Introduction: Silversmith Jewelry (Lost Wax Casting)
20 years ago, just before I proposed to my wife, she commented that she was not interested in an expensive engagement ring. So I was left trying to figure out a way to give her a ring that would have more sentimental value than market value.
Some months earlier, actually on the night of my brother's bachelor party, he removed a couple silver rings he wore and said to "I guess I won't be need these anymore since I need to make room for my wedding ring." I told him I would hold on to them, not sure why I did though. And one day while I was thinking about my own engagement ring dilemma, I saw those rings and the thought ran across my mind "Would it be possible melt those rings down and make an engagement ring?!" So I decided to give it a try.
The internet was in a much more rudimentary form back then, but I came across a site that described the basic steps to making jewelry by using the Lost Wax Casting method. And what is more, it showed how to do it with very cheap and available equipment. A few things you may have to send away for, but they are affordable.
So far I have seen some stellar Lost Wax Casting tutorials on Instructables, and I encourage you to read a few to get a more complete idea of the concept. Yet many of them involve a store bought kiln or spinner or something which can be expensive, especially if you are just getting started or you just prefer to tinker. We will use steam to make our casting.
So here we go! (And forgive some of the older looking photos, they actually came out of my wedding album)
Step 1: Gather the Goods
Here are the materials with some alternate suggestions in parenthesis:
Safety gear (goggles, gloves, suit of armor... in fact wear it all now as you read on.)
Empty Tuna Can
6-8" wooden dowel
1-Screw
Paper towels (tissues/toilet paper...)
Empty Tomato Paste can (both ends open)
6" flower pot (or 8" or so)
Wire coat hangar
Aluminum Foil
Propane Torch
Single Burner Propane stove
1/2" Hardware cloth (something to let heat come up through)
Casting Investment (I use Satin Cast 20. You might have to spring for this one as I heard plaster of paris cracks under high heat)
Clay/Silica crucible (or gouged out firebrick or small cast iron melting pot)
Clay
Silver (or any metal with a low melting point. More then the project itself will use.)
Wax (for model and for sprue channels)
Borax (cleansing agent)
Dremel
Optional:
Jeweler's file
Ring sizer
Step 2: Wax On! Wax Off!
Make the Jewelry
First make an exact version of what you would like in wax (Making extra models or test models helps with the learning curve). I made a simple ring with a single petal coming off both sides and a pearl in the middle. Remember, all the wax becomes metal. So whatever wax you may leave on that is "extra", will be metal you have to grind or sand off when you are finished. Trust me, wax is easier to remove then metal.
As far as wax, I used Sprue wax to make the entire ring. Sprue wax is a bendable wax stick in different diameters with a low melting point. I even worked with some of it under warm water to get it the right shape and thickness for the ring and petals. Paraffin (canning) wax is good to work with at warm temperature. So is dental wax.
(You can also order pre-made wax ring blanks if you want to make this step easier. It's up to you.)
Secure the Jewelry
Take some aluminum foil as a base and then make a clay mound to mount the ring on. (This mound will create a crucible for the silver later on.) It must fit within the tomato paste can while leaving about a 1/8" gap between the edge of the clay and the can. (You can see in one of the photos what it will look like with the clay removed, and the wax sprue holes and the 1/8" lip around the edge).
Now we need to add channels to allow the wax to leave the mold and silver to enter the mold. These are called sprue channels. With my example, the ring is simple enough to only need one sprue channel off the bottom.
With a hot needle or Exacto knife, secure a wax stem (sprue) to the wax jewelry. Think about the proper placement of the sprue channel (wax stem) so that when the wax melts, gravity allows all the wax to exit through the channel. I made the stem flare out to a tripod at the bottom. This can be done by twisting small stems into a larger one or by branching out a medium size stem.
Side Note- In other methods this sprue channel is quite large, but here you do not want it to big or the molten silver will leak in prematurely. (Nor so small that the silver can not get in sufficiently.) I ended up with a main Sprue channel the width of the band where it connected to to the ring. But smaller where it connects to the clay.
Drip a few drops of wax on top of the clay mound. Then attach the Sprue wax/channel to the wax on the clay mound by just touching the feet with a hot needle or Exacto knife to the wax button on the clay mound.
The end should be the wax model of the ring standing upright with a wax stem connecting it to the clay.
Step 3: Time to Invest
When this is finished, lower the tomato paste can over the model and bring the aluminum foil up around the can. Secure it with a rubber band.
Now gently mix the Casting Investment in a bowl so that it doesn't fill with bubbles. Instructions should come for mix ratios, but this is just over a 2 to 1 ratio. (Or about Belgian waffle batter consistency.)
Pour it into the can leaving around 1/2" head space.
After a it hardens on top, enough to scratch your name in it, flip it over and remove the aluminum foil and peel out clay. After about 4 hours you will be ready to burn out the wax. (Some say they have only waited two hours, others waited months...)
Two hours into cure time and your ready to start the kiln. (In fact, it's a good time to make the kiln if you haven't yet, or build a steam stamper).
Step 4: Under Pressure
To make a Steam Stamper, you simply attach the dowel to the tuna fish can with a single screw in the middle of the can.
This will contain a wet paper towel later in the process. This wet paper towel must not touch the melted silver! Because high temperatures reacts so violently with water, steam will be quickly created and used to drive the molten silver into the empty mold. (As opposed to Centrifugal force.)
(Warning! Do not ever mix molten metal and water, it is not safe!)
Step 5: You're Kiln Me
The kiln is nothing more than an aluminum covered clay flower pot. You can bend a handle for it out of a metal coat hanger. This handle will get hot, so use gloves or pliers after the kiln is started.
Bend the wire like shown in the photo and then insert it into the hole in the pot.
Then take the single burner propane stove and start it up. Place a strip of 1/2" hardware cloth across it. (This is all best done outside as there will be some smoke from the wax burning off. )
After the stove is lit and the hardware cloth is in place, place the can with your wax model/plaster in the center with the Sprue channel and "bowl" facing down! (The wax must melt out of the holes that the wax stem leaves behind.) Immediately place the flower pot over the top of the burner.
Let the whole thing burn for about 2 hours. The worst of the smoke is in the first half hour.
At the 90 minute mark, prepare to finish the project because it moves quickly at the end.
Step 6: Feel the Burn... Actually Don't Touch It!
30 Minutes Left
About 30 minutes before the kiln time is finished, start to prepare the final steps.
Take your steam stamper and stuff a couple wet paper towels into the top of it. Press extra water out, but leave moist. (Do not fill it full of paper towels, you do not want to make contact with the silver! Again,this step creates a steam chamber by the moist paper towel reacting with the heated 1/8" lip).
Next take your silver (Make sure it is really silver before you get to this step, I pre-melt everything early to test it). Place it in your crucible and melt it down. I have a very cheap small crucible that I melt silver in. You can go cheaper by chiseling out a pocket in a firebrick. Or you can grab a cast iron melting pot from a box store.
Hold the torch to the silver. The larger the chunk of silver, the longer it takes to get up to it's melting point. It will turn colors and eventually start to melt. When it has melted you can sprinkle in some borax to purify the metal. When you finish this step, it's time to remove the mold from the kiln. Here comes the part where everything happens quickly.
The Finale
It's now about the 2 hour mark, so lift the flower pot off and quickly set it aside in a safe spot (It will be really hot). Then with tongs (or pliers) grab the mold and flip it upright so that the bowl is facing up (like in the photo). Then with the tongs grab the already preheated chunk of silver out of your crucible and place it in the bowl of the mold to the side and not directly over the holes. This allows the silver to flow down and pool over top of the channels while it melts, assuring you that it is all molten and not just a part of it.
When it is in a pool in the center of the bowl, grab the steam stamper and firmly stamp down on top of the whole mold. This creates a steam reaction and forces the metal down the path of least resistance (ie. the sprue channels in the ring mold.) Hold it for about 5 seconds. It's recommended you have enough material that not only is the whole ring formed, but there is a silver "button" left behind that was unable to fit into the mold.
It's important that this whole thing happens quickly because the mold is hot from the kiln, the silver is hot from the crucible that you were pre-heating it in, and if anything cools down too much then the silver will set-up prematurely.
After you have done all this, let the whole thing cool for a little bit.
Step 7: She Said Yes!
Once the mold is cooler, you can put it in water and shake it around to dissolve the plaster mix.
Pull the ring out of the water, it will be pretty black so start cleaning it up. You can use Dremel tools or wet sandpaper or jeweler's files or a little of each.
I cast mine with a stud to a pearl earring in it so that I could mount a pearl in it when it was finished. I bought a half drilled pearl before making the ring which was the backward ways of doing it. I should have made the ring and then brought the ring to a jeweler to have a pearl sized to it. That would have been much easier. (But this does mean you can retro fit a jewel if you have one that you would like to use...)
The whole casting took me a few tries to finally get everything right.
Afterwards I carefully cracked and hollowed out a walnut, lined it with some red felt, put the ring in it and glued it back together. I asked her to marry me and handed her the walnut as my token of love. She smiled and said yes. Then she cracked it open and quickly learned the only nut in the room was me!
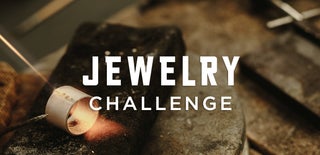
Participated in the
Jewelry Challenge