will notice a grid of metal bars being put in place inside the forms, concrete has little strenght in tension, and massive amounts in compression. The metal rebar in the concrete gives it strength in tension.
As I said before, foam is strong in compression, but weak in tension . Pull on a foam joint and the top layer of the foam will just tear away. Roughing the foam up with the werner 250 adds more depth to the glue bond, but even this is really more to resist peeling, it does very little to give the foam more strength in tension.
Now we add the rebar, in this case, a fabric skin. The skin will take the tension, especailly at the GS joints which are the weakest link in the hull. I actually broke one joint just moving the boat around, some GG brushed into the joint sealed it all back together.
I reinforced the inside seams of the boat with 4 inch wide "tapes" of fabric, glued on with TitebondII (TBII). Since inside the ends won't be exposed to the sun, they were left with bare foam other than the tapes.
The cockpit will see the main stress of the hull, it needs to support the paddler, and will see the most stress from the feet of the paddler as they get in and out. The teardrop site "experts" suggested using "chipboard", large sheets of lightweight cardboard, like you have on the back of a pad of paper. I couldn't find this in any stores near me.
I finally used cardboard from the back of pads of paper (we use many forms at work, I just saved the backs from the forms). As you know cardboard is not waterproof, but with the addition of the "MIX" 1/3 mineral spirits mixed with 2/3 oil based polyurethane floor sealer, the cardboard becomes waterproof. you can make a carboard bucket that will hold water and not fall apart if you treat it with the "MIX". I perforated the cardboard panels with the werner 250, glued them to the floor with TBII. Once the TBII cured I treated the cardboard with the MIX, making it waterproof. Some scuffing of the cardboard surface to give the TBII some tooth, and a layer of fabric covers it all. As long as you don't jump on the floor on the land, it will be strong enough.
The ends of the boat will become air boxes, mostly used to keep the boat on the surface of the water is it is swamped. This is over kill in a boat made of foam, the empty hull itself has enough bouyancy to keep the boat up. I ended up making the end boxes into storage compartments with large hatches.
Step 8: Rails
since the sides of the cockpit are just 1" foam, I knew it wouldn't stand up to much force. tied to the roof of the car the load put on the rails by carrier bars and straps would dent the foam badly, a paddler leaning on the rail could split the side of the boat. To fight this I added plywood rails to the top of each side of the cockpit. GLued on with GG, the rails stiffened the sides of the boat up perfectly. I used left over scraps of plywood from another project, you could also use 5 gallon bucket stir sticks, or cheap wooden yard or meter sticks. My local Home Depot gives the stir sticks free at the paint counter.
Step 9: Decks
One of the great design features of the mouseboat is the sealed air boxes, these give a great safety margin, even full of water the boat will not sink. Since this boat is made of foam, it is already unsinkable. The decks give the hull the strength it needs, and give a secure place for storage.
you will see I tried a different deck and hatch design to start with. My first idea was decks of 1" foam with simple hatches cut in them. the hatches had beveled edges to hold them up, and a fabric hinge.
The first day we tried it, my dad put his elbow through a hatch, cracking it in half. Since he wanted the boat, he also wanted a tougher deck.
I tried plywood decks, but they proved to be heavy. I went back to foam decks, I added triangular blocks of foam, glued to the sides with the wide end of the triangle up to support the deck, then glued the decks on with GS. I added my simple boat handles to each end. I melted a series of holes in each end of the strap, then sandwiched the inner ends between the bottom of the deck, and a foam deck supporting block. The handles are strong enough to hang the boat from, and keep the boat secure on the car roof at highway speeds. boat handles instructable
I added gama seal deck hatches. The gama seal lid is a water and air tight, screw off lid found made by the gama seal company. They are designed to snap onto the top of a standard 5 gallon bucket, making it air and water tight with an easy to remove lid.
By cutting away the outer lip of the snap on ring, removing the O ring, and then trimming the edge flush with the bottom of the groove, I made the bucket lids into deck hatches.
Use the ring to mark the foam, cut the foam to a circle, then trim it to ensure a fairly snug fit.
DO NOT GLUE THE RING IN NOW!!! I did and now will have to figure out how to get the fabric edge tight to the ring.
Step 10: Wrapping the Mummy
In reality we are almost making a skin on frame boat, the foam is the frame, but the real strength is the fabric, without it you have a very fragile box that could come apart at any moment.
I used bedsheet cotton as the skin, thinner than cotton drop cloth that I used in the poor man's fiberglass instructable.
I used the thinner fabric to save weight.
I cut each fabric panel a couple inches wider than each foam panel, this overlap will give each joint more strength. when I was smoothing the hull out, I rounded each corner over, this makes it easier to get the fabric to stick without lifting. Since the sides are all curved due to the shape of the hull, when you glue the edge down to the next panel it will tend to have wrinkles. I found the best way to take care of this, but you won't need to deal with that until we get to the glue stage.
cut all of your fabric panels for the outside of the hull, then lay them aside, in order, from the bottom panels to the top panels. Once the glue is in the roller and pan, you want to do the covering in one shot, I chose to do the top of the decks first, then the sides, bow and stern, and finally cover the bottom panels last.
Step 11: All Hands on Deck!
Now it is time to glue the fabric skin on. This step is where your preplanning will make or break you. Make sure you have all of the fabric cut to shape, and make sure it is laid out in a way that you remember what goes where.
I started with the decks first, the sides, bow and stern, then the bottom. The cockpit was left for last.
Before gluing, make sure all foam surfaces are perforated.
First roll on a thin coat of glue, you can tell you have enough glue, when every pore in the foam caused by perforations, has a dot of glue in it. then work the fabric into the glue with gloved hands, remove any bumps or wrinkles and stretch and smooth the fabric into the glue. Since I put the glue on thin and sticky, the fabric stuck fast quickly, allowing me to go right on to the next panel.
As I showed before, I cut gores into the edges of some panels, then I got lazy and just left the overlaps uncut. when glueing them down, wrinkles would form, I would cut the top of the wrinkle with the razor, then glue both edges down flat. this is much easier and faster, and you don't end up with extra cuts where you don't need them.
I rolled a bit more glue onto the fabric where it would be under a joint, you want these overlaps to be fully glued, they are the real strength of the boat. Otherwise no extra glue is needed.
Once the fabric is glued onto each deck, and the glue has cured, use a razor knife to cut the fabric on the edge of the deck hatch holes. Using PLpremium adhesive, glue the rings into the decks of the boat. screw the lids in, and put weights on them to help them stay seated until the glue is cured.
Step 12: Keeping It Straight
since the mouse is a short wide boat, paddling will tend to make it wander from side to side as you go, or just spin around in circles. A skeg is the answer, a short fin running from about the deepest part of the hull back to the stern.
search through the waste sections of foam until you find a section that will run from the deepest part of the hull center V back to the stern so that is will be as deep at the stern as it is in the middle of the boat. I found a piece that was close enough, with a bit of fitting it worked. However foam is not strong in bending, a skeg sees side loads most of the time, even with a fabric skin, the foam would fail from paddling or hitting rocks or trees.
This became another point for some wood reinforcement, I glued a strip of wood along the top of the skeg, trimming it to fit exactly, and another that runs down the back of the boat and the trailing edge of the skeg. together they keep the skeg from bending. I used more GG to glue them on.
Step 13: SPLASH!
After applying fabric to the inside of the cockpit, I then painted the whole boat with exterior house paint, in my favorite color.
My parents have a small pond behind their house, we were all getting together for the weekend there anyway, so I launched Seafoam, and we all enjoyed the rest of the mice on the pond.
Being a joker, I also brought foam scraps left over from building. after the picture of the boat on one hand (15 lbs!) I had my daughter take another picture of me standing in the lake with the off cuts floating around me. I told the foamies on TnTTT.com, I'd named the boat "titanic", was it the name!? some of them believed me and couldn't figure out what went wrong.
Meanwhile I launched Seafoam, got a picture in the boat, then took her out for a spin. On the water the weight isn't noticed, the V bottom is a bit faster though. After a bit of chasing the kids in their mice, and exploring the stump and rock infested edges of the pond, I began to trust the strength of the hull. I went looking for stuff to run up on, then forced the hull over what ever it was, instead of backing off, or tipping the hull to float off. Then I went back to the shore and checked out the damage.
no tears in the fabric, no scratches in the paint, just some long shallow trenches in the foam surface. The faomies all know small dents like hail damage, or grooves from tree branches are easy to remove from a foamie trailer, just put a thin towel over the damage, and using a steam iron, iron the divots out. TBII and foam are both activated by heat, they swell up, and are put into shape by the iron.
My dad tried the boat out, of course we raced, I had one of my flat bottomed mice, and could just barely pull ahead of him paddling flat out. He has had a couple heart operations, has a few more pounds on me, and isn't a regular paddler like I am. The V bottom is just faster!
That evening I checked back in with the foamies, one of them had finally questioned if that was really parts of the boat floating around. I had a good laugh and shared the pictures of Seafoam afloat.
Step 14: Now That You Want to Build One
Get the plans, since Gavin Atkin is such a nice guy, giving the plans away free, and also giving tons of advice on line for free (though not on foamies) do him a favor, he published a book and that is the only money he gets from the whole deal. Buy a copy and in it you will find plans for a bunch more boats to fire the imagination and get you started. (you can't build just one boat!)
I've already gotten pictures of other foam kayaks, including a mouseboat, in the comments on my Sawfish foam kayak I'ble, from a builder far away.
As far as tweaks to make the mouse better, I ended up adding a rib of foam 1" deep and 1" wide the full length of the center seam. this has helped the boat track much better, it runs back and along the top of the skeg. Such a short boat just needs more to help it go straight.
This past summer Seafoam has been on many trips, including a camping trip in the Adirondacks, where the only access is by boat. The deck hatches come in very handy for this. We each have a bucket or two with our clothes in them, when it is time to launch we just unscrew the deck hatch, stuff as much smaller loose gear into the cargo tank as possible, then drop a bucket in the ring in the deck. We also carried our 5 gallon drinking water jug in a ring the same way. The Gama seal lids are carried in the cockpit for the trip out and back.
As you can see, I still haven't finished putting the fabric inside the cockpit or on the new decks. I will get around to it someday, but I have other projects going on, and this boat does just fine without the skin on the decks.
Step 15: Gearing Up
As soon as you start planning to build a boat, you also need to keep an eye out for the gear to use it safely.
three things are an absolute must:
-a life jacket, while there are many cheap ones, a life jacket meant for paddling is worth the money.
the arm holes will be bigger to avoid chafing, it should have pockets for your whistle, and there should be more areas open for ventilation, as paddling is work that warms you up. Try some on at a walmart or boating store, if the prices or scare you off, or they don't have paddling ones, Amazon and Ebay, even Craigslist are good options.
-a paddle, you can make your own, here are a few different ideas, an inexpensive one, a greenland style, or an eskimo style, there are plenty of DIY paddle plans for free on the web also.
I have a variety, mostly from Amazon.com,because the price was best, but now I find Walmart has then in the fishing and boating department for even less money. For a better selection check out the walmart website with free shipping to your nearest store.
I prefer blades that are brightly colored, as they tend to flash in the sun, increasing your safety on the water through better visibility.
I keep all of my paddles in one paddle quiver bag to protect them and keep them organized.
-a seat. the Oniva seat is the best I've found, I have done many two hour paddles without my seat going numb. every other seat I've tried left me sore and numb. amazon and ebay are the best source for them, unless you live near an ocean state job lots store, they sell them for much less money, without the Oniva name.
a large car wash sponge works best to remove water in the boat.
I always carry my phone in the boat for safety. I also use the here app for data free GPS positioning and maps. GPS trip recorder is another free app I use to track where I've been, as well as time, speed, and distance.
I keep the phone in a phone dry bag that allows me to hear music, and take pictures through it. it will float if dropped into the water.
get a good paddling hat, bring sun glasses, sun screen, bug repellent, bandages (great for blisters), and a waterproof camera on a floating strap.
never forget a water bottle!
share pictures of your mouseboat on the Mouseboats facebook page, church of the double bladed paddle facebook page, duckworks facebook page, and send a picture of the launch to duckworksmagazine.com for the Splash page. Enjoy!
Step 16: Hall of Fame
I may have mentioned that I got the idea of fabric covered foam from the teardrop building site tnttt.com, from a man who goes by the name GPW. I built this boat, and many more foam boats, to figure out the best ways to build my own foam camper. I never expected anyone to want to build a foam mouseboat, so I didn't share much about it for the first year I had it. When I finally made and released the instrucatable I was shocked by the response. I had 33,000 hits in just a few days, and the numbers just keep jumping every day.
Thanks to all of you for your interest, and for the votes that brought this instructable a 1st place win in the hand tools contest!
I was even more surprised by the short time it took for builders to start sending me shots of their foam mouseboats.
-The first one was the yellow and blue one, from a builder in Eastern Europe somewhere, he used 3 cm foam, with plywood for the decks, and my strap and pipe handles. He also sent me a picture of his FOF (fabric on foam) version of a Nick Schade Ganymede, the kayak design he gives away free for adults.
-The second one is the yellow one, all the way from Nigeria. I like how he even copied my original hatch idea.
-The third light blue one, is from Australia. Remember how I got the FOF idea from GPW, well he got it from foam RC air plane flying. The builder in Australia knows GPW from the web, and has flown some of those foam airplanes! He added a foam and wood bracket to the read deck to allow a trolling motor to be clamped on. He included a video of his boat, zipping around with his 30 lb thrust motor. He also showed his own hatch idea, the tops of beer brewing containers.
-Normally I know someone is very interested in building because they start asking serious questions instead of the usual "will it float" type questions that lead me to believe they didn't bother to read the whole thing before announcing that fact to all of us. The white Mouseboat was the fourth foam boat I received pictures of, as far as I know, he didn't ask me anything first, just went ahead and built a great boat! The board across the back is a long board type skateboard. I would love to see a picture of him cruising on his board towing the mouse on the dolly he built!
David Cutts has been working on his foam mouseboat for a few months, his quality of build and detailed paint job make my boats look ugly in comparison. He told me he was interested in using his mouseboat to get close to wildlife for great pictures.
If you share your pictures in the comments below, I would love to share them to show everyone else. If you have a name for your boat, I would love to hear it, and a general idea of what state or country you are in. I know the glues I used are not easy to find in every part of the world, if you found a local product that worked instead, sharing that info will help the next guy find options.
Wow! Five mouseboats built in less than five months! All of you are awesome!
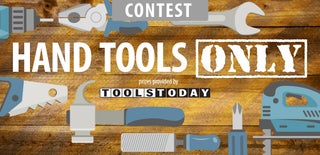
First Prize in the
Hand Tools Only Contest 2016