Introduction: The Fantastic Plastic CNC Mill
Being a woodworker all my life I welcome the opportunity to explore new materials especially ones machineable with most woodworking tools.I have a friend in the plastics fabrication business that has an endless supply of plastic cutoffs all I needed was a project and yet another opportunity to use my homebuilt cnc.
The main part of this project is a material called HDPE plastic or “puckboard”it is machine friendly and can be cut with hand tools as well.The bearing blocks and router mount are made with UHMW plastic that has much the same characteristics as HDPE.
Most of this project can be accomplished with a table saw.drill press and a generous supply of drill bits.
Step 1: Materials
These are some of the sizeable pieces they consider scrap The owner of the company only gets 3 cents a pound so go to a plastic fabricator and make an offer. The black material is the UHMW and is what we will be making the bearing blocks out of.All of the holes will be created using forstner or brad point bits as they are more precise and easier to align holes. In the case of the bearing hole where you only want to drill to partial depth the bit will leave a mark where to continue through with the smaller clearance hole.
Step 2: X-axis and Y-axis Bearing Block
Cut 2 pieces on the table saw 8 ½” x 1 ¼” x 13/16” thick
for the X-axis :
Cut 2 pieces 4” x 1 ¼” x 13/16” thick for the Y-axis
Stack pieces and clamp
drill outer holes right through with 22mm forstener bit
With them still clamped drill a 1” hole 1/8”down now use a 5/8” bit and drill right through
first layer and with a 5/16” bit continue down through bottom layer.
Drilling in this fashion helps keep your centers more accurate.Drilling in this order with a brad point or forstener bit leaves a center mark where you can proceed with the smaller drill size.
Step 3: Z-axis Bearing Blocks
Cut 4 pieces 3” x 1 ¼” x 5/8”
Stack and clamp 2 pieces and drill outer holes with a 15 mm bit through both layers
Drill 1” hole 1/8” deep,drill 5/8” hole through first layer and continue through bottom layer with 5/16” hole.
Set aside other 2 blocks for now.
Assembling blocks bearings and rods :
Cut 4- 12mm rods to 13”
Cut 2- 8mm rods to 6 1/8”
Bevel rod ends slightly to avoid damaging rubber seals on bearings.Now put external snap ring in one groove of each bearing and push through corresponding holes until groove is exposed on other side and then attach other snap ring.
I used one of those assorted packs you can buy, it was imperial but found 7/8” fit the 22mm o.d. bearings and the 5/8”worked on the 15mm o.d. bearings.Snap ring pliers would probably be a good idea as they are pretty cheap.Keep the 1” drilled piece to the outside as shown.
Step 4: Cutting the Frame Base
I had access to 3/8 HDPE so I doubled it up to make the machine more robust this also provided some assembly benefits you will see as we continue.
The cutting and drilling order is most important to maintain accuracy.I like to cut everything a little oversize and then give the pieces a finish cut.Cut similar sizes at the same time.
Inside perimeter sides : 2pcs 12 ¼”x 2 1/8”
Front and back : 2pcs 11 ½” x 2 1/8”
Outside perimeter sides : 2 pcs 13” x 2 ½”
Front and back : 2 pcs 12 ¼” x 2 ½”
Base braces : 2pcs 13” x 3 ½”
Step 5: Drilling and Assembling Base
stack and drill 2 - 12 ¼” pieces as per drawing right through with a 3/16 bit
Stack and drill 2- 11 ½” pieces drill 5/16 center hole through both pieces
Drill 12mm holes through both pieces
Drill remaining 3/16” holes around perimeter through both pieces
Assemble pieces as shown in picture keeping 3/16” holes to top. Take 3/16” brad point bit drill through front and back pieces just enough to mark centers on sides and then take 1/8” brad point bit and continue to drill to a depth of an 1”.Assemble with 1” number 8 screws.
Drilling and assembling outside perimeter base :
Take one 12 ¼” piece and drill ½” hole where indicated to a depth of 7/32”
take other 12 ¼ “ and drill to a depth of 7/32” as well till the ½’ bearing fits is just below the surface.
Now you can stack the front and back and drill through with 3/16” where indicated.And finally drill through with 3/8” to center of ½” hole.Drill 1/8” holes to a depth of ¼”.
Turn over and fit in base drill 1/8” clearance holes and fasten with 5/8” #8 screws.
Step 6: Drilling Cutting and Assembling Y Axis Uprights and Brace
Cut 4 uprights rectangular for now we can cut angles after drilling is completed.
Cut 4 pieces 5” x 9 ½”.
Take 2 pieces stack and drill 12mm holes where indicated right through.
Drill ½” bearing holes to a depth of 7/32” keeping in mind you have a left and right piece.
Cut out notch on inner uprights also keeping in mind you have a left and right side.
Now stack 2 inner uprights and drill 3- 3/16” holes near notch.
Stack and drill 4 pieces keeping left and right pieces aligned and drill 9 -3/16” holes through all pieces excluding 2 on angle.Here is a simple jig I made for cutting angles.You just attach a strip of wood that fits into your mitre guage slot on to the back of some scrap wood large enough to accommodate your side piece and run it through table saw.Then lay your side piece with angle locations lined up with the edge of the board and screw down some wood slats to hold it in place.Run all 4 pieces through to perfection.
Now you can stack and drill 2-3/16” holes on exterior pieces on angle.
Almost forgot drill 4- 1/16” motor mount holes in right side outer upright.
Cut 2 braces to sizes indicated.Drill the 3/16” holes right through the large piece And the 1/16” holes to a depth of about ¼’on smaller piece. Keep one inch hole to left.Use 1”#8 to assemble. If you used panheads drill indents for clearance.Again use 1”#8 screws for end holes use Use 5/8”#8 for 2 holes on angle and 8 holes on brace.
Step 7: Z-plate Cut Drill and Assembly
Cut and drill Z backplate to required dimensions countersinking lower 3 holes.
Cut and drill Z top plate ½” inch center hole to a depth of 7/32” and then continue through with a 3/8” hole.
Drill 8mm holes all the way through.Do the same to the center hole of the bottom plate but drill 8mm holes to a depth of 5/16”.Assemble as shown.
Step 8: Threaded Rod
Insert threaded rod into centers of all axis 2- 15 ½” pieces in the X and Y and an 8 ½” piece in the Z.
Take the large piece of the antibacklash nut put on the spring and put on the small piece.Compress the spring slightly as you thread the rod through now attach 1” diameter end to rear bearing block with ½”#6 screws.
Now as far as I know anti backlash nuts are only available for tr8 acme threaded rods the ones pictured that I am using I have made with my cnc machine and will be on my website in the near future,just have to get a few bugs worked out.With the backlash nuts fastened press the ½”bearings into a all axis locations.
Step 9: Router Mount
Cut and drill the ¼” thick aluminum plate to specs in drawing or you can use HDPE plastic.Cut UHMW plastic to 3” x 3” block by 1 ½” or whatever thickness you managed to pick up.Cut out center of block with in my case a 2 1/8” hole saw check the diameter of your rotary tool.Remove excess I have outlined in red with a bandsaw.Set your table saw to make the notch on the side.Drill and tap four holes on back,drill and tap 2 holes on front deep enough to go past gap on side.Drill 3/16” holes to allow clearance to tighten to provide clamping action.Use 1”10/24 screws to fasten mount to plate and use 2- 1 ½” 10/24 screws for clamping router.
Step 10: Table Assembly
Table adapter plate is cut out of 5/8” thick UHMW after cutting to size drill 3/8” holes 3/16” deep with a forstner bit then drill the 3/16 holes all the way through then drill 1/8” holes to attach table top.Fasten block to X bearing blocks using 1”#8 screws then fasten table to block with 1”#8 screws. I had a red piece of 1/4'” ABS plastic 8 ¾” x 8 ¾” I centered on the table for a spoiler board.
Step 11: Couplers and Stepper Motor Mounts
Who says couplers have to be round.I cut these out of UHMW plastic and drilled a ¼” hole through the middle for the threaded rod cut the vertical slot to a depth of ½” and the horizontal slot to a depth of ¾” on the table saw be careful though use a push stick.I then drilled the 1/4” screw hole aout an 1/8” to counter sink the head and then a 5/32” hole down to the slot and then a 3/32” hole right through.If you have a different size motor shaft just enlarge the hole half way through. For the motor mounts I cut a 2 1/2” tube 2 ½” long for each mount I then drilled a 1 ½” Hole in the center with a hole saw.I then put the nema 23 in the hole and marked the screw locations and drilled and tapped them.I fastened the mounts to the machine with 5/8”#8 screws and fastened the motors to mounts with 10/24 ½’ screws.
Step 12: End
The down side of owning a router mill would sure love a shot at that grand prize
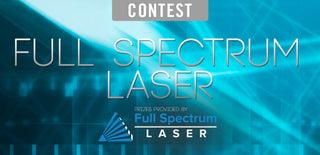
Participated in the
Full Spectrum Laser Contest 2016