Introduction: Sliding Shelves
A number of years ago, while living in a much smaller house, I realized that the space we were using as storage in the basement was very inefficient. We had a bunch of shelving units, but to be able to get to the contents there needed to be a considerable amount of space between the shelves, space that was totally wasted.
A normal shelving system needs a minimum of 1.5 shelf widths for each shelf, one for each shelf, plus at least the same amount between each pair of shelves. The simplest example is 2 shelves. There has to be at least 1 shelf width, and usually more, between the shelves to be able to add and remove items from the shelves, so that makes 2 shelves plus the space between, or 3 shelf widths.
[1-][2-][3-] |--| |--| | | | | |--| |--| | | | | |--| |--| | | | | |--| |--|
A larger example would be string of 10 shelves, each 18" deep. This requires 18" (1.5') for each shelf on the end, 36" for each pair in between (which can be placed back-to-back), plus space between the shelves. This adds up to 270" (15 x 18") or 22.5'.
[1-][2-][3-][4-][5-][6-][7-][8-][9-][10][11][12][13][14][15] |--| |--||--| |--||--| |--||--| |--||--| |--| | | | || | | || | | || | | || | | | |--| |--||--| |--||--| |--||--| |--||--| |--| | | | || | | || | | || | | || | | | |--| |--||--| |--||--| |--||--| |--||--| |--| | | | || | | || | | || | | || | | | |--| |--||--| |--||--| |--||--| |--||--| |--|
An idea struck me, based on something I had seen in a library at one of the places that I had worked. They had shelves that moved on a floor track, such that several shelves could be moved so that they had no room between them, making room elsewhere. When you want something on a shelf you simply moved the shelves to the left or right out of the way, making space in front of the shelf you wanted to get to.
That type of shelving only uses N + 1 shelf widths to hold the same number of shelves, so 10 shelves only requires 11 feet, instead of 15, a saving of 4 feet, which allows another 4 shelves to be installed in the same space, an increase of 40%!
Step 1: Hardware Found!
I thought about putting shelves on wheels, but given the amount of stuff I would be putting on them, and the fact that the basement floor wasn't perfectly flat, moving them would be a problem because they would tend to want to fall over easily. This was potentially a recipe for disaster, both for the stuff on the shelves and anyone who happened to be in the way!
I was at my local home store one day and found my answer! Rather than rolling the shelves on the floor I would suspend them from the ceiling, using hardware designed for sliding barn doors!
The hardware I used was made by Stanley, and consisted of a rail and a trolley which rode in the rail. There were several different trolleys available but the trolley I choose was similar to the current 5001 model, which had 4 steel wheels, Delrin bearings and a 7/16"-14 bolt suspended from it. The trolley was meant to be bolted to a bracket connecting it to the barn door, allowing the barn door to slide along the rail to be opened and closed. The rail are available in lengths anywhere from 6' to 24', to meet just about any need. The 5114 Plain Box Rail is rated at 600lbs, and I decided to use 3 of them, giving me a total of 1800lbs of storage on my selves. The trolleys, "5001 Box Rail Hangers", are rated at 225lbs each, and I was using 6 of them per shelf, for a total of 1350lbs. I figured that would be more than enough.
Step 2: Installation of Version 1.0
I hung the three rails from the first floor joists in my basement, using some lag bolts and the brackets that were made for the rails (51HB box rail bracket). I constructed my shelves out of 2x3s, 2x4s and some plywood. They weren't pretty, nor were they adjustable at all, but they held a pile of stuff, were cheap and served me well.
I eventually moved the entire thing to my new home in 2002, but I wasn't satisfied. This contest gave me the incentive to make Version 2 of the shelves.
Step 3: Choosing New Shelves
I had been wanting to replace the shelves with something more flexible so for this instructable I decided to redesign them, reusing the same hardware, but replacing the shelving itself. A visit to my local home store provided me with a number of different shelving options, but there were a few constraints:
- They had to be easily adjustable without having to disassemble the entire structure
- They had to be strong
- They had to work in a hanging configuration
- They had to be relatively inexpensive
I looked at making my own shelves out of angle iron, which would have been very strong, but would require tools to move shelves around, and was also very expensive.
I looked for pre-made shelves and found the ones shown above. The first shelf was made of plastic, and although quite strong they aren't at all adjustable, nor would they work in a hanging configuration. The next one was strong, but not adjustable at all, at least without tools. The next two shelves are easily adjustable, but were the shelves themselves are made from particle board so are pretty flimsy, despite their rated capacities. The second to the last one was quite beefy, but only had three shelves and was quite expensive. Finally I settled on wire shelving units shown in the last picture. These shelves are strong, easy to put together, adjustable different heights in 1" increments, had five shelves and are fairly inexpensive. The only problem was figuring out how to make them work in a hanging configuration.
Step 4: Designing Version 2.0
My original idea for using the wire shelving was to flip the uprights upside-down, and screw the trolley into the bottoms, which is where the leveling feet or optional wheels are usually installed. There were a couple of major problems with this idea, the first being that the bolts for the trolley are 7/16, and the threaded inserts at the bottom of the uprights are 5/16. I thought I might be able to drill them out and retap them, but I quickly learned that the threaded inserts are simply pressed in, with nothing but friction holding them in place. Plus they were designed to be placed in compression, not tension, so weren't all that robust.
The first picture shows the ends of the uprights and the hardware that goes into them. The piece on the left is one of the adjuster feet, screwed into the threaded insert on the bottom of the uprights, shown in the second piece. The third piece shows how one end is tapped for a coupler, which is the right-most piece, that connects the upper and lower uprights together, second picture. The top of each upright simply holds a plastic plug.
I considered welding the threaded inserts in place, but decided against it as my stick welder (more like the operator) doesn't work well with thin material, and I was pretty sure the inserts were made of some pot metal, which isn't weld friendly.
While wandering around the home store I came up with an idea! I grabbed some 1" id black pipe nipples, which fit around the uprights nicely. I'd drill and cross bolt them onto the top of each upright, then screw a black pipe cap onto the end of the nipple, drill that for the trolley bolt and connect everything up. The third picture shows the end product.
The only downside was that the nipples and end caps each cost a couple of bucks, and even if I bought longer nipples and cut them in half (I only needed the threaded ends on one side) it still got to be expensive. Then I looked at the original uprights and it hit me. DOH!
Step 5: Designing Version 2.1
My original design used some U-shaped construction hangers that I flattened and drilled out for the trolley bolt. I could do the same thing for the new design. Unfortunately the construction hangers were sized for 2x (1.5") material, and the uprights were 1" od, and I thought they might not be strong enough (the old design had the thickness of the 2x4's to support the hangers and keep them from bending at the top), so I decided to just redo them from scratch.
I bought two 1"x1/8"x72" flat steel bars. These were cut into 6" pieces and bent into a squared off "U" shape, with a metal working vice and a hammer, making a yoke. Then they were drilled for the top bolt and cross-drilled to hold the pipes. Note that the drilling was done after bending the bars, otherwise the bars would want to bend where the holes were drilled, as it was weaker there...
Step 6: Assembling the Uprights
I was worried that the cross bolts might compress the thin-walled uprights if they were over-tightened, so I took some 1" oak dowel that I had lying around, cut those into 1.5" segments and inserted them into the ends of the uprights when I cross-drilled them. The plastic cap went on top of the oak plug, and they were left in place when they were bolted to the yoke.
When I hung them from the tracks, which by now had been removed and reinstalled at the correct width for the new shelves, I noticed that they were about 8" off the floor, meaning there would be 8" of wasted space under each shelf. Rather than ignore the issue I bought some 7/16" threaded rod, cut them into 8" pieces and using couplers and jam nuts I extended the trolley bolts. The fifth picture shows the extended uprights hanging from the tracks. The diagram shows how it all goes together.
There's something that I should mention here. You'll notice that there are three tracks, and three sets of uprights, but the shelves only have two sets of uprights each. That's because I decided to let the middle track/uprights do double duty and hold two sets of shelves, the left side of one and the right side of the other, while the end tracks/uprights hold one set each. It's easy enough to do this, as long as you stagger the shelf positions, and interleave the shelves as you're installing them. It also has the advantage of allowing you to build two long shelves which is effectively like having four regular shelves, but you only have to buy three shelf units!
This works because with three shelves you get twelve uprights (four for each unit), and when you combine them into longer shelves you only need six uprights for the two combined units. Confused? You'll see later...
So, it all goes together like this:
- Build/Install the tracks:
- Mark a center line on the 2x8 cross member
- Predrill holes every 2' or so in the cross member to accept the bolts holding the clamps
- Bolt the track clamps to the 2x8 cross member, leaving the bolts slightly loose, so the clamps can pivot if necessary
- Slide the track into the clamps
- Bolt the 2x8 cross member with the clamps and tracks across the joists (*)
- The tracks MUST be spaced appropriately for the width of the shelf units for them to slide easily
- The cross member should be pre-drilled with oversize holes for the lag screws
- The joists should be pre-drilled through the oversize holes with a bit just smaller than the lag screws to make it easier to drive the lag screws home
- Build/Install the uprights:
- Insert the trolley bolt into the trolley
- Optional:
- Screw a jam nut onto the bolt
- Screw a coupler halfway onto the bolt
- Tighten the jam nut to the coupler to hold it in place
- Screw a jam nut onto the length of threaded rod
- Screw the length of threaded rod onto the coupler
- Tighten the jam nut to the coupler to hold it in place
- Screw another jam nut onto the bottom of the bolt/rod
- Insert the trolley bolt (or threaded rod) into the hole at the top of the yoke
- Screw another jam nut onto the bottom of the bolt/rod
- Slide the trolleys into the tracks
- Install end-caps to keep the trolleys from falling out of the end of the tracks
(*) My suggestion is to build something like a large "T", shown in the last picture, that you can use to hold up one side of the track while you're lag bolting the other in place. I did find it easier to use a couple of long drywall screws to initially tack the track up in place while I pre-drilled for the lag screws. This also helps with positioning the shelves to get the spacing correct before pre-drilling.
Step 7: Assembling the Shelves
With the uprights in place I began assembling the first shelf. Normally this type of shelf is assembled from the bottom up, by sliding the shelves onto the uprights from the tops, positioning the plastic wedge spacers where the shelf is supposed to go, then driving the shelf onto the wedge spacers with a mallet. Since all the hardware for the trolleys was in the way that obviously wasn't going to work, at least without me taking everything apart again, which I really didn't want to do.
Instead I decided to just build the shelves from the top down, so I slid the first top shelf onto the left-most set of uprights, snapped on the wedges, dropped the shelf onto them and hammered them home. Then I did the same thing on the right-most set of uprights, just 2" lower, so as to not interfere with the matching shelf on the left. The first picture shows this.
Next I added the third shelf 13" below the first on the left, and another 13" below the second on the right. I chose 13" because I have a bunch of plastic bins that I store stuff in, and they are 12" tall.
I continued adding shelves, but increased the distance between them to hold larger items at the bottom.
I had purchased three new shelving units, identical to some others that I was already using elsewhere in the basement. My plan is to add these to the system when I get a chance.
Each of the three units I bought has five shelves, for a total of fifteen shelves. These are scattered across two double wide units, so one of the units will have one less shelf than the others (4/4/4/3). This is OK because it will allow the storage of something that is much taller than the other shelves will handle. If this wasn't desirable I could always purchase an additional single shelf from the manufacturer.
Step 8: Version 2.1 Completed!
These pictures show the final product, loaded up with stuff. The first picture shows the two shelves that I've already installed, pushed together against a third, fixed, shelf. You can see how little space the shelves take up like this.
Once the first shelf is moved out of the way the second picture shows the contents of the second shelf, and the third picture shows the space between the shelves.
The forth picture shows the backside of the second shelf, a sliver of the fixed shelf on the far right, and the space made by moving the first two shelves.
In the final picture, taken just after the first shelf was completed, I laid out four of the shelves side by side, next to the one shelf that was already installed, to show how much room they would take. It's easy to see that there is plenty of room to have up to five total shelves in this relatively small space, giving you 420 total cubic feet of storage space (8'x7'x1.5'x5).
Step 9: Demonstration Videos
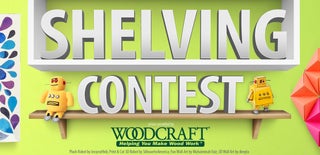
Participated in the
Shelving Contest