Introduction: SpectrumLED V2.0 - the ULTIMATE Variable Spectrum Lamp!
The story of SpectrumLED V2.0
-
Back in 2015, I built SpectrumLED (V1) - An INSANELY Bright, 200 WATT, Variable Spectrum LED Panel. It was extremely useful - to be exact, there has not been a day that I used my table for something without turning it on, since I built it. However, my needs have changed a bit:
Most of the time, I wan't to change the brightness of my lamps, and not the spectrum, which is something that isn't very easy with SpectrumLED (V1), so I came up with a simple solution: I built the Articulating 70W Spectrum-Balanced LED Panel, which has the perfect spectrum for my needs, and has a dimmer that controls only the total brightness. This was a HUGE success!
However, I noticed that when taking pictures, making sure that all of the lights that shine on the object emit the same color temperature is really important. This is something that is fairly difficult to do with SpectrumLED (V1), considering the amount of times that I change brightness, without wanting to change the spectrum... I'm also not that satisfied with the articulating arm - it didn't turn out as well as I thought it would: it's either too loose and shakes, or too hard to change from position to position. This might not sound like a big issue, but since it isn't counter-weighted, I have to tighten the tilting bolt (the base) extremely tightly. The other arms also aren't that simple to adjust.
As you can see, the combination of both of them wasn't as good as I thought it would be, so my first thought was to replace SpectrumLED (V1) with another articulating spectrum-balanced LED panel that I would build, which would give me what I wanted. However, I still wanted the option of changing the spectrum, and I didn't come this far only to come this far, so in this 21 step Instructable, I will show you how I made SpectrumLED V2.0 - The World's Most Over-Engineered, 80 Watt Variable Spectrum LED Lamp. I will also show you how to make an wooden articulating arm that contains 5 degrees of freedom, meaning that it both swivels and tilts in two different places, and telescopes. The arm is balanced by a unique counterweight, which provides an incredibly smooth tilting action (more on that later :).
-
(Watch the YouTube video: LINK FOR MOBILE VIEWERS!)
-
SpectrumLED's features:
• Variable spectrum made easy with switches! ✓
• Uses a Non-Flicker Dimmer (better for cameras, doesn't give headaches, simpler than CC) ✓
• Energy saving light output with 8X10W LED's (equivalent to ~500W incandescent lamp) ✓
• Has a balanced articulating and telescoping wooden arm (5 degrees of freedom), and can be adjusted to different positions WAY faster! ✓
• Reaches almost every part of my room (for example, even under my table in this video) ✓
• Can be built with fairly basic tools ✓
• Very low cost to make (*Ahem*, PERFECT FOR YOUR BUDGET!) at $6 ✓
• Looks AWESOME! ✓
I will be giving away free Instructables memberships to members that make their own SpectrumLED V2.0. Will you be the first one?
Let's get started!
Step 1: The Plan
As you can see above, this was the plan that I made. It took me over 2 weeks to come up with this design, since every time that I thought I finished it, I had another idea for improvement. While building, I made only a few changes, which I will explain later.
Below are the three main mechanical differences (others were explained in other steps/the intro) between this one, and the mechanics of the articulating arm that I built for the 70W Spectrum-Balanced LED Panel:
The Counterweight - I added a counterweight (transformer that was salvaged from a microwave) because I don't want to have to tighten the bolts down really tightly, which causes some problems. It also makes it easier to change from one position to a different one, reduces the stress on the mounts, and more. In addition, if a bolt failed because of contraction of the wood, or any other reason, the lamp would fall onto my table slowly, and would not wake me up in the middle of the night. Ask me how I know that...
The Adjustable/Telescoping Stand - I don't think I'll need a big articulating arm where I'm going to mount it: most of the time, I don't need to make the light reach a far place, so I fold them, and they get in a the way a bit. Also, 3 articulating segments aren't enough, and 4 are awkward to use. I can also turn it, so I don't need to make an additional swiveling mechanism for the top. The telescoping arm that I salvaged from a fan stand swivels, and also makes it easier to connect to the counterweight.
Don't have an adjustable fan mount? An adjustable handle from a mop stick, a selfie stick, and an leg of an old tripod are all good alternatives.
The Plywood Discs - I decided to use two thick plywood discs for the swiveling part, instead of two intersecting pieces of wood, which is what I used for the articulating spectrum-balanced LED panel. The discs eliminate 90% of the wobble (bigger surface area + thick and hard plywood), and most importantly, provide a fixed amount of friction. They will also self polish themselves over time, meaning that probably in a few weeks, they will feel almost like glass. After seeing how well these work, I'm considering to do this to the tilting mechanism too! Thanks to Matthias Wandel for the idea.
And...The Difference in the Amount of LED's - I had quite a few decisions to make with this, but for short, with 3 warm LED's, and 5 cool LED's, I can have a pretty substantial light source with each spectrum, along with getting an option for the exact same spectrum, or significantly cooler or warmer than the 70W spectrum-balanced LED panel, which was the main reason.... They also draw the maximum amount of current that my dimmer can supply, and fit perfectly on the heat sink that I chose, as you can see in the pictures.
Step 2: What You'll Need:
Below is a list for everything you'll need to complete this project. The parts are either ones that I already had (found/salvaged/made for another project/etc...), or bought (on eBay). If you don't see something that you think should be here, or would like to know more about a specific tool/part that I used, feel free to ask in the comments.
I built it for $6 since I already had almost all of the parts, but if you're planning on buying everything (tools excluded), I think that it would cost you around $50
-
Hardware & Materials:
- 5 Cool-white 10W 12V LED's
- 3 Warm-white 10W 12V LED's (they're better than the ones that I used before - they light up more evenly, and don't have a pink-ish tint, as far as I can tell so far)
- High-speed dimmer
- European Beech wood (bigger the articulating arm = more wood...)
- A large CPU/Active heat sink (w/ a fan)
- 12V Power supply (10 amps or more)
- Bolts w/ nuts
- Wires
- Shelf brackets
- Alcohol swab
- Screws
- 5 Toggle switches
- Plastic container
- A microwave transformer
- Birch-plywood
-
Chemicals & Adhesives:
- Thermal adhesive
- CA glue
- Wood glue
- Vaseline
-
Tools (+Attachments):
- Wave - The world's best soldering helping hands vise (PCB's)
- Drill bit set
- Pliers
- Clamps
- Homemade wooden vise
- Measuring & marking tools
- Multimeter
- Japanese saw
- Scissors
- Wire cutters
- Snips
- 80mm Hole saw
- Knife
- Hammer
- Calipers
-
Electric/Power Tools:
Subjects: Woodworking, Electronics, LED's & Lighting (& a bit of physics, of course!)
Recommended Safety Equipment: Earmuffs, Respirator, Safety Goggles, Gloves, Ventilated environment
Approximate Time: 50-100 HOURS (aka 2+ months)!
Difficulty: Fairly Hard
Step 3: Choosing a Proper Heat Sink (or More!)
You'll need a big active heat sink that has enough surface area for all of the LED's, and has a built it fan. This can be salvaged from an old desktop computer.
I also recommend adding 2 pipe heat sinks (I salvaged mine from old ATX power supplies), which are glued to the side of the main heat sink, since you can never had too much passive cooling. I glued the heat sinks together with thermal paste, and then added a few clamps.
Note: If you see another heat sink in any of the pictures, ignore it. I thought I would need another heat sink (which I glued onto the main heat sink), but eventually removed it.
Step 4: Glue the LED's Onto the Heat Sink
A task that takes only a few minutes to do can take half an hour to fix when skipped, so after making sure that none of the LED's were defective, I made sure to arrange them in a way that makes sure that the negative (-) side of all of LED's faces the center (inward). This will make the future soldering process easier.
I cleaned the heat sink with an alcohol swab, and then put a pea sized drop of thermal paste onto the back (aluminum) side of each LED, and squeezed it tightly onto the heat sink.
Now while making the Instructable, I realize how I could have arranged them ( a bit) better, but I don't think it'll matter, since I'm planning on adding a diffuser anyway.
Step 5: The Heat Sink Mount & Tilting "Head" (1)
After brainstorming quite a bit, I came up with an idea of drilling holes into the heat sinks, and screwing on shelf brackets, which get screwed onto the articulating arm.
I drilled two holes into each side of the heat sink and screwed in small wood screws. There even were some holes on the heat sinks that matched the holes on the shelf brackets, so it saved me some time. Lucky coincident!
The two other heat sinks that were glued onto the main heat sink also make it more rigid, increasing the strength of the, easier to mount.
As you might remember, I wanted to be able to tilt the heat sink, so I clamped 3 pieces of wood in my homemade wooden vise and cut them to the size that I wanted. One broken vise and a few screws later, I applied some CA glue to glue them up, since this is an adhesive that cures really quickly. I then drove in four small screws, connecting the wood to the shelf brackets. Don't forget to drill pilot holes!
Unlike my first articulating lamp, the heat sink was connected to the articulating arm in a way that helps dissipate the heat better. Hot air wants to rise, so making the heat sink open on the top is beneficial!
Step 6: Making the Telescoping Stand Easier to Mount on the Tilting "Head" (2)
I needed to connect the telescoping stand to the tilting mechanism that I was planning on building. It needed to be strong.
I cut down two pieces of wood to a little over 8cm, and then clamped them together tightly in my vise, along with a bar clamp. I used a 25mm spade bit to drill a hole in the endgrain, as shown one of the pictures (Sorry for the poor lighting - I had to use my flash, since I still had to unplug the articulating spectrum balanced LED panel, since operations like this one need a lot of power! Don't worry, this issue has been fixed with magic called an extension cord ;)
I didn't do it before Drilling so now was the time: I drilled two holes, and drove in two screws to secure both pieces of wood together. I did this in the vise so I wouldn't have to waste time afterwards trying to align the pieces correctly.
Well... Change that to seven screws since I added another two to the first two, then had the idea of using even two more small screws as shims for the adjustable rod, and then added another screw, which works the same as a pin that goes in a motor's shaft. I can pick up my table with this!
After doing all of that, I decided to tighten on of the screws even more. This was a big mistake, as the wood split open before I was even able to blink. So... I squeezed some CA glue into the hole, and clamped it really tightly in my metal vise. Hopefully this will hold up (the crack was only bad in terms of aesthetics, though)
About one week later: Wow! Unlike what I thought, this still hasn't failed!
Step 7: The Tilting Part of the "Head" (3)
Connecting part 1 and part 2 together. This makes part 3, in a way that's even better than what I made for the plans!
First, I screwed screwed a small block of wood onto the wood that was connected to the shelf brackets (in part 1). It will act as a spacer for the other piece that is need for the tilting mechanism.
I cut a another small piece of wood, which will be used for the top half of the tilting mechanism. After that, I cut two narrow pieces of wood to a length of 9cm. I then drilled a hole in all three pieces, and found a bolt that was just big enough for the holes.
I tried to connect the piece of wood that was used for the top half to the "head" (AKA the heat sink mount) with screws, but the screws stripped, so I used a different hole to assemble (almost!) everything together. I added a few washers, since the screw was a bit too long, and I didn't want it to come out of the other side.
To finish it off, I drove four more screws, connecting the small 9cm pieces of wood to the piece of wood that is connected to the telescoping stand. Don't forget to drill pilot holes! :)
This has probably been quite confusing to read (and to write!), so make sure to look at the pictures!
Step 8: Making the Telescoping Stand Easier to Mount
I found a big piece of wood, which I used both for my homemade wooden vise, and for the articulating spectrum-balanced LED panel. I used my saw to cut it down to two pieces that were both 10.5cm long
I drove in two big screws to connect both pieces together, and then marked where to drill (according to the holes that were on the bottom of the telescoping stand), drilled pilot holes, and drove in metal screws.
Did I tell you how much I want an impact driver?
Step 9: Making the Big "Bar" (main Tilting Part: Part 1)
The part that has been screwed onto the telescoping stand connects to the main tilting part of the articulating arm. It has to be really strong because of the (leverage/torque?*) that is applied onto such a small surface area from of the of the weight of the head.
I started by gluing two long pieces of wood together with wood glue. I've used the same piece of wood for the articulating arm of the spectrum balanced LED panel, and since I'm gluing two pieces together, this should be really strong. I added many clamps to make sure that the pieces would bond properly.
Should this be called a bar or a beam? Maybe something else?
*Sorry for not learning this in a physics class that I don't go to :)
Step 10: Connecting the Telescoping Stand to the Big Bar
After the glue had dried in the big bar, I clamped it to the bottom wooden part of the telescoping stand so it wouldn't move. I put two shelf brackets on the top, two on the bottom sides, marked where to drill with a pencil, and finally, drilled pilot holes.
To help drive in the big screws, I dipped them inside of Vaseline, which helps lubricate them, and lower the friction.
Step 11: Finally! the Tilting Mechanism! (Part 2)
I decided to go with a 10mm bolt, since while experimenting, I found out how amazing carriage bolts are, and I had one that was 10mm in diameter. Also, if I ended up not liking them, I had several other 10mm bolts in my collection, meaning that I would be able to replace it easily, if needed.
I clamped the main structure tightly onto the table of my drill press, and used a 10mm drill bit to drill a hole all the way through the big bar. I then found 2 more beech wood pieces, clamped them together, and drilled a 10mm hole in them too.
Assembling it was a piece of cake!
I should add that the bolt is tightened so I have the minimum amount of friction that is needed to tilt the arm. I need a bit of force to start moving it, but when I stop pushing, the arm stops (see the video, even though I haven't had the chance to adjust it to the perfect amount).
Step 12: STOP! Here's What I've Done So Far...
Are you a bit confused? No need to worry!
Here is a quick video showing what I have done till this step:
Step 13: The Counterweight
For the counterweight, I decided to use a microwave transformer. Yes, a microwave transformer. You're saying you didn't know I collect these? :)
The one I chose weighs a little over 3kg, and from my experiments, placing it about 30cm away from the bolt of the tilting mechanism works well.
I quickly cut two pieces of wood to 12.5cm long, and screwed them onto the transformer. While the whole articulating arm was clamped tightly in my wooden vise, I clamped the transformer to the big bar really tightly, drilled two pilot holes, and drove in some screws. I cut off the excess wood that was left.
Some more ideas:
You can build a track and make the transformer slide on the big bar, for adjusting it even more. I think I'll go with putting a knob on the main tilting mechanism - way simpler!
I might replace this with a (or add) pneumatic/hydraulic piston in the future, though I'm not sure if the one I have is strong enough.
Step 14: The Swiveling Base (1)
As I believe I've already mentioned, I will be mounting SpectrumLED (V2.0, of course!) on a shelf that's near my desk. This is where SpectrumLED V1 has been mounted for the past couple months (see the last step for a picture of that)...
When I cut the two pieces that connect to the main tilting mechanism and the swiveling base, I wasn't sure how long to make them, so I cut the pieces too long, just to be safe. I experimented with the stand a bit, and thought that making it so the bolt of the main tilting mechanism sits at about 25cm over the shelf looked good to me. Since the swiveling mechanism will be a few centimeters high, I was even able to cut the pieces even shorter that what I marked.
I started by mounting an 89mm hole saw in the chuck of my drill press. I drilled four holes in what I'm pretty sure is Baltic-birch plywood, giving me four disks.
To prevent tearout, I recommend drilling from both sides. Any tear out that I did end up having was then removed easily with a sharp knife.
The reason I made four disks was because I didn't have any thick plywood. I glued two discs together to make 2 thicker ones with wood glue and CA glue, and clamped all of them together, while using a drill bit to keep them aligned as best as possible.
Here are some more tips for drilling with a big hole saw: https://www.instructables.com/id/Drill-Powered-Tool...
Step 15: The Swiveling Base (2)
Similar, but not exactly what I drew out for the plan, I screwed the leftover piece that I had from the big bar (the counterweight part, remember?) onto one circle, and drilled a hole in with with a 6mm drill bit.
I then repeated the exact same process with another piece of wood (the one that gets clamped onto my shelf for mounting SpectrumLED V2.0), and then found a bolt and a nut that fit.
Remember the the two pieces that connect the main tilting mechanism to the swiveling base? I cut part of them to the length that I wanted, and connected them to the swiveling base with 4 screws. I messed up a bit with drilling part of this step, but there's no need to bore you with the details :)
I cut off the excess wood that was left.
DONE!With the articulating arm...
Step 16: The Switches, & Soldering Them
What's the most efficient way of turning different LED's on and off?
From right to left:
Switch #1: Turns on 1 warm LED
Switch #2: Turns on 2 warm LED's
Switch #3: Turns on 2 cool LED's
Switch #4: Turns on 2 more cool LED's
Switch #5: Turns on 1 cool LED
Want to turn on one LED? Turn on switch #1. Want to turn on two LED's? Turn switch #1 off, and turn on switch #2. Want to turn on three LED's? Turn both switch #1 and switch #2 on.
Since these switches were salvaged from old electronic appliances, I made sure to test that they work, with the continuity function that's on my multimeter.
Soldering: I found a thick speaker wire, spliced of the insulation, and soldered it to the "0" (aka "off") side of each switch. This is not very easy to do, so I recommend doing it on a PCB if you aren't planning to put them in an enclosure. This should save you a lot of time.
Step 17: Soldering the LED's (1)
I removed the insulation from some more speaker wire, tinned it, and soldered it to the negative side of the LED's. See why gluing them this way makes the soldering process easier?
Soldering gives me awful nausea, so I solder outside. Unfortunately, it was practically freezing outside, so don't judge me by my solder joints ;)
Step 18: The Switch Box
I decided to go with a plastic enclosure for the switches. The container I used is probably around 40 years old, and was made in England for Kodak. I think that it was used for something that relates to films - you tell me!
Each switch is about 1.9cm by 1.3cm, so by connecting them together, I needed to cut a hole that was about 1.9cm by 7.2cm. I marked it with a caliper, and then cut it out with a utility knife. A hot knife would have saved me a lot of time...
I also cut a small slot so the wires could pass while the box was flush with the surface of what I made in step #8.
Step 19: Soldering the LED's (2)
First, I soldered a long wire to the positive side of two warm LED's, and soldered another different long wire to the positive side of another warm LED.
I then found 3 more long wires. I soldered the first one to two cool LED's, the second one to two more cool LED's, and the third one to one cool LED.
Does that bold help?
I soldered the switches, from right to left, similar to what I showed in a previous step:
Switch #1:Turns on 1 warm LED
Switch #2: Turns on 2 warm LED's
Switch #3: Turns on 2 cool LED's
Switch #4: Turns on 2 more cool LED's
Switch #5: Turns on 1 cool LED
Since I had the articulating spectrum-balanced LED outside, I tested the LED's and... IT WORKED!
So... I turned on my hot-glue gun, and glued the switch box to the big bar.
Notes:
In case you're wondering since I didn't provide a schematic, when all of the switches are in the "on" position, it's as if I soldered all of the LED's in parallel.
When I don't extend the telescoping arm to its maximum length, the wires fall to the side. If you have an idea for making some kind of dispenser that will hold them, I'd love to hear it!
T̶h̶e̶ ̶f̶a̶n̶ ̶-̶ ̶S̶i̶n̶c̶e̶ ̶i̶t̶'̶s̶ ̶p̶r̶e̶t̶t̶y̶ ̶c̶o̶l̶d̶ ̶n̶o̶w̶,̶ ̶I̶'̶m̶ ̶s̶t̶i̶l̶l̶ ̶n̶o̶t̶ ̶s̶u̶r̶e̶ ̶w̶h̶a̶t̶ ̶I̶ ̶w̶a̶n̶t̶ ̶t̶o̶ ̶d̶o̶ ̶w̶i̶t̶h̶ ̶t̶h̶e̶ ̶f̶a̶n̶.̶ ̶I̶ ̶w̶a̶n̶t̶ ̶t̶o̶ ̶m̶a̶k̶e̶ ̶t̶h̶e̶ ̶f̶a̶n̶ ̶t̶u̶r̶n̶ ̶o̶n̶/̶o̶f̶f̶ ̶w̶i̶t̶h̶ ̶t̶h̶e̶r̶m̶o̶s̶t̶a̶t̶s̶,̶ ̶a̶n̶d̶ ̶i̶f̶ ̶I̶ ̶d̶o̶ ̶d̶e̶c̶i̶d̶e̶ ̶t̶o̶ ̶d̶o̶ ̶t̶h̶a̶t̶,̶ ̶y̶o̶u̶ ̶s̶h̶o̶u̶l̶d̶ ̶s̶e̶e̶ ̶i̶t̶ ̶i̶n̶ ̶a̶ ̶f̶u̶t̶u̶r̶e̶ ̶I̶n̶s̶t̶r̶u̶c̶t̶a̶b̶l̶e̶.̶ ̶I̶f̶ ̶I̶ ̶d̶o̶n̶'̶t̶,̶ ̶I̶ ̶w̶i̶l̶l̶ ̶p̶r̶o̶b̶a̶b̶l̶y̶ ̶d̶o̶ ̶w̶h̶a̶t̶ ̶I̶ ̶d̶i̶d̶ ̶t̶o̶ ̶t̶h̶e̶ ̶a̶r̶t̶i̶c̶u̶l̶a̶t̶i̶n̶g̶ ̶s̶p̶e̶c̶t̶r̶u̶m̶-̶b̶a̶l̶a̶n̶c̶e̶d̶ ̶L̶E̶D̶ ̶p̶a̶n̶e̶l̶.̶ ̶S̶e̶e̶ ̶m̶y̶ ̶r̶e̶p̶l̶y̶ ̶t̶o̶ ̶T̶h̶e̶H̶o̶m̶e̶s̶c̶h̶o̶o̶l̶H̶o̶u̶s̶e̶ ̶i̶n̶ ̶t̶h̶e̶ ̶c̶o̶m̶m̶e̶n̶t̶s̶ ̶s̶e̶c̶t̶i̶o̶n̶.̶
EDIT: I've updated (added more pictures) to the I'ble a few days after uploading it, so if you're wondering what's with the fan, I replaced the fan of the main heat sink to one that spins faster, and runs WAY quieter! While I was doing that, I also added a tiny fan for cooling the dimmer, since gluing another heat sink wasn't enough... It's amazing how silent they are!
Step 20: The Dimmer
I started by connecting two speaker wires to the output of a 12V power supply, which I then connected to the input of the high speed dimmer. I then I connected the negative and positive wires that came from the switch box to the output of the dimmer, and after I made sure that everything worked properly, I hot glued the dimmer to the big bar, next to the switch box!
Regarding "burning up the LED's in seconds" (I get these types of comments a lot): These LED's are being undervolted, and are kept at a cool temperature (aka the resistance shouldn't keep increasing to the point where they kill themselves). I fail to see why I should use an expensive constant voltage (or was that a constant current driver?), when I can use a simple dimmer.
DONE DONE DONE DONE!
Step 21: Done!
PERRRRRRRRRFECT! Perfect, perfect, perfect, perfect, PERFECT!
Click "Show More" to see more pictures, and in case you haven't already seen it, here's the video.
As you can tell, this has been a HUGE project, and Instructable, so I'm sure I missed information about stuff you might be interested in. If you have any questions, or would like to know more about something, don't hesitate to post a comment! :)
Liked the Instructable? 


Are you following me on Instructables? Join 1000+ members that don't miss my future Instructables by clicking the Follow button! (located at the top of my member page)
For more projects similar to this one, check out my other (80+) Instructables.
You can also check out my new YouTube Channel! Over there, I upload quick videos of my projects in action, and more - Subscribe!
If you made your own SpectrumLED, what special features would YOU add?
-
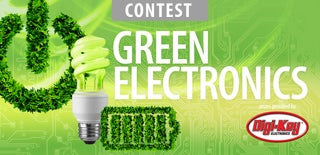
Runner Up in the
Green Electronics Contest 2016
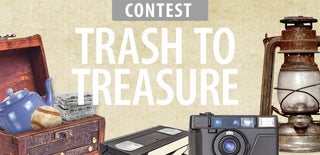
Participated in the
Trash to Treasure Contest 2017
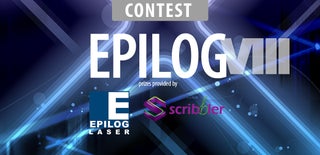
Participated in the
Epilog Contest 8
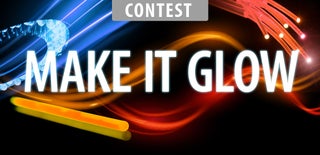
Participated in the
Make it Glow Contest 2016