Introduction: The Arcus - Fully 3D Printed Rubber Band Gatling Gun
Winner of the Instructables 2016 3D Printing contest!
The Arcus is a fully 3D printable rubber band Gatling gun that is capable of delivering 48 rubber bands downrange in mere seconds.
Unlike almost all of the other rubber band Gatling guns out there The Arcus uses the energy from the rubber bands that it is shooting to spin the barrels. The Arcus also features the arm mount system, meaning that to hold it you put your arm through the center and the barrels will spin around your arm. A cam system is used so that when you pull the trigger the barrels will start the rotation.
All of the parts are designed to snap together, no screws or glue will be required, because of this it can be taken apart and reassembled as many times as you want. The only other thing used in the assembly besides the printed parts is rubber bands. All of the parts are designed to be printed without any supports, and all the parts will fit on a print bed of 200mm X 200mm. This assembly is designed to work with #64 Rubber Bands with six Rubber Bands loaded onto each firing block.
Here are some articles that have been written about the Arcus:
http://www.digitaltrends.com/cool-tech/rubber-band...
http://www.popularmechanics.com/technology/design/...
http://gizmodo.com/3d-printed-gatling-gun-fires-48...
http://www.3ders.org/articles/20160710-arcus-3d-pr...
http://www.guns.com/2016/07/16/3d-printed-gatling-...
My Settings for printing:
Printer: Ultimaker 2
Material: ColorFabb XT White
Layer height: .15mm
Wall Thikness: .8mm
Fill density: 25% (unless otherwise stated on the part name)
Nozzle size: .4mm
Step 1:
Print all the parts. The file name says the number of times that part is to be printed. Some of them also say a cretin fill setting, If it does not say a fill setting then it should be set to 25%. After printing clean off all excess burrs and bumps. All of the parts are designed to be printed in the orientation that they are set in the STL's
Before printing make sure that your printer is calibrated correctly and is printing true circles, the bearings will not work if it is off.
Attachments
All Parts zip folder.zip
Cam Wheel Holder-Print 1.STL
Cam Wheel-Print 10.STL
Cam-Print 1.STL
Clicky Ring-Print 1.STL
Core Bar-Print 4.STL
Firing Block-Print 8.STL
Front Inside Plate-Print 1.STL
Front Outside Plate-Print 1.STL
Grip-Print 1.STL
Long Screw-Print 2.STL
Outside Bar-Print 8.STL
Rocker-Print 8-50% fill.STL
Short Screw-Print 6.STL
Small Pin-Print 28.STL
Star Bearing-Print 8-100% fill.STL
Star-Print 8-100% fill.STL
Temporary Holder-Print 4.STL
Tip-Print 8.STL
Tool-Print 1.STL
Trigger Bar-Print 1.STL
Trigger-Print 1.STL
Back Bracket-Print 1.STL
Back Inside Plate-Print 1.STL
Back Outside Plate-Print 1.STL
Back Plate Top-Print 1.STL
Bearing Wheel-Print 12.STL
Big Pin-Print 8.STL
Brace-Print 8.STL
Cam Holder-Print 1.STL
Cam Pusher Holder-Print 1.STL
Cam Pusher Insert-Print 1.STL
Cam Pusher Spring-Print 1.STL
Cam Stick-Print 1- 50% fill.STL
Step 2:
Step 3:
insert 8 of the Bearing Wheels into the Back Inside Plate
Step 4:
Put the Cam Stick into the notch in the Back inside plate and then put the back outside plate over it.
Step 5:
Put the Back Plate Top onto the Back outside Plate and then put the clicky ring onto the posts of the back outside plate
Step 6:
Insert the Temporary Holders into every other hole of the Back outside plate. These will not be part of the final assembly but are needed now to hold everything together.
Step 7:
On the back insert the two Long Screws through the Back Bracket and then through the back inside plate, the slot in the Back Bracket must line up with the Cam Stick. Then insert two Short Screws through the other two holes of the Back inside Brace.
Step 8:
Insert one of the Cam wheels into the bottom hole of the Cam Stick.
Step 9:
Slide the Cam Holder onto the four screws, the Cam Stick must line up with the slot on the Cam Holder. Add a cam wheel to the top part of the Cam Stick.
Step 10:
On the Cam assemble the Cam Pusher Holder and the Cam Pusher Insert.
Step 11:
Insert the Cam Pusher Spring in the notches in the Cam and the Cam Pusher Insert. Push a Small Pin through as shown to lock the assembly together.
Step 12:
Insert 4 Cam Wheels into the side of the Cam Holder. Slide the whole Cam assembly over the Cam Holder, the Cam Wheel on the top of the Cam Stick needs to go into the slot on the inside of the Cam.
Step 13:
Insert 4 Cam Wheels into the last 4 outside holes of the Cam Holder.
Step 14:
insert the Cam Wheel Holder and then the 4 Core Bars. The Core Bars will only screw in on one end.
Step 15:
Install the Trigger Bar using a Small Pin. Make sure that the notch is pointing down and is at the back as shown.
Step 16:
Slide the Front Outside Plate over the 4 Core Bars and let it hang lose for now. The flat on the Front Outside Plate needs to be towards the back.
Step 17:
Insert 4 Short Screws through the Front Inside Plate and the Grip as shown.
Step 18:
Install the assembly onto the 4 Core Bars.
Step 19:
Use the printed Tool to tighten the four short screws.
Step 20:
Insert 4 Bearing Wheels into the holes in the Front Inside Plate. Slide the Front Outside Plate forward onto the Bearing Wheels.
Step 21:
Install the Trigger and connect it to the Trigger Bar using Small Pins.
Step 22:
Attach a Rubber band to the two notches on the Bearing Wheel Holder and the notch on the Trigger Bar.
Step 23:
Step 24:
Insert the Star Bearing into the Star.
Step 25:
Add the assembly to the Firing Block using the Big Pin. The pin will not snap into anything yet.
Step 26:
Insert the Rocker into the Firing Block and secure it with a Small Pin.
Step 27:
Screw in the Outside Bar and the Tip. They should line up as they are shown in the picture when the are fully screwed down.
Step 28:
Insert a Rubber Band between the notch in the Rocker and the front part of the Firing Block as shown.
Repeat steps 24 to 28 till you have all 8 of the Firing Block assembles.
Step 29:
Step 30:
Insert the Brace onto the post on the Back Outside Plate. The Brace has a short side and a long side, the long side needs to go onto the post of the Back Outside Plate.
Step 31:
Install the Firing Block Assembly as shown in the video.
Step 32:
Push a Small Pin through the Tip and The Front Outside Plate.
Step 33:
Push a Small Pin through the brace and the Firing Block
Repeat steps 30 to 33 until all 8 Firing Block assembles have been installed.
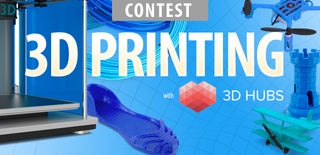
Third Prize in the
3D Printing Contest 2016