Introduction: Stainless Steel Doors
So in this instructable, I am going to show you how to make stainless steel doors. So this is definitely not a new idea for making doors out of stainless steel but the different thing is that I am going to build it without tig or MIG welding, not because of a challenge, but in reality, I really don't have those machines. But I personally think that for building something out of limited tools the only thing you need the determination, which I think plenty enough in my body. So I made this project with stick welding and that was really a challenge for me. Because usually, their wall thickness is not enough for stick weld. Most of the times there are chances of metal warping and blow holes but if you are going with stitch welding then you get better results rather then the long welds. If you think that any of my statement has no weight than I think you have to give one shot to stainless steel project and try to finish it with stick welding. I am working with these metals for almost 2 years, even then I am not perfect in the welding of stainless steel with stick welding, although there was no slag visible onto my project, there is still lack of finish in the joints. Although they shine like what it has to be but I personally think that there is a lot more to learn still in stainless steel welding. I made a couple of projects in the past and as the time pass on I saw little bit improvement in my builds. I think that's called an experience which only achieved by giving something some time. So that's all about this build and if you like this build than make sure to leave your feedback in the comment section down below. If you want to share your experiences than leave them as well I am definitely interested in them. Along with this project I use all the basic safety equipment which are required to build this project, if I missed something then I didn't have that.
Step 1: Material and Tools Used
For cutting down the material most of the time I use the chop saw and but I think you can do all that with the angle grinder as well as its most versatile tool in making but you have to be careful with that. I didn't use it with guard but not recommend you to do that. Always Use proper safety equipment while using power tools. For the material, I use ss202, since these doors remain under a shade and I think they have very less contact with rain that's the reason I choose ss202. I go with 3 different dimensions of the material, but this thing completely depends upon your requirements. I don't want these to be too heavy that's why I go with 1” dimension in the thickness of the pipe, the width varies according to the need.
For the mainframe, I use 1"X 3" pipe, for the middle design I use 1" X 2" section and for the support structure of the sheets, I use 1/2" square pipe. The sheet cut to the custom shape with the help of an angle grinder depends upon your design. The main frame is welded together with but joints and all of the interior 1/2" square pipes are connected with the miter joint.
For the inserts, I used Brazilian ipe wood as an insert. I wanted to make CNC inserts But at the time of this build my machine gave up. Although the plan was to make V carve inlay and fill that with the glow in dark resin but in the end, it wasn't succeeded
Tools Used:-
Following are the list of tools I used in this build. Tools might subject to change according to your need.
1.
Angle grinder 4 inch
https://amzn.to/2P0qYWL
2. Bosch grinding wheel
https://amzn.to/2OZw4T4
3. Cutting wheel
https://amzn.to/2RbEgRE
4. Bosch Chop saw
https://amzn.to/2OZuvnW
5. Weld cleaning gel (Pickling gel)
https://amzn.to/2RcV8HN
6. Buffing wheel
https://amzn.to/2Ra2vQ9
7. Steel polishing Compound
https://amzn.to/2xQcTnY
8. S.S welding Rod
https://amzn.to/2DHUpeW
9. Welding Helmet
https://amzn.to/2DHUZcC
10. High-speed drill bit set
https://amzn.to/2P0nkfc
11. Heavy Duty C clamp
https://amzn.to/2OWIv1T
12. Arc welding Machine
https://amzn.to/2DIUsai
13. Hand drill machine
https://amzn.to/2xNYlp3
14. Chipping Hammer
https://amzn.to/2Rdhqcu
15. Weld brush
https://amzn.to/2OZbQZH
16. Quick locking Welding clamp
https://amzn.to/2R6iFdn
17. Heavy duty welding Magnets
https://amzn.to/2OWLjvX
18. Cordless drill
https://amzn.to/2R8KJwN
19. Respirator Mask
https://amzn.to/2NcFSqT
Step 2: De-Burring the Edges
There is one disadvantage of using a cut-off wheel is that it creates sharp edges and to make a better joint you have to deburr all the ends.
Step 3: Welding the Basic Skeleton
Since the height of the doors is near about 7ft that's why my sawhorse came very handy. I have plywood pieces with which I create an 8ft long table. Then I lay my pieces onto the work table. I clamped one side to the table since I didn't have big deep clamps I decided to make jigs which holds the pieces to its place so that during the welding if any warping occurs those clamps help to prevent that warpage. After that check then with the help of square because if this went wrong it would be difficult to correct that mistake unlike the wooden doors we can easily trim down the excess with the help of planer or some other tools but in Stainless steel pipes this wouldn't be possible. So always kept some margin while making metal doors. Then I first tack weld all the corners and then check the squareness of the frame and everything seems ok. Then I started the work onto the the square which are going to held my inserts in them. Here I prefer Miter joint to make it look more clean and smooth. I didn't do the complete weld on these squares as well. Then I lay pieces into the door main frame and make them square to the side and start the tack weld process. I flip the frame to the other side and tack weld from backside as well.
Step 4: Finalising the Welding
once the tack weld has been done on both sides of the frame I check the squareness of the frame and then stop the welding. At this point one thing has to be note down that if you are welding thin metal then never go with continuous weld beads because if you do so then you might end it up a blowhole in the material with the stick welding. Generally tig welding is used for stainless steel work since I don't have that that's why I used stick welding. For the welding I used stitch welding technique in which I made a tack and stop for a second and then tack again and so on. So what this thing does is that when you take a break after each tack then it gives the metal sometime to cool down and in next tack, there would be no problem. I follow this technique on all joints and complete the welding work. You can see in the images that how those tack welds are done. Since I have a requirement of two doors I do the same thing with both of them.
Step 5: Support Pieces and Sheet Cutting
Once the basic frame has been completed I start the work onto the decorating portion. I measured the dimensions of the top Plus sign and then transfer those measurements onto the Steel sheet having a thickness of 1 mm and then cut it with the help of angle grinder. During the cutting, I placed some scrap pieces of wood so that they did not damage the marble surface. For cutting the sheets I want to suggest you that instead of scoring lines over the surface was not a good idea rather than that you have to enter into the material from one side with the complete cut and then follow your marking lines. Buy this way there are fewer chances of the grinder to slip off. I cut down these sheets slightly undersized so that there would be no problem while tack welds them on to the door. To provide a structural support to the sheet I cut out some half inch square tube follow the profile where I am going to weld these sheets. For the visible area, I decided to choose mitre joint and the area where joints not visible I prefer simple but joint.
Step 6: Welding the Decorative Parts.
Once material has been cut down I deburr the edges and then start the welding process. For welding the sheets I have to first weld the support pieces and for that instead of going for long continuous weld I decided to go with some tack welds. In one of the door instead of installing the sheet I decided to weld some ½” square pipes in such a way that it looks pleasant to eyes. This thing makes it airy also. In the middle of the door I decided to screw a piece of ipe wood as its most dens wood and have no effect of water onto it as it's a rainforest wood. Initially the plan was to make a v carve designs into it and then filled it with the resin and I think that will definitely increase the beauty of this door. But unfortunately there are some issues occurred in my CNC as it started skipping the steps, it also break some of my precious v bits and because of that I decided to leave that part. In the second door I weld the sheet into the lower portion because I have to install this in a room and I don't want the dust to enter in the room. Until this time I decided not to remove the protective covering from the sheets as it gets the scratch quite easily because of the mirror finish onto it. Even if I am going to use newly buffing wheel with compound onto the surface it creates fine scratches onto the surface. Once the support braces has been welded on to the door design periphery I tack weld the sheet from back side as well and off camera I made some blow onto the sheets to check whether it holds up or not, but there is no change occurs into the material which is a good sign that everything works nice and sturdy.
Step 7: Buffing the Doors.
Since I am using stick welding that's why the weld beads or not that much good as compared to tig welding and also because of the temperature and the material thickness the joints are slightly wobbly. To remove most of the material I chose flexible grinding disk which removes most of the heavy weld beads. From my last stair railing project someone suggests me not to use these aggressive grinding disc onto stainless steel and I also not recommend those disk as well onto the stainless steel, but in my builds I not usually do it with too much aggression, just give it a light run onto the joint. Then with the help of 120 grit flap disc remove the scratches made by the previous disc. After that I switch onto the Scotch Brite wheel and give a good standing until it diminished the scratches created by flap disk. Once scratches has been removed I switch the wheel to the buffing one and with the help of green compound buff all the surface. Although I didn't get factory like finish onto some of the joints but at the end they are not noticeable from a distance of 1 ft and more. Buffing part is one of the most time consuming process in stainless steel builds. No matter how careful you are during the welding time the scratches came all over the surface and in the end you have to remove all of them to make it look more cleaner. In my case, I took 2 days to finish both doors and it's definitely a challenging task. Sometime it seems that finish has been completed then at some spot scratch become visible and then I have to move to remove that also.
Step 8: Finishing Touches
For the final finishing touches I welded 4 hinges each having 5 inches long spaced out roughly and then welded with the one side of the door, so that it will hang up to the door frame. To lock the door I welded latches as well. I welded them to the one side only. The handles are welded to them as well so that it became easy to open and close the door. There are some areas where it wasn't possible for the grinder to remove the slag, at that area I uses pickling agent to remove that but don't keep it for a long time as it corrodes the metal.
Step 9: Installation
Installation of doors is the easiest part of this build. There was a time when to me this seems to be the most difficult part of the doors build but when I install 6 doors of my house I completely mastered this technique and same technique I used to install these doors. Instead of welding the hinges permanently to the door frame I decided to use self-tapping screws. First, I placed A spaced underneath the door and fasten one screw to the top hinge and the one screw to the bottom hinge and then I remove the spacer underneath the door and then swing it. Once I satisfied with the alignment I fasten the rest of the screw as well and the result is in front of you. Once the door installation completed I install the wooden inserts to it and now it ready to use.
Step 10: Finally.
The final work is in front of you. If you have any suggestion for this then make sure to leave it in the comment section down below.
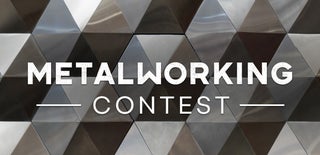
Runner Up in the
Metalworking Contest