Introduction: Shop Sign (CNC-cut and LED-backlit)
This is the journey taken to create a shop sign for my woodworking, creative project, etc. hobby. A friend of mine (http://www.rybakwoodworking.com/) had recently bought an X-Carve, and we had a mutual need to put something together on it.
Step 1: Design
With some illustrator and design consultation, I put together a logo in Illustrator (though you could use any software that can make an .svg file) using some inspirations from throughout the internet. I wanted something large, round, with some ornamentation like a vintage product label.
Step 2: Easel
Importing the .SVGs into Inventables' Easel wasn't hard, but there was some learning curve with figuring out where all of my pieces would fit, how to do shallow cuts to guide placement of pieces later, etc. This step took a week or two of fiddling before I even touched an X-Carve. I planned to use MDF for smooth, detailed cuts...which worked OK. That 5+ hours of cut time is legit at this size...and I had several sets of cuts to make (for individual letter pieces, the back piece, and rings to add thickness to the sign).
Step 3: Carve!
This was the gnarliest step by far. The previous step talked about the time spent, this was an all-day affair from Saturday morning to Saturday night.
This was aided by a few beers, though hiccups encountered along the way meant that no beers might've been optimal. As some of the smaller letters were cut out of MDF, one got hooked onto the bit and made a horrifying sound as the several-thousand-RPM piece of MDF made a burn mark on the MDF sheet. Lesson learned...maybe use a laser or something else to cut out finer letters.
Step 4: Sanding and Glue-up
Light sanding was all that was required to take off the machining marks. After I glued-up the rings onto the back piece to add some thickness and space for the LED lighting, it was clear the rings were not the same size as the large rounds (despite being exactly the same size in Illustrator). No matter...that's what belt sanders are for! After I screwed all the large pieces together and employed 5-10 minutes of relatively careful belt-sanding, I had a perfectly round sign. Sweet!
Step 5: Wiring for Lighting
I used an LED strip acquired from amazon and some wiring to set up some lighting behind the acrylic pieces. I added the ring around the perimeter, but this wasn't necessary for my design in retrospect. I used some .007" thick light diffusing film affixed to the front plate to diffuse the LEDs as best I could. There was only about 1" of space between the front/back pieces (two rings of 1/2" MDF added thickness), so I bought the thickest light diffuser film I could easily get. This worked OK, but you can still see some hot-spots. Using a 1/8" translucent white acrylic might've worked better.
Step 6: Fitting Acrylic Pieces
Finishing the acrylic pieces meant a few days of dremel tool carving on my acrylic pieces. To get them to fit in the holes cut into the face piece (MARBISHO LABS), they had to be individually ground down to fit. I killed my POS harbor freight tool, and upgraded to a real variable speed Dremel. This part wasn't hard, but took the most time.
Step 7: Painting
I used spray paint to paint the large pieces (matte dark gray), individual letters and ornamentation (red poppy, blue lagoon), and robot (steel metallic). This was straightforward, and a refreshing change from the recent wood stain projects I had completed.
Step 8: Finishing
I added in the acrylic pieces, which fit snug and only required a small amount of CA glue. In retrospect, CA glue was the wrong choice, as it left a fine cloudiness in the airspace between the acrylic and the light diffuser film. It's not a problem unless the sign is off, then you can see the variably foggy acrylic. Bleh.
Each MDF piece had to be glued individually, using a small weight for each small section.
I was really happy with how the sign turned out overall, and learned a great deal about this new tool (X-Carve).
Leave any questions below, and I'll try to clear things up.
Final Parts List:
- Home Depot
- 1x 1/2" x 4' x 8' MDF sheet
- 1x Rustoleum Aged Metallic Weathered Steel spray paint
- 1x Rustoleum Painter's Touch satin Poppy Red
- 1x Rustoleum Painter's Touch satin Lagoon Blue
- 2x Rustoleum Painter's Touch flat black
- Inventables
- Clear Acrylic Sheet (cast) #23876-19, 1/4" x 8" x 12"
- Fluorescent Green Acrylic Sheet #24141-06, 1/4" x 8" x 12"
- Light Diffuser Film #25049-01, .007" x 12" x 36"
- Amazon
- WenTop Waterproof Led Strip Lights SMD 3528 16.4 Ft (5M) 300leds 60leds/m White Flexible Rope Lighting Tape (amazon)
- SoundOriginal LED Light Strip 12V Inline Toggle Switch Dc power adapter Connector (amazon)
- TMEZON 12 Volt 2 Amp Power Adapter AC to DC 2.1mm X 5.5mm Plug 12v 2a Power Supply Wall Plug Extra Long 8 Foot Cord (amazon)
- Miscellaneous
- 6x 1.75" wood screws
- Titebond III wood glue
- hot glue for wiring
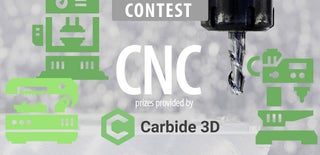
Runner Up in the
CNC Contest 2016
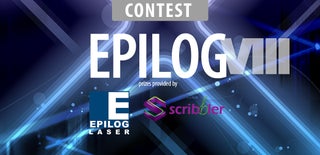
Participated in the
Epilog Contest 8
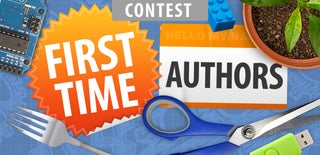
Participated in the
First Time Authors Contest 2016