Introduction: Stainless Steel Stair Guard Rail Build & Installation
Hello and the warm welcome to the instructable community. This my 16th instructable and in this instructable, I am going to build stairs hand/guard rail for my newly constructed upper floor. This is one of my biggest projects I have ever done it took almost three weeks to build.I saw various stairs railing on the internet and in my city, they are usually simple & assembled type also easy to install with the help of fasteners and have very limited welding work needed to build such type of railing.I want to make a unique stair railing for my upper floor, but there is a lot of challenges with the project. First, my stairs are not straight they are of L shape. Second, my stairs are made of Marble and granite & that is very hard to drill & brittle. Third, I have never ever welded any steel before also steel thickness is too thin for the weld that I realize when I started welding. Forth, the workplace is not safe for the work because Marble is slippery & a lot of time I have to go up and down on stairs & there are a lot of tools laying on my stairs also I have to weld in very discomfort positions.Fifth, Stick welding (308 weld rod) is very dangerous to Steel (Grade 202). When weld bead cools the slag over the bead pops up like a bullet and if it falls over your skin then it gives very bad burn marks.i have attached GIF image of Poping in Welding of Pillar section.Sixth, Also weather condition is not in favor of work. I have made this railing during this summer and I have to work in 47-degree centigrade temperature and a lot of sweat dripping from my body.but, in the end, my patience, skill & hard work turned simple pieces of steel tubes into a beautiful structure & I am very much pleased with my work.
If you like this overall build & have some suggestions for improvement then don't forget to leave your feedback in the comment section below.
Step 1: Tools Used
Following are the list of tools which we used in this build: -
1. Arc welding set
2. Angle grinder with speed regulator
3. Drill machine
4. Chop Saw
5. Center punch
6. Speed square
7. Measuring tape
8. Mallet
9.Chipping hammer
10. Table Saw
11. Miter Saw
12. Flap Disk (60,80,120 grit)
13. Scotch wheel
14. Buffing Wheel With buffing paste
15. Stone grinding diamond pad (60, 100, 200, 400, 800, 1200, 1500, 2000 grit)
16. Sandpaper (60, 80, 120, 220, 320, 400 grit)
17. Custom CNC20. 90-degree v bit for carving
18. Digital Vernier caliper
19. Cotton waste & rags
20. Marker
21. welding clamp
22. C Clamp
23. Hot blower
24.Combination square
25. Auto-darkening Welding helmet
26. Welding Gloves
27. Paint Mask
28. Diamond Core drill bit
Step 2: Guard Rail Design
For the design of stair guardrail from the beginning of this build, I want my own design. I don’t want to install anything which is prebuilt and just install onto the stairs. When I go to local shop to buy material for this build, I saw readymade posts and pillars for the stairs and some of them looks nice and some of them look too cheap, but that is enough to give me an idea of what design of post and pillar I needed for my build. I want a wow factor in my guard rails and wants to see them in dark too. That’s why I choose this design.
For the main post of the guard rails, I choose steel section at top and bottom covered with 4” square plate and in between them angled frame in which cnc v-carved inserts are added. For intermediate pillars for the guard rails which supports the handrail portion of them and make this build sturdier. Since I didn’t install pillars on every step, so that’s why I installed braces between those intermediates pillars. For braces design, before this, I am going to build a different type of braces, since at that time I am not familiar with the design. As soon as I came to know about the design I changed my plan because its way more difficult to do that thing with arc welding. Making clean weld with arc welding on wall metals is too difficult for me. After that, I build some more projects but still struggle I think if you are making the same thing with MIG or TIG welding you get a way better result. Don’t go with arc welding if you want a cleaner result.
Because It was quite a time-consuming build I divided this Instructables into two parts and following are the steps taken to build them.
1. Building of two main posts
I. Cutting of material
II. Remove burrs
III. Cutting wood for inserts
IV. CNC machining wooden inserts.
V. Filling with resin and finishing them to make a box-like structure.
VI. Welding the parts to make posts
VII. Grinding and finishing
VIII. Post Installation
2. Making of pillars and installation, installing handrail middle braces
I. Cutting material
II. Welding the Pieces
III. Making the anchors for the pillars
IV. Drilling the holes
V. Installation of the pillars
VI. Installation of handrail
VII. Installing the middle braces
VIII. Making CNC inserts and machined with 90-deg V-bit
IX. Filling inserts with glow in dark resin
X. Sanding, staining and finishing the CNC inserts.
XI. Installing the CNC inserts
XII. Finishing everything
Attachments
Step 3: Cutting Material for the Post
Since the complete Build is made out of stainless steel and these guard rails are not exposed to outside weather that’s why I decided to build this Project with SS 202 grade steel. Although It has less resistance towards the moisture.This will also reduce your project cost to some extent. If you are making something for the exterior purpose highly recommend building your project with ss 302 as it highly resistive to moisture.
I. 8” long 4 pcs of 3”X3”
II. 20” long 8 pcs of 1” X1” stainless steel angle
III. 4” X4” 8 pcs of ¼” thick stainless-steel plate
IV. 20” long ¾” thick 8 pieces of canadine pine wood
V. 2 sets of 4” dia phenyls
VI. 2 pcs of thread rod 4” long having 10 mm Dia.
One suggestion if you guys are using Chop saw with cutting disk installed in that, always make sure that don’t put too much pressure on the chop saw while cutting large pieces. If you do so you notice that your cut piece is not square. It may or may not happened with you but in my case, it’s happening every time. I think this thing happened because there is slight flexibility in the cutting wheel. To make sure that whether your piece cut in the square make sure that mark at least two sides of the workpiece one is parallel to the blade and other is perpendicular to it and make sure that both of them visible to you.
Step 4: De-burring Everything
To get clean weld joints I deburr every piece of steel with 120 grit flap wheels. With the help of same flap wheel, I slightly chamfer the edges to get nice penetration into the joints. In 4”X4” I slightly fillet the edges with the help of flap wheel in the angle grinder to get rid of any sharp edges in my build. After that, with the help of grinder and scotch, I lightly grind the angles because they have some rough textured over it. After getting these things done, these pieces are ready for the welding.
Step 5: Cutting Wood for CNC Inserts
Since I don’t have ¾” thick wood but I have 1¾” thick pine wood which I choose for this build. First I cut the wide board into the required width which I needed. This work is carried on my table saw. After I got my stock for required width I cut it in half from the center having a thickness of ¾” thick. By doing this I got 2 pcs from one thick piece of wood. After getting all pieces I sanded each piece first with 60 grits and then with 120 grit orbital sander.
Step 6: CNC Machining Wooden Inserts
After getting 8 pieces of 20” long wooden pieces I move on to my CNC. For the design, I chose simple vines design because I don’t have enough width. On CAD I traced vines image and then machined the wood using Mach 3. For machining the wood, I chose tapered engraving bits. My plan was to fill the machined area with resin. I machined the area up to the depth of 4mm. These engraving bits gives more detailing rather than end mill. You can also use v-carving bits. The more complex design less amount of depth is achieved by these bits. Since I have to machine same design repeatedly and I don’t want to screw my job that’s why I made this jig. I screwed couple pieces of scrap wood on the bed perpendicular to the bed and screwed two toggle clamps on opposite side. By doing this there will be no mark left on the workpiece and I have no need to align my job with the bed multiple time. Just insert those pieces into the machined area and start the machine. Jig makes my work a lot easier.
Step 7: Filling With Resin and Finishing Them to Make a Box Like Structure
After getting my machined pieces ready I prepared it for next step which is filling the machined area with resin. Before pouring the resin into the machined area I apply masking tape all around the piece and keep the machined area uncovered. During the machining process, I applied tape on these inserts but that thing didn’t get success. The masking tape keeps peeling off during the machining. It’s good to use vinyl’s which gives a better result than masking tape. After that, I mixed the resin and mixed some colored dye in it. Then spread it uniformly over the machined area. After allowing it to cure for 24 hours I sanded it completely with 120 grit sandpaper and clean the left-over residue with acetone. After cleaning everything I stained the wood. I gave it two-toned color. For one box I chose walnut and yellow stain. After staining it I make a box-like shape. I glued the pieces and screwed them to make it sturdy, once the glue dried I removed the screw and round over the edges with the round over bit. Since angles have a small amount of curvature in inside portion that’s why this roundness is needed in this box. You can make it round with block plane also. Just needed a small chamfer on all four sides. After that, I apply two coats of varnish over it.
Step 8: Welding to Make Post
Since I have to install these post on the surface that’s why I needed something to grab that post on the floor, so that post can stand straight onto the ground. For that, I cut 2 pcs of 4” long thread rod having dia 10 mm. I made holes in the 4”X4” square plate with the help of carbide drill bit, the high-speed steel drill bits didn’t work on this and then insert the threaded rod in the hole and weld it with the plate. Then I weld these pieces with the 3”X3” square tube for both posts so that I can anchor it to the floor. First, I tack weld on all 4 side when it seems good I complete the weld. I don’t make a complete weld. I just weld 2/3 weld on each side. After the block section completed with the help of Clamps, I wrapped angle around all 4 corners of the wooden box and make sure that it's completely square. To prevent the wood from burning I apply tape on the uncovered portion of the wood so that during the weld it provides little protection from weld spatters. I also kept a spray bottle filled with water which I use to keep my wood little moist so that it will not burn during welding and that thing helped a lot.
Step 9: Grinding and Finishing of the Post
Since I am using arc welding there is a lot of grinding work needed on this post. During the grinding work, I found some slag area in which weld is not done properly. In that case, I need to reweld that area. This is the portion in which I struggled a lot. Because of my first project, some weld joints which seems good from outside after grinding there are some small holes left behind. These welds can go for mild steel but in case of stainless steel, there should be a need for perfectly clean and shiny weld. For grinding first I grind off everything with coarse wheel then I move one to 60 grit flap wheels. I didn’t use it too much just barely use to minimize the scratches produce from the first wheel I used. Make sure that always grind in one direction, if you grind randomly than some scratches will be left out and difficult to remove. After that, I rind up to 120 grits with the flap disk. When scratches are completely diminished I grind with the scotch wheel. Finally, with the help of green compound and buff wheel shine all the weld joints and completed the post.
Step 10: Installation of the Post
Since my stairs are 42” wide and I have to maintain the same distance throughout the stairs. Then I measure the distance of 39” from the wall side mark the location then placing square along that point I marked 6” distance from the riser ( the vertical portion of the stairs called riser and lateral part over which we place our foot is called tread). By doing this I get the exact location where I need to drill hole. Since I have marble floor and I don’t want to produce cracks over the surface I used diamond drill attached in the grinder than make a hole into the surface. I use enough water to keep the bit cool during drilling. Since bit wasn’t too long that’s why I complete rest of drilling with the hammer drill. After that, I filled the holes with two-part anchoring grout and then insert the post anchor into the holes. To make it perfectly straight I apply some supports from two sides. Within a ½ hour, the anchoring grout completely dries and make the post very sturdy.
Step 11: Installation of Finials for Post
After the posts completely dry I completely buffed the top surface because after welding it's quite difficult to clean that area then I marked the center on the top of the post and weld a bolt over it which comes with that ball. First, I tack weld it on the plate and then make it perfectly straight. Then I complete the weld and slightly grind off the excess. Then I insert the cover plate and screwed the ball onto that bolt.
Step 12: Making Pillars for the Stairs
Cutting Material: -
After completing the first part I move onto the second phase, which is cutting the material for the pillars. Although there are the bunch of pre-built pillars available in the market but they are skinny, infect they are looking just a piece of pipe. But I want something different. Instead of a simple pipe, I made a design in which there is a rectangular shape is at the center & rectangular pipe connected at the top and bottom portion. In the rectangular piece, I have installed CNC inserts filled with glow in dark resin so that this thing visible in the dark too. The total height of the pillars is 36” long and divided into three sections: -
· Rectangular portion
· Bottom piece
· Top piece
I am not going to install pillars on every step and decided to build 5 pillars which I am going to install after leaving every two steps. For the joints of pipes, I choose miter joints. Here is the cutting list of material which I used to make pillars for stairs.
· 20” long 1”X2” rectangular tube 10 pcs.
· 9” long 1” X2” rectangular tube 10 pcs.
· 8” long 1” X2” rectangular tube 10 pcs.
Step 13: Welding of Pillar
After that, I clamped these pieces onto my temporary made workbench and clamped it securely onto my table and check the squareness of my rectangle with the help of speed square. Before that, I deburr those pieces. After that, I tack weld all the four side of the rectangle and repeat the process on the opposite side. Then I recheck my rectangle and then complete my welds. You see in the video that I am not going for through weld and this is because the material wall thickness is not thick. It's almost 1.76mm thick. If I am going for a through weld the end result was a blowhole. That’s why I am doing tack welds only. After that, I grind off the excess material. Then I marked the center of the rectangle and the pipes which I needed to connect with the shorter side of the rectangle. After that, I clamped these onto my workbench and check the squareness of the piece and tack weld. Then I complete those welds joint and create perfect seamless joints. I repeat these process five times and made 5 pillars of similar dimensions.
Step 14: Making Anchors for the Pillars
After making my pillars for the stairs I need something with the help of which I can install these pillars onto my stairs. Since there are no proper fasteners available for these kinds of work that’s why I have to build them too. For the anchor, I chose mild steel bar 6 mm thick and 40 mm wide. On that, I make marks after every 2” and then marked center where I need to drill. Then I first drill pilot holes with 4 mm bit and then enlarge with 10 mm bit. After that, I cut this bar to 2” long pieces. Then I cut thread rod up to a length of 4” long. Since I have folded stairs that’s why I don’t goo too much depth. The overall step thickness is 5”. If your steps are thick than make little larger anchors. Then I insert nut into the bolt just to provide support to the plate which I am going to weld it with the bolt. So that this provides surface to rest the piece over it during the welding process. After the welding done I remove that nut from the bolt because its no longer needed.
After making the anchors I insert the cover plate into the pillar and then attach the anchor piece to the pillar by keeping the threaded piece to the outer side. Than I First tack weld and then complete the weld joints. By doing this these pillars are ready to install.
Step 15: Drilling Holes for the Pillars
After making those pillars it’s time to install them. Since I am going to install them after leaving every two steps. The width of my steps is 41¾” having ¾” molding overhang at its side. That’s why I am drilling these holes 3¾” from this far end. Then I find the center of my tread and mark the point where I need to drill and the distance is 6” from the riser. After that with the help of diamond drill bit attached to the grinder and start drilling holes. To make it cool during the drilling process I continuously spraying water over the bit. I repeat this process for all the remaining steps. Then with the help of hammer drill, I slightly increase the depth of hole because my Dimond drill wasn’t long enough.
Step 16: Installation of the Pillars
After drilling holes I cleaned all the holes with the help of compressed air to remove all the loose dirt from the holes. If you don’t have an air compressor then you can also use vacuum cleaner too. Some grout has property to cure into the water too so if you don’t have any of them then by pumping water into the holes you can remove all the loose sand particles from the holes. I already cut the piece of handrail and used it to keep my pillars in the straight position until the grout dries. Then I mixed anchoring grout and filled the holes one by one. I installed another pillar after ½ an hour.
Step 17: Installation of the Handrail
Since I already cut the handrail piece but here is some information about that. For that, I used 1½” X 1½” stainless steel pipe as a handrail. I measure the distance from top post to bottom pillar where there is a turn. I keep the length little long because I am not sure about that. After that, I clamped the rail along those pillars and make sure that the rail is parallel to the stair angle. I clamped the pipe to the top pillar and measure the distance from the bottom of the step and then go to the last step and maintain same distance. By doing this the handrail becomes parallel to the stair step. Then I marked the area which I needed to cut so that I can place those rail over those pillars. Although the cutout angle is 56 deg. After marking those lines I cut the pillar top with an angle grinder and clean of them with the help of flap wheel. Then I clamped the handrail over the pillar and to connect the handrail pipe with the post I marked the area which I needed to cut to weld it with the post. By placing the rail over pillar top I marked a straight line at its end with the help of spirit level. Then I cut it with the help of the cut off wheel. After doing a little bit of cleaning I join it with the post by keeping it over the pillars with the help of clamps. Then I tack weld them and after it secured properly remove the clamps and complete the welds. Then with the help of flap wheel clean the weld joints.
This is the first part of the handrail and the next part is the L-shape portion. For that, I cut it at an angle of 14 deg. to make it horizontal then I tack weld that piece and continue my handrail. After a small distance, there is a turn in the stairs that’s why the guardrail also need to turn at 90 deg. From the bottom pillar, I marked the center position on this top handrail and marked where I need to cut miter angle. Then I tack weld them and after that make it permanent. This is generally hit and try the method. Because sometimes the working position is slightly different than the actual design. After that, I cut the L-shape at an angle of 38 deg. After that, I install the bottom rail pipe. The portion which needs to connect with the post cut at an angle of 55 deg to make it parallel to the stair slope. I also cut the top portion of the bottom pillar so the pipe can rest over it. This pillar is cutting little short than the rest of the pillar and I think this is because of the awkward design of the stair. Then I first tack weld and then complete the weld to make it permanent. After that, I clamped the piece between that gap and marked the lines which I needed to cut to make it fit into those gaps. After doing a little bit of adjustment I successfully installed that portion very easily and completed the handrail. Then I do grinding and finishing to make the joints smooth.
Step 18: Installing the Middle Braces
Because I install the pillars after every two steps that’s why there I plenty of gap in the guardrail. To make it more secure I planned to install braces between each pillar by keeping the same slope. Then I marked the points on the pillar where I am going to start those braces. These are made with ½ “X ½ “ square pipe. I measure equal distance from the top of the rail to the pillar approximately 10½ “down from the top rail. Then with the help of a 2½ “ long scrap piece of pipe I marked the equal distance on both the pillar and then measure this distance with the help of tape measure. Then I cut the one side of the pipe at an angle of 56 deg and then marked the total length of the pipe and cut the alternate angle on the other end up to the marking area. Then I place it on the marked point and tack weld. Repeat the process for the other. By doing the same procedure I install all the braces. I didn’t cut the material at the same time because at some points the length is slightly varied. I measure the distance and cut the pipe which I needed to weld in between those pillars.
The braces in the bottom portion are quite different because the situation is quite different than the remaining portion. On one side I can easily weld it with the pillars but on the opposite side, there is the woos, so that’s why I go with this design I measure the distance and cut it in equal length then I cut them at 56 deg angle on both sides. After that’s I cut a stainless steel bar having length 10½“ and then drill holes and countersunk those holes so that screw can sit into them. Then I weld those pieces with that bar by maintaining the same distance of 2½“ and screwed it onto the post and on the other side, I weld it by maintaining the same gap between each brace. I don’t have welding pictures of this portion because my phone shut off and I didn’t notice that and keep doing my work.
Step 19: Making CNC Inserts and Machined With 90-deg V-bit
For the cnc Inserts I have some leftover piece from my door build project and the width of the pieces is 5” wide. I cut them to the required length which I needed with the help of miter saw 16” long and make a test by inserting them into the pillars. The dimensions are very accurate for using them as inserts. After that I sanded those pieces up to 120 grit orbital sander and make them ready for the machining. Then I made a jig on my cnc table so that I can hold my job over it without any fasteners. After that I start machining those wooden inserts with the help of v bit. I carved some different design on each insert. Since I am a huge fan of batman I carved batman vs superman figure on one of the inserts. My main plan was to use different colors of wood but in my area its impossible to get those wood that’s why I decided to go for staining. By doing this I am able to get desired color which I needed for my build. I stained each insert with different color and then apply one coat of clear varnish over it. And there is a big reason toward that. When you are going to do resin art on wood than you will notice that small part of resin is absorbed by the wood and if you are going to re-stain that Its quite difficult to do that. Although I know that I need to re-stain it again once I fill the carving with resin. Without the resin these inserts still looking very beautiful.
Step 20: Filling Inserts With Glow in Dark Resin
After the staining work I covered the remaining part with masking tape so that less amount of sanding done onto the inserts. After covering with the tape, I make bunds on the insert where I am going to add different color resin. This thing is done with the help of glue gun. The glue kept the resin in its area until it cures. For the color I choose different color glow in dark powder which I am going to mixed in the resin then I added the hardener in the resin and with the help of blower removes the bubbles from the resin and then poured into the carving. Then I again het that resin with the blower so that there would no air bubble left inside. Same procedure done with the remaining colored resin. Once one side cured repeat the step for the back side first by making bunds and then following the remaining steps.
Step 21: Sanding, Staining and Finishing of the CNC Inserts
Once everything cured for 24 hrs. I sand it with 60 grit sandpaper because there is a lot of material to remove from the insert. After that sand, it with 120 grit and then sanded up to 400 grit. After 220 grit I do wet sanding and this will definitely increase the finishing of the carving. After sanding a lot of stain removal from the inserts that’s why I needed to re-stain them but before that, I need to dry it for few hours because I do wet sanding on them. If I wipe stain over the carved design then the small amount of color is absorbed by those design that’s why with earbud I stain them where there is very detail carving is done. After retouching them I apply two coats of clear varnish over them. The final piece is in front of you.
Step 22: Installation of CNC Inserts in Pillar
For the installation, I sanded the inside portion of the pillar with 60 grit sandpaper to make it rough so that epoxy has some rough area to stick. Then I clean the portion with acetone and mixed two-part epoxy. Then I apply that epoxy in the pillar and insert the CNC insert in it. There I some excess epoxy squeeze out and I wipe it with acetone. Repeat the process with remaining inserts.
Step 23: Final Finishing
At the turn, I install a small phenyl over it and it definitely increases the overall aesthetics of the guardrail. After that, I buffed the complete build with a buffing wheel and green buffing compound to give it mirror-like finish. The final build in front of you. There is another build I am currently working on. Although all the welding work has been finished and the only thing left is the CNC inserts. I am trying to use different techniques for this inlay. So stay tuned for this build too. If you like this build than don't forget to give your feedback, I really appreciate that.
Step 24: Finally
The final build in front of you. If you like this build than don't forget to vote & give your feedback, I really appreciate that.
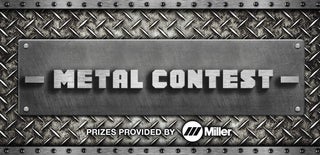
Participated in the
Metal Contest 2017
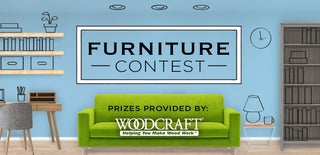
Participated in the
Furniture Contest 2017
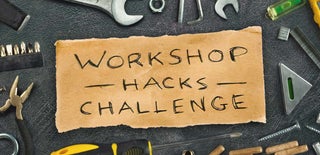
Participated in the
Workshop Hacks Challenge 2017