Introduction: Sofa Reupholstery With Biscuit or Square Tufting
I had to part ways with my old leather sectional, something with sentimental value as a hand-me-down from my mom. I didn't need a new sofa really, just some additional seating in the cave. As a result, it seemed silly to drop a few thousand dollars on a sofa that fits my long-term home design goals (minimalist, mid-century modern, + wood accent), such as a Dunbar. Actually, my search for inspired led to this specific Wormley model 5136.
Why not make one from scratch? I doodled what I wanted on paper, then in SketchUp. Something with straight lines with some subtle angles on the arms, a tight seat and tight back for simplicity and tufting for added visual interest. However, after a few weeks-months of research and doodling, it was clear to me that starting a project like this from scratch was optimistic, requiring techniques and technology that I didn't possess at the time. Additionally, this would be still expensive to some new retail purchases requiring hardwood lumber, springs, and other materials just for the frame.Finally, it’s not quite eco-friendly to create a new sofa out of new materials to emulate a decades-old design when so many examples exist in good enough shape. Let’s reupholster!
I started a Craigslist quest to find a suitably-sized sofa with a pleasing shape and a reasonable price. I found this striped specimen in Cockeysville, MD at a furniture resale shop, and was able to talk them down to $75.The structure was in solid shape, and a hole in the dust cover fabric along the bottom revealed 8-way tied springs (bonus!). This was a more legit method than I would have likely done in a new sofa, such as sinuous springs or webbing.
As I finished school, this striped sofa sat in the cave providing periodic support for Nintendo sessions. Months later, it was time to get to work.
Step 1: De-upholstering
With most reupholstery jobs, the first step is starting to remove fabric from the bottom and back and work your way up. As you start working on it, it becomes clear that there are many, many tacks and/or staples for each layer of fabric.
Although I planned on a different design with a tight seat and tight back (e.g. without cushions), I kept the outermost panels to estimate yardage with more accuracy. My cat, Henley, helped me measure for foam.
This couch was reupholstered at least once, based on the number of markings from tacks around the existing fasteners. Since the vast majority of fasteners were tacks and all padding was worn out (and crunchy) foam and cotton batting, I’d guess this striped fabric is from the early 1980s. There aren’t any helpful tags or markings that reveal any dates or history, though.
Step 2: Renewing the Padding
Now that I had removed all the upholstery and decades old cotton batting, I replaced the padding with modern materials that would hopefully be long-lasting and easy to work with. I ordered my first batch of foam from FoamByMail.com, who offers high-density foam in custom sizes. While waiting on the foam to arrive, I had some more work to do.
For my sofa design, I needed to box in the seat back a little more. I glued and screwed a a 1″x3″poplar board cut to fit onto the seat back uprights.
It wouldn’t be overly noticeable later, but I filled in the spaces around the tied springs with firm sections of leftover cotton batting and foam. This should keep things in the right place over time.
I then wrapped the seat back to help even out the profile of the springs. The middle was a bit bowed out as compared to the side sections. In retrospect, it perhaps would have been optimal to retie all the springs.
My first batch of foam had arrived! I ordered FoamByMail’s HD-36 high-quality (2.8 LB/ft3 density, 35LB ILD) in 4″ thickness. A 3″ foam probably would have been sufficient for padding and tufting (since I was going to add at least one layer of dacron wrap), so I ordered thinner padding for the seat back.
In following the lead from the book from ‘Spruce’, I added edge roll to all of the hard edges of the frame. This should prevent the most-used areas–arm, front of seat, top of frame–from wearing too quickly.
I received foam batch number two: 3″ super-soft foam (not pictured, 1.2LB/ft3 density, 12LB ILD) and plenty of dacron. Time to get ready for tufting.
Step 3: Prepare for Tufting
This was essentially a geometry lesson with lots of trial-and-error. I needed to divide up the tufting areas on the seat and back, each roughly 26″ x 84″, into squares. This ended up being about 5.5″ square.
I trimmed the pieces to fit perfectly using an electric carving knife, and began fitting this to the sofa frame. I used a method described by the ‘Spruce’ book where you adhere burlap to the foam, then adhere the burlap to the frame. This made for a nice pretty profile, but didn’t last forever…the burlap eventually pulling away from the foam as was forewarned in the ‘Spruce’ book. This method is probably ideal for smaller tight seats and backs that can be finished in a short amount of time. I was just too slow.
I used some HD-36 1″ foam to cover other sections of the frame. I used a 1.25″ hole saw to cut holes in the foam. This was easier on the firm foam, and required periodic lubrication to avoid binding up. Allowing the hole saw/drill to come up to full speed before introducing to foam also helped avoid any shenanigans from movement of foam or hole saw. There is a specific tool for cutting foam that may work better, but I opted for a more multitasker tool.
Also shown are some grooves I cut into the surface of the firmer section of foam. I had seen this technique performed on some professionally upholstered tufted sofas, and should allow the folds of the tufts to sit tighter.
I wrapped both the seat and back in one layer of 1″ medium density polyester fiberfill and 1″ low density/softpolyester fiberfill. I cut crosses into the fiberfill layers where tufting folds will eventually lay.
With the sofa padding wrapped with fiberfill, all that’s left is to order fabric…the most expensive individual step and the official point-of-no-return for the project.
Step 4: Fabric Incoming and Starting Tufting
I selected 'Hourglass' in 'Liberty' color by Knoll Textiles. This was an attractive choice (in my opinion) by a well-known source with high durability and easy cleaning (water and water-free solvent approved). I ordered 15 yards of the fabric and was excited to receive it. Shown in the photo is a small sample of the same fabric in yellow to I could practice.
As described in the previous step, I applied the same math principles to the tufting layout. On the inside of the fabric, I drew out the spots for buttons. After viewing a wide variety of YouTube clips on tufting, I decided to expand the grid beyond 5.5" square. It was clear, though, that this was in error as this left far too much slack in the fabric for my padding. The grid ended up being closer to 6" square, but will depend on the "fluffiness" of the padding you choose...more foam, dacron, etc. means larger space needed between buttons.
Speaking of, I whipped up some buttons with a DIY kit. This led to some heartache later, and I would recommend having some buttons made locally and professionally. Specifically, DIY covered buttons can pop apart when lots of force is applied when executing tufts. This makes the tufting process take much longer, as you're fixing buttons as you go.
Using waxed string and a jumbo upholstery needle, I started tufting! Each button got about 18-24" of string which was strung through the back of the button. Both ends were threaded though the eye of the upholstery needle, which was then poked through the fabric at the appropriate grid point. After the needle was pulled all the way through the fabric, dacron, foam (via the hole punched out), and burlap, the string was tied using a slipknot. This is a bit tricky to see in my photo, but there are innumerable tutorials on YouTube. The knot alone won't hold the button against the burlap, so you'll need to add a small piece of leftover fabric, a cotton ball, or anything else small probably. This allows you to tighten the knot, while pushing the button into the padding with your other hand (or more ideally, the handle end of a big screwdriver like I did).
Several hours and beers later, I had the entire seat done! Time for video game break!
Step 5: More Tufting and Finishing the Edges of the Cushions
Keep tufting, perfecting your slipknot technique, and using your pre-measured grid for button placement. You'll find that tufts/pleats start occurring naturally, and any loose or baggy spots can be overcome by tightening the nearest button's slipknot. Soon, the back and the seat were finished!
In order to complete the effect on the edges of the sofa, you pull the fabric--ensuring the pleats are laying correctly-- and staple the fabric onto the frame. This takes a bit of practice, and you'll screw up a few of them. I think doing them from the middle out led to the best result, but don't be afraid to undo all your staples and start over.
The only photo I have of this last portion of this step is blurry...sorry about that.
Step 6: Padding the Arms and Seeking Professional Help
I had already applied edge roll to the arms. I added 1" HD High Quality foam wrapped around any surface that would be leaned on. Lots of staples held this in place, though looks pretty heinous in retrospect. Dacron wrapping later would hide these crimes.
Any portion of the arm that wasn't padded would get a layer of burlap stapled on. The photo I took here revealed I was running out of burlap, and only had enough to cover most of this gap...whoops.
There weren't too many portions of this project that I couldn't do myself. Although it's on my wishlist, I didn't have a sewing machine. That meant any sewn portions (only a small handful in the entire project) needed to be outsourced. I sent the arm fabric I had retained, measurements for piping required, and a few yards of fabric to my local upholstery shop for some help. He gave me a killer deal: $85 for 5 yards of piping and two sewn arms (each with a bit of piping on the outside edge). If you're in Baltimore, give this guy your business.
Step 7: Finishing Arms and Apply Additional Piping
With sewn arms and piping in hand, I could get these arms done. Although they were a bit tight (with my overzealous padding and wrapping) and required some massaging into place, the arms fit great! Pull all of your fabric tight and staple. It's not pictured here, but cutting of extra after you're sure you're finished can help get extra material out of your way when you are in tight quarters.
I stapled my piping onto any spot that needed it. Shown here is the front of the sofa below the seat. The order goes like this, very similar to closing the back of the sofa in the next step: (1) staple piping, with fabric flap down, (2) staple on fabric on piping's fabric flap to cover the area, (3) staple cardboard tack strip under the fabric butting up against the piping (see pic), (4) pull fabric tight and staple onto frame. That's it! Curves like on my sofa can be a bit tricky and blind stitching by hand may be required, especially if in a high visibility area.
Step 8: Finishing Touches
As with the piping in the previous step, finishing the back is easy. You'll staple any piping or fabric onto the frame, add a tack strip and any dacron, then pull fabric down tight and staple onto frame. More padding here might have been optimal...specifically adding burlap for strength and more foam or dacron to 'fill out' the area. Since this sofa will almost always be against a wall, I didn't sweat this detail too much, but YMMV.
I added some Pretty Pegs legs on brackets, as you can see here. I didn't attach a fabric dust cover at this stage, but would recommend one. Not only does it keep dust out(?), but keeps any loose strings from your springs or buttons from being visible below your masterpiece.
Step 9: Finished!
I picked up some down pillows from a resale shop and the sofa was complete!
All told, this project took almost exactly 3 months of nights and/or weekends, but a pretty good amount of idle time waiting for ordered products to arrive, outsourced sewing, etc.
This was a tough project, but I learned many new skills along the way. Let me know if you have any questions!
Here is a mostly accurate list of costs with products used:
- Sofa, used - $75
- Professional Help
- Sewn arms and piping - $85
- Fabric
- Padding
- 4" HD foam for seat - $93
- 3" super soft foam for back - $40
- 1" HD foam for arms and extra areas - $20
- 1" polyester fiberfill (medium, for seat) - $30 total
- 1" polyester fiberfill (soft, for everywhere else) - $15 total
- 3/4" edge roll - $14
- Legs
- Miscellaneous
- Waxed button thread - $4 each, about $24 total
- Cotton piping - $12
- Upholstery tack strip - $8
- Size 36 (7/8") Button kit - $17
- Upholstery dust cover - $7
- Adhesives, Fasteners
- Total cost (not including tools, time) = $870
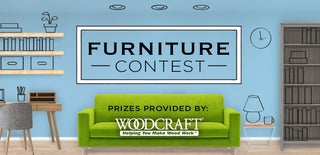
Judges Prize in the
Furniture Contest 2017