Introduction: The Hexachord, a Rotary Musical Instrument
During a stint as a "Tech Disruptor" (Maker-in-Residence) at an Intel Experience popup, I spent some time building a spinning noisemaker using recycled materials. This led to thinking about motorized musical instruments, and to the realization that there are far too few rotary string instruments. There are a few really fabulous projects, like the Rotoharp, Eric Rosenbaum's Musical Gears (not strings, but awesome nonetheless), the Hurdy-Gurdy, Wheelharp, and the Viola Organista, but I had a few specific ideas in my minimalist-music-lovin mind.
I wanted repeated chords that you could retune, that you could turn on or off on the fly, and I wanted it to have the feeling of an ensemble, thus multiple sound chambers.
I've also been on a mechanical engineering kick, and incorporating mechanisms appealed to me.
The Hexachord is an instrument that I developed and tinkered into existence. It's a six-chambered string instrument with a spinning plectrum arm in the center that plucks each resonating chamber as it turns. Each chamber is mounted on a hinge, so that it can be maneuvered in or out of the way of the plectrum arm with a series of mechanisms, effectively turning them on or off. The spinning arm is powered by a motor from an old VCR.
In this instructable, I'll show you how the different parts of this came together. Maybe you'll get some ideas of your own for a new instrument.
Step 1: Materials
Wood (and lots of it):
Various types of plywood - a future version will use hardwood for the sound chambers.
3/4" Solid (Poplar, Oak, etc) Boards
Various Size Round Dowels
1x1" Poplar Square Dowels
Bamboo Skewers
Large Wooden Beads
Adhering:
Wood Glue
Screws (and a LOT of them, I went through over a hundred)
Bolts for attaching sound chambers
Tools:
Drill and Driver
Clamps - I bought a ton of dollar clamps from Home Depot, plus a few larger clamps
Good Ruler/Protractor/Square
Scroll saw
Drill Press - with various bits and hole saws
Belt sander
Dremel
Orbital sander
Various hand tools for tweaking
Other:
Soprano Ukulele Strings
Tuning pegs
Guitar Pick
Motor and Hookup Wire - I used a motor from a video cassette rewinder, along with other bits from the machine, such as the belt and pulleys
Zip Tie
Wood Stain, Multiple Colors
Step 2: Sketches and Plans
The idea of this was somewhat vague at first, and needed a lot of hammering out, so I did many sketches, and plenty of details changed over the course of the project. I did a lot of writing, a lot of drawing, and a fair amount of chatting with friends to try to explain it.
You'll see in my sketches that I considered a number of mechanisms in the planning process.
Step 3: Crashspace and Accountability
Getting a complicated project like this done requires some serious discipline, and in the end, you've gotta adopt some strategies. At CRASHspace, my local hackerspace, there is a very close and supportive community, and I committed myself to show my progress at each weekly member meeting. This meant that I always had to have substantial progress to show, that I needed to be able to document and describe what I'd been doing, and that I had to look at it through other people's eyes.
One of the beautiful things about this community is the interest that everyone has. People love to get intellectually involved in other people's work, and some very very smart people will make very very good suggestions. My instrument wouldn't be what it is, nor would it have come together as quickly as it did, without the help of my fellow Crashers. Love you guys.
Step 4: Prototypes
Some of my favorite materials for quick prototypes include skewers, hot glue, cardboard, and rubber bands. (I have a more detailed post on my blog about tinkering and prototyping materials, if you're interested.) In order to convey the idea of this instrument, and to help solidify the concept in my head, I made a small (about 1/3 size) version. Folks at Crashspace didn't seem to fully comprehend that it was just a tiny version until I brought out the first parts of the frame, which is - no mistake - big.
This small prototype has since fallen apart, but it was never meant to last. It allowed me to try out a couple mechanisms for manipulating the sound chambers.
I tried a couple sound chamber shapes as well, also in cardboard, which obviously isn't going to be the best for getting real sound, but it did give me a very rough idea of what the construction would look like.
Step 5: Sound Chambers
As I mentioned, I tried a couple different shapes for these. My original thought was to have a nice, curved lute-type shape. It became clear, though, that the construction of this shape would be much more complicated than I was looking for in a first version of this instrument. Ultimately, and since I did like the shape and sound, I landed on a straight-sided design closer to a balalaika. This was a natural fit to the shape of the whole, and helped to emphasize the hexagon theme.
I fine-tuned the design through several different versions, using increasingly nice wood for each. My first plywood was some very rough stuff from Home Depot, a next version used a thinner and higher quality ply from Rockler in Pasadena, and by the time I'd been through two versions, I was really clear on my design and could move to an all birch 3-ply wood from House of Hardwood. It came in a huge sheet that had to be cut down just to fit in my car.
The last wood was surprisingly resonant for plywood. I would have preferred a solid wood, though the cost in time and money was higher than I wanted, at least for this first full version.
(This is one thing I learned quite well during this project: it's better to cut a few corners than to get mired in too many details and not get it done at all.)
Since I had limited time available with the woodworking tools, I would calculate, measure and mark at home, then dive into the actual cutting at the shop.
The sound chambers were created the way they were thanks to consultation with another Crash member, Theron, who had built ukuleles in the past and was able to help me fine-tune the design (no pun intended). There is a block of wood that is glued just inside and provides support for the neck. Without this, the neck would never have been able to handle the pressure from the strings. See pictures.
Sanding happened throughout, but after the basic bodies were assembled, I did a thorough job with an orbital sander, which took care of any jutting flaws, lingering glue, and let me thin the face of the chambers some more.
Additional details came after the staining process, like adding the hinges, carved nut and saddle (see pictures for these), tuning pegs and strings.
Step 6: Frame
My Hexachord is built on a hexagonal frame, which I assembled with both wood glue and screws, cause a heavy, three-foot-tall instrument is not something you want falling apart on you. Two frames are held six inches apart to allow room for the mechanisms that control the sound chambers, and an additional structure extends to hold the sound chambers themselves.
I have learned just how much precision is required for wood joinery (for the record: invest in good measuring tools). I have also discovered that CrashSpace members are all in love with the laser cutter, and everyone tells me how much easier it would be if I used it to make my mechanisms, or my sound chamber pieces, or… my lunch or something. In some ways, I’m sure it would, but sometimes I just want to get in there and use my hands. (Except for lunch. I’m a lousy cook.)
I fixed pieces in place with wood glue, clamped them, and since it's a six-sided affair, this is where the multitude of inexpensive clamps proved their worth. It would have taken ages to wait for one or two pieces to dry before moving onto the next side. The glue was good for getting the joints where I wanted them, and once they were initially set, I would drill and screw them to make them more sturdy.
Lotsa screws. Lotsa screws.
Step 7: Mechanisms
The reason for six separate sound chambers is the ability to manipulate them independently.
I wanted to be able to control the position of each sound chamber from the same side. No dancing around to make it work (though that could be fun too). As rotary motion is pretty easy to translate over long distances, I decided on using a knob for each sound chamber that connected via dowel to a scotch yoke mechanism. It’s very efficient for converting rotary motion to linear. There’s a disc, pegs, and a U-shaped yoke, attached to dowels placed at right angles to each other. You can see a number of drawings in the pictures for this step.
Assembling this all on the frame required adding more 1x1" square dowel braces through which to run the knob dowels.
The knobs (which were cut on a drill press with hole saw) were stained to match their associated sound chambers (so you can tell which one you're moving), and were placed on the left side. It was a bit of a task maneuvering it all to fit, and I wound up modifying the shape of the disc (as you can see in my drawings). But the work paid off. Each mechanism effectively converts its rotary motion to the yoke mechanisms placed behind each sound chamber and gets them out where they can be played.
Step 8: Hinges
Two types of hinge attach the sound chambers to the frame and allow them movement. A ball and socket joint is glued to the back and conveys movement from the scotch yoke mechanism, and a basic butt hinge connects the small end of the sound chambers to the frame and keeps the motion in one plane.
The hinges, like most everything else with the Hexachord, are made of wood. I was planning to use pre-made metal butt hinges, but a) they would have stood out like a sore thumb amongst the lovely wood (as pointed out by Crasher Steve Goldstein), and b) I am a glutton for punishment. The ball and socket hinges I wanted would have been a bit harder to acquire pre-made, so I set about making my own custom ones.
Ball and Socket:
I used a drill press and scroll saw to build the socket in multiple layers. The bottom and top layer have holes slightly smaller than the ball to give it an approximation of a complete socket. In the end it doesn’t need more than a few points of contact - having the socket in contact over the whole ball would have applied a lot more friction than I wanted. The center is made of a square the same size as the top and bottom pieces, but with a hole a bit larger than the ball. I ultimately cut it into four pieces and used only two as spacers on opposite corners. The bottom piece was glued to the sound chamber, and the inside corner pieces were glued to that. The top piece I connected with screws in case I needed to remove/replace the sound chamber from the rest of the instrument. It’s a complicated thing; I like to leave myself the ability to repair and replace.
For the ball, there are nicely formed wooden spheres you can get, but finding just the right size wound up being more of a hassle than some wooden beads I tracked down at Michaels. I used a Dremel rotary tool to widen one hole to the right size for the dowel, and voila! A lovely, polished ball for the socket. Glue a dowel into the wooden bead and assemble it all. The whole construction works rather well.
(Note: when using a power tool to widen an existing hole, don’t hold it with a finger over the other opening. Ow.)
Butt Hinge:
The butt hinge was easier, as there are folks who have done very fine tutorials (this one is gorgeous). Mine had three knuckles (the interlocking parts that contain the axle). If you drill the axle holes before cutting and sanding the knuckles, it’s much easier to get the pieces to line up properly. I bolted the cut pieces together, and then glued (and clamped) the flat side of the small ones to another block. Good, strong wood glue is important in something like this. I like Titebond. In future versions, I will probably use a glue more suited to musical instruments for the sound chambers, but it did the job pretty well here.
If you take a look at all of the pictures I've uploaded, you'll also see that I used the back of the hinge as a tie-bar bridge, and attached the sound chamber's strings there.
One side of these hinges is glued to the small end of the sound chambers, the other side is bolted to the frame, so that the sound chambers are easily removed/replaced.
Step 9: Face and Plucking Arm
The face plate of the Hexachord is a simple piece of plywood, measured and cut to match the small hexagon formed by the front of the frame. To attach it (and make it easily removable), I drilled holes for pegs and glued the pegs into the frame. Matching holes in the face plate let you slide it on, and secure it with skewers through the pegs.
The motor was salvaged from a video cassette rewinder. It came with a convenient belt and pulley, to which I attached the plectrum arm base – a hand-cut wooden gear I’d made a couple months before and was dying to use. My original thought was to drill into the gear at an angle and secure the arm into that, but it wound up being more feasible to build a structure from bamboo sticks that would support the position of the arm. For one thing, it was easier to adjust, and for another, I just plain like building with bamboo skewers.
Onto the arm is attached a guitar pick, which is what plucks the strings. And the motor has wires that run back through the frame to attach to a variable voltage AC to DC adapter, so I can change the plucking arm's speed with the twist of a dial.
Step 10: Beta Testing, Aka Maker Faire 2014
Not only did I give myself weekly deadlines of updates at Crashspace meetings, I also decided that I wanted to present a working Hexachord at Crashspace's booth at the Bay Area Maker Faire in May 2014. I called it not so much a deadline as something on the horizon that I wanted. Wording is important, even in motivating yourself.
I spent a lot of long nights in the weeks before the event, but I did manage to get it finished and enjoyed seeing people interact with it all weekend. I also got to see all of the bugs in my design and cataloged them for redesign.
Step 11: Adjustments
Some people get nervous when approaching a thing someone else has made, for fear of breaking it. If you knock it over and smash it to smithereens, then yes, I will be upset. But if something isn't working properly, I want to know about it, and I'm fine with things falling apart in other people's hands. Hey, I made it once, I can make it again.
So a few obvious flaws worked their way to the fore at Maker Faire:
- It needed a sturdier stand than the basic frame, especially considering that the bottom sound chamber extended below the bottom of the frame; it could only sit at the edge of a table. The day-of hack was to prop it up, weigh it down, and tie it to the chain link fence behind our booth. Yeah, I fixed that quickly.
- Pieces of the mechanisms kept slipping from their spots on dowels. I'd glued them, but they needed some additional stabilization, which I solved by making discs I could cut in half and reattach with sufficient glue against the dowel and wobbly piece in question.
- The pick had a tendency to get stopped by the strings. The problems were that the belt wasn't getting enough tension, and the pick was too firmly attached to the arm. A guitarist's fingers have more give than my construction gave the pick. I wound up solving these problems by adding tension pulleys to the belt system, and adding a mildly flexible zip-tie between the arm and pick. You might notice in the video that there is a slight unevenness to the spinning of the arm. These modifications fixed that.
- The weight of the sound chambers is considerable, and ones on either side of the Hexachord move and stay in place fine, but the top and bottom chambers have that pesky gravity thing to deal with. For the top one, I added a counterbalance on its dowel. For the bottom, I added a friction brake.
Step 12: Fin and Future Development
That's my Hexachord, most of whose creation was accomplished in a little over a month of my "free time." I'm fairly pleased, and a lot of folks have wanted to hear about it. I was even invited to do a talk at Two Bit Circus' STEAM Carnival.
As I mentioned earlier, I do have some plans for where this can go from here. In addition to using higher quality materials, I have some designs for a smaller version whose sound chambers are moved by servos or solenoids and controlled by a human user via flex sensors. (Arduino ftw)
It would also be fun to have this instrument incorporated into a song. Hm, perhaps in a band of hand-made instruments. Anyone game?
Hope you enjoyed learning a bit about how I made my Hexachord!
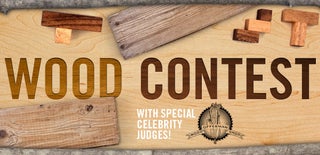
Participated in the
Wood Contest