Introduction: Sixty Foot Water Feature
This is how I went about making foam molds for a water feature. At Oregon Institute of technology the Civil engineering department wanted to make a teaching sculpture. The sculpture was built first then when they got more money they expanded the project to include concrete walkways and the water feature. To read more about the project see HERE. To build the concrete sections they hired contractors but to outsource the molds they received quotes of around $4000. We built the molds for much less. We could choose any method we wanted to build the molds and had two terms to build it.
Step 1: Design
We were given 2D AutoCAD drawings of the plaza with several cross sections and just a little description. The files that we started out with were drawn by civil engineers in a style useful for civil engineers with a lot of curved lines and no dimensions. We had to copy out the sections of the drawings useful for us then import them into SolidWorks. We used SolidWorks because FeatureCAM, the NC code program we used, had a plug-in that worked well with SolidWorks not Inventor. The easiest way to import the drawings was to convert the drawings from .DWG to .DXF. After we had the 2D drawing imported into SolidWorks it was easy to accurately create 3D models.
Step 2: SolidWorks
In SolidWorks we designed models as best we could from what we were given. I took screen shots of our drawings with emphasis on sections I thought might cause problems and sent them to the civil department for review. They replied back, we had several meetings then finished the models. Some of the early drawings are shown in the pictures
After the models are drawn I had several models that were 20ft long. The problem was that the ShopBot CNC machine was only 7ft long. I had to chop the models up and fit them in the cutting area of the machine, to do that I chopped the molds into smaller sections and imported them into a large assembly. This caused a small problem when exporting them as a single .STL file for ShopBot that was fixed by resaving as a single part before exporting. I found out towards the end of the project that it could also be fixed in the .STL settings.
After the models are drawn I had several models that were 20ft long. The problem was that the ShopBot CNC machine was only 7ft long. I had to chop the models up and fit them in the cutting area of the machine, to do that I chopped the molds into smaller sections and imported them into a large assembly. This caused a small problem when exporting them as a single .STL file for ShopBot that was fixed by resaving as a single part before exporting. I found out towards the end of the project that it could also be fixed in the .STL settings.
Step 3: Practice
Because we have never used the machine to cut this much material before we needed to practice and experiment with cut speeds. The easiest way to speed up the process was to remove the roughing passes because the foam was soft enough that it was unnecessary. Next we increase the distance between each cut and the cutting speed. We anticipated that it would be quicker to use sand paper on the molds when we were done then to have a small distance. On our practice parts everything sanded easily and we had no problem getting the shapes we needed. The pictures show the settings we used to cut the blue foam boards.
Step 4: Molds
The molds took a lot longer than we expected. Each 2x7 foot board took about an hour to cut if we didn’t have any problems. Cutting was fun but because we were taking such deep cuts our vacuum clogged up and we ended up needing to sweep it most of the time. One of the pictures should be a time-lapse of the cutting process.
After the parts were all cut out it took a little longer to sand then we anticipated but it was still faster than with a lower cutting stepover. To rough in the edges of the mold we used a band saw. Next we used Oscillating Spindle Sander and disc sanders to make the edges smooth and even. Lastly hand sand it till it is perfect.
After the parts were all cut out it took a little longer to sand then we anticipated but it was still faster than with a lower cutting stepover. To rough in the edges of the mold we used a band saw. Next we used Oscillating Spindle Sander and disc sanders to make the edges smooth and even. Lastly hand sand it till it is perfect.
Step 5: Concrete
The concrete started with the standard plywood forums. They were filled with concrete and then the molds were stamped in. As you can see in the pictures some boards were then fastened to the forums and then over the top of the molds to keep them in place. The foam molds wanted to float on the concrete and needed some pressure to push in. After the concrete cured the majority of the mold came out easily and the rest came out with a little scraping or pressure washing.
Step 6: Finished
The project is done and here are some pictures. With it being so large it was hard to fit it in the picture.
The water feature has some cool things that I was not really involved with but you might find interesting. All winter long the fountain would be frozen if it was not for the geothermal heated water. The water should stay about 40 degrees Fahrenheit all winter. There is a section where the water goes down through a siphon under the sidewalk and back up the other side. The different shapes the molds go through are to help show how water flows. The flow of the water can be adjusted to show the different effects over the bumps and ridges.
The water feature has some cool things that I was not really involved with but you might find interesting. All winter long the fountain would be frozen if it was not for the geothermal heated water. The water should stay about 40 degrees Fahrenheit all winter. There is a section where the water goes down through a siphon under the sidewalk and back up the other side. The different shapes the molds go through are to help show how water flows. The flow of the water can be adjusted to show the different effects over the bumps and ridges.
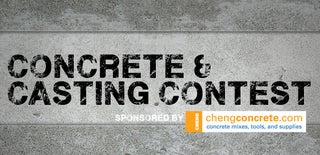
Participated in the
Concrete and Casting Contest