Introduction: Simple Backyard Pot Belly Stove
I'm not an outdoors person but I wont pass up the chance to weld something together.That picture makes it looks like the Leaning Tower of Pisa but it's really pretty straight. It's just me......
My sister Eletra showed me a picture of one of these made with 2 old car rims.
I updated the design a bit with legs, a fire door and 2 more rims. I also added a baffle so you can use a frying pan and not get burned while holding the handle.
It makes a nice addition to my backyard grilling corner.
Step 1: Collecting the Rims
You need cheap steel rims. Nothing fancy here. I had 2 old 14" Volvo rims lying around but I needed 2 more so I turned to Craigslist and found 2 15" BMW rims really cheap, only $25. This worked out pretty well since they would interlock when stacked.
I grabbed a plasma cutter and removed the center section from one of the 14" rims. You could use a sawzall or cutoff wheel too.
I stacked the rims to get an idea of how tall it would be. Even with 4 rims it seemed a little short but I will add legs later to fix that.
Step 2: Cleaning Everything Up
These had the old fashion Lead wheel weights. A chisel and hammer removed these pretty quick. A knife could be used to remove the valve stems but since I had the chisel in my hand I used it to chop them off too.
After that I ground the inside of the 15" rims and the outside of the 14" rims so I could weld them together..
Step 3: Welding It Together
I used little 1 inch stitch welds every 4 inches crisscrossing my way around the rims. I started with the top section but any way you feel comfortable works. Just remember to stack them properly.
I started with a 14 on the bottom and alternating on the way up to a 15 on top. The two bottom rims face down while the two top rims face up giving a large firebox.
You should see good penetration on the opposite side of the rim. I didn't completely weld the circumference. You can if you want to.
Step 4: Legs
I needed a little more height.
I decided to make a door on the side rather than just a bare opening so the extra height will really provide good airflow.
I used a piece of 1 1/2 EMT tubing and cut a couple of ~6 inch pieces. I didn't measure, I just cut off what looked proportionately appropriate and made three of the same length.
A little prep on the belt sander to remove the galvanizing and they're ready to weld on.
Step 5: Valve Stem Holes
I was going to weld up the valve stem holes but then I looked through the top and noticed the valve stem hole in the second rim down was in a nice position to hold a thermocouple. It's partially shrouded from the rising fire and about the right size so I left them alone.
This will be the subject of another Instructable.....
Step 6: Cutting the Fire Door
I took the Plasma cutter and made a vertical cut up the the edge of the middle weld between rims. Then I switched to a sawzall to cross the middle cutting right through a stich weld. I then went back to the plasma cutter and finished the cutout using the sawzall to cross the middle on the way down.
A little tap from a hammer and it fell right out...
Step 7: Finishing the Opening
Cutting through the weld with a sawzall gave a really nice edge that need very little cleanup.
A quick pass with a grinder made all the edges nice and smooth
Step 8: Making the Door
I took a scrap of piano hinge and traced the profile of the rim on to it. I rough cut it on the bandsaw and perfected the fit with a grinder.
I couldn't decide whether to put the hinge on the side or bottom. I ended up putting it on the bottom. I was going to tack weld a spring on to the top for a handle but the lip of the rims seemed good enough to me.
Attachments
Step 9: Leftovers
Not a lot of waste so far and even the valve stems got a second chance at life. I used them for handles for valve core removers. A little drop of loctitie and then crews on a remover and you have a neat little rubber handled valve core remover......
Step 10: Still Not Done
It looked done but what about actually using it. My sister had given me a nice cast iron dutch oven for Christmas. Its supposed to be good to 1000 degrees just right for outdoor cooking but I might want to use a standard frying pan too.
I made a template for a semicircular baffle to block the flames where the frying pans handle would overhang the stove. I wanted there to be plenty of room between the rims holes and the baffle to keep up the air flow but not too high so it hits the pan
I could have just welded a couple of the rims holes up but his way there is still airflow all around the stove. It also nicely covered the top valve stem hole.
I turned to my scrap pile and found a nice heavy piece of steel. Using the plasma cutter I cut out the shape and refined the fit with a grinder.
This one I did stitch weld connecting them from end to end. A little cleaning with a wire brush and it is ready for some high heat paint...
Step 11: Finally Done and Ready to Fire
I have to find a good Chilli recipe for next weekend. My sister is coming up to visit and I'll make the first firing of it then....
Step 12: First Firing
I put a bunch of charcoal around the outside and then I added 3 short logs to the middle.
Once lit it warmed up quick. the paint seems undamaged except for some soot on top of the stove. the fire was a little smokey at first but soon settled down. the air coming up through the center made a nice flame...
I used a wok to brown the meat so I could easily drain off the fat. Simple Chilli recipe, tomatoes, peppers, beans, chopped beef, seasonings and a couple of hours of bubbling heat....
The temperature seemed perfect. bubbling but never burning...
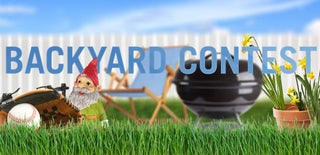
Participated in the
Backyard Contest