Introduction: Steampunk Raku Howl's Moving Castle
It's about time I posted some details about my epic ceramic project from the winter. The process was long, there were a few bumps in the road and a few scares but I finally finished my beloved castle and it's time to show it off!! I have had a love for ceramics and building whatever pops into my head out of clay ever since I took a ceramics class for my elective back in 2007. There is something so relaxing and fulfilling about building something with your hands that becomes a functional/beautiful permanent thing. My Howl's Moving Castle project began with a love for the movie itself. When I first saw Hayao Miyazaki's film, I instantly fell in love with the characters and the dreamlike story. Who wouldn't love a magical castle that transported you through dimensions?
The only tools I used was some basic clay, ceramic throwing tools like sponges and ribs and trimming tools. The most important tool you can have in this process is patience! Don't add too much in one day and make sure everything dries very slowly to prevent cracking.
I began the construction process by making the base of the castle and the upper part in two separate pieces so that I could make sure it was very stable and not too heavy. I planned on gluing them together after the Raku process. I began by hand throwing the bowl shapes and the cylinders for the top and the bottom and then over time, adding on hand made pieces. I used rolled up paper for the pipes so they would keep their shape.
I had to plan the piece very carefully so that it was not to big to fit into our Raku kiln and I also had to keep in mind that we needed to somehow pick up this molten hot piece of clay once it was done firing and move it to its reduction can. I made some handles for the sides and the back that would appear to be pipes and hopefully compliment the style of the castle. I wasn't able to find good photos of every side of the castle to know how to accurately reproduce every detail so I pretty much made some things up but the spirit of the castle was definitely there.
It is important to let the piece dry slowly and evenly. Too fast and cracks happen. This piece took about 6 months to dry and I added pieces in steps and then would wrap it as tightly as possible at the end of the day in heavy plastic wrap so it would dry very very slowly.
I after completely building all the pieces on, I let the entire piece dry lightly covered for a month until it was white and bone dry.
Before raku firing, we had to put the piece in a bisque kiln to get the rest of the remaining moisture out. If you don't do this, the piece will explode in the firing process. The piece was placed in the bisque kiln to dry for a week and then was turned on very slowly. Raising the temperature at a moderate rate so avoid any breakage since this is a very delicate piece. Once it is bisqued, it is ready for the raku process!
I painted various parts of the piece with raku glazes. Some where very shiny, others where crackly and others looked like slick oil. This brings the steampunk feel to the piece.
Usually a Raku piece is so small it is not a problem to just pick it up with the tongs but this castle was very large (the largest they have attempted to put into the Raku kiln) and needed THREE people to lift it out of the kiln and place onto the prepared sand pit where it was then covered with a metal trash can. Normally you would put the piece in a can and then the lid over it for the reduction process but in this case, we used a bucket for the base with some sand and newspaper inside and then put the can over the top.
You can watch the video process here. It's quite the sight to see especially when flames start shooting out the side like a jet engine!!
When we pulled the paper away and I saw that beautiful copper I almost fell over. The piece managed to make it through this whole process and didn't explode AND the color turned out perfect! All that broke was a wing when we put the can over the top right after it came out of the kiln. I managed to glue that on later and you can't even tell! I got so dang lucky on this one I couldn't believe it.
You can see how the different glazes came out so well. They still need to be cleaned up to show the detail but they are looking good!
I have entered this piece into the Oregon State Fair Art Competition. You can see it in person at the Hart of the Garden building where it is on display with a lot of other awesome artwork. Guess the judges are a fan of Howl too because I won first place :) It's nice when hobbies pay off isn't it?
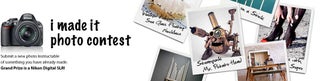
Participated in the
I Made It Photo Contest