Introduction: Small Knife and Sheath
This is a quick run down of how you could make a little knife and sheath. The idea being to make a little knife that you could attach to anything with a carabiner for easy access when needed.
to complete this project you will need the following.
Materials:
1) steel, ~5"x1" , I used some old 5160 steel I had from an old leaf spring
2)leather, maybe around the size of half a sheet of paper should be more than enough
3) wood, again about 5"x1" the thickness of your steel and 2x your wood thickness should be a nice size for your hand
4)2 large nails for pinning the handles to the blade
5)metal D ring, or something else suitable for attaching to a caribiner
6)assorted little things like: needles, thread, glue, pushpin, cardboard, spraypaint
Tools:
1)angle grinder or something suitable to grind your steel to the shape of your knife
2)belt sander/grinder or file to bevel the edges of your knife
3)drill
4)kiln/furnace/oven/torch for heat treating
5)assorted files/ sandpaper for shaping the handle scales and polishing the blade.
Step 1: Design and Pattern
The first step is to come up with a design for your knife. I was aiming for a knife about 5" long with a 2.5" blade. if you want to use it for more arduous tasks you'll probably want to make the handle longer. I drew out a bunch of different designs then cut them out in some cardboard to see which felt the best in my hand. I picked out two I liked and arranged them on my steel so they fit nicely.
Step 2: Mark and Cut to Shape
I cut the piece of steel I had in two so both knives would fit then marked their shapes on each piece with some black spraypaint. Next I used an angle grinder to cut the steel to shape. you could also use files and a hacksaw but it would take longer. it's also important to make sure the sides of your steel are flat, especially if you're using something old or had to flatten it already. I used my belt sander to flatten out both sides of the knives.
Step 3: Edge Bevel
next up is to bevel the edges. I used a normal woodworking belt sander with some new belts just for this project. I found 120 grit belts worked quite well. I did it all freehand which is the simplest method but not particularly accurate for a first time. to try and get both sides relatively equally ground you need to mark the middle of the edge. Mark a line on either side of the blade an even distance from the edge, then grind from that line to almost the middle of the edge. you can do this a couple times moving the lines on the flats further from the edge. I ended up going all the way to the back edge of the knife to make a fully flat ground blade, but you can stop before then.
you want to leave the cutting edge ~1mm or so thick so it doesn't overheat during heat treatment.
once you have it ground to shape it's a good idea to use some sandpaper and get it nice and smooth before heat treatment. The steel will be much harder later and more difficult to get scratches out of. I would take it down to 600 grit paper.
now is also a good time to drill holes in the handles for the pins to help keep the scales on. I drilled two holes the same diameter as the nails I used for my pins.
Step 4: Heat Treat
I used a little enameling kiln to do my heat treatment. my procedure for 5160 steel is: heat to 850 C and hold for 2 minutes then quench in oil. Temper in any kind of oven at 200 C for 30 min then quench in water and do another 30 min then quench again. Using this process I get blades ~ 55 HRC which is a bit low for a small knife but not bad for a more hard use knife.
For the initial quenching process you just have to get the blade hot enough that it's not magnetic since the high temperature phase you want the steel to transform into isn't magnetic. Once it's non magnetic you can quench it in water or oil. with water you stand more chance of warping or cracking, but you can just dispose of the water normally. the oil is a bit slower cooling rate so there's less chance of cracking but you'll need to responsibly despose of the used oil afterwards, the oil will also likely ignite when you put the blade in so be careful! This applies to most steels, the biggest difference being whether water or oil is the preferred quenching media.
The tempering time/temperature is much more dependent on the steel you're using. If you're not sure it's better to use a low temperature and just extend the time you're keeping it there rather than increasing the temperature. you can google what you're using for your blade and see what other people have done successfully.
if you don't have an oven that gets hot enough, you can build a little "soup can forge" that should be able to get the blade up to non magnetic. You can find good instructions on how to build one online, I also included a couple pictures of the two I made.
Step 5: Handle Scales and Sanding
Next up is to make some handle scales and to polish the blade. you can just sand the scale off from heat treatment or you could polish the blade all the way to a mirror shine, whatever you prefer!
for the handle scales you need two pieces of something the same thickness that feels good in your hand with the blade between them. you can use the holes in your blade as a template to drill holes in your scales the right distance apart. Sandwich the scales together and use the nails through the holes to keep them aligned while you shape the scales the way you'd like. basically just make the knife comfortable to hold.
once it's nice to hold you can glue or epoxy the the scales to the blade. put glue between the scales and blade as well as in the holes then insert your pins through. once the glue/epoxy is all set you can cut the pins flush with your scales. make sure it's all sanded nice and smooth then add some oil to the whole thing, I used boiled linseed oil. it will make the scales look nice and a bit of oil on the blade will stop it from rusting.
Step 6: Sheath Pattern
next up is to make a pattern for the sheath. you can use some paper and play around until you have a shape and fit you like. it's better to make it a bit tight since the leather will stretch, but you don't want it so tight that the knife won't go in or come out.
Step 7: Cut and Glue Leather
use your paper template to cut out an appropriate piece of leather. fold the leather around the knife and glue the sheath closed. I used some binder clips as clamps which worked well.
Step 8: Sew the Sheath
once the glue is dry you can remove the knife and sew the sheath along the glued edge. I used a tack/push pin to pierce the holes then a regular sewing needle and thread to sew back and forth along the edge.
Step 9: Add D-clip and Hanger
you can then add a belt loop/ D ring by folding a strip of leather in half and gluing/sewing it to the sheath in the same way.
Step 10: Now You're Done!
now you're done! you can use the D ring and a carabiner to attach the knife to just about anything!
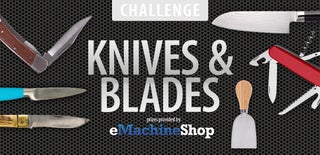
Runner Up in the
Knives and Blades Challenge
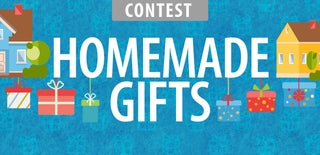
Participated in the
Homemade Gifts Contest 2016