Introduction: Strengthening Sun-dried Concrete Bricks While Reusing Discarded Plastic.
Concrete is a marvel. Most architectural wonders won't be present today if not for it. In my opinion, it is one of the greatest discoveries. It's strong and moldable. Studies show that a type concrete is capable of growing stronger over time, instead of weakening. We need concrete. It helps us.
Unfortunately, I can't boast so much about plastics. Sure, they can be useful, but what happens after use? They're disposed in landfills or rivers, polluting the world. In my opinion, the beauty of science and life is about taking something useless and making something great out of it. This was what I did. I used plastic( the type used in packaging) to make concrete even stronger.
We could turn waste into something useful and beautiful. This particular instructable involves making stronger concrete bricks for use in masonry structures and other aspects. Follow the step by step procedures to discover how you can better a product with no added cost.
Step 1: What You Need
Gather everything you need before you begin.
Ingredients:
-Sand. (Sand can either be white or red as long as the particle size is between 2mm to 5mm. I was able to get mine from a drainage near my home.)
-Cement. (Portland cement is best used. Can be gotten from a building materials store or ordered from online stores)
- Water. (With no added chemicals or grease.)
- Plastic packaging. (Preferably the disposed and unusable one. We see this everyday. It seals most stuff we see on the supermarket shelf such as biscuits, candy, chips etc)
Notice that I haven't written any quantitative figures. This means you can get as much as you want, depending on the scale of your project. I made mine on a very small scale, just so I can show the proof of concept.
Tools:
-A mould. (Any size will do. Considering we are making concrete bricks, a rectangular or cubical mould is preferable. This can bought in any building materials store)
-Scissors or blade. (Can be gotten from a hardware store or ordered online)
-A shovel or trowel.
Step 2: Shred Plastic Packaging
If you have a shredder, it should make quick work of shredding the plastic. A shredder isn't the best option because it may not get the packaging very thin. It needs to be thin and long. You can use a pair of scissors or a blade. Note that when doing this, the shreds should be long and thin. The longer the better. You can shred as much as you want, depending on the quantities of your other materials.
Once this is done, keep the shredded plastic packaging in a bowl and set aside. It shall come in handy later on.
Step 3: Mix Sand, Cement and Water.
On a flat surface, pour in sand and cement. Whatever quantity you use, make sure the ratio of sand to cement is 3:1. That means for every three cups/shovels/bags of cement you use, there should be one cup/shovel/bag of cement used. Mix thoroughly with a shovel or trowel.
Next, create a hole into the mixture and pour in water, slowly. The mixture should be repeatedly mixed until a moldable texture is achieved. This step is rather critical. Care should be taken when adding water. Too little water will make it crumbly. Too much will render it too soft.
Step 4: Divide Mixture, Add Plastic and Mould.
For the sake of comparison, you could make two different but identically-shaped bricks: One will contain the plastic and the other won't. It will be like a test experiment and a control experiment respectively. That way, you could compare which is stronger at the end. If you choose this approach, then divide the mixture in half. Fit one half into a mould of your choice using the trowel. Make sure to press level the top to avoid any air spaces in the mould. Leave under the sun to dry.
While it is drying, get the other half. Pour in the shredded plastic and mix thoroughly. The more you use, the better. Just don't overdo it. You won't want to end up with more plastic that concrete, will you?The next step is to put this into a mould. Don't worry if the plastic stick out. It could be trimmed later. But if this bitters you, you could always fill the mould in such a way that it doesn't stick out. This will require a level of expertise though. Keep under the sun to dry.
Step 5: Final Product
Depending on the size of your bricks and/or the amount of sunlight received, it should take a day to one week for effective drying. If you have plastic shreds sticking out, you're free to trim them off with a pair of scissors.
If you created the two different bricks (test and control), you can examine them and determine ways to test the differences in strength. Try dropping them from a height and see which one breaks first.
*My picture shows a closeup of the two bricks lying size by side once they were done. That on the left is the test brick and that on the right is the control. Notice that there isn't much of a physical difference. Mine was done on a small scale, reason why the bricks are so small.
Step 6: The Science: Why Does It Work?
It all comes down to propagation of cracks. When a brick or any breakable object is hit on one direction, it may crack. The crack easily spreads from one point to another because of a solid, joined structure, hence, causing the product to shatter completely.
By infusing plastic shreds into your concrete brick, you could halt the spread of cracks. If a crack occurs in one point, the plastic prevents it from moving farther. There's no way for the crack to go through. It's almost like seeing a red light or signalling 'stop'. Also, perhaps the plastics could also act as shock absorbers, sucking in the force of impact.
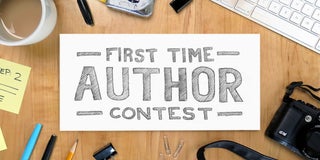
Participated in the
First Time Author Contest
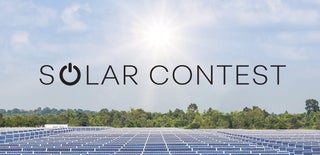
Participated in the
Solar Contest 2017
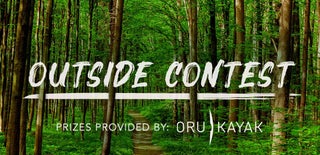
Participated in the
Outside Contest 2017