Introduction: Spare Parts Garage/shop Stool
I was standing in my garage the other day wishing I had a suitable place to rest my bones, when I spied my broken motor parts from my old Firebird. This got my wheels a turning and I came up with a plan to put together a simple stool using only leftover pieces and parts.
If your anything like me, now is when you should hit the "see all steps button"
If your anything like me, now is when you should hit the "see all steps button"
Step 1: What You'll Need
One old spare wheel, tire optional - If your not using a tire I recommend going to an auto store and buying some heavy vacuum line or gas line and splitting it to go around your rim. This will prevent scratches etc in your floor.
One damaged crankshaft - I used one from a Pontiac 400 that I ruined the rod bearings in, but a v6 crank may be a more suitable height.
Harmonic balancer - This should match the crank you are using ideally. Mine was junk, as the machine shop operator labeled it.
Proper bolt and washer to connect harmonic balancer to crank - I had to call a dealership to find out the size of the bolt so I could get it at the hardware store, and found a washer that would work after drilling it out.
Flexplate or flywheel - I had an old flexplate for an automatic transmission that wasn't proper for my set up (I could only use 4 of the 6 bolts). I had other options, but they are actually good parts yet. Also need the bolts to attach to the crankshaft.
Wheel spacers - These may be unneeded, but I needed something to take up some slack, and I was never going to use these again.
Screws - This was my method of attaching the seat to the frame, I didn't use washers with mine (the first time) but I highly recommend it.
Scrap 3/4" plywood - This is what will make up the base of the seat that attaches to the frame.
Foam or padding - I recently took apart our old worn out bed so that I could make use of the foam, there are many things that would work well here. I used 3" foam cause I have a boney posterior.
Seat covering - I used a piece of vinyl I had bought a while back hoping it would work in my car interior, but it wasn't stretchy enough for that. Worked well enough here.
One damaged crankshaft - I used one from a Pontiac 400 that I ruined the rod bearings in, but a v6 crank may be a more suitable height.
Harmonic balancer - This should match the crank you are using ideally. Mine was junk, as the machine shop operator labeled it.
Proper bolt and washer to connect harmonic balancer to crank - I had to call a dealership to find out the size of the bolt so I could get it at the hardware store, and found a washer that would work after drilling it out.
Flexplate or flywheel - I had an old flexplate for an automatic transmission that wasn't proper for my set up (I could only use 4 of the 6 bolts). I had other options, but they are actually good parts yet. Also need the bolts to attach to the crankshaft.
Wheel spacers - These may be unneeded, but I needed something to take up some slack, and I was never going to use these again.
Screws - This was my method of attaching the seat to the frame, I didn't use washers with mine (the first time) but I highly recommend it.
Scrap 3/4" plywood - This is what will make up the base of the seat that attaches to the frame.
Foam or padding - I recently took apart our old worn out bed so that I could make use of the foam, there are many things that would work well here. I used 3" foam cause I have a boney posterior.
Seat covering - I used a piece of vinyl I had bought a while back hoping it would work in my car interior, but it wasn't stretchy enough for that. Worked well enough here.
Step 2: Base Assembly
This step would be safest with the help of a friend. I had to balance the crank shaft using the flexplate, seen on the very bottom.
Next I balanced the wheel/tire combo on top of the crankshaft.
Note: My crankshaft is 87lbs, and the wheel and tire combo is all of 40-50lbs. If it were to fall on a child or your foot it will hurt. Please hand a friend a barley pop and make them hold on.
Next I balanced the wheel/tire combo on top of the crankshaft.
Note: My crankshaft is 87lbs, and the wheel and tire combo is all of 40-50lbs. If it were to fall on a child or your foot it will hurt. Please hand a friend a barley pop and make them hold on.
Step 3: Base Assembly Continued
Now that the wheel and tire is balanced AND centered, I stacked my wheel spacers on top of the wheel.
Next I slide the harmonic balancer in place.
Lastly I started the bolt in by hand, and snugged it up with my impact wrench. (not needed, but handy)
Next I slide the harmonic balancer in place.
Lastly I started the bolt in by hand, and snugged it up with my impact wrench. (not needed, but handy)
Step 4: Attaching the Seat Frame
After righting the stool base (a friend could be helpful again) it is time to attach the seat frame (flexplate) Notice I was able to only use 4 bolts, but that should be more than enough to support any human.
I had to tighten the bolts using 12 point wrenches since they are 12 point bolts.
I had to tighten the bolts using 12 point wrenches since they are 12 point bolts.
Step 5: Seat Base
I used my 3/4" plywood for the seat base. I measured the diameter I needed and then drew a circle a little bigger than that using a compass.
I started to cut out the circle using my multicut tool, but that was going nowhere fast. I drove to the shop to use the bandsaw, of course I forgot my camera.
Here is the finished wooden base. Notice it has more than one diameter circle line on it. I kept changing my mind on how big I wanted the base to be.
I started to cut out the circle using my multicut tool, but that was going nowhere fast. I drove to the shop to use the bandsaw, of course I forgot my camera.
Here is the finished wooden base. Notice it has more than one diameter circle line on it. I kept changing my mind on how big I wanted the base to be.
Step 6: Cushion
This step would have been easier with a bandsaw or some other slick tool, but I did things the hard way.
I used a utility knife to cut the rough size I needed, and then marked around the wooden base on the foam.
Again, I used the utility knife to cut a half decent circle around the marks on the foam.
Here's were it gets a little dicey. I used an angle grinder with a diamond wheel on it to cut the recess out for the wood to go into. This wouldn't have to be done if you used actual seat filling, but this made it easier to hide the wood.
After the wood fits nicely into the foam I used spray adhesive to attach them to each other. Make sure to spray both surfaces and let them get tacky.
Note: always turn the can upside down and spray until the can sprays clean. This will help keep the nozzle unclogged.
I then flipped the seat cushion over and started to do some shaping again with the angle grinder.
The angle grinder sounds a lot more dangerous to use than what it was in actuality, but if you have another way to do it, I recommend trying that first.
I used a utility knife to cut the rough size I needed, and then marked around the wooden base on the foam.
Again, I used the utility knife to cut a half decent circle around the marks on the foam.
Here's were it gets a little dicey. I used an angle grinder with a diamond wheel on it to cut the recess out for the wood to go into. This wouldn't have to be done if you used actual seat filling, but this made it easier to hide the wood.
After the wood fits nicely into the foam I used spray adhesive to attach them to each other. Make sure to spray both surfaces and let them get tacky.
Note: always turn the can upside down and spray until the can sprays clean. This will help keep the nozzle unclogged.
I then flipped the seat cushion over and started to do some shaping again with the angle grinder.
The angle grinder sounds a lot more dangerous to use than what it was in actuality, but if you have another way to do it, I recommend trying that first.
Step 7: Upholstering
This portion is probably the most visually "ugly" part because the material would not stretch. The best I could do was make a wrinkle and staple it. My skills here are not very good, but all I really wanted was a functional stool that was a bit of a conversation piece.
Step 1 - Cut material to rough size
Step 2 - Cut corners off the material so you don't have so much to deal with.
Step 3 - Start by pulling material snug and tacking it with a staple. Less is more at this point.
Step 4 - Pull opposite side tight and tack.
Step 5 - Pull and tack remaining 2 sides.
Step 6 - Start a few degrees away from where you stapled, grab some material, pull, fold, and staple. Repeat all the way around the stool. Try to keep as many folds hidden from view as you can. (I wasn't able to accomplish this very well) or at least keep the folds uniform.
Step 1 - Cut material to rough size
Step 2 - Cut corners off the material so you don't have so much to deal with.
Step 3 - Start by pulling material snug and tacking it with a staple. Less is more at this point.
Step 4 - Pull opposite side tight and tack.
Step 5 - Pull and tack remaining 2 sides.
Step 6 - Start a few degrees away from where you stapled, grab some material, pull, fold, and staple. Repeat all the way around the stool. Try to keep as many folds hidden from view as you can. (I wasn't able to accomplish this very well) or at least keep the folds uniform.
Step 8: Attaching Cushion to Frame
My flexplate had 6 small holes that worked well for attaching. I used (6) inch thick screws to put it all together. I should have used washers to make things simpler, but I didn't have any at the time. This has since been resolved.
Make sure you get the cushion centered, and have a buddy hold it in place while you run the screws in.
As you can see from the finished picture, it is just a bit tall perhaps. I am 6'1 as a reference. I am very comfortable on it, but shorter people not so much. a V6 crankshaft would probably be more ideal for most. A footrest and backrest could be added, but would be a little more advanced.
I hope you enjoyed this Instructable, as it is my first (of many I imagine, I'm addicted to this dang site)
Please give me some constructive feedback so I can improve for next time.
Thanks
Chad
Make sure you get the cushion centered, and have a buddy hold it in place while you run the screws in.
As you can see from the finished picture, it is just a bit tall perhaps. I am 6'1 as a reference. I am very comfortable on it, but shorter people not so much. a V6 crankshaft would probably be more ideal for most. A footrest and backrest could be added, but would be a little more advanced.
I hope you enjoyed this Instructable, as it is my first (of many I imagine, I'm addicted to this dang site)
Please give me some constructive feedback so I can improve for next time.
Thanks
Chad
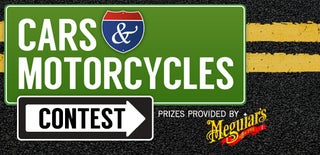
Second Prize in the
Cars & Motorcycles Contest